1. 引言
随着互联网技术的高速发展,工业4.0 [1]、中国制造2025 [2] 等概念的提出,传统制造行业正发生着根本性的变化,从传统的制造模式开始向智能制造转型升级。智能化的转变,首先体现在传统生产过程中孤立的生产设备向各设备间数据的互联互通的转变。而实际生产中,往往是不同底层通讯协议的各设备间的信息进行互联,本文提出的一种基于数字孪生概念的数控设备信息可视化系统的设计架构 [3],采用了OPC协议 [4] 对服务端采集到的来自不同类型的实时生产数据进行读取、格式转换并存入实时数据库中,并通过建立数据字典(包括数控机床字典、AGV机器人字典等)作为数字孪生模型实时驱动数据源,使用Blender进行孪生体的几何建模,并利用Unity数据驱动引擎驱动孪生模型,进行实时映射,实现了从物理实体到数字孪生体的同步运行。使用了Html、Vue.js等前端展示技术、Echarts可视化图表、Ajax异步传输技术等进行生产大数据的图表化与可视化。最终实现了对生产流程、设备运行状态以及实时生产信息的可视化。
2. 系统架构设计
在传统工业生产的可视化平台中,通常由工业物联网平台作为系统的核心,依靠其进行生产管理、设备监控、边缘计算等工作。本文提出的架构中(见下图1),MES起到相同的作用 [5]。作为整个系统的核心,在承担车间生产管理任务的同时,其向上层提供了支持孪生模型驱动运行的各种数据,这些数据来自于生产过程中产生的计算结果,以及从下层设备采集到的设备数据。最下层的物理层中,MES与边缘网关间进行交互,网关主要负责解析来自不同多源异构设备的数据,统一数据格式后传递给MES。数据采集部分使用统一架构的OPC采集协议,利用支持该协议的传感器对来自不同品牌和厂家设备的生产数据以及孪生数据进行采集和整合,同时具有对不同底层设备提供数据驱动支持,使得不同品牌和厂家的数字生产设备的数据之间实现互联互通,包括了生产的实时数据,例如本车间生产过程中的实时电流、电压、以及设备的物理状态数据等。最上层可视化界面实时更新图表数据段(使用Ajax以JSON方式推送)、以及生产过程中的孪生单元运动同步,通过MES对车间的生产订单的生成、下发、销毁,车间人员管理、设备的生产流水、使用情况、维修保养情况进行整理与记录,并根据历史数据信息向平台反馈、统计、筛选,实现报表可视化和生产优化。
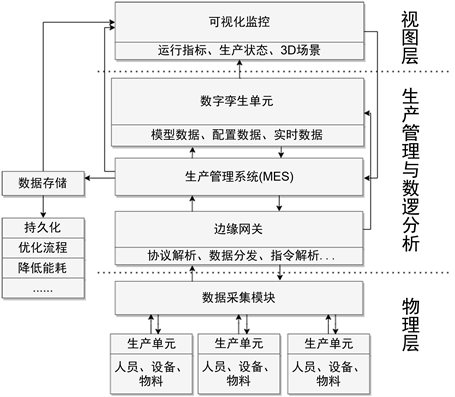
Figure 1. Digital twin visual monitoring platform architecture
图1. 数字孪生可视化监控平台架构
在上述的平台架构上,利用数字孪生关键技术进行建模,实现整体的三维可视化车间的监控平台,是较为可靠和合理的方案。从数字孪生制造的角度出发,MES被看作是数字化建模的可靠工具和数据产生源头。在企业生产制造过程中,MES将大量过程数据收入囊中,并将海量的历史数据进行归档与分析,成为了制造企业在未来生产过程中建立预测模型和优化生产的有力基础。在人机界面中,MES时刻承担着与其数据线程进行交互的重要任务,且在整个生产流程,其也与数字孪生体全生命周期的数据驱动过程保持着紧密的联系。此外,该架构底层采用OPC采集协议,OPCServer对用户提供异步数据订阅通知的方式向上反馈数据变化,这种方式非常适合与依赖状态与事件驱动的数字孪生体运动的实现。
