1. 引言
汽车轻量化是汽车产业实现节能减排的主要方式,而铝合金、超高强钢等轻量化材料,是实现汽车轻量化的重要手段。铝合金因其密度低,比强度高,可回收等特点被广泛应用于汽车内、外板。由于铝合金材料属性与钢不同,点焊拉剪接头的断裂模式、接头的承载力与钢有着明显的不同。
Pereira等人 [1] 研究了不同焊接参数下6082-T6铝合金接头的拉剪试验和接头硬度,指出熔核直径与拉剪强度线性正相关,并总结出了接头在不同断裂模式下的拉剪强度计算公式。Hassanifard [2] 研究了电极压力对1.5 mm 5083-O铝合金点焊接头疲劳裂纹萌生的影响,发现提高电极压力,熔核尺寸变小,疲劳裂纹延缓萌生,接头疲劳寿提高命。此外,该作者 [3] 基于建立的ANSYS有限元模型分析了5182-O疲劳样件的疲劳裂纹扩展路径,有效预测了裂纹的扩展路径。Han等人 [4] 研究了5754铝合金接头拉剪性能,发现拉剪性能取决于焊核直径,随后根据熔核直径和力学性能数据,拟合出了拉剪性能与熔核直径间的函数关系。R.S. Florea等人 [5] 研究了6061-T6铝合金点焊接头的晶粒尺寸与分布,发现熔核中心晶粒细小,边缘晶粒粗大,承载拉剪强度低,裂纹沿界面扩展。WU [6] 通过研究2 mm AA6111铝合金点焊接头的微观组织,显微硬度,发现点焊接头熔核内部硬度比热影响区低,认为在十字拉伸过程中发生界面断裂的原因取决于熔核和热影响区的硬度。由此可见,上述研究没有建立不同属性区域点焊接头拉剪过程有限元模型,未分析拉剪过程中裂纹的扩展路径,不能有效的预测接头的断裂模式及拉剪承载力。
本文以1.0 mm AA6061-T6铝合金为例,基于熔核区、热影响区、母材区赋予不同材料属性的接头拉剪过程有限元模型,分析拉剪过程中裂纹的扩展路径。结合断口处形貌,分析断裂原因。根据接头断裂模式,推导接头拉剪确定预测公式,并对该公式的可靠性进行验证。
2. 有限元模型
2.1. 建模过程
在Hypermesh软件中进行几何建模和网格划分,建立的FEA模型尺寸均与实际焊接接头尺寸一致,如图1所示。模型共分为三个区域:熔核区、热影响区、母材区;板间无间隙,接头表面无压痕,板材长度为130 mm,搭接宽度为38 mm。考虑到对称性和计算的效率,建立1/2三维模型。对网格进行划分时,根据关注重点,对熔核区和热影响区进行局部网格细化,母材区和夹持区受力简单,进行粗网格划分。然后在LS-PREPOST中设置材料属性,加持区的左侧固定,右侧以3 mm/min速度均匀移动;1/2模型的中心面仅在对称平面内移动。最后用LS-DYNA求解器进行求解计算 [7]。



Figure 1. Geometric size and mesh of Lap-shear fracture model
