1. 引言
先进复合材料(ACM)具有高比强度、高比模量、耐高温、耐腐蚀、耐疲劳、阻尼减震性好、破损安全性好,性能可设计等优点,在航空航天、电子信息等高技术领域得到了广泛应用 [1] [2] [3] [4]。随着航空航天工业的发展,对复合材料的耐温性能要求越来越高 [5] [6],常用的聚酰亚胺基复合材料耐温等级为400℃左右,逐渐无法满足需要,而耐温性较好的石英陶瓷基复合材料成本高、制备周期长、加工性能差,限制了其在中温区的应用 [7] [8] [9]。因此,研究耐温等级更高的新型高性能树脂基复合材料成为未来的研究趋势 [10] [11] [12]。
含硅芳炔树脂是指大分子主链中具有芳炔链节和硅烷链节的聚合物,为目前耐温性最高的有机材料之一 [13] [14]。该树脂具有优异的耐热性、较低的粘度、固化温度低,可使用于多种成型工艺等优点,其石英纤维增强含硅芳炔树脂基复合材料具有在宽温宽频范围内介电常数和介电损耗稳定的优点,是耐高温天线罩理想基体树脂 [15] [16] [17] [18]。
本文对含硅芳炔树脂(PSA)的化学反应特性、流变性能进行了测试分析,研究了加压温度、加压大小、固化温度等不同工艺参数对石英纤维(QF)/PSA复合材料力学性能的影响,在此基础上确定了复合材料的成型工艺制度。考察了复合材料在500℃高温下的力学强度以及宽频范围内的介电性能,为石英纤维/含硅芳炔复合材料进一步应用于耐高温透波材料领域提供参考。
2. 实验方法
2.1. 原材料
含硅芳炔树脂(PSA),华东理工大学;B型石英玻璃纤维布(QF),纤维布厚度0.2 mm,面密度(210 ± 21) g/m2,武汉鑫友泰光电科技有限公司;丙酮:分析纯,上海凌峰化学试剂公司。
2.2. 试样制备
将PSA树脂和丙酮按质量比2:1混合,均匀涂覆在石英布表面,晾置12小时后在烘箱中烘干制得石英纤维布增强含硅芳炔预浸料(以下简称预浸料)。将预浸料裁剪、铺放于模具中,并在压机上采用模压工艺制备得到QF/PSA复合材料层压板,机械加工得到力学性能和介电性能等测试试样。
2.3. 性能测试方法
2.3.1. 树脂性能
示差扫描量热分析(DSC)采用日本岛津公司生产的DTG-60Plus型差热热重同步热分析仪测定,测试温度范围为−65℃~350℃,升温速率为10℃/min,氮气氛围;热重分析(TGA)采用日本岛津公司生产的DTG-60H差热热重同步热分析仪测定,测试温度范围为30℃~800℃,升温速率为10℃/min;红外光谱分析采用日本岛津公司生产的IRPrestige-21型傅里叶红外光谱仪进行测试,测试范围4000~500 cm−1;树脂的流变性能采用德国HAAKE公司的 Mars 40流变仪进行测试,升温速率5℃/min。
2.3.2. 复合材料性能
力学性能采用Instron1185型万能试验机并参考标准GB/T 1447-2005 [19]、GB/T 1449-2005 [20]、GB/T 1450.1-2005 [21] 及GB/T 9979-2005 [22] 进行测试;动态力学分析(DMA)采用瑞士METTLER TOLEDO公司的DMA 1型动态力学性能测试仪进行测试,升温速率5℃/min。介电性能由航天材料及工艺研究所采用带状线谐振腔法和短路波导法对复合材料的介电常数和损耗角正切进行相关测试。
3. 结果与讨论
3.1. PSA树脂固化反应特性
