1. 引言
随着工业智能化的改造,计算机技术的快速发展,深度学习技术在已经被广泛应用到图像分类和语音识别和分类中,各类算法模型对数据进行大规模训练极大的提高了分类和识别的准确率,逐步提高模型的性能,并成功投入使用,例如人脸识别技术 [1]、车辆检测技术 [2]、语音识别技术 [3]、音频分类技术 [4]。而对于设备故障诊断技术来说,其机理模型都是通过硬件采集收集设备运行的振动信号,一般通过采集信号的时域图和频域图来描述设备的运行状态。根据设备故障诊断分类的基理模型,一般可以借鉴音频信号分类相关算法模型和先进的技术来迁移到旋转机械设备故障诊断上,其共同点包含,数据集的处理方式都是通过时域和频域图,音频信号和振动信号可以通过相同预处理方式,来提取信号深层的特征,由深度学习算法进行训练可以极大地提高模型的性能。
目前,在智能化工业生产中如何可以精确地进行设备故障分类是重要的研究内容。相对比传统时域和频域分析和专家诊断,深度学习算法和人工智能技术在旋转机械设备故障诊断更具有发展前景。深度学习故障诊断技术通过大数据积累和模型的训练可以有效地分析设备运行的状态,故障发生的部件和故障产生的原因,确定设备是否需要进行维修。同时对于设备进行智能化的诊断,减少各种财力物力的浪费,使工厂可以长周期运行,提高经济效益。
深度学习和机器学习等多种算法的到来,已经成为加快了设备故障预知性维护和故障诊断技术的发展。本文总结了设备故障诊断技术发展的历史,分析了深度学习技术在故障诊断分类的现状,以及未来的发展趋势,本文为工业旋转机械类设备进行智能化改造,以及引入深度学习故障诊断分类算法提供参考。
2. 传统设备故障诊断分类技术概述
传统的机械故障诊断技术以前主要依靠现场有工作的经验的人通过人耳和触摸设备仪器进行分析,这个方式需要有大量工作经验的积累,依靠专家经验的积累并不能很好的进行推广,其次存在人的主观因素和客观因素,故障诊断结论人为干扰性大。除此之外,一般设备故障诊断都是通过振动信号来分析设备的故障原因,其主要技术都是通过时域图和频域图来分析设备的特征频率来对应不同的故障类型,具体的分析如下:
2.1. 时域波形
时域波形反应信号幅值及相位随时间变化的特征,时域波形一般可以通过对信号滤波和放大等处理方式采集到设备的信号,时域信号可以很直观的表现在不同时刻下设备的运行状态及其参数量,此时收集的振动波形可以反映出设备的健康状态,通过直观的观看振动信号波形,可以得到振动信号在不同时刻的变化 [5]。一般机械设备的振动信号都是非平稳的信号,其振动的波形是由设备多个部件旋转产生的,信号波形公式一般为:
(1)
其中
为原始信号,
和
为解析信号频率幅度。
对原始的信号进行欧拉公式变化可以得到
(2)
则:
(3)
振动信号一般波形反映了信息包含有量纲参数峰值、峰峰值和有效值;无量纲参数有波形指标、峰值指标、脉冲指标、裕度指标、峭度指标;每个参数量的具体描述如下:
振动时域信号中的均值描述信号振幅集中局势的特征参量。均值u公式一般为:
(4)
均方值描述振动信号的平均功率。均方值是反映信号强度的特征参量。信号均方值表达式是:
(5)
峰值指标
是反应峰值变化的特征参量,峰值x是信号中的最大值,峰值的表达式为:
(6)
其中:
为平均值。
脉冲信号指标c是反应振动冲击的特征参量。脉冲信号表达式为:
(7)
峭度指标是也是反应信号冲击的特征参量。峭度指标表达式为:
(8)
裕度指标是来定量评估发输电系统充裕度的特征,裕度值越大,系统越稳定。裕度指标表达式为:
(9)
2.2. 频域波形
由于时域波形在设备故障分析中,比较单一,设备部件的振动信号进行了叠加,不能直观的分析出设备此时的状态,从而需要将时域信号进行傅里叶变化,将动态复杂的信号进行分解,将不同频率的弦波在频域图中体现出来,频域图的故障特征频率可以反映设备此时的运行状态。将信号波形进行时频转换可以将采集到的一个周期内的波形转换成多个频率分量。根据时域波形将信号进行积分得到傅里叶变化 [6]:
(10)
对信号进行离散傅里叶变化得到
(11)
频域信号是将振动信号从时域信号映射到频域上,频域图中反映了信号的幅度关系和特征频率的关系,频域信号分析不需要考虑信号是否为线性关系,直接通过频率信号来反映设备的运行状态。
3. 深度学习理论在故障诊断分类的应用
深度学习算法有着更强的自适应能力可以对网络模型进行深层训练,训练的结果也有很高的分类准确率。深度学习算法可以通过多层训练机制对采集数据集进行训练,通过深层非线性的网络结构,对训练的模型进行归一化收敛,实现复杂函数的逼近,提高故障分类的准确率。
