摘要: 本文以添加0.1~0.3 wt.% Fe含量的Al-0.7Mg-0.6Si合金为对象,研究了不同Fe含量Al-0.7Mg-0.6Si合金在富氧溶液(57g NaCl + 10ml H
2O
2/L的腐蚀溶液)中的腐蚀行为,通过扫描电镜表征了浸泡腐蚀后样品表面的腐蚀形貌和腐蚀产物,在金相显微镜下表征了晶间腐蚀的截面深度,并与恒应力腐蚀后材料屈服强度的损失情况对比。结果表明,添加不同Fe含量的Al-0.7Mg-0.6Si合金材料的应力腐蚀性能存在差异。在富氧腐蚀环境中,Fe含量0.1 wt.%、0.2 wt.%、0.4 wt.%合金的腐蚀速率分别为:3.11 × 10
−4 mm∙A
−1、3.68 × 10
−4 mm∙A
−1、4.24 × 10
−4 mm∙A
−1;在富氧腐蚀环境中进行应力腐蚀实验,Al-0.7Mg-0.6Si合金强度与断后伸长率的损失随着合金内Fe元素含量的提高而提高,应力腐蚀性能变差。随着微量元素Fe含量的提高,Al-0.7Mg-0.6Si合金内的AlFeSi相数量逐渐增多,并会使得合金材料的应力腐蚀性能变差。
Abstract:
In this paper, Al-0.7Mg-0.6Si alloy with 0.1~0.3wt.% Fe was used as the research object. The Al-0.7Mg-0.6Si alloy with different Fe content was studied in oxygen enriched solution (57 g NaCl + 10 ml H2O2/L). The corrosion morphology and corrosion products of the sample surface after im-mersion corrosion were characterized by scanning electron microscopy (SEM), and the cross-section depth of intergranular corrosion was characterized by metallographic microscope, and the yield strength loss of materials after constant stress corrosion was compared. The results show that the stress corrosion resistance of Al-0.7Mg-0.6Si alloy with different Fe content is different. The results show that the corrosion rates of 0.1 wt.%, 0.2 wt.%, 0.4 wt.%, are 3.11 × 10−4 mm∙A−1、3.68 × 10−4 mm∙A−1、4.24 × 10−4 mm∙A−1, respectively. The stress corrosion tests in oxygen enriched environment show that the loss of strength and elongation after fracture of Al-0.7Mg-0.6Si alloy increase with the increase of Fe content in the alloy, and the stress corrosion resistance becomes worse. With the increase of trace element Fe content, the amount of AlFeSi phase in Al-0.7Mg-0.6Si alloy increases gradually, and the stress corrosion resistance of the alloy becomes worse.
