1. 引言
电机作为一种能量转换设备在日常生产生活中具有举足轻重的作用,是一种重要的机械系统原动机 [1]。在对电机的性能进行评价的指标中,除了将热转化为功的热效率外,电机的输出特性也是问题的重点。其中常以输出功率和电机自身重量的比值当作评价电机输出性能的重要指标,称为功率密度,表征单位电机质量能提供的输出功率 [2]。功率密度越大,电机的输出性能越好;功率密度越小,则电机的输出性能越差。为提高电机的输出性能,提升其高功率密度是最重要的方式 [3] [4]。高功率密度电机受到其散热性能制约。如果电机本身热量不能及时散去,其性能会受到高温影响而降低,严重者甚至会造成电机烧毁等问题。传统电机的散热方式有风冷、水冷、油冷等。风冷采用空气进行散热 [5] [6] [7],水冷采用水来散热 [8] [9] [10] [11],油冷采用油来散热 [12],此外还有一些混合散热方式,如采用蒸汽 [13]、水雾 [14] [15] 散热方式等。但这些方式的原理都是利用流体将电机内部产生的热量传递到流体中,然后利用流体的流动将热量排出电机体外。然而,由于流体的比热容以及导热系数的限制,这些散热方式不能完全满足电机的散热需求,特别是电机在某些过载工况下,产热量激增,电机的散热越发显得困难。为了解决高功率密度电机在短时过载情况下的发热问题,本文特提出一种不同于传统电机的散热方式,采用冷热中和的原理,提高传热温度差以增加散热效果,保证电机短时内能够稳定运行,降低由于温升导致的电机失效问题。
2. 短时过载散热方案设计
2.1. 方案原理及设计
针对高功率密度电机短时过载情况下的高产热问题,本文设计一种高功率密度电机瞬时冷却方案,在满足电机高功率输出的同时,将热量去除,使其在短时过载的情况下,也能保证正常的散热需求及较高的电机性能。
具体的方案流程如图1所示。首先,根据前期研究完成的优化电机 [16] [17] 在运行过程中需要判断电机运行模式,在额定工况运行过程中,采用常规水冷方式冷却电机柱面,同时监测电机温升状况,一旦出现温升过高等情况,适当增大水流速度,增加散热能力。当电机处在过载运行模式下,采用水冷与冷热中和散热模式。冷热中和散热模式是指提前在储藏器中储存一定冷却介质,当电机温升过高时释放冷却介质,中和电机产热,达到降温效果。实验过程中实时监测电机温升状况,当电机温升过高时,适当增加冷却介质释放速度。
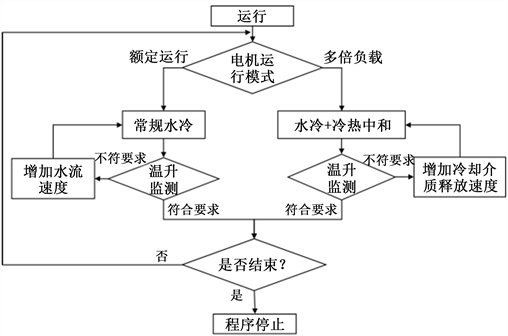
Figure 1. Selective flowchart of motor dissipation mode
图1. 电机散热模式选择流程图
按照前文所述的电机散热方案及流程,完善电机结构布局如图2所示,冷却介质储藏器分布在电机两端,主要对电机中热损耗比例较大而温升最高的端部绕组进行针对性的散热。
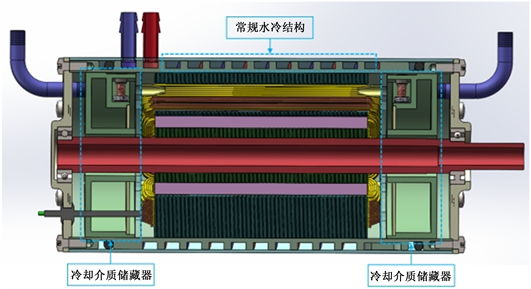
Figure 2. Design diagram of cooling of temporary overloaded motor
图2. 短时过载电机冷却方案设计示意图
