1. 引言
汽车的燃油箱作为汽车发动机燃料能源的供给功能的重要部件,燃油为易燃液体,在油箱路试过程中,充油的燃油箱容易发生结构破坏 [1],因此燃油箱的性能一定程度上将影响到汽车中乘员的安全性。因此在研发一款新油箱过程中,需要考虑其能抵抗外界环境变化时,引发的燃油箱箱体内的压强变化对燃油箱本体的破坏。燃油箱的结构设计过程相对较为复杂,不同结构的油箱在承受一定的压强后箱体的变形不同,祁涛等 [2] 根据不同结构的油箱底面设计出了三款燃油箱,研究了不同结构油箱受压后变形量的具体分布情况,对燃油箱的变形趋势和形变情况的影响因素作出了综合性的分析。结果表明燃油箱设计应该减少大平面区域结构设计,结合仿真分析结果可选择出油箱结构的最佳方案。目前国内多数汽车配件供应商采用的开发路线基本是遵循产品初期设计、样品制造再到试验的开发线路,此种传统设计方法的需要进行多次修改设计数据,多次样品制造和试验,开发周期长,对于目前飞速发展的汽车行业来说,缩短开发周期就显得尤为重要。随着计算机的辅助技术发展与进步,结合先进的CAE计算机辅助技术,在设计阶段制造样品前,通过仿真分析来提前预测产品设计前期开发中可能存在的风险点,从而进行针对性的优化和验证。根据有限元仿真分析优化后的数据进行修改设计,避免一些潜在的风险,减少前期开发样品的制造次数,一定程度上既缩短开发周期,又降低了研发新产品的所需要的开发成本。本文对某车型燃油箱在进行正负压强耐压性的台架试验的基础上,进行有限元仿真分析,提出了一种铁质燃油箱在承受正负压强循环变化的耐压性疲劳仿真预测方法。
2. 金属燃油箱
汽车燃油箱是汽车中唯一的燃料能源存放器;根据材质可以分为金属和非金属(多层高密度聚乙烯材料,HDPE)燃油箱;金属燃油箱一般由上、下壳体、防浪隔板、吊耳加强板、隔热板等部件组成;箱体上安装有油泵、阀体、传感器、油管等附件 [3]。
3. 燃油箱耐压性台架试验
随着现代科技的发展与进步,目前许多的汽车行业为了更加快速地开发汽车新产品占领市场,许多的零部件就必须在前期就要完成相应的性能保障测试,从而衍生了快速完成实验的方法——台架试验。台架试验可以短时间内快速地测试出零部件的疲劳耐久性能是否达标,在批量生产前避免一些设计缺陷或者存在的隐形问题等,从而缩短开发周期。本文针对某车型的燃油箱在进行的台架试验中出现的开裂问题进行分析与优化验证,得出一种关于油箱耐压性疲劳的仿真分析方法。
3.1. 试验条件
如图1所示,在试验开始前,燃油箱需要按照汽车正常使用情况下安装燃油箱的所有附件,同时封堵燃油箱与外部的所有通口,再进行试验。
测试项目:正负压试验
1) 测试设备:正负压脉冲综合试验机
2) 实验室环境条件:室温
3) 参考标准:金属燃油箱进行正负压脉冲试验,测试完成后,燃油箱能正常使用,不能泄露或者破损情况。
4) 脉冲试验技术条件:
循环次数:12,000;
循环频率:4 cycles/min;
正压:15.0 kPa,负压:−7.0 kPa;
内部加75%额定容积的水。
3.2. 某车型燃油箱的正负压试验结果
对某车型设计阶段初期的三个燃油箱样件进行了产品耐压性试验,三个样件均在测试过程中还未达到试验要求的次数,油箱上壳体相同位置的焊接边缘出现了开裂,开裂位置如图2所示。
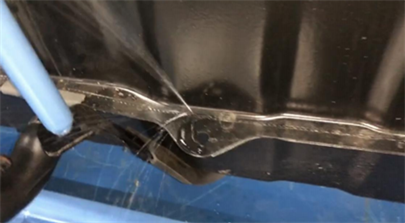
Figure 2. Location of fuel tank cracking
图2. 燃油箱开裂位置图
对于同批次样件燃油箱进行样件检测,各项要求均满足图纸要求。且燃油箱材料(DC04)力学性能满足要求,屈服强度:120~270 MPa,抗拉强度:270~350 MPa [4]。
