1. 引言
中间包作为钢液凝固前最后一个耐火材料容器,其钢液流场对去除非金属夹杂物有着重要影响,进而对保障钢产品的性能起着重要作用 [1] [2] [3] [4]。
Harnsihacacha等人 [5] 分析了挡坝、导流挡墙对中间包流场的影响,发现增设挡坝后死区大小由原型的44%减小到33%,而增设挡墙后,死区大小减小到23%。说明挡坝和挡墙改进中间包的流场性能十分有效。Zhong等人 [6] 通过研究改变挡坝高度对中间包死区的影响,发现将挡坝增高后,死区从28%减少到17%。胡铁军等人 [7] 通过改变湍流抑制器侧壁高度、挡墙高度、挡坝高度来探索其优化效果,发现改变湍流抑制器侧壁高度影响不大,而改变挡墙、挡坝高度后,死区大小有明显改善。王德永等人 [8] 通过对几种不同的中间包控流装置进行比较,发现湍流抑制器能有效防止开浇时钢水喷溅和二次氧化,增设导流孔挡板和设置透气砖吹氩均能有效降低死区大小。郑淑国等人 [9] 研究了不同类型的“V”型挡墙及其与挡坝、湍流抑制器组合对中间包流场的影响,发现带横墙的“V”型挡墙和不带横墙的“V”型挡墙均能改善流场的流动特性,且在此基础上增设挡坝,能进一步降低死区比例。张利君等人 [10] 通过将原型中间包的挡墙和挡坝间距增大,有效提升活塞流的比例,并将死区比例降低了2.2%。李怡宏等人 [11] 通过对双挡坝中间包进行研究,发现低挡坝应设置在高挡坝之后,且当低挡坝与高挡坝导流孔同高时,钢液平均停留时间达到最大稳定值,高低坝距离在40~160 mm之间时,低坝后无涡产生。许建飞等人 [12] 结合唐钢中厚板材公司现场生产情况,通过水模实验,对中间包内部结构进行优化研究,发现“抑湍器 + 单挡墙 + 双挡板”的组合优化方案,可将死区减小为0.14%。由此可见,随着中间包流场优化目标的提高,优化的方法也逐渐从有无控流装置,发展到单控流装置结构参数优化,最终发展为多控流装置组合优化。
针对某公司钢坯杂质含量偏高的现象,本文基于计算流体力学方法,对连铸中间包中的流场进行分析,对不同导流孔、挡坝等结构参数下的流场进行数值模拟,并寻找出优化方案,为改进中间包流场特性提供理论指导。
2. 中间包模型
2.1. 物理模型
以五流中间包为研究对象,其结构如图1所示,内部设置有长水口、湍流抑制器、导流挡墙、塞棒、侵入式水口等部件。其中,导流挡墙将内部空间分隔为冲击区和浇铸区两部分,钢液经导流孔从冲击区流向浇铸区。导流孔孔径d1 = d2 = d3 = 150 mm,仰角α1 = α2 = α3 = 10˚。五流中间包的主要工艺参数列于表1中。
(a) 五流中间包 (b) 导流孔
Figure 1. Schematic diagram of five-strand tundish structure
图1. 五流中间包结构示意图
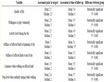
Table 1. Process parameter of tundish
表1. 中间包工艺参数
2.2. 数学模型
中间包的运行过程可分为三个阶段:充包阶段、稳态浇铸阶段、空包阶段。为简化计算,本文仅考虑稳态浇铸阶段,且忽略钢液的散热,因此钢液的流场可用稳态不可压缩N-S方程进行描述,湍流模型采用SSTk-𝜔模型,即:
1) 连续性方程
(1)
式中,ρ为密度,kg/m3;
为方向j的速度,m/s;
为j方向的坐标(j分别取1、2、3,代表三个坐标方向),m。
2) 动量方程
(2)
