1. 引言
表面自纳米化技术是一种新兴的表面强化技术,其基本原理是通过在材料表面反复施加大应变,使得表层晶粒逐渐细化至纳米级。根据Hall-Petch关系式,材料的强度或硬度随晶粒尺寸的减小而提高。因此,表面的纳米晶可以提高材料表面的硬度和耐磨性。该技术自提出以来已经被广泛应用于钛、铜、铝等各类金属与合金的表面硬化处理当中 [1] [2] [3] [4]。常用的实现表面自纳米化的工艺有表面机械研磨处理(Surface mechanical attrition treatment, SMAT)、高能喷丸(High energy shot peening, HESP)和表面机械碾磨处理(Surface mechanical grinding treatment, SMGT)等 [5] [6] [7]。相比于SMAT和HESP这两种工艺,SMGT具有工艺实现难度低、效率高等优点成为近年来表面自纳米化工艺的研究热点之一。其工艺原理是通过半球形刀头对旋转的材料表面施加外力,使其表面产生剧烈塑性变形,进而生成大量的位错、孪晶、层错等晶体缺陷,最终使得表层粗晶组织逐渐细化至纳米级 [8]。
Ti-6Al-4V (TC4)钛合金具有优良的力学性能、组织稳定性和热稳定性良好等优点,已成为目前应用最广泛的钛合金材料之一。但是TC4钛合金耐磨性能较差的问题也限制了其应用 [9]。SMGT工艺为提高TC4钛合金的耐磨性能提供了一个有效途径。一般研究材料的SMGT工艺往往采用实验法,但钛合金的试验成本较高且试验周期较长。本文采用效率较高、成本较低并且较直观的有限元分析方法,利用Abaqus商业有限元软件将Johnson-Cook本构模型与位错密度演化模型进行耦合,对SMGT过程中钛合金位错密度和晶粒尺寸动态演变进行仿真,研究在SMGT过程中碾磨速度和单道次碾磨深度这两种工艺参数对TC4钛合金表面微观组织的影响规律,对后续的TC4合金SMGT工艺设计和优化具有积极的指导意义。
2. 有限元模型建立及仿真试验参数设定
2.1. Johnson-Cook材料本构模型及相关参数设定
材料的流动应力本构模型是用来描述材料的力学性质,表征材料变形过程中的动态响应的函数。在有限元仿真中材料的宏观组织一般被设定为致密均匀的,材料的流动应力主要受到变形程度、变形速度和变形温度等因素的影响。本文采用的Johnson-Cook流动应力本构模型,该模型可用于描述大应变、高应变速率下金属材料的强度极限 [10],其表达式如式(1)所示:
(1)
式中
为等效流动应力,其值由该公式计算得出;
为等效塑性应变,
为等效塑性应变速率,T为材料的瞬时温度,以上均为有限元仿真计算中的变量;
为参考塑性应变速率,一般根据仿真的加工工艺来确定;
为材料熔点,
为初始温度,一般根据仿真的加工环境温度确定;A、B、C、n和m是材料常数,可根据材料的拉压扭转实验拟合获得。TC4钛合金的Johnson-Cook本构模型相关参数及其意义如表1所示,TC4钛合金的材料性能参数如表2所示。
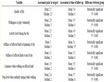
Table 1. Johnson-Cook material flow stress constitutive model parameters of TC4 titanium alloy [11]
表1. TC4钛合金的Johnson-Cook材料流动应力本构模型参数 [11]
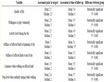
Table 2. Material performance parameters of TC4 titanium alloy [12]
表2. TC4钛合金的材料性能参数 [12]
2.2. 基于位错理论的晶粒演化模型及相关参数设定
Estrin [13] 等人提出了一组微分方程来预测材料大应变速率条件下加工过程中位错密度的演化速率。该方程与在不同应变,应变速率和温度条件下开发的材料本构模型兼容,并且已经适应于具有高应变速率的其他变形过程的建模,例如铜、铝和钛等金属材料的机械加工 [14] [15]。