3. 数字孪生概念及模型构建
3.1. 数字孪生概念
孪生体的构建依据陶飞 [6] [7] 等人提出的数字孪生五维模型。模型、数据、通信作为基础,工业互联网为平台进行构建。数字孪生技术2003年由Grieves教授提出,结合智能制造与深度信息融合的时代背景被广泛地应用于工业生产的各个领域。美国空军研究实验室(nation aeronautics)基于数字孪生技术,利用高保真飞行模型与影响飞行的结构偏差和温度相结合,构建飞机飞行的疲劳寿命预测模型 [8];美国通用电气公司基于数字孪生体,结合云服务平台Predix,利用大数据、工业互联网等先进技术构建发动机的实时监测系统,实现了发动机生产过程故障诊断与预测性维护;达索公司利用数字孪生3D交互平台,通过用户在虚拟端的体验信息不断地优化与改进相应的实际物理模型;中国对空导弹研究院基于数字孪生的思想,借助调制传递函数将机载广电系统性能影响因素统一映射到能量域,解决了系统性能退化多场耦合建模难题。
3.2. 数字孪生建模
根据生产车间关键要素理论进行抽象 [9],具体可分为车间的生产模型DMequip、功能模型FMfunction、真实设备与孪生体之间的实时通讯接口模型CMinterface、以及服务模型SMservice。
功能模型FMfunction,要求根据车间实际生产业务建立对应功能的孪生模型,该模型要求三维模型的高度拟真,以及生产数据采集和传输的准确和实时性。
设计接口模型CMinterface时,首先对各模型与参数进行分类,并对车间资源进行整合,如下图2所示,分为几何模型Gm、物理模型Pm、状态参数模型Sm以及行为模型Bm,分别进行接口设计。在几何模型Gm方面,定义该孪生单元的物理坐标以及运动约束等。在物理模型Pm中,为不同的孪生资源定义不同的数据实体,并根据该孪生单元所属资源,创建相关物理参数集。同样的,在状态参数模型Sm中,根据不同生产资源,分别创建生产运行参数集、事件状态集、生产单元属性集。最后,在行为模型Bm中,使用CEA事件驱动的方式,定义孪生体驱动的接口。
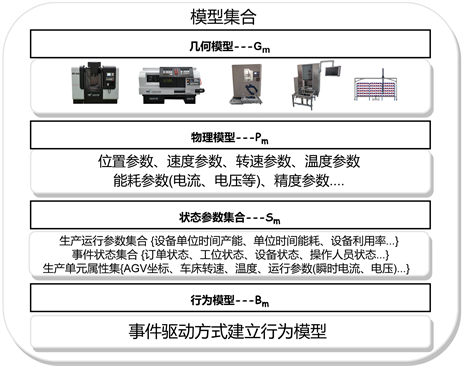
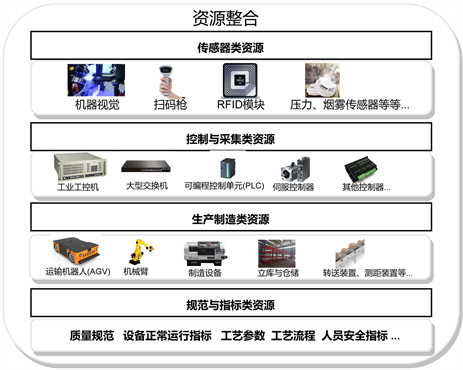
Figure 2. Model and resource integration
图2. 模型与资源整合
最后,服务模型SMservice中定义了孪生单元与可视化界面的数据交互方式、与MES系统的数据传递方式等。
以上就是对整个车间生产模型的定义。
此外,生产设备在进行数字模型的构建时,要求孪生模型具有和实际设备在几何、行为、各类约束都高度一致的三维模型,如下图3所示。这就要求在构建孪生模型时,不仅要考虑该模型的具体情况,同时也要构建相应生产车间的一些空间状况,且保证其与真实生产环境高度吻合。

Figure 3. Twin model (left) and production equipment (right)
