1. 引言
传动轴是汽车传动系统的关键部件之一,其扭转强度等机械性能直接关系到汽车的安全性与稳定性,对整个汽车的动力性能起到重要作用 [1] [2] [3]。传动轴的主要作用就是将发动机总成的动力和旋转运动传递出来,在传动过程中会受到较大扭矩,会产生较大的应力应变。而且在汽车系统运行过程中,快速启动、急刹车、急转弯等复杂工况对传动轴的扭转强度提出了更高的要求。为了降低研发成本,缩短研发周期,现在利用CAE软件在设计阶段评估传动轴强度以及测试过程中分析传动轴失效原因已经成为当今趋势。
国内外学者在传动轴性能方面进行了大量研究,主要集中在疲劳寿命、静力学强度和结构优化等方面。国内,王肖英、习伟博、王成明 [4] [5] [6] 等人主要对汽车传动轴的疲劳强度进行了大量研究,主要采用试验与仿真分析相结合的手段,为强度和可靠性的分析提供数据支撑;而马叶叶、张小红 [7] [8] 等人基于强度仿真分析结果,对传动轴薄弱点进行了结构优化。国外,研究主要集中在复合材料传动轴的疲劳性能和轻量化方面;S. A. Mutasher等人 [9] 主要通过试验研究复合材料传动轴的弯曲疲劳性能;Valavan, D. [10] 主要进行碳纤维增强传动轴的设计和性能分析。
本文基于Ansys Workbench平台对重型卡车汽车的传动轴系统进行扭转强度分析,得到不同工况下的传动轴的应力分布,分析在扭转作用下传动轴各部件的应力分布规律,找到传动轴强度相对薄弱处,并与实际试验结果进行对照,验证了传动轴有限元模型的准确性,并根据仿真分析结果提出了传动轴的结构优化建议。
2. 理论基础
2.1. 结构计算模型
传动轴结构模型计算方程即为结构动力学运动方程 [11],数学表达式为:
(1)
式中,M、C、K分别为结构的质量阵、阻尼阵及刚度阵;
、
、
分别为随时间变化的加速度向量、速度向量及位移向量;P(t)为作用在叶片上面的时变载荷。
2.2. 有限元计算模型
在有限元计算中,结构都是由三维单元构成的,而本研究中三维单元主要指四面体单元和六面体单元。结构的强度计算均是基于单元刚度矩阵进行的,单元刚度矩阵数学表达通式为:
(2)
式中,[B]单元集合矩阵,[D] = E为单元弹性矩阵,[ke]为单元刚度矩阵,V为单元体积。
3. 传动轴扭转强度有限元分析
3.1. 有限元模型建立
重型卡车传动轴主要由突缘叉、花键轴、滑动套、万向节叉、万向十字节、卡簧等零部件构成,传动轴整体装配图图和坐标系如图1所示。其中突缘叉、花键轴材料为45钢,滑动套、万向节叉材料为40钢,万向十字节材料为20 Cr,卡簧为65 Mn,各部件材料见表1。
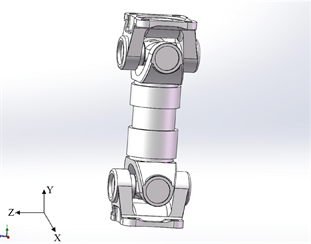
Figure 1. Assembly drawing of drive shaft
图1. 传动轴装配图
因传动轴主要关注部件为突缘叉、花键轴、万向节叉、万向十字节、滑动套,故对其他非主要零部件进行简化处理:(1) 删去滚针轴承中的滚针,填充滚针轴承内外圈间隙;(2) 对花键轴、滑动套等零部件的小孔、倒角、圆角进行简化处理。将简化处理后的几何模型导入workbench中进行网格划分,设定网格大小为1 mm,单元类型为四面体单元,生成网格,传动轴模型有限元单元节点数为1705230个,有限元单元网格数为838720个,网格模型具体见图2。
3.2. 边界条件设定
因重型卡车传动轴扭矩的传递路径为突缘叉–万向十字节–万向节叉–滑动套–花键轴–滑动套–万向节叉–万向十字节–突缘叉,在启动、急刹车等极端情况下,一侧的突缘叉可能被卡死,因此考虑到严酷工况,本文对传动轴进行扭转强度分析时将其中一个突缘叉的连接面进行固定约束,如图3所示,扭矩施加在花键轴和滑动套上。具体工况有以下三种:(1) 万向节转角0度时,转矩施加在花键轴和滑动套上,力矩选用总成公称扭矩668 N∙M,如图4所示;(2) 万向节绕Z轴转角15度时,转矩施加在花键轴和滑动套上,力矩选用总成公称扭矩668 N∙M,如图5所示;(3) 万向节绕X轴转角15度时,转矩施加在花键轴和滑动套上,力矩选用总成公称扭矩668 N∙M,如图6所示。