排除了设计及制造问题,初步判断主要是油箱在承受正负压强循环载荷作用下引起燃油箱开裂,样件局部位置可能存在应力集中且产生疲劳损伤,在足够多的循环次数下导致疲劳断裂。
4. 仿真分析
结合台架试验对样品的试验边界条件,以及测试过程,利用CAE仿真技术,按照台架试验的测试条件,对此款开裂的燃油箱进行有限元建模仿真分析,根据分析结果得到油箱可能潜在的风险点位置,最后将分析结果与台架试验结果对比,观察有限元分析结果趋势显示的风险位置是否和台架试验中开裂位置相吻合,在结果趋势与开裂位置基本一致的情况下,再将结果进行耐压性疲劳耐久分析即可得出相应的疲劳分析结果。
4.1. 有限元模型建立
根据燃油箱的几何数据,对燃油箱上、下壳体、加强板、绑带、减震橡胶垫进行几何处理、有限元网格的划分,同时做好相关焊点、滚边焊以及螺栓连接等;其中上、下壳体进行10 mm片体网格划分,绑带、加强板进行5 mm片体网格划分,单元类型采用缩减积分单元S3R、S4R,橡胶垫采用10 mm的六面体(三层以上)实体网格划分,单元类型为C3D8H;同时考虑材料的非线性和几何性。如图3所示。

Figure 3. Finite element model of fuel tank
图3. 燃油箱有限元模型
4.2. 静态分析
根据实际的台架试验边界条件,对有限元的模型螺栓安装孔位置以及橡胶减震垫与车身接触的位置进行全约自由度(spc = 123456),橡胶与油箱接触的位置保留接触处理。加载条件:在燃油箱上、下壳体内箱壁上法向施加单位压强P = 1 KPa进行仿真计算,得到单位压强下的油箱壳体的强度分析应力结果,壳体应力云如图4所示(其中A、C、D为上壳体焊接边靠近圆角位置应力相对较大的点,B点为箱体上端面特征位置的点)。

Figure 4. Cloud diagram of fuel tank intensity results (unit pressure)
图4. 燃油箱强度结果云图(单位压强)
上壳体应力结果如下表1。
从静态仿真分析结果来看,在加载1 KPa压强作用下,最大应力位置为上壳体圆角靠近滚边焊位置处C点处,即开裂位置的应力为29.8 MPa,此位置处存在明显的应力集中,其他位置点未出现开裂现象,但仅单方面从应力的结果还无法进行油箱的相关循环耐压性能的评估,因此需要在此结果的基础上再进一步开展耐压疲劳的仿真分析。
4.3. 疲劳寿命分析
目前疲劳理论可归纳为以下三类:线性疲劳累积损伤理论、修正的线性疲劳累积损伤理论和非线性疲劳累积损伤理论。线性疲劳累积损伤理论认为在循环载荷作用下,疲劳损伤是可以线性地累加的,各个应力之间相互独立和互不相关,简称Miner理论 [5] [6]。在工程类问题中,一般采用的是比较直接和简便的Miner线性疲劳累积损伤求和。
若构件在k个应变水平
作用下,各经受
次循环,则总损伤D为:
(1)
式中,
是在
作用下的循环次数,由载荷谱给出;
是在
下循环到破坏的寿命,由E-N曲线确定。根据Miner线性疲劳累积理论的破坏准则:
(2)
式中,D为总损伤值,D = 1代表失效。
根据前面静态分析结果得到结构在单位压强下的的强度应力特征响应,结合油箱耐压性台架试验载荷谱以及油箱壳体的材料E-N曲线(如图5),利用E-N静态疲劳分析方法对燃油箱的上、下壳体进行相应的疲劳寿命分析。
通过分析得到相关的疲劳分析结果,结果显示:在单次循环下燃油箱上壳体圆角附近的滚边焊位置C点处最大损伤0.118‰,根据Miner线性疲劳累积理论的破坏准则,即此位置循环次数约为8460次,未达到目标要求,存在较高的疲劳开裂风险,损伤情况如图6所示。