图3. 孪生模型(左)与生产设备(右)
在几何模型的形状建模过程中,使用Blender进行模型结构的搭建以及场景的渲染,其提供从建模、动画、材质、渲染等一系列制作方案。在场景搭建与渲染时,必须保证虚拟车间与真实场景的高度吻合,包括了空间大小、设备的形状大小、摆放位置等,虚拟车间的场景搭建如下图4所示。
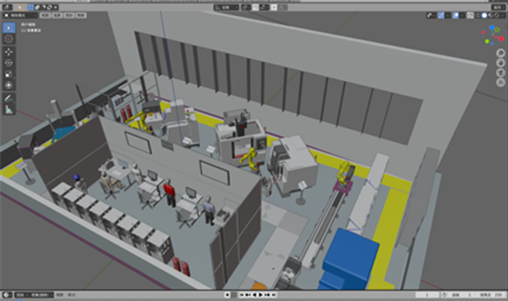
Figure 4. Virtual workshop scene construction
图4. 虚拟车间场景搭建
对于虚拟车间中具有运动属性的孪生单元,需对其进行运动约束,包括了物理约束与实际工艺流程约束。例如在运输任务中,AGV的运动约束受到该工件运送工位的约束。而在物理约束中,需要对只在固定方位运动的孪生单元进行运动方位的规定,例如场景中的六轴机械臂,其物理运动受到轴向运动方位的限制。在本文,物理约束使用了在动画制作中为动画人物绑定行为的骨骼绑定技术,为机械臂搭建固定轴向的骨骼,并规定其按照固定方向运动,解决了孪生单元的几何约束问题(如下图5)。
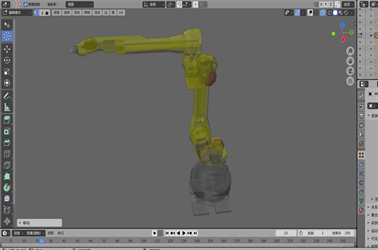
Figure 5. The robotic arm (left) and the robotic arm with bone constraints (right)
图5. 机械臂(左)与带有骨骼约束的机械臂(右)
3.3. 数据映射与驱动方式
同时,虚拟车间要与真实车间产生关联,必然通过数据互通,虚拟车间要同步真实车间的生产过程,也需要数据的驱动。对于虚实车间的数据映射和驱动方法,本文使用以下的方法。
由于工业现场的设备具有多源异构特点,可以通过使用XML格式对创建孪生单元数据实体,通过对每种资源进行分类,对每种资源中所需要的数据或状态集合进行分类,使用XML解析方法对不同资源下的孪生单元动态的生成具有不同属性的数据结构(见下图6)。
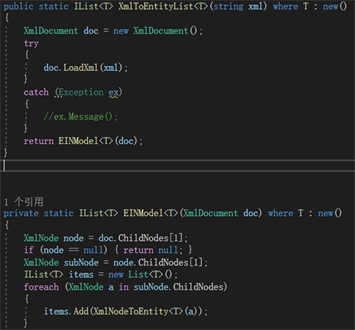
Figure 6. XML parsing method (left) and resource unit data set XML definition (right)
图6. XML解析方法(左)与资源单元数据集XML定义(右)
其次,要将孪生单元的数据实体需要与底层采集到的数据进行绑定。基于OPCServer提供的数据的异步订阅–推送模式(如图7),这种模式根据底层变化进行反馈数据,可以根据客户端设置的扫描周期,定时轮询下位机的点位地址,若数据变化,且是订阅数据时,向上推送该条数据。这种方式的好处在于,并不会时刻与上层通讯接口进行频繁的数据传递,将大量工作主要集中在采集层。且这种反馈方式,实时反馈变化的数据,交由MES包装为事件状态的变化,再将事件变化反馈给孪生车间对应的单元,做出相应动作。使用该类方式驱动孪生车间的虚拟生产,是一种实时的、高效的驱动方式 [10]。
基于事件状态变化的驱动方法 [11],可以使用“条件–事件–行为”(Condition-Event-Action, CEA)来实现事件驱动:
其中,
代表满足虚拟车间的实时属性集合,
为对应事件,
为对应动作。在虚拟车间中,
建立实时属性集合,实时属性根据真实车间的生产情况实时变化,在生产过程中,按照条件判断是否触发对应的事件,若匹配,则执行该事件对应的相关动作。
如下图8,以AGV运送工件进行加工为例,介绍事件驱动方法在虚拟车间的映射机制。开始时,当任务下发,物理车间AGV接收到上层任务指令,开始运输任务,并像虚拟车间发送对应触发属性,孪生车间接收到该属性后,根据对应孪生单元数据实体,匹配对应的事件,匹配结束后,执行相应的动作。在该例中,AGV匹配到传输事件,并开始向目标工位运动,当结束时等待,真实车间中当工位A上的工艺流程开始进行时,向虚拟车间发送触发属性,包括AGV到达工位A、以及工位A上执行对应的工艺信号,分别触发了孪生单元AGV的到达事件以及工艺开始的各种事件。工位A上的工件加工完成后,同样按照此机制,进行后续生产流程。当工件在工位B进行加工时,若该工位设备出现故障,同样通知虚拟空间,触发故障事件,生产后续流程可由管理人员提供决策或是建立模型和算法库做出决策。通过该驱动方式下,属性的实时更新,不断完善算法库,逐步将虚实映射程度提高到较高水平。
4. 可视化界面实现
无论是出于安全角度,还是提高生产效率、降低能耗分析的角度,实时的生产过程可视化以及清晰的生产参数图表都是车间稳定生产的保障,也逐渐成为未来数字化生产模式的必要条件。
本系统中的生产可视化分为了数字孪生车间生产过程的可视化,以及生产参数的可视化,生产参数主要以图表形式进行展示,包括了设备占用率、生产效率、合格率、日产量、能耗信息统计、物料消耗信息统计等。
孪生车间部分的实现,将几何场景建模后的模型以带有骨骼绑定的fbx格式模型导出,该模型利用Unity3D编写C#脚本,与模型绑定,最终由WebGL技术嵌入web页面中,如下图9所示。

Figure 9. Twin workshop embedded web way
图9. 孪生车间嵌入web方式
生产数据的web端展示结构如下图10所示,OPC服务器采集到下层设备的实时生产数据以及由用户订阅推送的实时变化数据,传到MES系统进行筛选与处理,供Web服务器使用,同时数据实时存入MySQL数据库中进行归档。IIS服务器通过发送请求的方式,得到以JSON格式的各类数据。Web端通过HTTP请求获取web服务器中的数据,前端通过Ajax技术动态解析来自IIS服务器上的数据 [12],同样以JSON格式传输。最终数据被推送到浏览器端,进行实时渲染与显示。
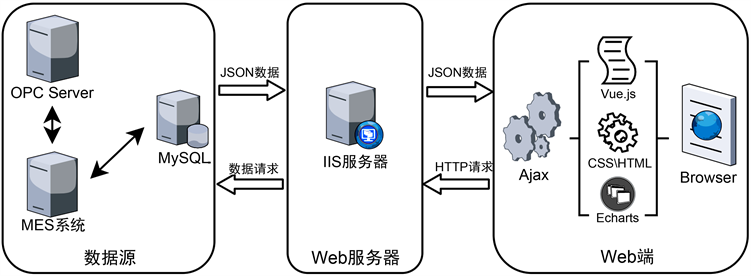
Figure 10. Web-side data transmission structure
图10. Web端数据传输结构
5. 系统的实现与验证
5.1. 车间生产状况
该车间主要生产任务是对金属轴类和盘类工件的加工,工件由机械臂从立库取出(如图11),由AGV送往车床。
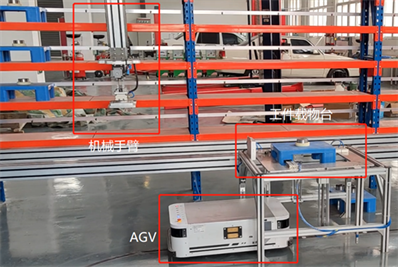