1. 引言
Al-Mg-Si系铝合金力学性能较高,可加工性能优异,耐腐蚀性能较强,已广泛应用于汽车车身板,幕墙等民用行业 [1] [2]。因其可时效强化的特点,同时具有优异的可焊接性,符合轨道交通对材料性能的使用要求,6005A,6082等中高强Al-Mg-Si合金得到越来越多的关注。但该合金容易发生较快的时效响应进而影响其腐蚀性能,使其应用受到挑战 [3]。Fe元素在Al合金中常被视为杂质元素,形成的FeAl3和AlFeSi等化合物容易引起强度下降,点腐蚀严重。当合金中同时存在Fe和Si元素时,容易形成α-Fe2SiAl8相,而当Si过剩量大于Fe时,形成FeSiAl5相 [4]。这些含Fe相在一定程度上能抑制晶粒的生长,但其对腐蚀性能的影响关注较少,尤其是模拟复杂服役环境的富氧环境。
有关 Al-Mg-Si合金的研究主要是Cu含量 [5],Mg/Si比 [6],Zn含量 [7] [8],以及Cu-Zn混合添加的影响 [9] [10] [11] 及其时效热处理工艺的改进 [7] [8] [9] [10] [11],如何优化微量元素的添加以使其与过量的Si反应形成有利于提高合金性能的第二相更是研究的前沿。目前已有大量研究表明,添加微量Cu、Mn、Cr等元素能有效改善Al-Mg-Si合金的组织与性能,但是熔炼过程中引入的微量Fe对Al-Mg-Si合金的组织与性能的影响关注较少。本论文研究不同Fe含量的Al-0.7Mg-0.6Si合金在富氧环境下的腐蚀行为,探明Fe元素对微观组织与耐腐蚀性能的影响规律,为6系铝合金材料的生产及加工提供理论基础。
2. 实验材料及方法
实验材料为丛林铝业公司提供的Fe元素含量不同的Al-0.7Mg-0.6Si合金型材,分别为0.1 wt.%、0.2 wt.%与0.3 wt.%的Fe含量。表1为合金的主要化学成分(质量分数,%)。除了Fe含量的区别外,其它化学元素含量基本相同。
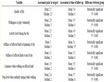
Table 1. Thechemical composition of Al-0.7Mg-0.6Si alloy (mass fraction/%)
表1. Al-0.7Mg-0.6Si-xFe 合金化学成分(质量分数/%)
材料的扫描电镜照片表征参照国标GB/T3246.1-2012执行,将样品进行粗磨、细磨、机械抛光后,参考GB/T23414-2009采用ZEISS MA10扫描电子显微镜对Al-Mg-Si合金材料的微观组织进行检测分析;结合GT/T17359-2012运用OxfordEDS型能谱仪对Al-Mg-Si合金材料及断口的第二相粒子进行能谱分析,测定其化学组成。Al-0.7Mg-0.6Si合金型材的室温拉伸试样尺寸一方面参考国标GB/T 228.1-2010。室温拉伸试验在DDL100电子万能材料试验机,实验过程中拉伸速率为2 mm/min,相当于3.3 × 10−2 mm/s,实验温度为室温(25℃ ± 3℃)。使用引伸计在拉伸试验过程中测量屈服点。每组材料取3个平行试样。应力腐蚀拉伸试验参照国标GB/T15970.6-2007进行,取样沿Al-0.7Mg-0.6Si合金型材的加工方向进行,试样厚度为3 mm,每种材料选取4组样作为平行样,实验分别在富氧腐蚀介质(57g NaCl + 10 ml H2O2/L的腐蚀溶液)中进行,每组材料取3个平行试样。