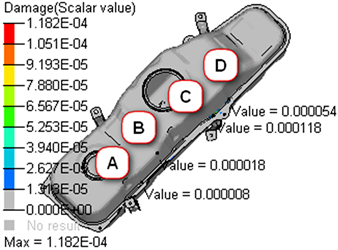
Figure 6. Cloud diagram of oil tank fatigue damage results (single cycle)
图6. 油箱疲劳损伤结果云图(单次循环)
上壳体单次循环损伤结果如下表2。
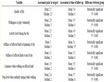
Table 2. Damage value at each position
表2. 各位置点损伤值
从分析结果来看最大损伤位置出现在滚边焊靠近圆角处,点与耐久台架试验的燃油箱开裂位置基本吻合。故验证了导致燃油箱试验过程中出现开裂的原因是油箱在承受交变压强的(循环)载荷下,产生疲劳裂纹,在足够多的循环扰动作用下最终出现开裂问题。
5. 优化验证
从疲劳仿真的分析结果看,再结合实际,开裂位置发生在滚边焊靠近圆角的位置,且该位置型面较为平整,刚度相对较差,圆角位置存在减薄率,同时滚边焊在焊接时会对母材造成一定的焊接损伤,综合评估开裂原因是该位置在交变压强循环作用下引起的疲劳开裂,故采用增加结构特征或者型面优化的方法针对该位置点进行优化,在该开裂位置附近的型面上增加加强筋,提高该位置的局部刚度,降低风险位置的应力和减小该位置在压强作用下的变形。
优化后重新建模,选择方案中最优方案重新进行单位压强下的强度和耐压性循环疲劳耐久的仿真分析,其中单位压强下的强度分析结果和疲劳耐久结果分别如下图7、图8所示。
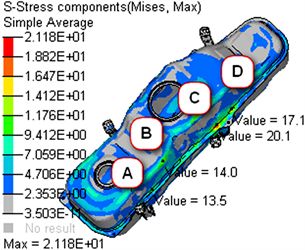
Figure 7. Cloud diagram of strength results of optimization scheme (unit pressure)
图7. 优化方案的强度结果云图(单位压强)
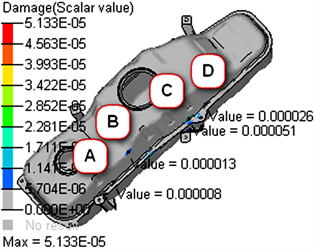
Figure 8. Cloud diagram of fatigue damage results of oil tank optimization scheme (single cycle)
图8. 油箱优化方案疲劳损伤结果云图(单次循环)
在单位压强下原开裂位置的应力由29.8 MPa降低到20.1 MPa;在单次循环下燃油箱上壳体圆角附近的滚边焊位置的最大损伤由0.118‰降低到0.051‰ (见图8),根据Miner线性疲劳累积理论的破坏准则,即此位置循环次数约为19,480次,较原方案寿命提升了1.3倍。原方案与优化方案结果对比如下表3。
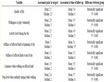
Table 3. Comparison of damage values between the original state and the scheme
表3. 原状态和方案的损伤值对比
最终选择此优化方案进行新的样件制造,经再次进行燃油箱耐压性台架试验验证,无试验样件开裂。
6. 结语
本文利用对燃油箱总成进行有限元建模,从而对燃油箱的耐压性进行疲劳仿真分析,并将计算机仿真结果与本文针对的燃油箱试验中箱体出现疲劳开裂的问题对比,提出了一种基于台架试验载荷的燃油箱的耐压性疲劳仿真分析方法,同时优化解决了某车型燃油箱在开发验证阶段耐压性疲劳耐久台架试验中出现的开裂问题。为后续多款车型的燃油箱在设计初期结构的设计以及性能的优化提供有力的技术支持和指导;通过仿真早一步发现并解决问题,很大程度上缩短产品的开发周期。本文的耐压性疲劳仿真预测方法具有较强的工程实用性,同样适用于其他同类型产品的耐压性疲劳耐久的问题分析与研究。