图1. 拉剪断裂模型几何尺寸及网格划分
2.2. 本构模型及断裂准则
实际使用的铝合金板材各向同性,弹性模型与泊松比与材料有关,与热处理状态无关,因此模型中各个区域的弹性模量为71.9 GPa,泊松比为0.3。铝合金母材的应力应变曲线通过实验拉伸获得,软化区和熔核区材料的应力应变曲线很难通过试验获得。根据公式可获得不同区域的硬度系数,根据硬度系数和母材应力应变曲线可获得相应区域的应力应变曲线,关系如下:
(1)
其中:
为相应区域硬度系数;HV为相应区域硬度;
为母材硬度。
对铝合金熔核表面进行硬度测量,获得硬度分布图,如图2所示,从图中可以看出熔核区内硬度最低约为55 HV,热影响区次之,平均为70 HV,铝合金母材硬度平均为110 HV。
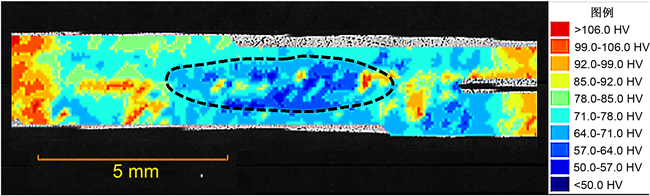
Figure 2. Distribution of hardness in aluminum joint
图2. 铝合金熔核硬度分布
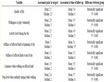
Table 1. Different area geometric size and hardness value
表1. 不同区域几何尺寸及硬度取值
(2)
其中:
为母材应力应变关系;
为相应区域应力应变关系。
根据表1中不同区域的硬度关系,带入公式(2),获得软化区和熔核区应力应变曲线,如图3(a)所示。应力三轴度可以反映出三个主应力,更好的揭示单元的受力状态,铝合金母材的应力三轴度与断裂应变之间的关系如图3(b)黑色曲线所示,基于材料断裂应变定义失效准则 [8] [9]。同理可以根据硬度系数获得热影响区和熔核的应力三轴度与断裂应变的关系。
(3)
其中:
为母材应力三轴度与断裂应变关系;
为相应区域应力三轴度与断裂应变关系。
(a)
(b)
Figure 3. (a) Curve of stress-strain; (b) curve of stress triaxiality
图3. (a) 应力应变曲线;(b) 应变应力三轴度曲线
2.3. 边界条件及加载
图1所示模型中,左端是固定端,施加固定约束,所有节点固定不动;右端为移动端,施加位移边界条件,加载端母材节点匀速移动。由于建立的是1/2对称模型,对称面处节点只能在平面内移动和转动,其余三个自由度受到约束。
2.4. 计算结果
通过有限元的计算,可以获得拉剪过程中接头内部应力应变变化及断裂过程,掌握焊点断裂分析,对整车CAE碰撞模型的分析具有重要意义。从图4所示的Mises应力分布云可以看出,拉剪过程中板材界面与熔核边缘接触区应力最大(图中红色区域),由于拉剪过程中偏心力矩的作用,接头连接处会发生局部偏转。导致红色分布区有沿板厚方向扩展分布的趋势,应力集中区最易产生断裂;在下一时刻,裂纹产生并沿着板厚方向倾斜扩展,贯穿板材,此时熔核边缘和热影响区应力减小。随着时间的延长,裂纹沿熔核周向撕裂熔核,最大应力转移到断裂位置处,熔核内部和热影响区内应力几乎为0。