PSA树脂的DSC曲线如图1所示。从图可看出,在固化过程中会发生明显的放热。树脂从160℃开始出现放热现象,峰值温度是224.4℃,固化终止温度为238.7℃,树脂固化放热为589.8 J/g,且300℃以上还有放热的趋势,具体数据见表1所示。
PSA树脂存在内炔和外炔基团,一般情况下,
PSA树脂的固化反应从外炔开始,即在160℃开始反应,250℃反应基本结束。由于内炔的位阻较大,反应活性远远低于外炔,因此300℃以上放热主要为内炔基团的交联反应。如果近一步提高固化温度至300℃,大部分内炔基团发生交联反应,树脂交联密度提高,会导致复合材料力学性能下降。因此树脂固化温度可以选在250℃~300℃之间。固化放热峰形比较尖锐,说明固化反应比较剧烈,反应速度过快将不利于固化反应的充分进行,固化过程应阶梯式升温固化,并在每个温度段留有充分的保温时间。
图2是PSA树脂固化前后的红外图谱。从红外谱图中可以看出,3299 cm−1处是端炔基中C-H键的伸缩振动吸收峰;2155 cm−1处的强峰归属于-C≡C-键的伸缩振动吸收峰,-Si-C-键的伸缩振动吸收峰在1245 cm−1。树脂固化前,3299 cm−1处的振动峰尖锐而强烈,固化后,该处的振动峰已基本消失,且2155 cm−1处的振动峰强度减弱,说明PSA树脂在固化后外炔基团大都发生了交联反应,只剩下内炔基团未完全发生反应,与DSC分析结果一致。通过控制固化温度可以在一定程度上,控制PSA外炔和内炔的交联反应程度,若使树脂内炔反应程度提高,则需进一度提高固化温度。
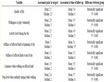
Table 1. DSC analysis results of PSA
表1. PSA树脂的DSC分析结果
Ti: initial curing temperature; Tp: peak temperature; Tt: terminal temperature; ΔH (J/g): the cure energy.

Figure 2. FT-IR of PSA before and after curing
图2. PSA树脂固化前后的红外图谱
3.2. PSA树脂及其复合材料的热稳定性
图3为固化后的PSA树脂在氮气中的TGA曲线,具体数据见表2所示。可以看出,PSA树脂5%热失重温度(Td5)高达600℃,10%热失重温度为715℃,800℃残炭率为86.3%,显示出含硅芳炔树脂具有良好的热稳定性。这可归因于其固化是由芳炔基的交联反应引起,可发生环三聚、共轭多烯等,形成高度交联结构,从而具有优异的耐热性能。
同时,采用动态力学分析法(DMA)测试了QF/PSA复合材料的玻璃化转变温度(Tg),结果显示,温度升至600℃时,未见损耗角正切出现显著地上升以及峰值,说明QF/PSA复合材料的Tg大于600℃,热稳定性优异。
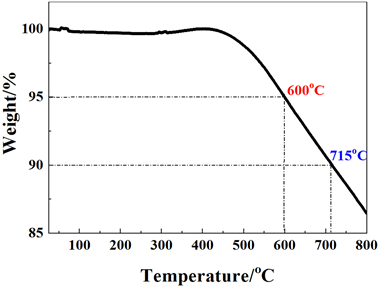
Figure 3. TGA curves of the cured PSA in N2
图3. PSA树脂固化物在氮气气氛下的TGA曲线
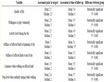
Table 2. TGA analysis results of the cured PSA resin
表2. PSA树脂固化物的TGA分析结果
T5, 5% weight loss temperature; T10, 10% weight loss temperature; Rw, char yield at 800˚C.