式中,p为压强,Pa;me为湍流粘度(即流体分子粘度m和湍流粘度mt之和),Pa∙s。
3) SSTk-𝜔湍流模型 [13]
(3)
(4)
式中, 为湍流动能,m2/s2; 为角频率,rad/s;且有:
(5)
混合函数
(6)
(7)
(8)
(9)
(10)
(11)
参数取值见表2。
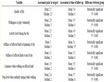
Table 2. The parameter of the SST k − ω model
表. 2SST
模型参数取值
4) 组分运输方程
为了获得中间包死区、停留时间等流场特性参数,常采用在其入口加入脉冲示踪剂、在出口监测示踪剂浓度的方法。这一过程可用非稳态的组分守恒方程进行描述,即
(12)
式中,Y为示踪剂的质量分数,D为示踪剂扩散系数,m2/s。
2.3. 网格划分
由于采用SST
湍流模型,对壁面附近区域网格有较高的要求,为此第一层网格高度在1 × 10−4 m左右,可以保证高流速区壁面处的y+在30~300之间,低流速区壁面处的y+在1以下。网格数量约为200万,如图2所示。
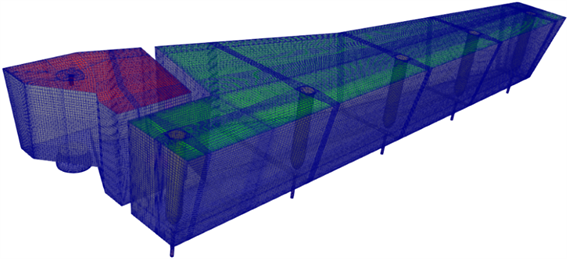
Figure 2. The mesh of five-strand tundish
图2. 五流中间包网格示意图
2.4. 边界条件及求解方式
中间包入口采用速度入口,速度大小为4.97 m/s,出口设置为压力出口,钢液液面采用对称边界,壁面设置为无滑移边界。钢液密度取7014 kg/m3,运动粘度取0.0064 Pa∙s [14]。
基于CFD开源软件OpenFOAM v8进行计算,使用simple Foam求解器对流动进行求解,使用scalar Transport Foam计算示踪剂的输运过程,采用GAMG求解器计算压力。
2.5. 模型验证
为了对中间包流场数值模拟结果的可靠性进行检验,对原型中间包流场进行水模型实验。
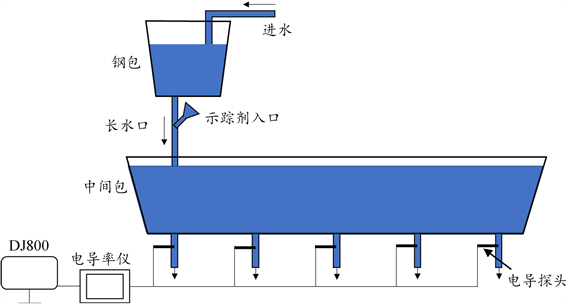
Figure 3. Schematic diagram of experimental device
图3. 实验装置示意图
根据中间包的尺寸,按1:3的比例搭建了水模实验系统。考虑到雷诺数(Re)较大,对流速分布的影响较小,故基于弗里德数(Fr)相等的原则,控制模型中水的流量。
水模系统由上水装置、示踪剂加入装置、数据采集装置和排水装置四部分组成,具体包括钢包模型、中间包模型、示踪剂加入装置、电导探头、电导率仪和数据记录仪(DJ800)等,如图3所示。其中,钢包模型、中间包模型均由有机玻璃组成。
流场特性参数通过“刺激–响应”实验方法获取,主要实验步骤包括:
1) 将合适比例的水、酒精、KCl配制成密度与水接近的盐溶液,作为示踪剂;
2) 通过塞棒粗调和转子流量计微调使出口流量达到指定值,调节水流的入口阀门使液面达到指定高度并保持稳定;
3) 在入口处通过脉冲方式注入示踪剂;
4) 同时对电导率进行采样监测,采样频率为20 Hz,采样时间为3倍模型中间包的理论停留时间。
分别通过数值模拟方法和水模型实验得到原型中间包的死区比例,见表3所示。数值模拟结果相对水模型实验结果的偏差小于2%,表明所建立的数值模型可以准确预测中间包内钢液流动过程。
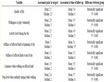
Table 3. Dead zone ratio of water model experiment and numerical simulation