通常端部绕组的温度最高,将其设为
,冷却介质从储藏器中喷出,温度极低,设为
,则利用牛顿冷却公式可得:
(1)
其中h为对流传热系数,单位是
; 为热流密度,单位是
。在高温环境下,储藏器中的冷却介质升温膨胀,从排放出口喷出时的冷却介质温度很低。而电机端部是所有部位温度较高并且难以冷却的区域,因此两个区域之间的温差
很大。此外,当冷却介质从排放出口喷出时,具有较高的流速,因此其对流传热系数h相对于传统对流方式来说更大。其最终结果将使得端部绕组的温度被大量带走,限制绕组铜线的升温,使其能在更大的电流下完成工作,并进一步提高功率密度。
冷却介质储藏器结构如图3所示。在电机工作前,为储藏器注入低温液态冷却介质(本实验为液氮),在电机温升过高时,储藏器中的冷却介质吸热气化,使容器内压力增加,气化后的气态冷却介质经由泄压阀释放到气体均压室中,再经由低温气体排放出口排放到电机定子绕组端部,对定子绕组端部进行冷却,达到冷热中和降温的效果。该散热方式能够最大限度的避免常规散热方式受热传递系数影响的问题,很好的解决了短时过载散热问题。
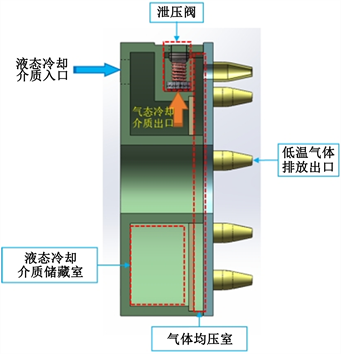
Figure 3. Design diagram of cooling of temporary overloaded motor
图3. 短时过载电机冷却方案设计示意图
2.2. 短时过载散热结构性能测试
对该方案的冷却介质储藏器进行原理样机加工装配,并灌注低温介质(液氮)进行试验,并测量相关位置温度。如图4所示,将测点一放置在喷出口边缘,测点二放置在气体均压室内部。利用双通道测温设备对其出口喷出的冷却介质气体进行测温,温度如图5所示,出口处温度为−43.0℃,其中腔体内气体温度能够达到−165℃。
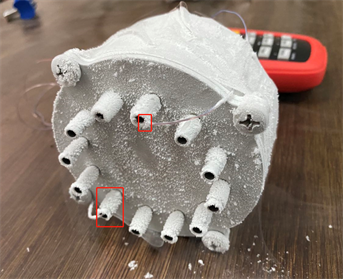
Figure 4. Contact of temperature measurement
图4. 测温触点

Figure 5. Result of temperature measurement
图5. 测温结果
3. 试验分析
将上述冷却介质储藏器安装到电机中进行测试试验,图6所示为电机输出性能测试系统的实物图。该测试系统主要由电涡流测功机、转矩转速传感器、三维工作台、交流电参数测量仪、控制柜、变频器和冷水机组成。交流电参数测试仪通过变频器将交流电转化为直流电以给电机供电,并设定电机运行模式。电机工作过程中启动水冷机给电机柱面供水进行水冷。电涡流测功机与电机轴连接检测输出转矩,记录试验参数。该电机输出性能测试系统能够在电机运转过程中对电机输出特性进行实时测试,通过联轴器将电机的输出轴和转矩转速传感器相连,收集电机的输出性能信息,得到输出性能曲线。

Figure 6. Experiment platform of motor test
图6. 电机测试试验台