实验温度控制在25℃,加载应力为150 MPa。在恒应力拉伸试验机上进行应力腐蚀实验。电化学试验参照国家标准GB/T24196-2009,并在Multi Autolab M204电化学工作站进行。试样尺寸为10 × 10 × 3.5 mm,试样电化学测试面积为1 cm2,试验前用导线连接试样,并在镶样时将其他5个非实验面密封。试验面(轧制表面)经打磨抛光后,用丙酮清洗干净。试样的电化学测试采取三电极体系,试样本身为工作电极,Pt片电极为对电极,饱和甘汞电极(SCE)为参比电极。电化学测试介质为质量分数3.5 wt.% NaCl溶液,试验测试试样的极化曲线,开路电位的测量时间为600 s,极化曲线测试中的扫描电位范围为−1.3~0 V,扫描速度为1 mV/s,实验温度为25℃。
3. 结果与讨论
3.1. 在富氧溶液中合金微观形貌的变化
图1为不同Fe含量的Al-0.7Mg-0.6Si合金在富氧腐蚀溶液中进行恒载荷腐蚀实验10天时试样表面的腐蚀形貌。由图1可以看出,在富氧溶液中,腐蚀会优先在合金晶界处腐蚀,从图中可明显观察到腐蚀出的晶界。晶界的腐蚀会降低合金晶粒间的结合力,随着腐蚀时间的增长还会使得晶粒变得容易脱落,从而使得在局部区域材料脆性增大,使得合金整体塑性下降。从图中可观察到随着合金内Fe元素含量的提高,实验合金试样表面腐蚀出的晶界数量逐渐增多。将SEM图片放大至500倍后观察,可在合金晶界上、晶粒内以及大的腐蚀坑中观察到大量因第二相产生的细小的腐蚀坑,对其进行EDS能谱分析后得到表2。由表2可知,腐蚀坑中残留第二相为AlFeSi相。在富氧溶液中合金沿晶界的腐蚀会对合金的强度产生小幅的影响,并会明显降低材料塑性,其中,合金试样表面腐蚀随着合金内Fe含量的提高而变得更严重,合金应力腐蚀性能变差。
图2为通过金相显微镜所观察到的在富氧溶液中实验合金进行恒载荷腐蚀实验10天时的恒载荷腐蚀深度情况。
由图2可知,Fe含量0.1 wt.%的合金试样(图2(a))最大腐蚀深度为35.5 μm,Fe含量0.2 wt.%的合金试样(图2(b))最大腐蚀深度为51.8 μm,Fe含量0.4wt.%的合金试样(图2(c))最大腐蚀深度为87.5 μm。随着Fe元素含量的提高,合金的最大应力腐蚀深度逐渐变深。
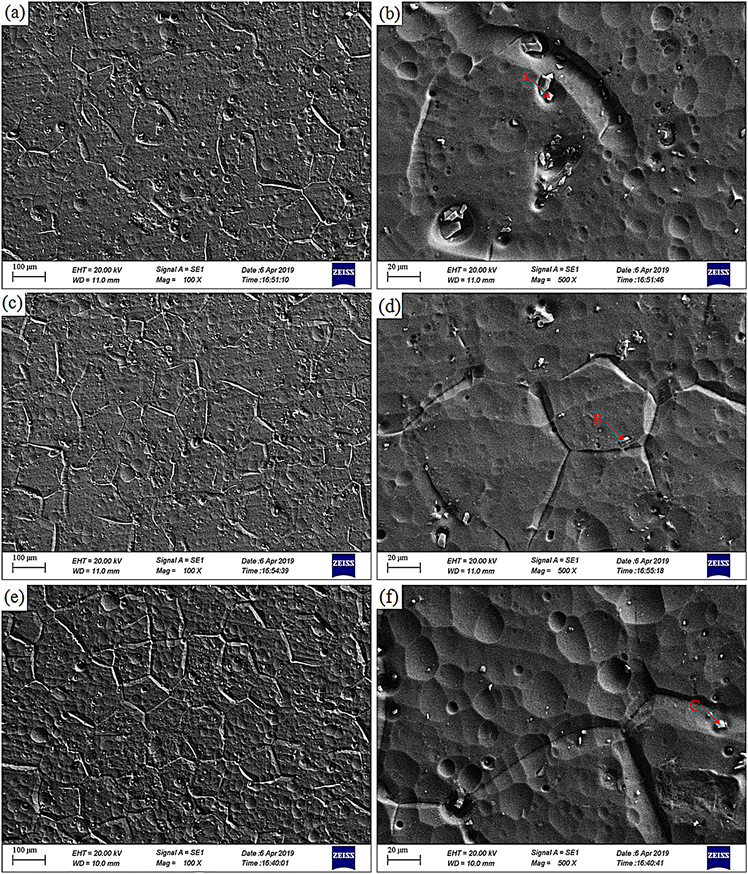
Figure 1. Corrosion’s morphology of Al-0.7Mg-0.6Si alloys in Oxygen enriched solution with 10 d 150 MPa: (a) (b) 0.1 wt.% Fe (c) (d) 0.2 wt.%Fe (e) (f) 0.4 wt.%Fe
图1. 10天150 MPa条件下在富氧溶液下Al-0.7Mg-0.6Si合金的表面腐蚀坑形貌:(a) (b) 0.1 wt.%Fe (c) (d) 0.2 wt.%Fe (e) (f) 0.4 wt.%Fe
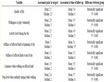
Table 2. EDS analysis results of Second phase in Figure 4~5(b), (d), (f)
表2. 图4~5(b)、(d)、(f)腐蚀坑内残留第二相EDS分析结果
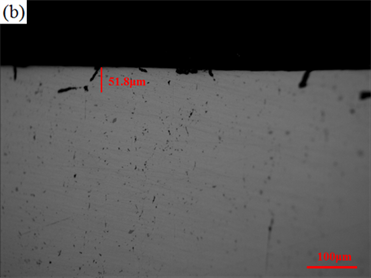
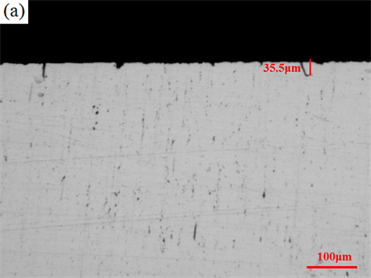
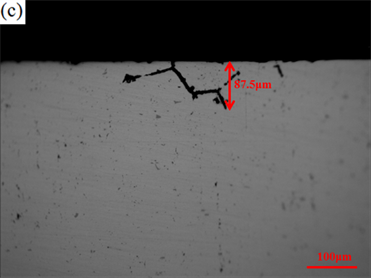