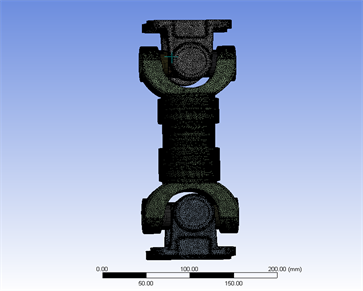
Figure 2. Mesh model of the drive shaft
图2. 传动轴网格模型
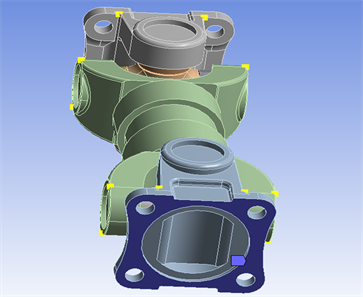
Figure 3. Connection surface constraint of flange fork
图3. 突缘叉连接面约束

Figure 4. Torque application under working condition 1
图4. 工况1转矩施加
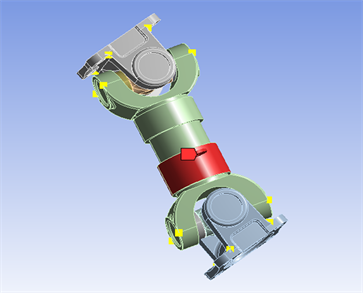
Figure 5. Torque application under working condition 2
图5. 工况2转矩施加
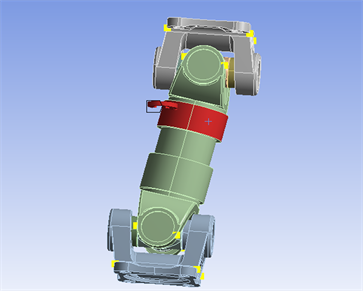
Figure 6. Torque application under working condition 3
图6. 工况3转矩施加
3.3. 计算结果与分析
1) 工况1
万向节转角0度时,传动轴的受力分析结果如图7~11所示。其中等效应力最大处位于万向十字节与其端部轴承过渡处,最大应力为169 MPa,如图11所示,因万向十字节的材料为20 Cr,屈服强度为540 MPa,安全系数为540/169 = 3.20;而万向节叉处最大应力处位于与万向十字节相连处,值为130 MPa,其材料为40钢,屈服强度为335 MPa,安全系数为335/130 = 2.58;突缘叉处最大应力位于与万向十字节相连处,值为120 MPa,其材料为45钢,屈服强度为355 MPa,安全系数为2.96,如表2所示。
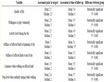
Table 2. Safety factor of each component under working condition 1
表2. 工况1各部件安全系数
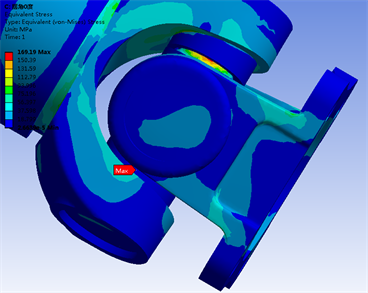
Figure 8. Enlarged view of maximum stress
图8. 应力最大位置放大图
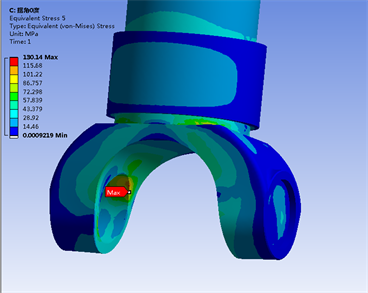
Figure 9. Force diagram of universal joint fork
图9. 万向节叉受力图
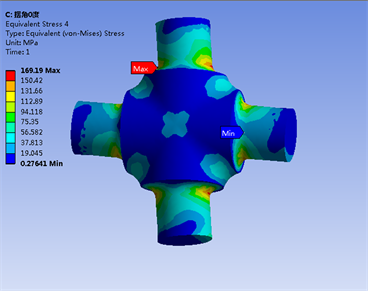
Figure 11. Force diagram of universal cross shaft
图11. 万向十字节受力图
2) 工况2
急转弯时,万向节绕Z轴转角15度时,传动轴的受力分析结果如图12~16所示。其中整体应力最大处位于万向十字节与其端部轴承过渡处,最大应力为169 MPa,如图16所示,因万向十字节的材料为20Cr,屈服强度为540 MPa,安全系数为540/169 = 3.20;而万向节叉处最大应力处位于与万向十字节相连处,值为128 MPa,其材料为40钢,屈服强度为335 MPa,安全系数为335/128 = 2.62;突缘叉处最大应力位于与万向十字节相连处,值为122 MPa,其材料为45钢,屈服强度为355 MPa,安全系数为2.91,具体见表3。
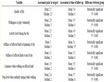
Table 3. Safety factor of each component under working condition 2
表3. 工况2各部件安全系数
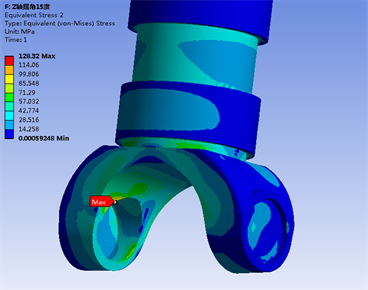
Figure 14. Force diagram of universal joint fork
图14. 万向节叉受力图
