1. 引言
伴随着中国公路桥梁的发展,高墩桥梁施工工艺日渐成熟,桥梁轻型高墩施工技术–薄壁空心墩在公路桥梁施工中得到了广泛应用 [1] [2]。但在高墩桥梁施工中,墩身工期对总工期有重要影响,所以提高薄壁空心墩施工效率,加快施工速度,关注模板设计验算质量也成为急需解决的问题之一 [3] [4]。鉴于此在山西静兴高速公路工程中采取了优化模板受力设计、模板验算和施工组织等方法对翻模法薄壁空心墩施工工艺进行了优化与提高,重点解决了模板的受力设计及验算难点,并规范了施工中的质量控制要点。
2. 薄壁空心墩施工工艺
2.1. 钢筋施工
为保证施工时的质量安全,除在原材料检测方面进行严格控制以外,本项目在施工钢筋加工起始阶段便进行了优化及质量控制。主要优化项目为墩身主筋在工厂直接采用直螺纹连接,相比设计时在现场进行主筋的连接经保守计算每节段节省工期约为0.5天。钢筋加工时严格按照规范施工要求,下料过程中不得用电焊直接切断钢筋,钢筋丝头加工时应添加水性切削液,用于连接的钢筋与套筒规格应一致,连接用钢筋丝头严格执行钢筋连接要求,主筋接长时可采用水平筋和斜筋将整排主筋进行固定。
钢筋加工过程中安排专人进行以上控制要点的检测及监督,确保钢筋一次性加工合格,为下一步施工节约时间,达到控制工程质量的目的,该工艺经优化后具有连接快、操作方式简单、可集中生产、效率高等优点。
2.2. 模板施工
安装模板时首先在墩身四周搭设支架施工平台,然后安装首段墩身模板,对模板进行加固及校正。2、3节段外模板安装时首先采用25 t汽车吊进行分块吊装当达到一定高度后再采用塔吊吊装,相应外模支撑位于首段外模顶部,支撑就位后安装2、3节段内模,最后利用拉杆对拉对墩身模板进行加固,加固措施如图1所示。模板安装顺序为先外模再内模。模板安装就位后进行钢筋笼绑扎及混凝土浇筑,拆模时先测量墩身混凝土强度,达到要求后利用脚手架平台提升吊架及电动导链进行拆模,并放置在指定高度。
墩身施工均按照上述方法进行模板安装、钢筋绑扎、混凝土浇筑,模板拆除,直至完成整个薄壁空心墩身的浇筑。本工程每1节等截面墩身高度为2.25 m、变截面墩身高度为1.5 m,最后墩顶高度按施工图设计标高进行控制。墩身施工图如图2所示。

Figure 1. Reinforcement measures for inner formwork
图1. 内模加固措施
2.3. 混凝土施工
按照薄壁空心墩墩高和施工地区的地理状况,我标段使用汽车泵浇筑法和塔吊结合料斗浇筑方式进行混凝土施工。为保证施工质量及安全,我标段在墩身高度以下30 m使用汽车泵浇筑,30 m以上使用塔吊进行浇筑,每次浇筑1 m3混凝土。我标段自建设有混凝土拌合站,从混凝土加工开始即进行质量控制,严格控制其配合比及塌落度,拌合后用混凝土运输车运至施工现场。混凝土浇筑是施工质量控制的关键阶段,施工时使用插入式振动器振捣,移动距离不得超过振动棒作业半径的1.5倍,插入下层砼5~10 cm。快插慢拔,每一点应振捣至混凝土不下沉,不冒气泡泛浆、平坦为止,振完后应徐徐拔出振动棒。振捣过程中不得碰撞钢筋和模板,谨防其移位、损伤。
2.4. 模板翻升
本标段模板翻升步骤共分为四步,即模板拆解、提升模板、安装模板和加固措施。
当前两节段的墩身混凝土强度达到要求,即可进行模板翻升施工作业,采用小型载人吊篮和内外围带相结合的方法进行模板拆解作业;利用塔吊将拆下的模板放置前一节模板顶部,对模板进行清理并按施工要求规范涂刷脱模剂,然后利用导链对内外模进行临时固定,用向螺栓将安装底口与下层模板联结,最后利用拉杆将已安装好内外模板连接进行加固。本标段模板翻升使用的设备设施主要为内外模板、围带、拉杆、内外模板固定架、作业平台。内外模板由标准板、边模板、角模板组成,模板之间用M12 × 30螺栓连接
2.5. 封闭墩顶