3.3. PSA树脂的流变性能
为了使树脂在模腔中较好地流动并有效浸润增强材料,树脂本身需要有较好的流变性能,以满足复合材料成型和加工的需要。图4是PSA树脂的黏温曲线,从图中可以看出,PSA树脂黏度随着温度升高而逐渐降低:温度上升至90℃时,树脂黏度即下降至100 mPa.s,当温度达到树脂粘度在160℃时达到最低,约为35 mPa.s。进一步测试了树脂在160℃温度条件下的黏时曲线,如图5所示。图中可看出,在
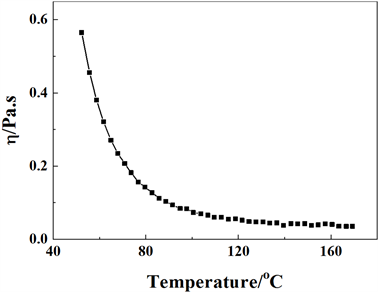
Figure 4. Viscosity temperature curve of PSA
图4. PSA树脂的黏温曲线
160℃条件下,树脂黏度随着时间推移而逐渐增大,这归因于树脂的缓慢固化。另外,从图中还可看到树脂在160℃条件下的表观凝胶点时间为41 min,具有合适的凝胶时间。
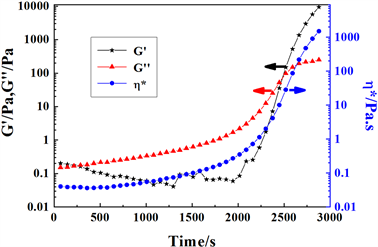
Figure 5. Isothermal viscosity profile of PSA at 160 ˚C
图5. PSA树脂在160℃下的等温黏度曲线
3.4. QF/PSA复合材料的成型工艺
3.4.1. 树脂含量对QF/PSA复合材料性能的影响
图6为不同树脂含量的QF/PSA复合材料的力学性能。由图中可以看出,树脂含量对QF/PSA复合材料的力学性能影响显著,随着树脂含量的增加,复合材料的力学性能呈现先增大后减小的趋势,其中弯曲强度和层间剪切强度变化明显。这是因为树脂在复合材料中起到应力转移和分散的作用。当树脂含量较少时,纤维粘结力不足,无法作为一个整体来抵抗形变和外力;当树脂含量过高时,纤维质量分数降低,致使纤维的增强作用减弱,复合材料的力学性能下降。因此,QF/PSA复合材料的树脂含量控制在30%~35%。
(a) 拉伸强度 (b) 弯曲强度 (c) 层间剪切强度
Figure 6. Effect of resin content on mechanical properties of QF/PSA composite
图6. 树脂含量对QF/PSA复合材料力学性能的影响
3.4.2. 成型压力对QF/PSA复合材料性能的影响
固化工艺参数中加压大小是影响QF/PSA复合材料构件成型的主要因素。加压压力越大,越有利于材料固化成型时小分子的排除,降低孔隙率,提高QF/PSA复合材料的质量和力学性能。图7是不同压力成型QF/PSA复合材料层压板的力学性能。可以看出,随着压力的不断增大,QF/PSA复合材料的拉伸强度和弯曲强度不断提高,但压力增加至3.0 MPa之后,强度增幅较小,压力的改变对复合材料的力学强度影响不明显,复合材料的力学强度趋于稳定。QF/PSA复合材料的层间剪切强度先随压力的增加而不断增大,但当压力增加至4 MPa时,层间剪切强度略有下降。这是由于压力过大时,大量树脂被挤出流失,使QF/PSA复合材料含胶量降低,层间粘结强度减小,层剪强度下降。因此,综合考虑QF/PSA复合材料加压大小应选择3.0~4.0 MPa。
(a) 拉伸强度 (b) 弯曲强度 (c) 层间剪切强度
Figure 7. Effect of pressure on mechanical properties of QF/PSA composite
图7. 成型压力对QF/PSA复合材料力学性能的影响
3.4.3. 固化温度对QF/PSA复合材料性能的影响
由PSA树脂的DSC测试可知,PSA树脂在250℃基本反应结束,以250℃作为固化温度的参考温度点选择不同的固化温度成型QF/PSA复合材料层压板,并进行力学性能的测试,结果见图8。试验结果显示固化温度为250℃时,QF/PSA复合材料的力学强度最高,与DSC测试的结果一致。选择最佳的固化温度,使固化交联完全度尽可能最大,提高了QF/PSA复合材料的质量和力学性能。
