摘要:
液氨储量超过10吨属于重大危险源,运输、贮存和使用过程均存在安全隐患。电厂现有脱硝液氨罐区属于重大危险源,液氨在运输、贮存和使用过程中存在较大的安全隐患。根据日趋严格的安全形势要求及从电厂安全生产风险防控的实际需求出发,脱硝还原剂供应由液氨改为尿素工艺是必要的。综合尿素水解和尿素热解的技术和经济性对比,电加热尿素热解、烟气换热尿素热解、尿素水解(含催化水解)、尿素直喷制氨技术在原理上、实际应用方面均可行、且有实际改造案例。电加热尿素热解制氨技术方案电耗大、运行问题多,经济性和稳定性均不佳,故不建议新建机组或改造工程项目采用该技术方案。尿素水解制氨技术(含催化水解)和烟气换热尿素热解制氨技术运行稳定、安全性好。可根据上述技术适用条件,针对各厂的实际情况进行选择。
Abstract:
Liquid ammonia reserves of more than 10 tons are a major source of danger, and there are potential safety hazards during transportation, storage and use. The existing SCR liquid ammonia area of the power plant is a major source of danger, and liquid ammonia has potential safety hazards during transportation, storage and use. In accordance with the increasingly stringent requirements of the safety and environmental protection situation and from the actual needs of power plant safety production risk prevention and control, it is necessary to change the supply of reducing agent in the denitration system from liquid ammonia to urea. According to the technical and economic comparison of urea hydrolysis and urea pyrolysis, electric heating urea pyrolysis, flue gas heat exchanger urea pyrolysis, urea hydrolysis (including catalytic hydrolysis), urea direct injection ammonia technology are feasible in principle and in practical application, and there are practical transformation cases. The technical solution of urea pyrolysis (electric heating) consumes a lot of electricity, has many operational problems, and has poor economy and stability. Therefore, it is not recommended to adopt this technical solution for new units or technical renovation projects. Urea hydrolysis technology (including catalytic hydrolysis) and urea pyrolysis (flue gas heat exchange) technologies are stable and safe. The selection can be made according to the above technical application conditions and the actual conditions of each plant.
1. 引言
当前火电机组脱硝所使用的还原剂主要来源于尿素、液氨、氨水三种 [1]。现阶段,国家、行业和一些地方政府对脱硝还原剂的安全合理使用提出了新的要求,并出台了相应的规范和导则,指导脱硝还原剂的选择和使用,如《大中型火力发电厂设计规范》(GB50660-2011)提出位于大中城市及近郊区的电厂宜选择尿素作为还原剂。本文对国内外脱硝还原剂液氨改尿素的技术路线进行了对比分析;梳理了各技术的特点。
2. 尿素制氨工艺的对比
尿素(CH4N2O)为无毒无味的白色晶体或粉末,是人工合成的有机化合物,其理化性质较稳定,广泛应用于农业及工业领域,它的运输,存储和管理相对安全。根据尿素生产氨的原理和过程的不同,尿素制氨技术可分为尿素热解制氨技术、尿素水解制氨技术、尿素直喷制氨技术。
2.1. 尿素水解制氨技术
如图1所示,把尿素颗粒和去离子水加入到溶解罐中,将其溶解成40%~60% (质量分数)的尿素溶液,使用尿素溶解泵将其送至尿素溶液储罐;再把储罐中的尿素溶液通过料泵、计量与分配装置送入水解反应器,在水解反应器中把尿素水解,生成NH3、H2O和CO2,再经氨喷射系统(双流体喷枪)进入SCR脱硝系统。其化学反应式为 [2] [3]:
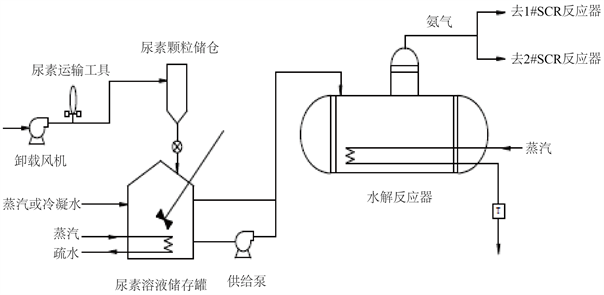
Figure 1. A typical technical process of urea hydrolysis to produce ammonia
图1. 一种典型的尿素水解制氨技术流程
CO(NH2)2 + H2O « NH2-COO-NH4 « 2NH3↑ + CO2↑ (1)
尿素水解制氨反应是一个吸热反应,是生产尿素过程的逆反应,反应速率受尿素溶液浓度、反应温度的影响。实际生产所需要的热量,可由蒸汽辅热或电加热提供,以满足水解反应。
