1. 引言
爆炸焊接,又称爆炸复合,1944年由美国的L.R. Carl [1] 首先提出;1959年美国学者V. Philipchuk [2] 在铝料的爆炸成型过程中偶然发现铝钢的爆炸焊接现象,并预言了其可能成为一种有用的方法;此后,人们逐渐认识到了爆炸焊接技术的潜在应用性,美、日、英、德、瑞典和苏联相继开展了爆炸焊接的理论及实验研究,使爆炸焊接技术日趋走向成熟。国内从1960年左右开始研究爆炸焊接技术,1968年大连造船厂陈火金同志成功实现了第一块复合板的爆炸焊接 [3]。经过近60年的迅猛发展,爆炸焊接技术已成为金属产品加工工艺中最具特色的一种。
通过爆炸复合法制备的层状金属复合材料,因兼具基复层金属各自的优点,可获得单一材料所不具备的物理和化学性质,从而可节约大量的有色金属和稀有金属,大大降低生产和使用成本。目前,通过爆炸复合法技术已成功研制了钢/钢、铝/铝、钢/不锈钢、钛/钢、钛/不锈钢、锆/钢、铜/钢、铝/镁、铜/铝、铝/钛/钢等金属复合板 [4] [5]。
钛/钢复合板属于比较常用的爆炸焊接产品,目前已广泛应用于石油化工、电力设备、核工业及海洋勘探等领域 [6],但是对于钛/钢复合板工艺研究仍不是十分完善。本文中使用不同爆炸复合工艺制备了一系列钛/钢复合板,研究了不同工艺下钛钢复合板的金相组织、显微形貌、显微硬度和结合强度的变化情况,通过实验分析优化确定了最佳工艺参数。
2. 实验部分
2.1. 原材料
实验所用钛板牌号为TA1,符合标准GB/T 3621-2007,钢板牌号为Q345R,符合标准GB 713-2014,钛和钢的主要化学成分见表1和表2,试板尺寸和原材料显微硬度见表3。
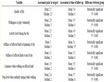
Table 1. Chemical composition of raw material of titanium plate
表1. 钛板原材料化学成分
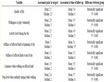
Table 2. Chemical composition of raw material of steel plate
表2. 钢板原材料化学成分
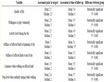
Table 3. Raw material specifications and microhardness of test panels
表3. 试板投料规格及显微硬度
2.2. 复合材料制备
本文中爆炸焊接时使用平行安置法,在复合板短边中心起爆,试验炸药为某型爆炸复合专用炸药,爆速1800~2500 m/s,具体爆炸复合装置见图1。按照不同工艺制备了5组复合板,编号分别为1、2、3、4和5,详见表4。

Figure 1. Schematic diagram of the explosion welding device
图1. 爆炸焊接装置示意图
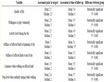
Table 4. Number and process of TA1/Q345R composite plate
表4. TA1/Q345R复合板编号和工艺