从图5所示的等效应变云上可以清晰的观察到拉剪过程中裂纹的扩展路径,图中绿色区域展示的是最大应变区,断裂处的材料具有较高的应变,当材料的应变达到断裂应变临界值时,材料发生断裂。绿色区域代表裂纹的扩展路径。从图中看出裂纹产生于板材界面与熔核边缘交界处,由于试件受到不对称的作用,在接头中心会产生弯矩,接头倾斜,裂纹沿板厚方向倾斜向上撕裂母材。当裂纹贯通母材后,裂纹沿熔核周向扩展直至将熔核拉出,此时拉剪力逐渐降低,直至降为0。
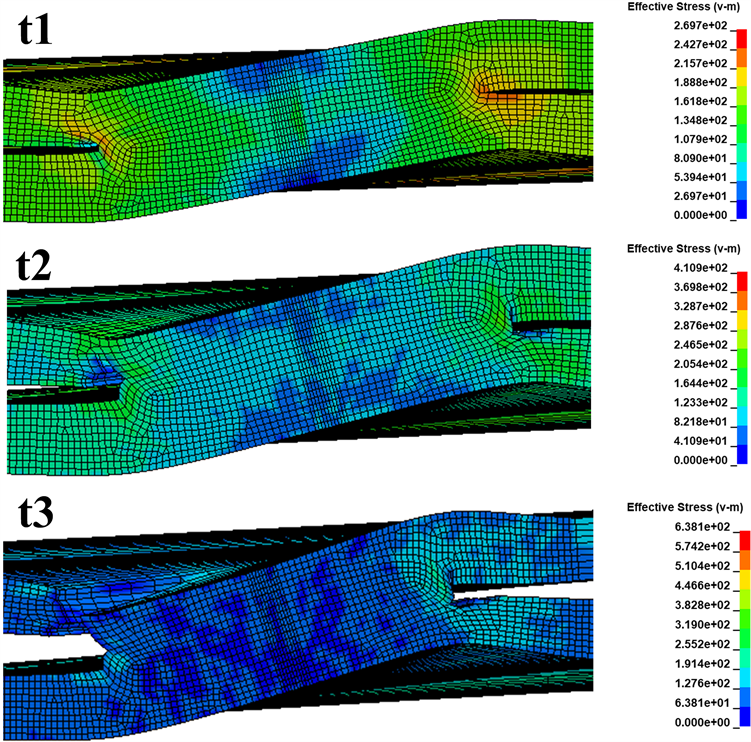
Figure 4. Stress change during lap-shear fracture (t1 = 3.89 s, t2 = 15.97 s, t3 = 22.64 s)
图4. 拉剪断裂过程中应力变化(t1 = 3.89 s, t2 = 15.97 s, t3 = 22.64 s)
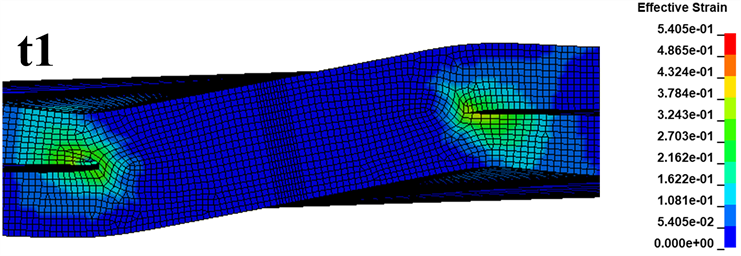
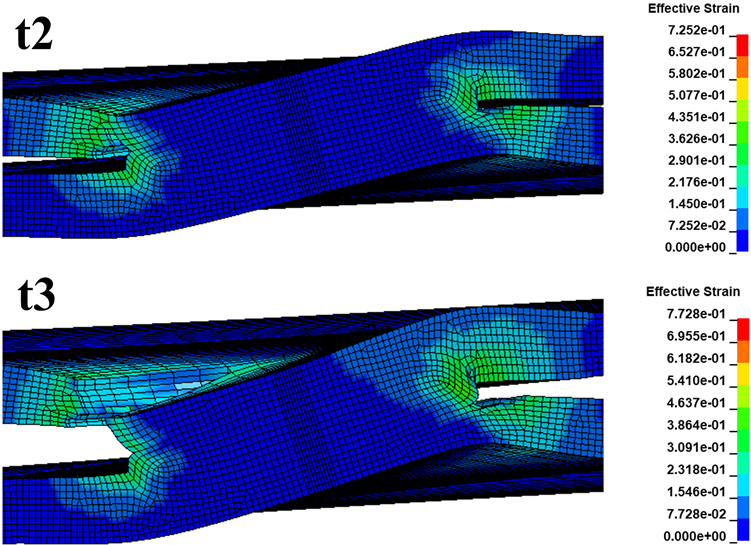
Figure 5. Strain change during lap-shear fracture (t1 = 3.89 s, t2 = 15.97 s, t3 = 22.64 s)
图5. 拉剪断裂过程中应变变化(t1 = 3.89 s, t2 = 15.97 s, t3 = 22.64 s;单位:%)
3. 实验验证
3.1. 实验材料与方法
本文所用材料为1.0 mm铝合金AA6061-T6,实验装置为Centerline公司C型中频直流伺服焊枪,采用凸点辅助铝合金点焊工艺,在点焊前,采用CMT工艺将4043焊丝先在板材上预置凸点,然后在凸点处进行点焊,凸点辅助点焊工艺如图6所示,电极端面直径为15 mm [10]。
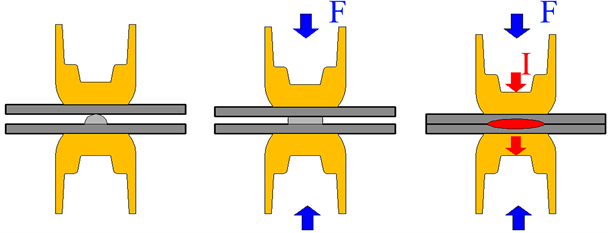
Figure 6. Diagram of bump assisted spot welding
图6. 凸点辅助点焊示意图
焊接参数为多段脉冲焊接,分为预热脉冲,焊接Ⅰ,焊接Ⅱ。预热脉冲为200 ms,18 kA;焊接Ⅰ脉冲为100 ms,27 kA。焊接Ⅱ脉冲为三段脉冲,分别是25 ms,24 kA;25 ms,27 kA;25 ms,30 kA。焊接时序如图7所示。
3.2. 实验结果与讨论
焊接后熔核的直径为6 mm,热影响区直径为11.2 mm,拉剪断裂模式为纽扣断裂,如图8所示。