在该模型中,假定材料在变形过程中形成了位错单元结构,该结构由位错单元壁和单元内芯两个部分组成,并遵守混合规则。模型中区分出不同类型的位错密度:胞内位错(
)和胞壁位错(
),材料在加工过程中两种类型的位错密度演变公式如下所示:
(2)
(3)
式(2)和(3)等号右边三项依次代表弗兰克-里德(Frank-Read)位错源引起的位错增殖、胞内位错向胞壁位错的转化以及动态恢复导致的位错湮灭。其中
代表有效位错源比例因子,
为位错分数,
为常数,n是温度敏感系数,f是胞壁位错的体积分数,b是材料的Burgers向量的大小,d是晶粒尺寸,
和
分别是晶界和晶胞内部的解析剪切应变率,而
是参考解析剪切应变率。该模型假设晶界和晶胞内部的分切应变率与等效剪切应变率相等,即:
(4)
式(4)满足沿着内部和边界之间的界面的应变相容性。解析剪切应变率
可以通过Von Mises应变率
,通过等式(4)来计算,其中M是泰勒因子。
(5)
胞壁位错的体积分数f,总位错密度
和晶粒尺寸d由下式确定:
(6)
(7)
(8)
式(6)中,
是位错胞壁饱和体积分数,
是位错胞壁初始体积分数,
是剪切应变,
是参考剪切应变;式(8)中K为常数。
该模型的参数可以分为两类:一类是有材料自身属性和初始微观组织结构决定的,例如TC4钛合金的初始位错密度、初始晶粒尺寸和伯氏矢量等;另一类是控制材料位错密度在加工过程中演变的参数,如
、
和
等。根据SMGT实验得出的晶粒尺寸数据,本文拟合出这两类位错密度模型参数如表3和表4所示。
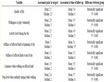
Table 3. Material property parameters
表3. 材料属性参数
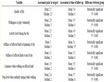
Table 4. Dislocation density model parameters
表4. 位错密度模型参数
2.3. SMGT模型建立及仿真试验参数设定
本文采用Abaqus有限元仿真软件对TC4样品和碾磨刀具进行二维建模。如图1(a)所示,TC4样品模型尺寸为30 mm × 10 mm。碾磨刀具为直径Φ20 mm的半球形刀头,材质为硬质合金材料,其密度ρ = 14,600 kg/m3,弹性模量E = 210 GPa,泊松比v = 0.22。本文运用软件内的用户定义子程序vumat,通过Python语言编程,将位错理论方程与Johnson-Cook材料流动应力本构模型进行耦合,从而实现对TC4钛合金SMGT过程进行有限元模拟。运用Abaqus/Expilict 6.13热–力耦合求解器进行仿真;采用工件固定、刀具移动的方式,在工件底部设置位移约束来限制工件位移如图1(b);设定模拟开始时的环境温度、刀具温度和工件温度均为20℃。表面机械碾磨仿真试验参数如表5所示。
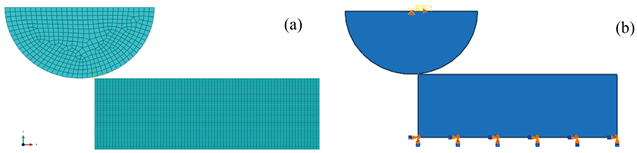
Figure 1. TC4 titanium alloy SMGT modeling: (a) TC4 titanium alloy SMGT two-dimensional model; (b) Model displacement constraints
图1. TC4钛合金SMGT建模:(a) TC4钛合金SMGT二维模型;(b) 模型位移约束
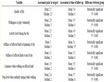
Table 5. TC4 titanium alloy SMGT simulation test parameters
表5. TC4钛合金SMGT仿真试验参数
3. 仿真结果分析与讨论
图2(a)~(c)为TC4钛合金SMGT仿真示意图,图中的彩色云图代表样品在SMGT过程中的受力情况以及经过SMGT加工后材料的残余应力。半球形碾磨刀头以如图2(a)所示的方向前进,TC4钛合金样品在刀头的挤压下先发生弹性变形,当刀头施加给材料的应力超过了材料的弹性极限时,材料发生塑性流动;在刀头前进过程中刀头前端出现材料的堆积,随着刀头的继续前进,前端堆积的材料一部分会从刀头下方流动,另一部分继续保留在刀头前端,如图2(b)放大区域所示;当刀头到达运行终点后退刀,重新开始下一道次的碾磨,如图2(c)所示。图2(d)是经过SMGT加工后材料残余应力云图,其中黑色方框1处是材料碾磨变形层,而方框右侧红色云图应力集中区域是由于材料在碾磨过程中材料流动堆积所导致的。为了对比不同工艺参数条件下材料碾磨层的残余应力和应变情况,选取了图2(d)黑色方框1处的64个单元作为分析对象。
