1. 引言
铅和锌是重要的有色金属元素,在国民生产经济中扮演着不可或缺的角色,广泛应用在冶金、电池、机械制造、医药等领域 [1] [2]。21世纪后,随着国际铅锌市场规模的扩大以及消费水平的提高,铅锌生产量稳步上升,其增量主要来自于我国 [3]。我国铅锌行业快速发展的同时,大量冶炼废渣的排放和积累导致资源浪费严重,环境问题突出。
我国铅锌原料过多的依赖进口资源,铅锌精矿对外依存度保持在20%~30% [4]。这将极大限制我国铅锌行业的快速发展,在不稳定的市场环境下会增加矿产资源供应风险。另一方面,我国铅锌行业对于资源的综合回收利用率较低。我国每年产生的含锌铅基废渣高达数百万吨,历史堆存过亿吨,造成大量的资源浪费 [5]。
随着铅锌消费量的增加,原生铅锌资源的含量和品位正在下降,含锌铅基固废作为二次资源,不仅可以回收其中的铅、锌、银等有价金属,还可以减轻对环境的压力。火法冶金具有对原料适应性强的优点,基本可以实现冶炼废渣的无害化和减量化,对环境危害的程度大大降低,依旧是工业应用的主要技术。相对传统火法回收方法,采用富氧熔炼技术处理铅锌渣,具有熔炼效率高、余热回收效率高、SO2利用率高等优点 [6]。
2. 实验研究
2.1. 实验原料
本实验所用矿样是由西北某铅锌冶炼厂提供的同一批次的铁矾渣,为获得铁矾渣元素的准确含量,进行化学元素分析,结果见表1。
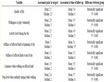
Table 1. Chemical element analysis of iron vitriol slag/wt%
表1. 铁矾渣化学元素分析/wt%
采用X射线衍射分析了铁矾渣中主要的物相组成,如图1所示,铁矾渣的主要衍射峰为黄钾铁矾(KFe3(SO4)2(OH)6)、锌铁尖晶石(ZnFe2O4)、石英(SiO2)、铅砷硫化物(PbAs2S4),成份复杂,多种相态混合在一起。
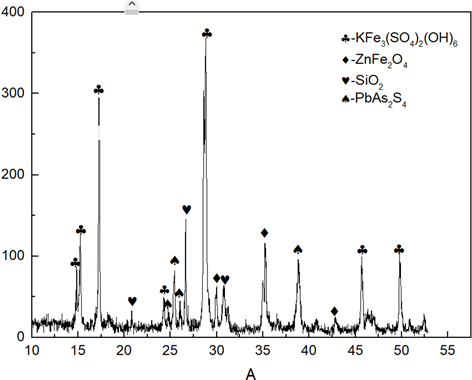
Figure 1. XRD pattern of iron vitriol slag
图1. 铁矾渣的XRD图谱
通过矿物解离仪MLA进一步分析检测元素的赋存状态,如表2所示。可见铁主要赋存在铁矾中,占比高达89.26%,其余铁则主要以褐赤铁矿、锌铁尖晶石形式存在。铅赋存于多种不同的化合物中,主要赋存在铁矾、铅矾、石膏、玻璃体中,其中铅矾结构致密,这很可能会影响铅的高温挥发率。锌主要赋存于铁矾、锌铁尖晶石、闪锌矿中,锌铁尖晶石结构致密。
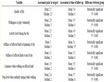
Table 2. MLA Phase analysis of iron vitriol slag/wt%
表2. 铁矾渣MLA物相分析/wt%
银通过化学物相分析,主要赋存在硫化物、难溶矿物的包裹银中,少部分以银单质存在,由于银的物相比较复杂,含量又特别低,给提银工作带来很多困难。
2.2. 实验设备与过程
本实验原料为铁矾渣,还原剂采用石墨电极碳粉,其碳含量为99.92%,熔剂为分析纯氧化钙、二氧化硅。实验装置如图2所示,设备型号为QSG-12-13,额定电压300 V,额定功率12 Kw,加热元件为硅碳棒,额定工作温度1350℃,通过铂铑热电偶从外部接触坩埚侧壁来测量温度,控温精度±5℃。实验采用内径120毫米、高200毫米的石墨坩埚作为反应器,喷枪采用刚玉管。