表3. 水模型实验与数值模拟的死区比例
3. 中间包原型流场分析
3.1. 速度分布
中间包原型流场数值模拟结果如图4~图6所示。由图4可知,钢液以较大的流速从长水口注入,形成射流,冲击底部的湍流抑制器。在湍流抑制器底部存在一个流速较小的区域,即为射流驻点。钢液遇到湍流抑制器内壁后向上流动,形成回流,并与射流引起的回流汇合。汇合后的钢液向上方流动,在靠近导流挡墙一侧形成一个较大的漩涡。
(a) 速度云图 (b) 速度矢量图
Figure 4. The melt velocity at longitudinal section though the inlet in impact zone
图4. 冲击区入口纵截面速度分布
图5为通过各导流孔的水平截面速度矢量分布,导流孔位置从高到低依次为A、C、B。在导流孔A截面上,由于入口射流流速大,在导流孔A附近形成了顺时针的回流漩涡。导流孔B截面靠近湍流抑制器,钢液在离开湍流抑制器时向四周流动。钢液经过导流孔时流通面积减小,流速增大,进入浇铸区后形成射流并诱发回流。其中,经导流孔A、B进入浇铸区的钢液,由于射流区域上方靠近壁面,钢液向上的流动受阻,向下流动形成回流区域。经导流孔C进入浇铸区的钢液在较短的距离内遭遇壁面,冲击壁面后向浇铸区的末端流动,在1#、2#出流口之间形成较强的回流。5#出流口附近的钢液流速较低,没有出现回流。
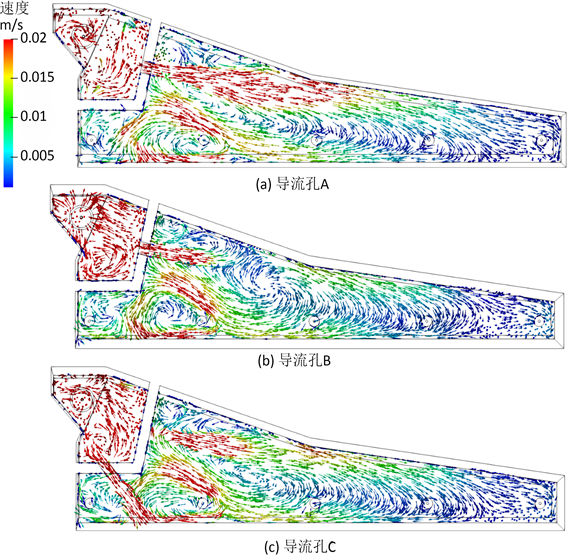
Figure 5. The melt velocity vector at the horizontal section though hole
图5. 各导流孔水平截面速度矢量分布
图6为出流口纵截面速度矢量分布。由于1#、2#、3#出流口更靠近导流孔,因此整体钢液流速呈现左高右低的分布趋势。导流孔C钢液射流位于在1#、2#出流口之间,具有较高的流速。导流孔C钢液射流方向向上倾斜,导致2#出流口液面附近钢液具有较高的流速,同时部分钢液呈现出向下流动的趋势。
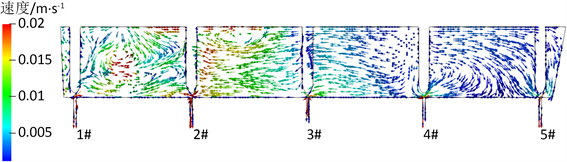
Figure 6. The melt velocity vector at longitudinal section though the outlets
图6. 出口纵截面速度矢量
3.2. 流场特性参数
1) 各出流口流量均匀性
将1#~5#出流口的流量进行计算,并示于表4中。不难看出,各流口流量分配百分比的极差仅为0.1%,说明当前中间包各出流口流量分布均匀。
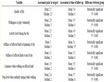
Table 4. Flow rate of each outlets
表4. 各出流口流量分布情况
2) 各流口的停留时间
通过对示踪剂组分输运过程的数值模拟,获得各出流口处的平均停留时间(RTD)曲线及其响应参数,如图7、图8所示。1#、2#出流口距离导流孔C较近,钢液流动路程较短,具有较短的响应时间。经导
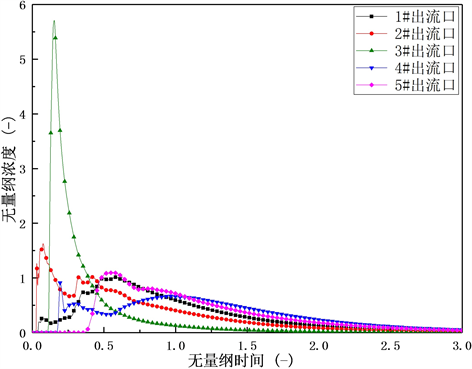
Figure 7. The average residence time distribution curve of each outlet
图7. 各出流口的平均停留时间分布曲线
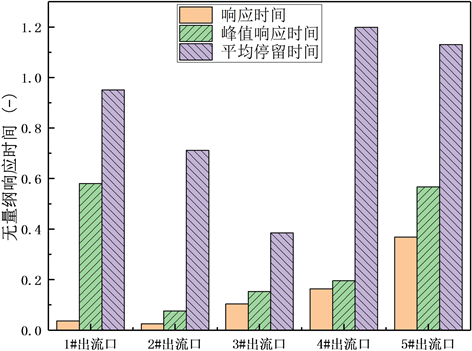