当模板翻升至墩顶封闭段底模设计起点标高时,在内外侧模板上要安装封闭段底模板。采用钢桁架作为其支架,模板采用5 cm厚的刨光木板,拼接时的拼缝要严密,按要求涂刷脱模剂后绑扎钢筋,然后进行外模板、围带、模板固定架、外侧施工平台、防护栏杆和安全网的安装搭设,最后浇筑墩顶封闭段混凝土并养护达到施工设计规定强度。静兴高速公路翻模施工工艺总流程图如图3所示。
3. 模板设计验算要点
本标段桥墩施工时需要的模板需要根据施工图进行模型受力设计及验算,为解决及简化相似翻模模板施工的模板计算问题,并形成本标段模板尺寸受力验算标准。根据施工图墩身节段及有关规范进行模板尺寸及相关参数 [5] 取值,具体尺寸为6.5 m × 2.25 m + 3.5 m × 2.25 m,面板采用6 mm厚钢板,横肋采用18#槽钢,竖肋采用10#槽钢,横肋间距Lx = 350 mm,竖肋间距Ly = 650 mm。
3.1. 面板受力及挠度计算
面板采用四边固结,选用板区格中三面固结及一面简支的最不利受力情况进行计算。Lx取350 mm,Ly取650 mm,由Lx/Ly ≈ 0.55,可得K0x = −0.0827,K0y = −0.0570,Kx = 0.0398,Ky = 0.0042,Kf = 0.00255。取1 mm宽度作为计算单元,则面板的线密度为q = 50 × 1 = 0.05 N/mm,支座弯矩、跨中弯矩、支座弯矩及跨中弯矩产生的最大应力及最大挠度如表1所示。
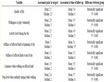
Table 1. Bending moment, stress and deflection table
表1. 弯矩、应力及挠度表
由表1可知支座弯矩产生的最大应力为200.7 MPa < σ = 215 MPa,满足要求。跨中弯矩产生的最大应力为45.1 MPa < σ = 215 MPa满足要求。最大挠度为0.46 mm,挠跨比为1/761 < 1/500,满足要求。
3.2. 横肋计算
横肋采用18#槽钢,间距650 mm,支撑在竖向大肋上,将横肋视为两端带悬臂的三跨连续梁受力结构体系。根据其相关参数,利用迈达斯软件进行横肋受力计算,具体参数如表2所示。
根据表3进行横肋相关的强度及挠度验算,具体计算过程如下所示。
1) 强度验算:
σmax = Mmax/W = 9.3 MPa < σ = 215 MPa,满足要求。
2) 挠度验算:
a) 悬臂部分挠度:ω = q × a4/8EI = 0.009 mm,ω/a = 0.009/275 = <1/500,满足要求。
b) 跨中挠度:ω = q × Lx4(5 − 24 × λ2)/384EI = −0.005 mm,ω/L = 0.005/350 = <1/500,满足要求。
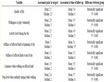
Table 2. Cross rib related parameters
表2. 横肋相关参数
3.3. 竖向肋计算
竖肋采用10#槽钢,间距为500 mm,支撑在横向大肋上,将竖肋视为两端带悬臂的两跨连续梁受力结构体系。根据其相关参数,利用迈达斯软件进行竖肋受力计算,具体参数如表3所示。
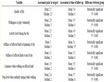
Table 3. Relevant parameters of vertical ribs
表3. 竖肋相关参数
根据表3进行横肋相关的强度及挠度验算,具体计算过程如下所示。
1) 强度验算:
σmax = Mmax/W = 50.4 MPa < σ = 215 MPa,满足要求。
2) 挠度验算:
a) 悬臂部分挠度:ω = q × a4/8EI = 0.27 mm,ω/a = 1/1795 < 1/500,满足要求。