综上所述,QF/PSA复合材料树脂含量应控制在30%~35%之间,成型压力为3.0~4.0 MPa,固化温度在250℃时为最佳。
(a) 拉伸强度 (b) 弯曲强度 (c) 层间剪切强度
Figure 8. Effect of curing temperature on mechanical properties of QF/PSA composite
图8. 固化温度对QF/PSA复合材料力学性能的影响
3.5. QF/PSA复合材料的高温力学性能
QF/PSA复合材料在高温下的力学性能如表3所示。可知,300℃时QF/PSA复合材料拉伸强度、弯曲强度、层剪强度保持率分别为73.3%、76.9%和69.6%,强度保持率均在69%以上;500℃时QF/PSA复合材料拉伸强度、弯曲强度、层剪强度保持率分别为54.6%、57.4%和51.4%,强度保持率均在51%以上。因此,QF/PSA复合材料具有优异的耐热性和力学性能,可以作为耐高温结构复合材料使用。
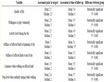
Table 3. High temperature mechanical properties of QF/PSA composite
表3. QF/PSA复合材料的高温力学性能
3.6 QF/PSA复合材料的介电性能
图9和图10为QF/PSA复合材料在不同温度和频率下的介电性能。可以看出,QF/PSA复合材料的介电常数和损耗随温度升高有所增加,但增幅不大,介电常数稳定在3.30~3.44之间,介电损耗在(4.7~6.9) × 10−3之间。而且,同一温度下,介电性能在7~18 GHz频率范围内波动较小。说明,QF/PSA复合材料在宽温和宽频范围内具有稳定的介电性能。
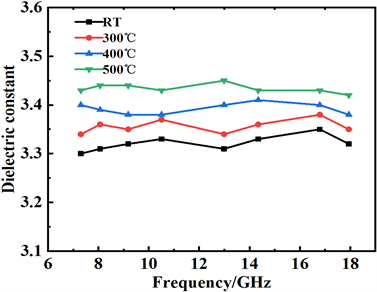
Figure 9. Dielectric constant of QF/PSA composites at different temperature and frequency
图9. QF/PSA复合材料在不同温度和频率的介电常数
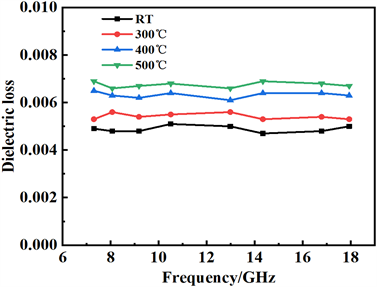
Figure 10. Dielectric loss of QF/PSA composites at different temperature and frequency
图10. QF/PSA复合材料在不同温度和频率的介电损耗
4. 结论
1) 采用DSC、FTIR和流变仪对含硅芳炔树脂(PSA)的固化反应特性和流变性能进行了表征。结果表明,PSA树脂在160℃开始发生放热反应,250℃之前基本反应完成;树脂黏度随着温度升高而逐渐降低,在160℃的凝胶时间为41 min,具有合适的凝胶时间。
2) PSA树脂5%热失重温度(Td5)高达600℃,10%热失重温度(Td10)为715℃,800℃残炭率为86.3%,显示出含硅芳炔树脂良好的热稳定性。
3) 采用模压工艺制备了石英纤维增强含硅芳炔树脂基(QF/PSA)复合材料,研究了树脂含量、成型压力、固化温度对QF/PSA复合材料性能的影响,确定了最佳制备工艺参数:树脂含量为30%~35%,成型压力为3.0~4.0 MPa,最佳固化温度为250℃。
4) QF/PSA复合材料具有良好的高温力学性能:300℃时QF/PSA复合材料拉伸强度、弯曲强度、层剪强度保持率分别为73.3%、76.9%和69.6%,强度保持率均在69%以上;500℃时拉伸强度、弯曲强度、层剪强度保持率分别为54.6%、57.4%和51.4%,强度保持率在51%以上。
5) 在RT-500℃范围内,QF/PSA复合材料的介电常数稳定在3.30~3.44之间,介电损耗在(4.7~6.9) × 10−3之间。同一温度下,介电性能在7~18 GHz频率范围内波动较小。说明,QF/PSA复合材料在宽温和宽频范围内具有稳定的介电性能。
参考文献