由于爆炸复合加工方法的特殊性,基复板界面附近会发生剧烈的塑性变形,造成区域硬化,给后续加工、使用带来不利影响,因此对其在电炉中进行540℃/2h的退火热处理 [7] [8]。
2.3. 复合材料的表征
利用光学显微镜观察了TA1/Q345R复合板的微观组织结构,取样位置在距离起爆点450 mm处,通过半自动显微硬度计检测样品维氏硬度,载荷200 gf,保压时间15 s。使用万能试验机对复合板的剪切强度进行了测试,在距起爆点400 mm处切取试样,见图2,为防止火切割的热影响区,切割方法为线切割,每个工艺下取三个样进行剪切试验,结果取平均值。

Figure 2. Sketch map for sampling for shearing and metallographic test
图2. 剪切和金相试验取样位置示意图
3. 结果与分析
3.1. 超声波检测
完成爆炸复合后,复合板外观良好,无裂纹或宏观缺陷,经超声波探伤检测后,除雷管区外,其余部分全部结合,结合率在99%以上。
3.2. 界面处显微组织分析
图3为不同工艺条件下TA1/Q345R爆炸焊接复合板的界面处显微组织形貌,图3(a)和图3(b)为1号工艺条件下的界面组织形貌,图3(c)~(f)分别为2、3、4和5工艺条件下的界面组织形貌。理论上,爆炸焊接的界面结合方式主要有三类:金属间的直接结合、连续的熔化层结合和波状结合。整体来看,五种
(a) 间隙S,药高H-20,100×;(b) 间隙S,药高H − 20,200×;(c) 间隙S,药高H − 10,100×;(d) 间隙S,药高H,100×;(e) 间隙S,药高H + 10,100×;(f) 间隙S,药高H + 20,100×。
Figure 3. Microstructure of TA1/Q345R composite plate under different process
图3. 不同工艺下TA1/Q345R爆炸焊接复合板界面组织
工艺条件下都形成了波状界面,波状结合界面增大了金属间的实际结合面积,有利于增强界面结合强度。在爆炸焊接中,由于压力的波动对金属射流的影响,会在波形的前端形成漩涡,一般情况下只要漩涡能对例如金属间化合物等缺陷进行良好的约束,在复合板承载时,不易发生缺陷的扩展 [4]。
通过一系列实验金相的对比可以看出,1号试样的成波波形较小,且前端漩涡外和波背上有金属间化合物,漩涡内也未将几种物质的机械混合物(金属间化合物、孔洞、基体金属碎块、待焊板面污染物和中间空气层等)完全包裹。因此,1号试验的工艺从金相上判断是5组里边最差的,推测原因可能是由于炸药的能量不足导致碰撞角和复板飞行速度不够。1~4号试样在其他因素一定的条件下,随着药厚的增加波形趋于规律且漩涡内的机械混合物变少,有利于界面的高结合强度。通过5组试样整体比较可以得出1至4号试样的硬脆相越来越少,4号试样的界面处和波前端漩涡处的硬脆相最少,而硬脆相的减少就能避免裂纹扩展保证界面的结合强度,5号试样的界面硬脆相虽然也少,但是波幅比2、3和4号试样的低,表5是五组钛/钢复合板的波幅比,原因可能是到达爆炸窗口工艺上限,而较大的波幅比相当于增加了结合面积和机械咬合。因此,根据金相分析结果显示4号试样的金相界面最好。