Figure 2. Corrosion depth of Al-0.7Mg-0.6Si alloys in Oxygen enriched solution with 10 d 150 MPa: (a) 0.1 wt.%Fe (b) 0.2 wt.%Fe (c) 0.4 wt.%Fe
图2. 10天150 MPa条件下在富氧溶液下Al-0.7Mg-0.6Si合金的腐蚀深度:(a) 0.1 wt.%Fe (b) 0.2 wt.%Fe (c) 0.4 wt.%Fe
3.2. 在富氧溶液中合金性能的变化
表3为不同Fe含量的Al-0.7Mg-0.6Si合金在富氧溶液(57 g NaCl + 10 ml H2O2/L的腐蚀溶液)中进行恒载荷腐蚀实验后试样的剩余强度情况。将表3中的合金剩余强度数据进行整理得到图3所示的合金恒载荷腐蚀剩余强度的变化图。由表3与图3(a)可以看出,实验合金试样在加载载荷为150 MPa时,材料经过恒载荷腐蚀实验后,其抗拉强度随实验时间的增加均出现小幅的下降,即合金材料发生了轻微的应力腐蚀。其中,抗拉强度损失最大的为Fe含量0.4 wt.%的合金加载10天的试样,抗拉强度损失为10.57 MPa,相当于初始抗拉强度的3.6%。由表3可以看出,随着Fe元素含量的提高,合金的剩余强度损失程度有所提升。故在富氧溶液中,合金发生较轻的应力腐蚀,且随着合金内Fe元素含量的提升,合金的应力腐蚀性能下降。由表3与图3(c)可知,进行应力腐蚀的试样相较于仅进行化学腐蚀腐蚀(未加应力)的试样强度损失更大,相差在1.5%~2.3%之间。仅进行腐蚀的试样抗拉强度损失很小,在1.1%~1.4%之间。实验合金在富氧溶液中的化学腐蚀性能优异。
表4为实验合金在富氧溶液中进行恒载荷腐蚀实验后试样的断后伸长率情况表。试样加载时长与加载载荷信息见表4中。图4为根据表4中合金断后伸长率情况所绘制出的反映合金断后伸长率情况的变化图。由表4与图4(a)可以看出,实验合金试样在经过恒载荷腐蚀实验后,材料断后伸长率有明显的下降。
实验5天时,Fe含量0.1 wt.%、0.2 wt.%、0.4 wt.%合金断后伸长率分别为13.3%、10.4%与7.5%,相比未实验试样断后伸长率分别下降了12.4%、16.0%与20.8%;实验10天时,Fe含量0.1 wt.%、0.2 wt.%、0.4 wt.%合金断后伸长率分别为12.7%、9.8%与6.8%,相比未实验试样断后伸长率分别下降了16.1%、21.5%与28.5%。合金在富氧溶液中进行应力腐蚀后,材料强度仅发生小幅下降,但材料塑性发生明显的下降,其中随着合金内Fe元素含量的提高,合金试样的断后伸长率损失变大,故合金的塑性也发生下降。由表4与图4(b)可知,未加载应力仅进行化学腐蚀的试样断后伸长率相对于未实验试样断后伸长率下降了3.4%~5.4%,其中Fe含量0.4 wt.%的合金下降最多。故化学腐蚀实验试样塑性仅发生小幅下降,且明显优于应力腐蚀实验试样。
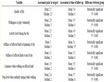
Table 3. Constant load corrosion’s residual strength of Al-0.7Mg-0.6Si alloys in Oxygen enriched solution
表3. 富氧溶液下Al-0.7Mg-0.6Si合金恒载荷腐蚀剩余强度
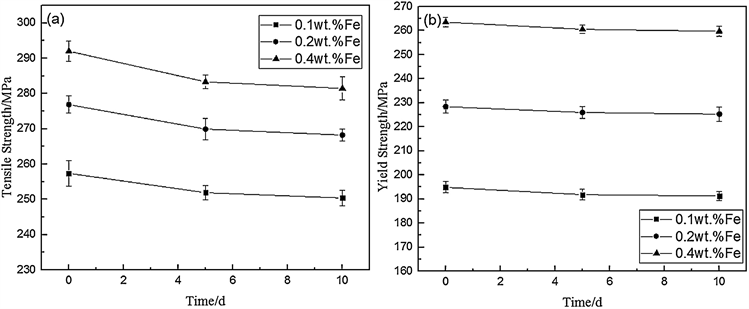
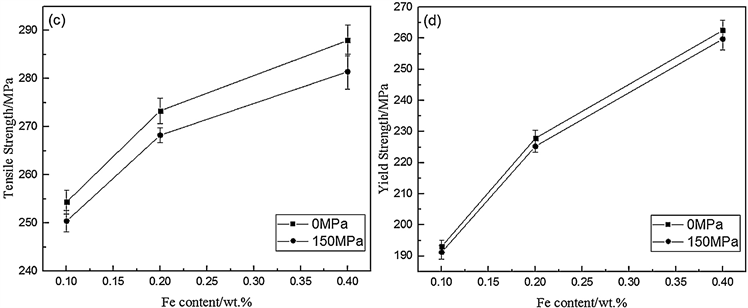