3.1. 残余应力场分析
在SMGT过程中样品表面强烈塑性变形不仅导致了晶粒细化还会在材料表层保留一定的残余压应力,而残余压应力有利于提高材料的抵抗裂纹扩张的能力 [16],图3为采用9组不同工艺参数的TC4钛合金SMGT残余应力场仿真结果,左侧图例中S. Mises代表Von Mises 应力,是基于剪切应变能的一种等效应力;Avg75%代表当节点相对变化率小于该值时,该节点的结果被平均,是一种平滑云图的算法。由图3可以观察到样品材料经过SMGT后在碾磨层下方和刀头行程终点前端材料堆积处都有较大的残余应力,其中最大值出现在图3(a)黑色箭头所指处,为1.043 × 109Pa。选取图2(d)所示的64个碾磨变形层单元格,计算出9组SMGT工艺参数条件下碾磨层的平均残余应力,如图4所示,由图可知在工艺参数为碾磨速度v = 0.1 m/s,单道次碾磨深度D = 10 μm/pass条件下碾磨层的平均残余值应力最大,为7.233 × 108 Pa。结合图3和图4的仿真结果,可以得出以下结论:当碾磨速度v一定时,单道次碾磨深度D越大,样品碾磨层的平均残余应力越小;当单道次碾磨深度D一定时,碾磨速度v与样品碾磨层的平均残余应力同样呈现负相关性。
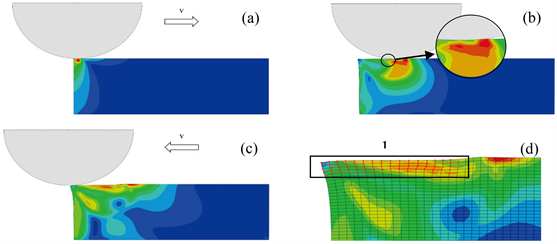
Figure 2. Finite element simulation of SMGT process of TC4 titanium alloy: (a) Grinding tool cut in; (b) Single pass grinding end point; (c) Retract; (d) Selected 64 grinding deformation layer units
图2. 有限元模拟TC4钛合金SMGT过程:(a) 碾磨刀头切入;(b) 单道次碾磨终点;(c) 碾磨结束退刀;(d) 选取的64个碾磨变形层单元
(a) v = 0.1 m/s, D = 10 μm/pass; (b) v = 0.1 m/s, D = 20 μm/pass; (c) v= 0.1 m/s, D = 30 μm/pass; (d) v = 0.2 m/s, D = 10 μm/pass; (e) v = 0.2 m/s, D = 20 μm/pass; (f) v= 0.2 m/s, D = 30 μm/pass; (g) v = 0.3 m/s, D = 10 μm/pass; (h) v = 0.3 m/s, D = 20 μm/pass; (i) v= 0.3 m/s, D = 30 μm/pass.
Figure 3. The residual stress field cloud diagram of SMGT simulation results with different process parameters, grinding speed v (m/s), Single pass grinding depth D (μm/pass)
图3. 不同工艺参数SMGT仿真结果残余应力场云图,碾磨速度v (m/s),单道次碾磨深度D (μm/pass)
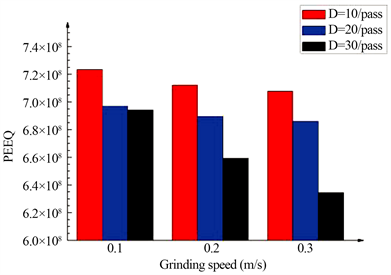
Figure 4. Average residual stress of the grinded layer after SMGT with different process parameters
图4. 不同工艺参数SMGT后碾磨层平均残余应力
3.2. 应变场分析