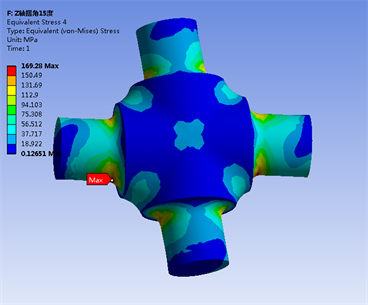
Figure 16. Force diagram of universal cross shaft
图16. 万向十字节受力图
3) 工况3
颠簸路面行驶时,万向节绕X轴转角15度时,传动轴的受力分析结果如图17~21所示。其中整体应力最大处位于万向十字节与其端部轴承过渡处,最大应力为168 MPa,如图21所示,因万向十字节的材料为20 Cr,屈服强度为540 MPa,安全系数为540/168 = 3.21;而万向节叉处最大应力处位于与万向十字节相连处,值为128.5 MPa,其材料为40钢,屈服强度为335 MPa,安全系数为335/128.5 = 2.61;突缘叉处最大应力位于与万向十字节相连处,值为119 MPa,其材料为45钢,屈服强度为355 MPa,安全系数为2.98,具体见表4。
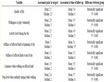
Table 4. Safety factor of each component under working condition 3
表4. 工况3各部件安全系数
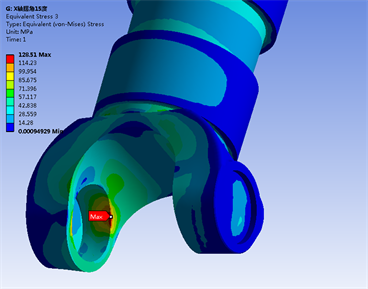
Figure 19. Force diagram of universal joint fork
图19. 万向节叉受力图
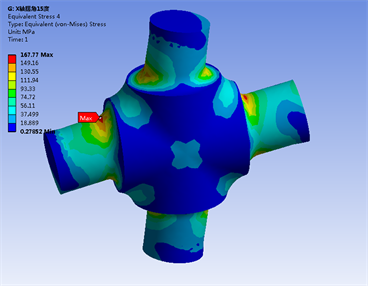
Figure 21. Force diagram of universal cross shaft
图21. 万向十字节受力图
4) 结果分析
计算结果分析发现万向十字轴、突缘叉、万向节叉部分扭转强度安全系数虽然均大于2.0,满足一般机械产品结构强度设计要求,但其组件突缘叉和万向节叉的安全系数偏低,且危险区域位于两者与万向十字节轴承接触处。当传动轴将较大扭转力矩通过突缘叉–万向十字节–万向节叉–滑动套–花键轴–滑动套–万向节叉–万向十字节–突缘叉进行传递过程中,两侧的万向十字节是力矩传递的关键零件,且由于与突缘叉和万向节叉之间通过滚针轴承配合,存在缝隙,因此在力矩传递过程中特别是启动和刹车时,万向十字节与突缘叉和万向节叉会产生碰撞,从而在接触处产生较大冲击力;且接触处未进行圆角过渡,导致应力集中系数较大;此外万向十字节材料20Cr的屈服强度远大于突缘叉和万向节叉的材料屈服强度,以上三点原因是导致组件突缘叉和万向节叉在与万向十字节接触处的安全系数偏低,容易出现失效现象。
3.4. 实验对照
在实际运行过程中,重型卡车的传动轴出现失效现象,突缘叉向侧向外扩展,导致万向十字节与突缘叉脱开,使传动轴功能失效(如图22所示)。而根据仿真分析结果,突缘叉和万向节叉安全系数偏低,其失效概率更大,且危险区域位于两者与万向十字节轴承接触处,与失效实物位置吻合,这验证了传动轴有限元模型的正确性。当出现重型卡车急刹车、急转弯或者其他突发情况时,突缘叉和万向节叉瞬间收到较大扭转力矩,产生较大变形,可能导致滚针轴承与万向十字节方式间的接触模式发生改变,滚针轴承随即发生应力集中和失效破坏。
4. 优化建议
为传动轴失效现象,提高传动系统的可靠性,根据有限元仿真结果,提出以下优化建议:
(1) 增加突缘叉两侧支耳厚度,提高突缘叉的结构强度;
(2) 增加突缘叉支耳与底部过渡直径,或对其形状进行优化,降低突缘叉根部应力集中系数。
5. 结论
本文以重型卡车传动轴系统为研究对象,建立传动轴有限元模型,分析传动轴的扭转强度,得出结论如下:
(1) 该传动轴突缘叉和万向节叉部分静强度安全系数均大于2.0,满足一般机械产品结构强度设计要求。
(2) 应力集中发生在突缘叉和万向节叉与万向十字节轴承接触处,理论上该应力集中部位发生破坏的概率更高,与失效实物情况吻合。
(3) 突缘叉和万向节叉失效变形后,可能导致滚针轴承与万向十字节方式间的接触模式发生改变,滚针轴承随即发生应力集中和失效破坏。
(4) 优化突缘叉的结构设计,可提高突缘叉的结构强度,有效减小传动轴的失效现象。
NOTES
*通讯作者。