1. 前言
工艺装备的柔性化一直是现代工业需要解决的难题,夹具的柔性化就是指同一类型的夹具能够更大范围地适应各种形状的零件,随着现代制造业的发展,零件加工越来越向多品种、小批量、精密化发展,工装也存在更换频繁的问题,这样会严重影响机床的有效切削时间,很多时间都浪费在工件的手动安装上,据统计,有些机床的有效切削时间比例还不到50%,因此,机床夹具的柔性化和自动化越来越引起制造行业的重视。国内外很多学者针对柔性夹具开展了研究和应用,董辉跃等 [1] 针对精密零件结构件装夹难点,提出了基于特征的精密结构件装夹方案设计方法。林勇等 [2] 通过对加载顺序以及加载方式等各种装夹方案的夹紧力位置、进行模拟分析,确定了最佳方案。Wu等 [3] 提出了确定夹具的自动定位方案。范玉青等 [4] 提出夹具元件选择方法。王细洋等 [5] 利用规则推理方法,来确定定位点布局和定位基准和方案。陈忠伟等 [6] 合理运用过定位技术提高工件刚度,采用并联油缸及旋转油缸实现工件的装夹。叶寒等人 [7] 采用“三柱为面、自定心机构为圆柱销、弹性伸缩机构为菱形销”的“一面两销”定位机构,通过液压系统对工件进行定位、夹紧的顺序动作,实现了工件装夹。以上自动夹具设计方案对工艺装备设计人员提供了一定的技术支持,但在自动化技术方面还存在不足。
气动柔性夹具是集机械、电气、气动和控制技术、信号处理技术等方面的交叉学科相结合的一门新兴技术,将电控、气动随行固持加工等技术相结合,刘伟 [8] 提出随行夹具对柔性自动化生产线适应技术,实现对被加工件的快速定位、装夹以及加工过程对零件压紧件的随行功能,并对随行夹具关键零件的变形提出了控制要求,提出了随行夹具的装配方案,赵冬梅等 [9] 提出了可转位零件夹具的设计方法,但对夹紧力控制的调节机构的介绍还不足。
2. 薄壁压铸件工艺分析
如图1为一个薄壁压铸件,需要对轮廓和孔进行精加工,零件外观比较规则,适合采用自动化夹具,由于刚性不是很好,夹紧力不能过大,需要自动调节夹紧力大小。由于材料是铝合金的,强度和硬度都比较低,导热性能好,适合高速加工,定位采用完全定位,夹紧方式采用气动夹紧方式,控制方式采用PLC程序对夹紧力进行适时控制、调节,防止零件受力过大变形的问题。
3. 夹具系统的建立
3.1. 夹紧力控制方式
夹具系统工作方式:通过PLC软件设计控制程序,下载到PLC程序控制器中,PLC运算各类传感器检测提供的电信号,控制空气电磁阀动作顺序进而控制气缸动作顺序,使气缸对工件实现自动定位和夹紧。
夹紧力大小影响结构件的加工稳定性和质量。如果夹紧力过小,会导致工件整体装夹刚性不足,产生工件让刀和刀具颤动现象;反之,夹紧力满足夹紧要求,但超过工件结构刚性时,易产生工件变形。因此需要确定目标夹紧力值和控制夹紧力始终趋于目标夹紧力变化。
具体操作过程是:先在触摸屏中设置上述的夹紧力,通过传感器对夹具夹紧力的大小检测,通过模拟量模块接受信号输入到数控系统内置PLC中,由于接收到的信号是模拟量的,应该选择合适的变送器将信号变成标准信号(0~10 V电压信号),通过PLC中的A/D模块转换,利用PID控制模块将与目标换算值相比较后,产生PWM反馈信号经放大器放大后与设定值进行比较,而对气路压力进行控制,这样避免夹紧力不足或者过紧控制图如图2。
夹紧力控制图如图3所示,当气缸夹紧工件后,压力传感器检测夹紧端的压力值,将其转化为标准量程的电压或者电流,经放大器放大,通过三菱FX-3U内部A/D转换模块能够将模拟量转换为数字量。利用PID控制模块将与目标夹紧力的换算值相比较后,产生PMW反馈信号经放大器放大后传递至高速空气开关,如图4中的Y6和Y7,通过高频率地控制进气和放气,使夹紧力接近目标夹紧力值。
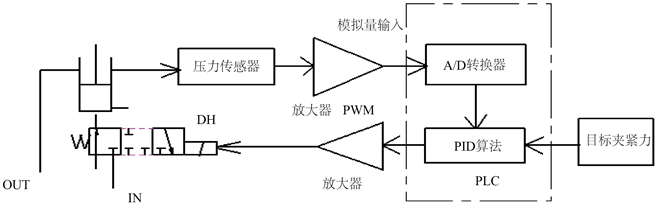
Figure 3. Clamping force control diagram
图3. 夹紧力控制图
3.2. 夹具系统气动回路设计原理图
根据夹具的运行,设计了气动原理图,如图5所示,根据夹具的运行,设计了气动原理图,如图5所示。气源装置提供足够的气压,五个气缸的摆放位置为气动夹具安装工件的位置,两位五通电磁阀YV通断实现气缸的夹紧和放松,高速空气开关SP1通过高速通断来完成气缸的高频率地进气与放气,这样可以动态地控制夹紧力。