尿素水解系统整体流程较为简单,主要设备包括:尿素溶解罐、尿素溶液储罐、水解反应器,尿素溶解泵、尿素溶液输送泵及喷射系统(喷枪)等。把50%(质量分数)的尿素溶液从尿素储罐中通过尿素溶液输送泵输送至水解反应器内。再通过在水解反应器下部设置盘管或电加热热阻,把饱和蒸汽输送进入盘管,使用蒸汽加热水解反应器中的尿素。而加热后的饱和蒸汽不与水解反应器内的尿素溶液混合,通过盘管内部回流冷凝,由疏水箱、疏水泵回收。
一般要求,平衡后在水解反应器内的尿素溶液浓度达到40%~50% (质量分数),溶液温度达到150℃~170℃,水解反应产生的气体和尿素溶液的两相平衡系统的压力达到0.48 MPa~0.6 MPa。
一般可采用单元制或公用制对尿素水解系统进行布置。单元制:每台炉的脱硝系统单独使用一套尿素水解制氨系统,一般布置于锅炉SCR脱硝反应器区域,每台炉均需要设置尿素水解制氨反应器,每个水解反应器配备两台(1运1备)疏水泵、1个疏水箱和两台疏水泵(1运1备)。水解反应器设置废水箱和废水泵用于水解反应器压力泄放及排污,废水箱内溶液将不再返回水解反应器。公用制:多台炉的脱硝系统共同使用一套尿素水解制氨系统,即在尿素溶解车间布置尿素水解系统,一般可设置为一套系统带2~4台炉。公用制的水解反应器间可以互相备用,对于多台炉情况下,推荐采用公用制方式进行布置,该方法在经济性方面或检修维护便利性方面均优于单元制。
2.2. 尿素热解制氨技术(炉外气–气换热器)
如图2所示,根据尿素热解热源的不同,炉外气–气换热器分为高温烟气换热器和电加热器两种形式。炉外换热尿素热解法制氨系统的主要设备包括:尿素溶解泵、尿素溶解罐、输送泵、尿素溶液储罐、计量和分配装置、尿素热解炉、控制阀、高温烟气换热器或电加热器等。计量分配系统就近布置在喷射系统附近锅炉平台上,以焊接或螺栓的形式固定。烟气换热尿素热解工艺和电加热尿素热解工艺均需用到计量分配装置和尿素热解炉,且两个工艺所配套的计量分配装置和尿素热解炉大小、型号和材质一致,烟气换热尿素热解工艺和电加热尿素热解工艺不同的部分是尿素热解热源:烟气换热和电加热。经过计量与分配装置和喷嘴等,尿素溶液进入热解炉内受热分解,生成的NH3、H2O和CO2与稀释空气混合均匀产生氨气浓度小于5% (体积比)的混合气喷入脱硝系统。
(a) 烟气换热器加热热一次风
(b) 电加热器加热热一次风
Figure 2. Technical process of ammonia production by urea pyrolysis method
图2. 尿素热解法制氨技术流程
当接到紧急停机指令时,在不会造成氨体积浓度超过电厂最大事故限值的前提下,系统具有在15至30秒内将氨供应从100%容量削减到0 kg/h的能力。接触尿素溶液的设备及部件应采用SS304不锈钢材料,尿素喷射器采用316 L不锈钢材料(表1)。
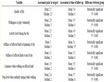
Table 1. Comparison of urea pyrolysis between electric heating and flue gas heat exchanger
表1. 电加热与烟气换热器尿素热解对比 [4] [5]
综合考虑两种加热热源的尿素热解制氨技术的成熟度、可靠性、经济性和节能特性,在烟气换热尿素热解和电加热尿素热解两者中,烟气换热尿素热解工艺优势明显。
2.3. 尿素热解制氨技术(炉内气–气换热器)
气–气换热器的工艺流程如图3所示,在锅炉的低温过热器或低温再热器区布置气–气换热器管束,利用锅炉冷(热)一次风自身的压头将冷(热)一次风送入气–气换热器的蛇形管束中,高温烟气对经蛇形管束的冷风进行加热,使其离开蛇形管束时的温度达到尿素热解所需要的温度(>600℃),并被送入尿素热解炉中,尿素溶液在热解炉中分解产生气态NH3,并喷入脱硝入口烟道中,最后进入SCR反应器发生脱硝还原反应。
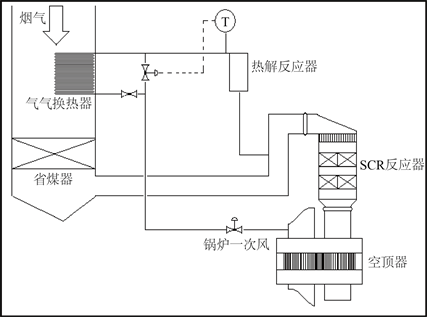
Figure 3. Gas-gas heat exchanger technological process
图3. 气–气换热器工艺流程
炉内气–气换热器尿素热解制氨技术能耗低,尿素热解效率高,系统简单可靠,在技术和经济上有不可比拟的优势。常规尿素热解用高温空气,采用电加热器或管道燃烧器对锅炉热一二次风进行再加热,能耗高,运行成本高。采用气–气换热器方案,除非低负荷烟温特别低,一般不需要对热空气再加热。少数项目因低负荷烟温过低需要配置辅助电加热器时,加热器的功率也很小,相对于常规技术的能耗降低很多。
2.4. 工艺和安全性对比
现就上述筛出的尿素热解和尿素水解制氨技术,对其进行详细论证。表2分析对比了上述这几种SCR脱硝还原剂制备工艺 [6] [7] [8]。
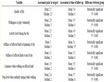
Table 2. Comparison of ammonia production technology by urea hydrolysis and urea pyrolysis technology
表2. 尿素水解制氨技术和尿素热解制氨技术的比较
注:此处尿素水解产品气中NH3体积浓度虽然可达28.5%~37.5%,但因产品气中并不含有氧气等助燃物质,因此不存在爆炸的可能。
3. 结论
综合尿素水解和烟气换热尿素热解的技术和经济性对比,得到以下结论:
1) 电加热尿素热解、烟气换热尿素热解、尿素水解(含催化水解)、尿素直喷制氨技术在原理上、实际应用方面均可行,且有实际改造案例。
2) 电加热尿素热解制氨技术方案电耗大、运行问题多,经济性和稳定性均不佳,故新建机组或改造工程项目不宜采用该方案。
3) 尿素水解制氨技术(含催化水解)和烟气换热尿素热解制氨技术运行稳定、安全性好。可根据上述技术适用条件,针对各厂的实际情况进行选择。
基金项目
国家自然科学基金项目(51976072),清华大学–中国华能集团有限公司基础能源联合研究院项目(U20YYJC01)。
NOTES
*第一作者。