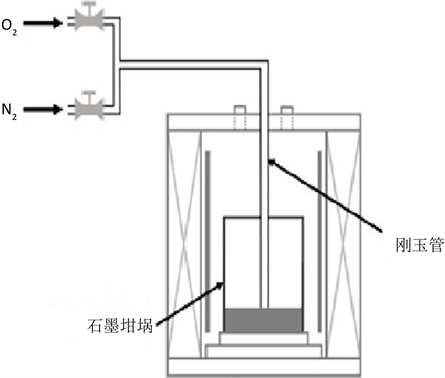
Figure 2. Schematic diagram of experimental equipment
图2. 实验装备示意图
干燥的铁矾渣与石墨粉以及熔剂(CaO和/或SiO2)混合均匀,装入石墨坩埚中,在立式电阻炉中在一定温度下熔化60 min。用刚玉管吹入一定压力的混合气体(一定比例的N2 + O2),悬浮吹入熔渣中,反应一段时间,并在高温下静置3分钟。实验结束后,将坩埚从炉中取出,在空气中快速冷却。实验尾渣取样后采用化学分析法测定尾渣中金属铅、锌、银含量。
3. 试验结果及讨论
基于碳热还原实验,采用单因素条件试验法,考察铁硅比、钙硅比、反应温度、配碳量、富氧浓度、反应时间六个因素对铁矾渣富氧强化挥发熔炼过程铅、锌挥发率、渣的减量化及尾渣银含量的影响。
3.1. 铁硅比对金属挥发率的影响
称取1000 g铁矾渣,20 g碳粉,配入SiO2调节炉渣的铁硅比。实验条件为:钙硅比为0.4,反应温度1250℃,富氧浓度40% vol,反应时间1 h。铁硅比对铅、锌挥发率、渣的减量化及尾渣银含量的影响如表3、图3所示。
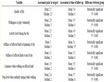
Table 3. Reduction of slag and metal content of tailings with different ratios of iron to silicon
表3. 不同铁硅比渣的减量率及尾渣金属含量/%
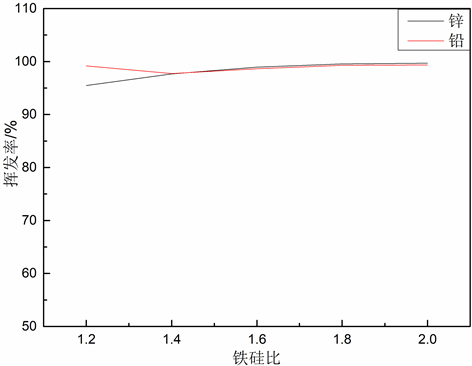
Figure 3. The effect of iron to silicon ratio on the volatilization rate of lead and zinc
图3. 铁硅比对铅、锌挥发率的影响
由表3可知,铁硅比的越大,熔炼渣的减量化效果越显著,主要的原因是,随铁硅比的增大,所需配的熔剂减少,尾渣量随之减少。另外,尾渣的金属含量随着铁硅比的升高而减小。由图3金属挥发率结果可见,铁硅比增大,有利于铅、锌的挥发,当铁硅比为2的时候,锌、铅的挥发率分别为99.68%、99.36%。原料的铁硅比为2.6,铁硅比越接近2.6意味着所需添加SiO2的量越少,熔剂成本越低。因此,本次实验确定炉渣铁硅比的最优值为2。
3.2. 钙硅比对金属挥发率的影响
称取1000 g铁矾渣,20 g碳粉,配入CaO调节炉渣的钙硅比。实验中,铁硅比为2,反应温度1250℃,富氧浓度40% vol,反应时间1 h。考察钙硅比对铅、锌挥发率、渣的减量化及尾渣银含量的影响,结果如表4、图4所示。
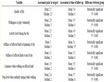
Table 4. Reduction of slag and metal content of tailings with different ratios of calcium to silicon
表4. 不同钙硅比渣的减量率及尾渣金属含量/%