图5是9组不同工艺参数条件下TC4钛合金经过SMGT后的等效应变场云图,由图5可知经过SMGT后材料的等效塑性应变主要集中于碾磨区域表层以下。如图5(a)所示,当碾磨速度v = 0.1 m/s,单道次碾磨深度D = 10 μm/pass条件下得到的等效应变值最大,达到了2.105;而碾磨速度v = 0.3 m/s,单道次碾磨深度D = 30 μm/pass条件下得到的等效应变量最小,仅为0.412,如图5(i)所示。横向对比图5中碾磨速度v相同的条件下的应变场分布图,如图5(a)、图5(b)和图5(c),可以得到单道次碾磨深度D的大小与TC4钛合金的应变程度成负相关性;而与应变区域范围成正相关性的规律,即在碾磨速度v相同的条件下单道次碾磨深度D越大,材料变形层的等效塑性应变越小,但是材料变形层的应变区域却随单道次碾磨深度D的增大而增大。纵向对比图5中单道次碾磨深度D相同的条件下的应变场分布图,如图5(a)、图5(d)和图5(g),可知碾磨速度v的大小也与TC4钛合金的应变程度成负相关性,而与应变区域范围成正相关性的规律,这与横向对比的影响规律相同。为了更直观地对比不同工艺参数对材料变形层等效应变大小的影响规律,选取如图2(d)所示的64个单元格,提取出9组不同工艺参数SMGT仿真等效应变数据求平均值,如图6所示,图中横坐标是碾磨速度v,纵坐标是平均等效塑性应变值。由图可以发现:在碾磨速度v相同的条件下,等效应变值随单道次碾磨深度D的增大而减小;在单道次碾磨深度D相同的条件下,等效应变值随碾磨速度v的增大而减小。
3.3. 位错密度和晶粒尺寸演变分析
图7(a)和图7(b)为第1组工艺参数条件下通过位错密度方程计算得出的经过SMGT后材料变形层的位错密度和晶粒尺寸仿真云图。选取如图2(d)中碾磨层的64个单元格,可以得到在SMGT过程中碾磨层的平均位错密度和平均晶粒尺寸演化数据如图8所示。图中横坐标为碾磨道次,纵坐标为位错密度或晶粒尺寸,可以观察到TC4钛合金在SMGT过程中位错密度随碾磨道次的增加而逐渐增大,晶粒则逐渐细化,且在总碾磨深度不变的条件下,前1/3的碾磨道次时位错密度的变化量不大,后2/3的碾磨道次时位错密度才逐渐提高。图8(a)和图8(b)是在单道次碾磨深度D = 10 μm/pass,碾磨速度v = 0.1 m/s、0.2 m/s和0.3 m/s的条件下得到的平均位错密度和平均晶粒尺寸演变仿真结果,经过表面机械碾磨后TC4表面变形层的平均位错密度分别为4.16 × 1015 mm−2、3.72 × 1015 mm−2和3.39 × 1015 mm−2,平均晶粒尺寸分别为27.3 nm、28.8 nm和30.2 nm。通过图8可知,本次模拟试验中都存在着相似的规律,即在总碾磨深度一定的条件下,单道次碾磨深度D和碾磨速度v越小则材料碾磨层的平均位错密度越大,平均晶粒尺寸也越小,该结论与丁利强 [17] 对铝合金高速切削模拟试验中得到的结论相同。在工艺参数为v = 0.1 m/s,D = 10 μm/pass的条件下仿真结果中平均位错密度最大,达到4.16 × 1015 mm−2,平均晶粒尺寸为27.3 nm,而工艺参数为v = 0.3 m/s,D = 30 μm/pass时由图8(f)所示,其平均位错密度最小,为1.78 × 1014 mm−2,平均晶粒尺寸为131.8 nm,比最大位错密度低一个数量级。碾磨速度为v = 0.1 m/s和0.2 m/s的6种模拟预测结果晶粒尺寸均在100 nm以下。根据仿真结果分析,TC4钛合金SMGT工艺参数在v = 0.1 m/s,D = 10 μm/道次时,晶粒细化程度最高。综上所示,单道次碾磨深度D和碾磨速度v对TC4钛合金表面纳米晶层的形成都有影响,且呈负相关性。
(a) v = 0.1 m/s, D = 10 μm/pass; (b) v = 0.1 m/s, D = 20 μm/pass; (c) v = 0.1 m/s, D = 30 μm/pass; (d) v = 0.2 m/s, D = 10 μm/pass; (e) v = 0.2 m/s, D = 20 μm/pass; (f) v = 0.2 m/s, D = 30 μm/pass; (g) v = 0.3 m/s, D = 10 μm/pass; (h) v = 0.3 m/s, D = 20 μm/pass; (i) v = 0.3 m/s, D = 30 μm/pass.