深度学习算法模型可以根据数据量和训练结果进行迁移学习,微调神经网络模型,充分利用各类算法模型的优势,进行融合多种算法进行故障数据集的特征的深度特征提取,保证数据集可以充分进行训练,模型可以收敛,减少深度学习模型拟合问题和梯度问题的发生,提高模型的泛化能力。一般基于深度神经网络的故障诊断模型流程可总结为以下步骤,如图1:
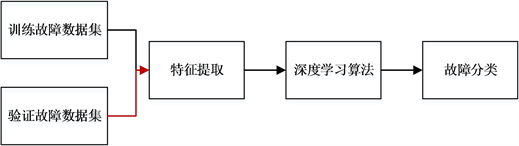
Figure 1. Flow chart of fault diagnosis model
图1. 故障诊断模型流程图
3.1. 数据集
数据集标签的精确性决定了模型训练的好坏,其次数据集的大小也影响着模型训练,所以需要一个数据集来支持深度学习的训练。目前最长用的数据集是美国凯斯西储大学(Case Western Reserve University, CWRU)轴承振动数据库 [7],该数据只针对轴承类故障,但是对于设备故障诊断来说远远不够,还有基于实验转子台模拟出的各类数据故障,这些数据没有针对性,需要结合现场工业设的环境和设备的运行状态进行收集,一般现场使用振动加速度传感器收集设备一段时间之内的离散信号,收集不同的工况下的设备运行时产生的故障。一般旋转机械设备故障分为整体上分为6大类故障,不平衡故障、不对中故障、松动故障、轴承故障、齿轮故障和其他故障。
平衡故障包含了静不平衡、动不平衡和力不平衡;不对中故障包含联轴器角向不对中和联轴器平行不对中,滑动轴承故障包含磨损或间隙、油膜涡动和油膜振荡,滚动体故障包含保持架故障、滚动体故障、内环故障和外环故障;叶片磨损;气蚀;紊流;回流;齿轮故障包含齿轮磨损、齿轮超负荷、齿轮偏心、齿轮间隙不适当、齿轮不正、齿轮裂缝或断裂、齿轮断裂、齿轮偏心、齿轮点蚀;皮带故障包含皮带轮偏心、皮带磨损、皮带共振 [8]。
针对以上的设备常见的故障类型,需要有针对性进行数据集进行收集,传感器采集到的振动信号可能包含多个部件的振动特征。机械设备在运行时可能存在不唯一的振动源,而且振动信号在传输过程中还会受到传输通道的影响,这都会使信号波形曲线呈现出混乱无规律的形态。如果仅对信号波形进行观察很难把握振动的特性和原因,因此需要采用振动信号特征提取技术,将有用的振动信号特征提取出来用于进一步的故障诊断分析,需要根据现场设备的运行情况采集振动的信号,振动类型的数据要和故障一一对应。先对信号的采样点数和采样频率进行设置。
信号采样点数一般为2的指数方,如16、32、64、128、256……。在振动分析领域一般要求最小的采样点数为256,其它采样点数为256*2n (n = 1, 2, 3, 4, 5, ......)的倍数,如512、1024、2048……、256 K (1 K = 1024)。
采样频率首先要根据足设备的参数,粗略计算设备的特征频率如;基频、齿轮啮合频率、轴承的特征频率;一般采样频率选择的一般原则是:1) 大于等于基频的20.48倍;2) 一阶啮合频率的10.24倍;3) 滑动轴承特征频率的25.6倍;4) 信号频率分辨率的8倍小于等于某2个特征频率之差的最小值。轴承的特征频率 [9] 计算如下:
外圈特征频率:
(12)
内圈特征频率:
(13)
滚动体特征频率:
(14)
保持架特征频率:
(15)
其中:接触角为α;滚动体直径为d;轴承内径为r。
设置标准的采样点数和采样频率,通过加速度传感器收集到故障数据集,制作成适用于现场工业环境设备故障和时域图一一对应。
3.2. 信号特征提取
信号的特征提取直接从数据集的提取故障特征,特征提取是实现机械设备模式识别和智能故障诊断的前提和基础,一般深度学习算法模型直接对图像或信号进行特征数值的学习和训练,因为深度学习算法模型是对深层次网络模型结构对数据集特征进行逐层学习,提取有效的特征信息进行训练。一般最常用的深度学习算法模型是CNN和LSTM,其次是这些神经网络变体模型。
1) CNN网络网络特性具有权值共享和局部连接。卷积神经网络的结构一般包括输入层,多个卷积层与池化层,全连接层和输出层;卷积层是卷积神经网络对输入的特征图进行卷积操作,相当于特征提取,降低特征图的维度,提取关键信息 [10]。一般连续卷积的定义公式如下:
(16)
其中:
为输出项,特征映射,
为输入的数据,
为卷积核