由表4可知,随着钙硅比的减小,渣的减量化效果显著,主要的原因是,钙硅比越小,所需配的熔剂越少,尾渣量越少。在钙硅比0.4时,尾渣含银量最少,为52.84 g/t,锌、铅含量也相对较少。由图4金属挥发率的结果可见,铅、锌的挥发率基本不受钙硅比的影响,在钙硅比为0.4的时候,锌、铅的挥发率分别为99.36%、99.11%,此时渣的减量率达到最高。因此,本次实验确定炉渣钙硅比的最优值为0.4。
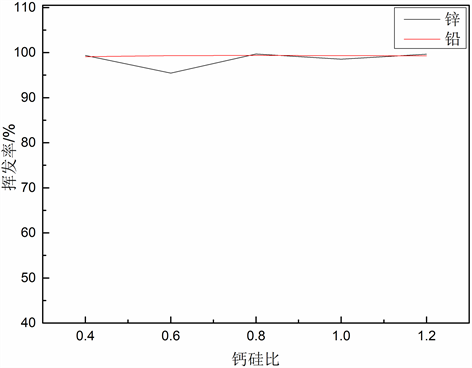
Figure 4. The effect of calcium to silicon ratio on the volatilization rate of lead and zinc
图4. 钙硅比对铅、锌挥发率的影响
3.3. 温度对金属挥发率的影响
称取1000 g铁矾渣,20 g碳粉,在铁硅比为2,钙硅比为0.4,富氧浓度40% vol,反应时间60 min条件下,考察不同温度对铅、锌挥发率、渣的减量化、及尾渣银含量的影响,结果如表5、图5所示。
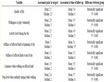
Table 5. Reduction of slag and metal content of tailings with different temperatures
表5. 不同温度渣的减量率及尾渣金属含量/%
由表5可知,随着温度的升高,渣的减量化效果显著。升高温度,有助于金属硫酸盐的分解和金属的还原挥发,挥发量越高,尾渣量越少。另外,尾渣的金属含量随着温度的升高而减少,表明尾渣的危害性越小。金属挥发率的结果由图5可见,熔炼温度对铅、锌的挥发率有着重要的影响。当温度小于1250℃时,铅、锌的挥发率随着温度升高均有较大幅度的提升,在1250℃时,锌、铅的挥发率分别为99.32%、99.06%。当温度增加到为1300℃时,锌、铅的挥发率增幅较小,分别为99.61%、99.73%。温度过高会消耗过多的能源,降低熔炼炉寿命。同时熔炼温度过低,会增大渣的粘度,进而降低熔渣流动性,减缓金属氧化物的还原速度,导致金属挥发速度及挥发率降低。综合考虑,本实验确定最优熔炼温度为1250℃。
3.4. 碳量对金属法挥发率的影响
称取1000 g铁矾渣,在铁硅比为2,钙硅比为0.4,熔炼温度为1250℃,富氧浓度40% vol,反应时间60 min条件下考察配入不同碳粉量,考察不同配碳量对铅、锌挥发率、渣的减量化及尾渣银含量的影响,结果如表6、图6所示。
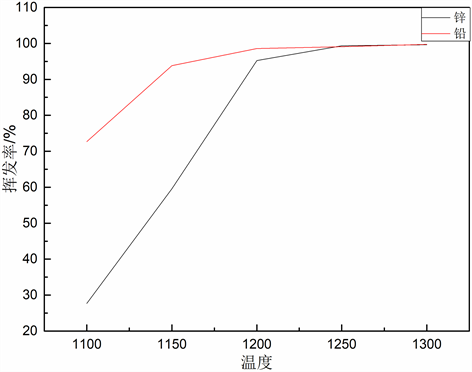
Figure 5. The effect of temperature on the volatilization rate of lead and zinc
图5. 温度对铅、锌挥发率的影响
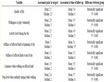
Table 6. Reduction of slag and metal content of tailings with different carbon content
表6. 不同配碳量下渣的减量率及尾渣金属含量/%