Figure 11. The workpiece is taken out from the warehouse
图11. 工件从立库取出
数控车床平床身数控车能够对各种轴类和盘类零件自动完成内外圆柱面、圆锥面、圆弧面、端面、切槽、倒角等工序的切削加工。
车床对工件进行双面的边缘倒角切削之后,工件由机械臂送往铣床,金属工件在铣床进行铣削(如图12所示)。
随后送往3D弧焊装置,在工件上表面进行3D浮雕。最后由AVG送往视觉检测装置(如图13所示),检测工件质量是否达标,最终由AGV送往立库相应区域存放。
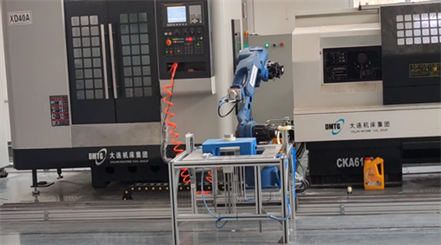
Figure 12. The workpiece is sent to the milling machine by the robotic arm
图12. 工件由机械臂送往铣床
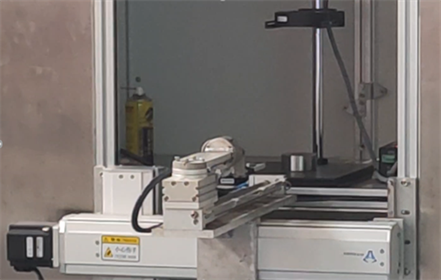
Figure 13. The workpiece is sent to the milling machine by the robotic arm
图13. 工件由机械臂送往铣床
如上,为该金属工件加工的一个完整流程,流程简图如下(见图14)。
5.2. 车间可视化系统展示
车间设备数据通过SIMATIC S7-1200模块进行采集,最终汇集到SIMATIC S7-1500主控向上层传递。下图15为车间生产过程中OPCServer运行情况。
数据通过采集网关解析,向上传递至MES系统。MES为车间生产提供包括制造数据管理、计划排程管理、订单管理、生产调度管理、工序工位管理、库存管理、质量管理、人力资源管理、工作中心、设备管理、采购管理、生产过程控制、底层数据集成分析等模块。
最后,在生产过程中,各种数据通过不同方式,推送至车间可视化看板进行展示,如下图16所示。
6. 总结
数字孪生,作为监控车间运行状况的新模式,在未来行业中被认为是生产制造的关键技术,对于推动工业4.0、智慧工厂、以及中国制造2025的先进生产方案与战略有着重要意义。本文提出的数字孪生车间的可视化系统方案,采用统一采集协议对多源异构设备数据进行获取和上传,利用MES作为核心,承载着工厂生产中的大量工作,并向上层提供生产数据,向下层设备发送状态指令。同时,本文中创建的虚拟车间场景有效地约束了孪生设备的物理行为,采用事件驱动的虚实交互方法能够将真实车间与虚拟车间有效地映射起来。在可视化看板中,较为全面与清晰地体现了从虚拟生产监控,到实时生产数据的图表化与可视化。最终在车间生产过程的投入使用中,系统也体现出稳定性与高效性,有效地解决了传统车间实时性较差,可视化、透明度较低等问题,有效提高了车间生产效率,同时通过对历史数据分析,有效降低了设备故障率。
通过生产过程的验证,该方案能够较为有效地匹配中小型生产车间的生产制造场景。在面对规模更大,设备、车间更加离散的生产状况,未来研究中数字孪生技术还需与5G、AR、大数据分析等多领域技术进行融合、发展,才能不断地发现数字孪生技术为工业制造带来的更多可能 [13]。
基金项目
重点研发计划项目(课题编号:2018YFB1701802)。
参考文献