池化层可以降低特征谱图的空间维度,一般公式定义为:
,
(17)
为第l层输出的第j个特征图,
为池化层的权重系数,
为池化层的偏置项,
为池化函数。
全连接层是将卷积层和池化层连接起来,一般公式为:
(18)
其中,
第l层全连接层的权值,
为全连接l层的偏置。
2) LSTM可以更好处理序列比较长的数据集,通过引进三个门函数,输入门、输出门和忘记门对LSTM的记忆细胞进行内容的控制,选择保留和遗忘特征信息,从而可以解决音频信号处理长期依赖的问题LSTM的三个门函数,输入门控制输入信号的流动,改变记忆细胞的状态 [11],这个时候的细胞状态为:
(19)
其中,
上一个细胞的输出
(20)
通过输入门,细胞函数的状态进行更新,更新公式为:
(21)
忘记门函数是对输入门的传递的记忆细胞信息进行运算,判定那部分信息需要被遗忘,忘记门的公式为:
(22)
忘记门输出一个(0,1)的函数值,输出层是对细胞更新的状态进行输出,输出的公式为:
(23)
(24)
3.3. 故障诊断分类
softmax分类作为神经网络最后一层 [12],可以直接输出故障分类结果。假设输入
,每一个类别j估算出概率值,类别标签
,则期望概率
是预估x的每一类故障发生的频率,假先设定函数
的形式为:
(25)
由期望概率将公式(式3.5)转化成
(26)
其中,
是模型的参数值,每个样本归属类别的期望概率如下:
(27)
上述公式表示的是对概率分布进行归一化,简单的说就是让所有概率和为1。正则化后softmax代价函数定义如下:
(28)
其中m代表样本数量。
除了使用神经网络的最后一层softmax,还可以使用其它深度学习算法,例如极度梯度提升算法,它是通过把许多树模型叠加组合成很强的分类器,主要通过使用泰勒二级展开式对树结构进行优化,由函数二阶近似值优化决策树切分点进行迭代,同时加上正则化项来控制树模型的复杂度。XGBoost的核心思想是对目标函数通过迭代不断进行优化,控制树和叶节点的数目进行分类和回归问题的处理。
3.4. 分类性能的判断规则
故障诊断分类的结果一般都是采用准确率、精准度、召回率和F1-Score作为准则 [13],公式为:
准确率公式为:
(29)
精确率公式为:
(30)
召回率公式为:
(31)
F1-Score公式为:
(32)
4. 讨论
4.1. 设备故障诊断分类技术的不足
基于传统的故障诊断分类,是通过时域和频域图对设备的故障特征频率进行分析,故障特征计算失误,收集到的时域波形和频域波形,无法显示故障特征频率,其次根据专家的经验,故障判断可能不精确,有一定的局限性。
而目前,深度学习算法故障诊断分类算法,神经网络单一、适用性不强,不能直接迁移到其他模型。其次深度学习网络层数太多,模型容易陷入过拟合,层数太少,模型训练不到位,容易发生欠拟合故障,导致分类准确率降低。其次目前故障诊断数据太少,针对工厂设备机械故障没有可以通用,进行大规模训练的数据集,训练出来的结果迁移性差。最后对于设备故障诊断的特征提取困难,收集到的时域信号,提取到有效的特征和故障标签一一对应的难度比较大,特征信息提取不到位。
4.2. 深度学习算法在故障诊断领域的发展趋势
深度学习算法对于工业上旋转机械类设备故障诊断具有重大的意义,通过深度学习算法模型不断提升故障分类的结果,对于现场工业设备维护起到关键性作用,其故障诊断结论,可以有效的指导现场进行设备维修和设备零件储备,所以准确的判断出设备故障,减少事故的发生。
针对深度学习算法在工业设备故障诊断应用,将针对某一类设备机械故障的大量数据集,数据集分为有效数据、无效数据和故障数据,深度学习算法将会得到有效的训练。其次深度学习算法模型,将与多种深度学习算法模型结合,融合各类算法模型的优势,提高分类精确率,其次模型的复杂度将会降低,模型的迁移性好,可以使用各类设备上;模型训练的时间也会缩短,深度学习模型的性能提高。
5. 结束语
智能化设备故障诊断分类技术是现在工业上的未来趋势,通过自动推送故障诊断结论是非常重要的,精确的诊断结论可以对工业现场的设备进行预知性维护,减少不必要的损失,提高经济效益。所以深度学习领域的故障诊断分类是以后的发展趋势,精确的故障分类为设备维护和保养起到了关键作用。随着计算机性能的提升,深度学习算法在故障诊断分类与识别中,可以通过大量故障数据训练,深度算法模型的深度学习,逐步优化模型的分类性能,提取数据特征的深层特征,提高最后故障诊断分类的准确率。