Figure 3. Constant load corrosion’s residual strength of Al-0.7Mg-0.6Si alloys in Oxygen enriched solution: (a) Change of tensile strength with times; (b) Change of yield strength with times; (c) Tensile strength at 10 days; (d) Yield strength at 10 days
图3. 富氧溶液下Al-0.7Mg-0.6Si合金恒载荷腐蚀剩余强度:(a) 抗拉强度随时间的变化;(b) 屈服强度随时间的变化;(c) 10天时的抗拉强度;(d) 10天时的屈服强度
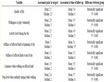
Table 4. Constant load corrosion’s elongation of Al-0.7Mg-0.6Si alloys in Oxygen enriched solution
表4. 富氧溶液下Al-0.7Mg-0.6Si合金恒载荷腐蚀断后伸长率
3.3. 在富氧环境下的电化学腐蚀性能
图5为不同Fe含量的Al-0.7Mg-0.6Si合金在富氧腐蚀溶液中进行电化学极化实验后得到的电化学极化曲线图。对实验合金的腐蚀速率进行计算,得到表5中的结果。
通过对比表5可知,在富氧溶液中,Fe含量0.1 wt.%、0.2 wt.%、0.4 wt.%合金试样的腐蚀速率分别为:3.11 × 10−4 mm∙A−1、3.68 × 10−4 mm∙A−1和4.24 × 10−4 mm∙A−1。可见,在富氧腐蚀溶液中,随着合金内Fe含量的提高,合金的腐蚀速率逐渐提高,其电化学腐蚀性能变差。
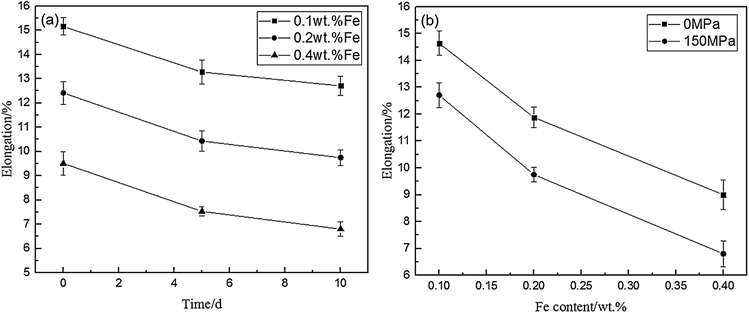
Figure 4. Constant load corrosion’s elongation of Al-0.7Mg-0.6Si alloys in Oxygen enriched solution: (a) Change of elongation with times; (b) elongation at 10 days
图4. 富氧溶液下Al-0.7Mg-0.6Si合金恒载荷腐蚀断后伸长率:(a) 断后伸长率随时间的变化;(b) 10天时的断后伸长率
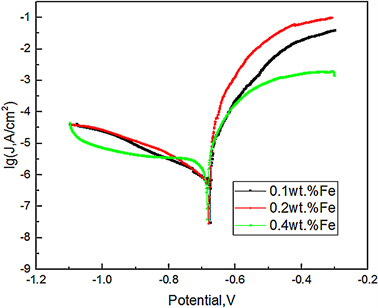
Figure 5. Polarization curves of Al-0.7Mg-0.6Si alloys in Oxygen enriched solution
图5. 富氧溶液下Al-0.7Mg-0.6Si合金的电化学极化曲线
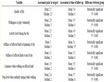
Table 5. Corrosion parameters of polarization curves of Al-0.7Mg-0.6Si alloys in different solutions
表5. 不同腐蚀溶液中Al-0.7Mg-0.6Si合金电化学极化数据
4. 结论
1) Al-0.7Mg-0.6Si合金材料的应力腐蚀性能存在差异。在富氧腐蚀环境中进行应力腐蚀实验,Al-0.7Mg-0.6Si合金强度与断后伸长率的损失随着合金内Fe元素含量的提高而增大,应力腐蚀性能变差。
2) 在富氧腐蚀环境中,Fe含量0.1 wt.%、0.2 wt.%、0.4 wt.%合金的腐蚀速率分别为:3.11 × 10−4 mm∙A−1、3.68 × 10−4 mm∙A−1、4.24 × 10−4 mm∙A−1;随着Fe元素含量的提高,Al-0.7Mg-0.6Si合金的电化学腐蚀性能变差。