由表6可知,随着配碳量的增加,渣的减量化效果越显著。在强还原气氛下,有助于金属硫酸盐的还原分解和金属的还原挥发。因此,配碳量的升高,挥发量越高,尾渣量越少。尾渣的金属含量随着配碳量的升高而减少,尾渣的危害性越小。金属挥发率的结果由图6可见,当配碳量为6 wt%时,锌、铅的挥发率分别为99.39%、98.91%,达到最高值,但是尾渣中的银含量为141.33 g/t,说明银得不到有效的回收。在配碳量为10 wt%时,锌、铅的挥发率分别为99.34%、98.77%,尾渣含银量最少,为12.45 g/t。这是由于在碳量高的存在下,银的硫酸盐以及氧化物得以还原分解成单质银,富集在炉底富铁层。综合考虑,本实验确定最优配碳量为10 wt%。
3.5. 富氧浓度对金属挥发率的影响
称取1000 g铁矾渣,铁硅比为2,钙硅比为0.4,熔炼温度为1250℃,配碳量为10% wt,反应时间60 min。分别测定铅、锌的挥发率,改变富氧浓度,考察不同富氧浓度对铅、锌挥发率、渣的减量化及尾渣银含量的影响,结果如表7、图7所示。
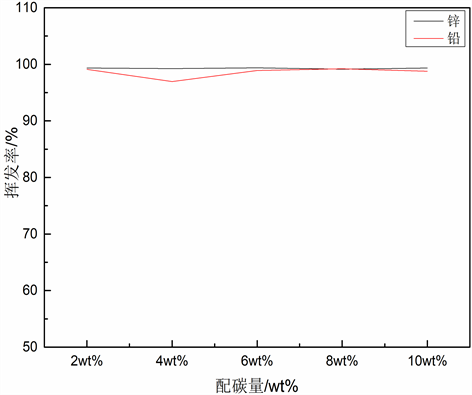
Figure 6. The effect of carbon content on the volatilization rate of lead and zinc
图6. 配碳量对铅、锌挥发率的影响
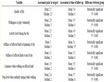
Table 7. Reduction of slag and metal content of tailings with different oxygen enrichment concentrations
表7. 不同富氧浓度下渣的减量率及尾渣金属含量/%
由表7可知,富氧浓度40% vol以上,渣的减量率稳定在50%以上。铁矾渣中,还有金属硫化物,富氧有利于促进硫化物转变成氧化物,使其容易被还原挥发。因此,在较高富氧浓度下,有利于金属硫化物的氧化还原挥发,尾渣量相应的就少一些。富氧浓度在40%~60% vol,尾渣中银的含量维持在12 g/t左右,铅、锌含量更低,表明尾渣的危害性比较小。但是,在富氧浓度70% vol时,尾渣中银的含量上升至175.12 g/t,说明大量的银得不到回收利用。这是因为,富氧浓度过大,提高了熔渣中的氧势,过多的消耗碳,使还原剂减少,导致银的还原率降低,无法沉降或者挥发。
金属挥发率的结果由图7所示,锌、铅的回收率随着富氧浓度呈稳步上升的趋势,锌、铅的发挥率由富氧浓度30% vol时的98.92%、97.84%,上升到富氧浓度70% vol时的99.62%、99.15%。在一定范围提高富氧浓度,可以使铅、锌的挥发率都维持在比较高的水平。一方面是金属硫化物的氧化,易于被还原挥发。另一方面,氧气可以和碳反应形成CO搅拌熔体,加快熔体的传质速度,有利于还原反应的发生。富氧浓度在40% vol时,锌、铅的挥发率分别为99.34%、98.77%,进一步提高富氧浓度,铅、锌的挥发率得不到大幅度的提升,渣的减量率增加幅度也很小,综合考虑,本实验确定最优富氧浓度为40% vol。
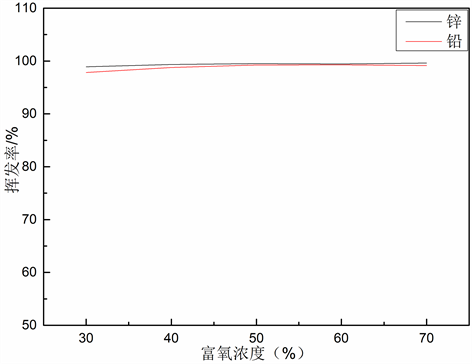
Figure 7. The effect of enriched oxygen concentration on the volatilization rate of lead and zinc
图7. 富氧浓度对铅、锌挥发率的影响