Figure 8. The time of tracer response at each outlet
图8. 各出流口的示踪剂响应时间
流孔C进入浇铸区的钢液大部分向2#出流口流去,致使2#出流口峰值响应更早、平均停留时间更短。
1#、4#、5#出流口的平均停留时间接近或高于理论停留时间,具有相对理想的流动状态。3#出流口的示踪剂响应时间与峰值时间相近,示踪剂响应快,说明存在短路流,不利于钢液中夹杂物的上浮分离,具有较大的优化空间。
3) 死区比例
为了对中间包流场的整体性能进行评价,计算了总平均停留时间分布曲线以及死区比例 [15]。图9所示为总的示踪剂平均停留时间分布。表5为原型中间包内流动情况统计,其流场以全混流为主(78.33%),死区比例为12.77%。
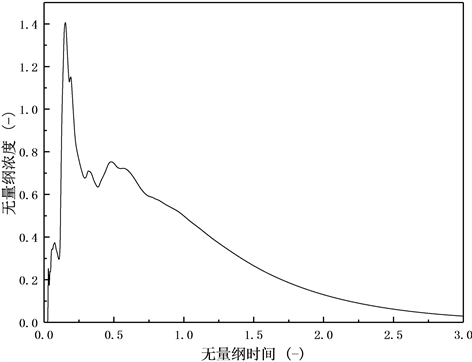
Figure 9. The total average residence time distribution curve
图9. 总平均停留时间分布曲线
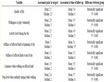
Table 5. Molten steel flow characteristic parameters in the prototype tundish
表5. 原型中间包钢液流动特性参数
4. 结构参数优化的数值模拟
4.1. 模拟方案
为了降低中间包流场中的死区比例,需对其结构参数进行优化。根据工程实践经验,通过增设挡坝、调整导流孔的仰角与内径,可以改变中间包的流场。为此,本文在3#、4#出流口之间增设挡坝,保持原型中间包导流孔A的参数不变,改变导流孔B、C的内径与仰角,其模拟实验方案见表6。
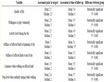
Table 6. The simulation cases with various hole structure
表6. 不同导流孔结构参数下的模拟实验方案
4.2. 结果分析
对表6中的9种实验方案下的中间包内钢液流动过程分别进行了数值模拟,并提取相应的钢液流动特性参数,如表7所示。不难看出,第9号实验方案下的死区比例最小,由原型的12.77%降至2.6%,同时具有最长的无量纲停留时间0.9774。中间包优化后的结构参数为:增设挡坝,导流孔B、C的内径均由100 mm扩大至200 mm,将导流孔B的仰角调整为30°。
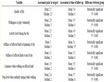
Table 7. The molten steel flow characteristic parameters with various hole structure
表7. 不同导流孔结构下钢液流动特性参数
5. 结论
本文基于计算流体力学方法,对原型中间包钢液流场进行了分析与结构优化,并通过水模型实验对其优化效果进行了验证,得到主要结论如下:
1) 水模型实验结果表明,建立的数学模型可以有效描述中间包内的钢液流动过程。
2) 原型中间包各出流口流量分配均匀;钢液在浇铸区中部形成较大的涡,有利于促进钢液混匀,中间包全混流占比达到78.33%,但2#、3#出流口存在钢液短路现象,死区比例较高,约12%。
3) 对9种不同导流孔结构的中间包流场进行了数值模拟,获得了具体的优化方案,即在3#、4#出流口之间增设挡坝,将导流孔B、C的内径扩大至200 mm,提高导流孔B的仰角至30°。