试验过程的通用设置为:将额定功率为4 kW的电机固定在平台支架上,通过联轴器与电涡流测功机相连。然后启动水冷机,往电机柱面注入循环流动水以模拟正常工作环境。一切就绪后启动变频器给电机通电,设置变频器参数让电机空载达到额定转速12,000 rpm,计算机将控制电涡流测功机,通过联轴器对电机加载,并实时监测电机的电流、输出扭矩、输出功率等参数,载入计算机测试软件中。此外还通过测温设备测量电机的实时温升。
本试验采用分别采用两种情况对电机进行测试,一种是不增设冷却介质储藏而在通常额定工况下运行的情形,另一种是增设冷却介质储藏器并提高电机功率短时过载的情形。通过比较两种不同情况下相同电机的输出特性和实际温升,对比得到冷热中和的实际效果。
4. 试验结果及数据分析
为了对比试验效果,以电机额定工况下的参数作为参考,首先测量电机额定工况下的运行情况及数据参数。
在无冷却介质的情况下,针对电机以扭矩值作为横坐标轴绘制电机输出特性曲线如图7所示。通过电机输出功率特性和机械特性曲线可以看出,电机输出功率可以达到4 kw的额定功率。同时电机效率也趋于稳定值,维持在80%以上。电机样机的质量为1.996 kg,按照额定功率4 kw计算,样机功率密度为2.004 kW/kg。在电机输出功率达到4 kw时,电机绕组内部温度通过预埋的PT100温度传感器进行测量其核心温度为80.2℃。利用温度测量仪表测量绕组端部温度值为50.1℃。
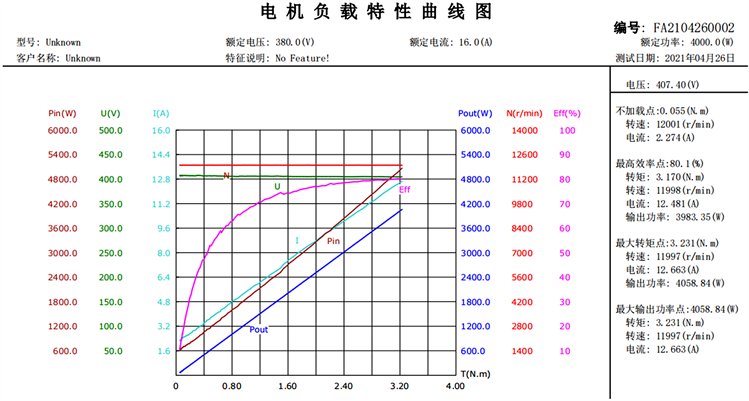
Figure 7. Motor characteristic curve in rated environment
图7. 额定工况下电机特性曲线
接下来测量电机短时过载工况下的运行情况及数据参数,同样以扭矩值作为横坐标轴绘制电机输出特性曲线如图8所示。通过电机测试数据可以得到,提高电机输出功率达到4.319 kW。相应地其输出扭矩同时测得核心温度为67.8℃。绕组端部温度值为29.8℃。
通过数据对比分析可以看出,在有冷却介质降温的情况下,相比于无冷却介质的情形,绕组核心温度由80.2℃下降到67.8℃,温度下降15.46%,绕组端部降温更加明显,由50.1℃降到29.8℃,降温幅度达到40.52%,同时,电机功率提升7.97%,电机功率密度可以达到2.164 kw/kg。因此,冷却介质储藏器能够有效提升电机的整体散热性能。在同功率4 kW情况下,添置有冷却介质储藏器的电机整体上温度更低,电阻的热阻率降低,从而电机所做的无用功减少,得到更高的效率和功率密度,提高了电机的输出性能。

Figure 8. Motor characteristic curve in temporary overloaded environment
图8. 短时过载工况下电机特性曲线
5. 总结及结论
针对高功率密度电机过载运行过程中产热较高的问题,创新性地提出一种基于冷热中和的方式,通过方案设计、样机试验测试,使高功率密度电机绕组核心温度下降15.46%,绕组端部降温幅度达到40.52%,同时,电机功率提升7.97%,电机功率密度可以达到2.164 kw/kg。解决了电机短时过载中产生的热量问题,保证电机短时内能够稳定运行。
基金项目
国防科技创新特区项目(1816321TS00100901)。