Figure 5. Equivalent strain field cloud diagram of SMGT simulation results with different process parameters, grinding speed v (m/s), single pass grinding depth D (μm/pass)
图5. 不同工艺参数SMGT仿真结果等效应变场云图,碾磨速度v (m/s),单道次碾磨深度D (μm/pass)
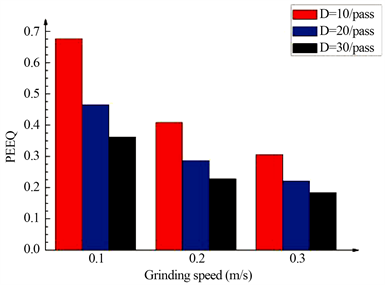
Figure 6. The average equivalent strain of the grinding layer after SMGT with different process parameters
图6. 不同工艺参数SMGT后碾磨层平均等效应变
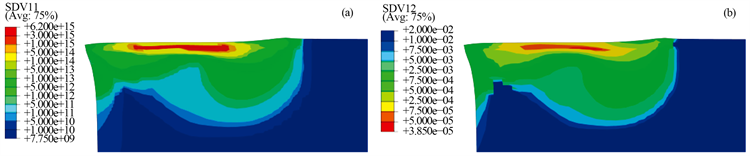
Figure 7. The process parameter is v = 0.1 m/s, D = 10 μm/pass SMGT simulation cloud diagram: (a) Dislocation density; (b) Grain size
图7. 工艺参数为v = 0.1 m/s,D = 10 μm/pass时SMGT仿真云图:(a) 位错密度;(b) 晶粒尺寸
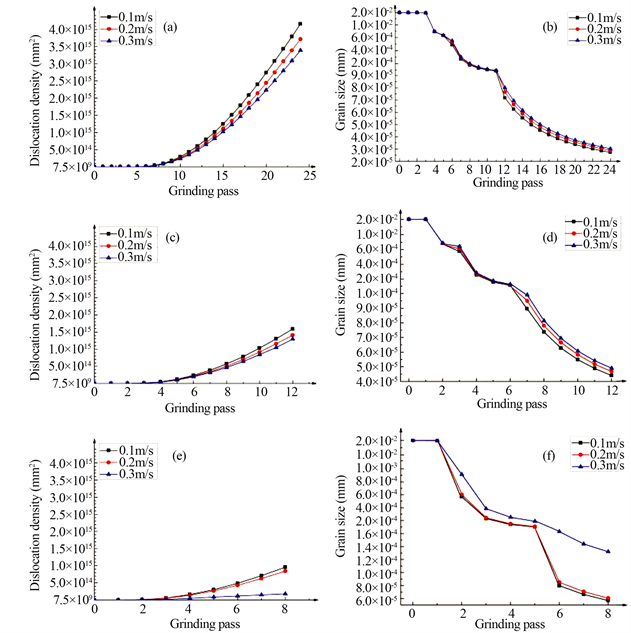
Figure 8. Evolution of dislocation density and grain size in SMGT process of TC4 titanium alloy: (a) (b) Single pass grinding depth D = 10 μm/pass; (c) (d) Single pass grinding depth D = 20 μm/pass; (e) (f) Single pass grinding depth D = 30 μm/pass
图8. TC4钛合金SMGT过程中的位错密度和晶粒尺寸演化:(a) (b) 单道次碾磨深度D = 10 μm/pass;(c) (d) 单道次碾磨深度D = 20 μm/pass;(e) (f) 单道次碾磨深度D = 30 μm/pass
4. 结论
建立了适合TC4钛合金表面机械碾磨模型,实现了材料变形层位错密度和晶粒尺寸在碾磨过程中动态演化的仿真模拟。通过对9组不同工艺参数条件下的仿真结果进行对比得到了以下结论:
1) 碾磨速度和单道次碾磨深度对表面纳米强化层晶粒的细化均有影响,在相同总碾磨深度速度的条件下碾磨越慢、单道次碾磨深度越浅,则表面纳米强化层的晶粒细化越高。
2) 该模型成功模拟了表面机械碾磨处理过程中碾磨层的位错密度和晶粒尺寸的演变过程,为表面机械碾磨处理在钛合金上的应用提供了一定的参考。
基金项目
国家自然科学基金(项目号:51604112),湖南省自然科学基金(项目号:2017JJ3089),湖湘青年英才(项目号:2019RS2067),湖南省战略性新兴产业科技攻关与重大科技成果转化项目(项目号:2019GK4048)和湘潭市企业科技特派员项目。
NOTES
*通讯作者。