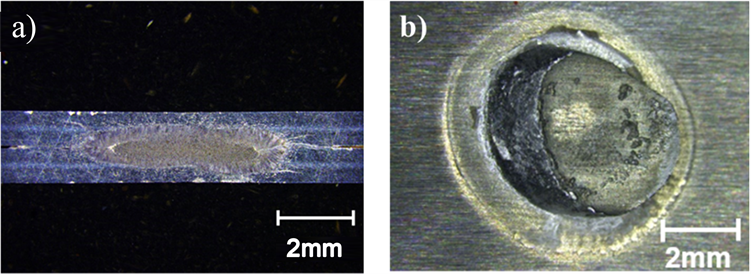
Figure 8. (a) Nugget morphology; (b) morphology of lap shear joint
图8. (a) 熔核形貌; (b) 拉剪断裂形貌
对比仿真结果和实验力位移曲线,两者曲线基本重合,断裂模式也一样。随着拉剪过程的进行,接头的承载力逐渐增加,当裂纹刚开始产生时,拉剪力达到最大值。随着裂纹的产生,裂纹沿板厚方向倾斜向上撕裂母材,由于板材局部已经出现失效,拉剪力迅速下降,如图9过程①到②。
裂纹在起初扩展的时候,先沿熔核边缘与板材交界处扩展,然后转向撕裂母材。对断口表面放大观察,可以发现断口表面存在塑性变形和剪切韧窝,接头在拉伸过程中,断裂裂纹为韧性,当裂纹扩展到缩孔等缺陷时,韧性断裂终止,随着拉伸的进行裂纹绕过缩孔,继续韧性断裂,如图10所示。
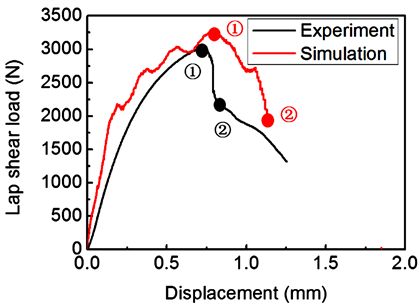
Figure 9. Comparison of simulation and experiment result
图9. 仿真结果与实际结果对比
3.3. 拉剪强度预测
对于材质均匀的铝合金材料,剪切极限强度与抗拉极限强度具有线性关系 [11],如公式4所示,由于熔核区内金属受热软化,熔核强度与原始母材强度不同,公式5反应了材料间强度和硬度的关系 [12]。
(4)
(5)
(6)
对于纽扣断裂,熔核沿热影响区向上拔出,断裂过程近似于正拉,如图11所示。承载区为以熔核直径为底面直径、板厚为高所在圆柱面,断裂强度为热影响区材料的剪切极限强度,如公式7。根据热影响区内硬度和熔核直径就可以计算发生纽扣断裂时的拉剪力,带入得到公式8。
(7)
(8)
调整焊接电流大小,得到不同熔核尺寸的工件,进行拉剪实验。根据表1不同区域硬度值,带入公式8绘出图12中虚线所示熔核直径与拉剪强度关系。图中红色圆圈为发生纽扣断裂接头熔核直径和拉剪强度坐标。对比理论曲线和实际坐标点,两者具有比较好的一致性,验证了理论计算公式的准确性。
4. 结论
本文主要研究了铝合金AA6061-T6电阻点焊接头拉剪断裂过程及拉剪强度与熔核尺寸的关系。建立拉剪断裂的仿真模型,研究接头在拉剪过程中,应力应变的变化及裂纹断裂路径。通过与实验结果对比,验证了模型的准确性。建立了基于熔核直径的拉剪强度计算公式,为预估拉剪强度提供便捷。具体结论如下:
1) 拉剪过程中对于纽扣断裂,裂纹产生在熔核边缘,随后沿板厚方向撕裂母材,最后沿熔核周向扩展,直至拉出。
2) 观察接头拉脱表面,发现存在塑性变形和剪切韧窝,在板厚的中间区域韧窝明显。
3) 熔核直径在5.5~6.5 mm,拉剪强度预测值与实际有较好的一致性。
参考文献