4. PLC控制系统设计
4.1. 控制要求与控制流程图
控制过程按照顺序程序进行,控制流程图如图6所示。
4.2. PLC地址分配及接线
根据该PLC控制系统系统要求,输入输出点数,以及需要模拟量输入信号(压力传感器),以及高速开关,PLC选型采用三菱FX3U-32MR,具体分配如表1所示。并且给出了PLC接口的接线图以及分配I/O接口,如图4所示:
控制程序梯形图(略),实现以下过程:
(1) 启动,将工件安装到工作台上,通过限位开关对工件实现定位。
(2) 定位完成后,启动气缸动作,夹紧零件,压力传感器测力,与设定值进行比较,当达到设定值后,停止夹紧。
(3) 数控加工,工件完成后,启动气缸动作,释放工件,为下一次加工做准备。
4.3. 有限元分析验证
本文中所选用的材料是7075-T7351航空铝合金,材料性能如下表2所示
该结构件在加工时的铣削力明显大于精加工,因此在计算目标夹紧力时只考虑粗加工时的工艺参数,计算不同方向气缸所需要的夹紧力大小。铣削力经验公式如下:
式中:ap为铣削深度,mm;fz为每齿进给量,mm/齿;aw为铣削宽度,mm,Z为铣刀齿数;d0为铣刀直径,mm;n为主轴转速,r/min;kFZ为铣削力修正系数。
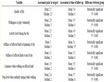
Table 1. Input, output and address assignment table
表1. 输入输出及地址分配表
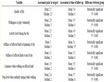
Table 2. Performance values of aviation aluminum alloy 7075-T7351
表2. 7075-T7351航空铝合金材料性能值
依据铣削用量参数手册查阅到所需要的参数,其中cF = 1670,XF = 1.0,wF = 0.2,yF = 0.75,VF = 1.1,qF = 1.3,kFZ = 1.6。计算结果如下:
根据本文中的夹具方案,夹紧力F平衡于最大夹紧力Fmax。为了安全起见,采取安全系数,则夹紧力
,取整为240 N。
从图7(a)和图7(b)看出,位移0.126 mm圆孔周边位移为0.0325 mm,应力64.5 mpa圆孔周边最大应力8.55 mpa。
位移为0.116 mm圆孔周边位移为0.022 mm,应力为51.6 mpa周边最大应力6.6 mpa,最大从图8(a)和图8(b)看出应力6.6 mpa。
将结构件模型导入到有限元分析软件Midas NFX中,根据航空合金的材料性能数据,以定位面为边界条件,划分网格,得到优化前后的应力应变云图。数据对比如下表3。
(a)
(b)
Figure 7. (a) Displacement diagram; (b) Stress diagram
图7. (a) 位移图;(b) 应力图
(a)
(b)
Figure 8. (a) Displacement diagram; (b) Stress diagram
图8. (a) 位移图;(b) 应力图
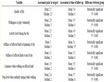
Table 3. Comparison of data before and after optimization of structural parts
表3. 结构件优化前后数据对比
数据分析表明,该航空铝合金结构件在铣削加工圆孔时,通过对比优化前后圆孔边缘极值,可以得出圆孔边缘处的位移和应力数值均能达到一定幅度的降低,降低幅度为32.2%和22%。因此,对于薄壁合金类零件,采用合适的夹具夹紧方案和工艺,能大大改善加工性能。
5. 结论
本文研究了基于PLC的自动化夹具的设计,通过薄壁压铸零件的工艺分析,由PLC程序控制零件的夹紧力,避免零件受力不足或过大,并运用有限元对零件进行受力分析,得出零件的应力应变图,为选择合理的夹紧力提供了依据,文章综合了机械、电气、气动、传感器知识,并且能够有效减少夹具组装时间和工件装夹时间,减轻了劳动强度,提高了生产率,提高了工件的加工质量。
基金项目
2020年台州市科技局科研项目,编号:2003gy38。