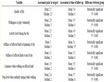
Table 5. The wave amplitude ratio of TA1/Q345R composite plate
表5. TA1/Q345R复合板波幅比
3.3. 界面附近硬度分析
图4为不同工艺条件下TA1/Q345R爆炸焊接复合板结合界面附近的显微硬度曲线,取样位置为起爆对边中心结合区100 mm处,整体来看,越靠近界面处显微硬度越高,且在一定范围内随着与界面距离的增大而减小,5号的最高硬度可达319.1 HV,主要是由于热效应下的再结晶和结合界面处在高速碰撞时产生的剧烈硬化效应所引起的。其次,对比前五组实验,可以得出在其他参数一定的条件下,结合界面的硬度随着布药高度的增加而增大,主要是因为随着药高的增加,炸药的能量增大,从而使结合界面处的碰撞速度增大,进而使得界面塑性变形引起的硬化效应更明显。另外,还可能有以下原因:① 炸药引爆的瞬间,结合界面是在高温、高压和高应变速率下进行的,高温下的界面以106~107℃/s冷却速率冷却时,类似于淬火效应,则会导致界面硬度值提高;② 爆炸焊接后界面冷却快加上碳来不及偏析,形成了碳在铁中的饱和固溶体,从而产生界面硬化 [9]。
3.4. 剪切强度分析
复合板的剪切试验,能够较准确的反应界面结合强度,因此参照GB/T6396-2008《复合钢板力学及工艺性能试验方法》进行了测试,剪切测试结果见图5。1号样的剪切强度最小为246 MPa,4号样的剪切强度最大为267.5 MPa,远高于《NB/T 47002.3-2019》标准要求的140 MPa,在剪切试验中,钛/钢复合板断裂都发生在界面处。对比1、2、3和4号试样,剪切强度随着药高的增加而增加,5号试样的剪切强度介于1和2号试样之间,主要还是因为工艺参数到了爆炸焊接工艺窗口上限附近。另外,在结合界面为波状结合的前提下,随着波幅比的增加,复合板的剪切强度也逐渐增加 [9] [10]。因此,结合前边金相分析中的波幅比数据,可以看出4号试样的综合性能最好。
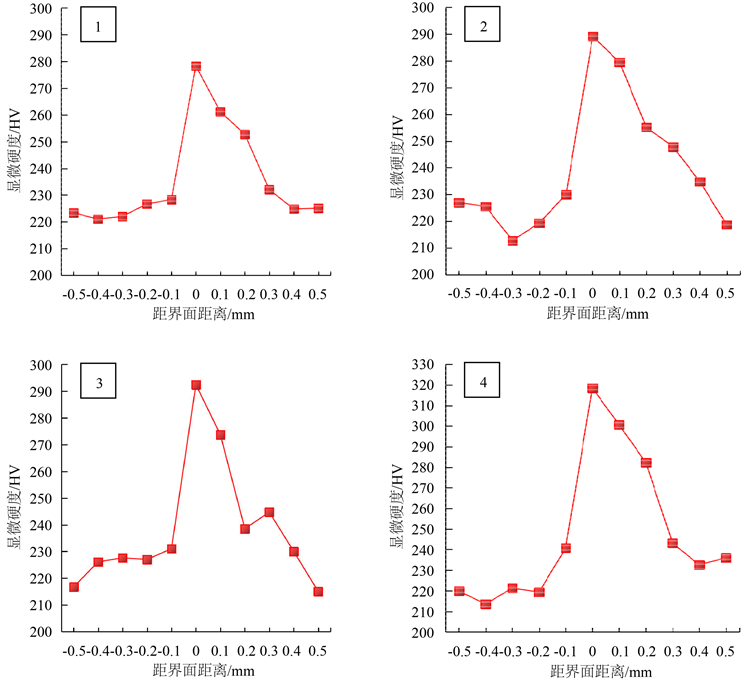
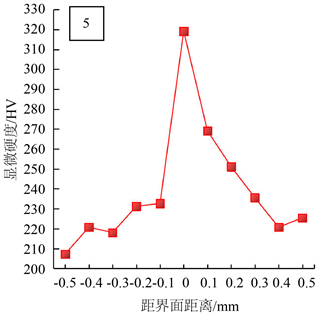
Figure 4. Micro hardness of TA1/Q345R composite plate under different process
图4. 不同工艺下TA1/Q345R爆炸复合板显微硬度
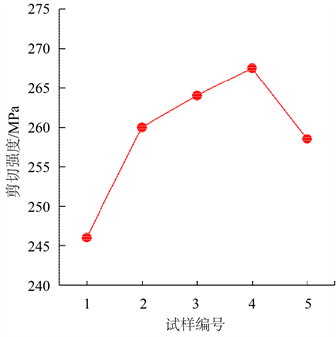
Figure 5. Shear strength of TA1/Q345R composite plate under different process
图5. 不同工艺下TA1/Q345R爆炸复合板的剪切强度
4. 结论
1) 在其他工艺条件一定的情况下,当间隙S mm,药高为H + 10 mm时,金相观测4号复合板界面的硬脆相最少,波幅比为0.27;
2) 爆炸焊接后界面附近发生了明显硬化,5号复合板的界面硬度最高,为319.1 HV;
3) 4号复合板的剪切强度最大,为267.5 MPa;综上,4号钛钢复合板的制备工艺为最佳。