3.6. 反应时间对金属挥发率的影响
称取1000 g铁矾渣,铁硅比为2,钙硅比为0.4,熔炼温度为1250℃,配碳量为10% wt,富氧浓度为40% vol。分别测定铅、锌的挥发率,改变通气反应时间,考察不同反应时间对铅、锌挥发率、渣的减量化及尾渣银含量的影响,结果如表8、图8所示。
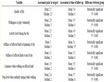
Table 8. Reduction of slag and metal content of tailings with different reaction times
表8. 不同反应时间渣的减量率及尾渣金属含量/%
由表8可知,整体上随着反应时间的延长,渣的减量化效果越明显。随着反应时间的延长,渣中的硫酸盐分解更彻底,尾渣量相应的就少一些。反应时间60 min后,渣的减量基本稳定,此时,尾渣中银的含量达到最低12.45 g/t。而反应70 min后,可能沉在炉底的银又溶解在上层尾渣中,导致尾渣中的银含量上升。
由图8可知,在反应时间30~70 min,锌、铅挥发率整体上升,锌、铅的挥发率分别由反应30 min的97.85%、96.94%,上升到60 min的99.34%、98.77%,而70 min后不再上升。这是因为,随着反应时间的延长,渣中的易挥发组分挥发接近完成。综合考虑,本实验确定最优的反应时间为60 min。
4. 结论
1) 铁矾渣的物相比较复杂,以铁矾为主,其次还有石英、含铅石膏、锌尖晶石、软锰矿、玻璃体矿物,各相态之间相互包覆、粘结,铅、锌、银等有价元素赋存状态复杂。
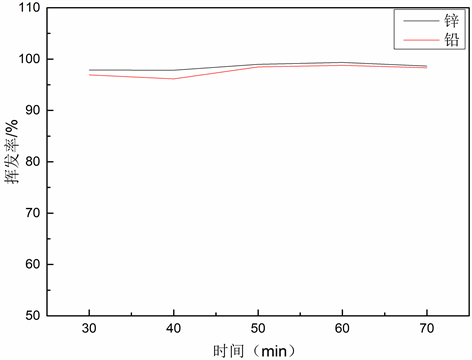
Figure 8. The effect of reaction time on the volatilization rate of lead and zinc
图8. 反应时间对铅、锌挥发率的影响
2) 铁硅比、钙硅比、温度、配碳量、富氧浓度、反应时间对渣的减量化、尾渣银的含量均有比较大的影响:高铁硅比、低钙硅比、高温、高碳、富氧、反应时间延长,均能提高渣的减量率;高温、高碳量能较大幅度降低尾渣中银的含量,富氧浓度在40%~60% vol能使尾渣中的银含量维持在12 g/t左右的较低含量,富氧熔炼60 min最有效的降低尾渣银的含量。
3) 温度对铅、锌挥发率影响最大,温度为1250℃时,铅、锌的挥发率稳定在97%~99.6%之间。
4) 最优条件下:铁硅比为2、钙硅比为0.4,还原温度为1250℃,配碳量为10 wt%,富氧浓度40% vol,反应时间为60 min,锌、铅的挥发率分别为99.34%、98.77%、渣的减量率达到51.65%,尾渣银含量降低为12.45 g/t。
5) 采用富氧还原挥发熔炼工艺,有利于铅、锌金属的挥发、降低尾渣中的银含量。一方面,有利于渣中的金属硫化物氧化,从而可以被还原挥发。另一方面,喷吹富氧,自身带有动能,和固体碳氧化成气体CO,进一步搅动熔体,加快传质速度,促进铅、锌、银等金属化合物的反应。
致谢
本研究工作得到了国家重点研发计划(2019YFC1907303)的资金支持,以及戴曦老师的悉心指导,非常感谢。
基金项目
本研究工作得到了国家重点研发计划(2019YFC1907303)的资金支持。
参考文献