b) 跨中挠度:ω = q × Ly4(5 − 24 × λ2)/384EI = −0.152 mm,ω/L = 0.152/650 = <1/500,满足要求。
根据表1、表2级表3分别求出的面板、横肋、竖肋的挠度,进行组合挠度验算,具体验算过程如下所示:
面板与横肋组合:ω = 0.46 + 0.005 = 0.465 < 3 mm
面板与竖肋组合:ω = 0.46 + 0.152 = 0.612 < 3 mm
由以上结果可知,组合挠度均未超出规定要求,模板设计满足施工的要求。
3.4. 调配方案
本标段单个墩身一次浇筑4.5 m,单独作业时经模板设计优化及墩身施工要求,最优模板数量为3套2.25 m高模板,仅需1部塔吊配合作业;若进行组合作业时,最优模板数量为4套2.25 m高模板及一部塔吊,可以达到节约成本,提高施工效率及缩短工期的目的。经研究本工程施工人员工艺水平及管理人员专业水平达到组合作业施工水平,因此采用对相邻墩身施工工序作业时间进行把控,一个墩身模板安装及混凝土浇筑作业时,相邻墩身进行钢筋绑扎作业,直至完成全部墩身施工,墩身施工作业平台如图4所示。
综合以上模板要点计算结果及实际施工效果可得本工程所用模板受力结构模型及验算要点均是可行的,本标段按上述计算结果设计的模板是安全有效的,在施工过程中有效的规避了模板质量问题,可以作为本标段模板尺寸受力验算标准。
4. 质量控制要点
4.1. 线形控制
本标段在施工过程中,严格要求墩身的测量和监控工作以确保高墩的施工的质量。在薄壁空心墩身施工前,在顶部、中部、底部均测设导线点及水准点作为测量点和控制点。对于这些测量点和控制点的使用来说,并不仅仅是采用一次测量进行控制,而是应该在整个的混凝土浇筑过程中进行多次复测。尤其是在混凝土浇筑完成一层之后,其测量的价值和必要性更是极为突出。这种复测过程对于后续的模板安装以及施工具备着较为明显的积极作用和价值,必须要引起足够的重视。
4.2. 垂直度控制
对空心墩的平面位置及垂直度进行测量时,分别利用铅锤线及全站仪进行模板垂直度控制。首先利用铅锤线在模板安装时测量模板的四个控制点,用于检测模板是否倾斜,然后利用全站仪在模板安装完成后测量模板四个控制点坐标并与理论坐标进行对比,误差不得超过5 mm。最后在每次浇注混凝土后,对墩身进行四角复测,确保墩身截面尺寸准确、顺畅,达到双控效果,即标高及线型控制,为下次立模提供数据参考,发现模板偏位之后应立即对模板轴线进行调整,调整方法为逐渐垫高模板,采用此方法可以避免线形的不美观,但需要多次调整不能一次性到位。现场垂直度测试如图5所示。
4.3. 高程控制
对墩身高程的控制体现着一个项目专业的管理水平,故对墩身高程要进行严格控制。进行控制时,仅仅采用丈量法或者三角高程中的一种都有无法有效避免误差,故本工艺中采用两种方法共同进行控制,采用100 m钢尺丈量法进行测量,并再次利用全站仪三角高程测量方法进行复核,确保高程误差在允许范围之内,体现出专业的管理水平。
4.4. 环境温差控制
夏季温差对混凝土的影响一直是施工中的不可控因素,对施工质量有着很大的影响,本工程在施工时贯穿夏季的高温时节,根据施工现场温度测量记录及检测时发现墩身混凝土产生不均匀膨胀,可得温差对墩身施工精度产生了很大的影响。为降低温差在施工中造成的不良影响,本工艺在施工中采用以下方法进行温差的控制以最大程度的降低温差的造成的质量干扰:1) 喷水降温:在内外翻模板结构上安装环形喷水洒养管,定时不间断地向墩身喷水,在养护墩身的同时起到降低温差的作用,从而将温差引起的墩身轴线偏位影响减少到最低。养护喷淋管如图6所示。
2) 确定基准温度和基准时间:为消除温差造成的对墩身垂直精度的影响。在夏季施工时选择固定时间(日出前后)测量墩身的高度和平面位置,作为基准参数,以消除温差造成的墩身平面位置偏移和墩身高度的不均匀变化,避免造成后续施工测量定位的困难。具体方法为:每天上午6:30左右,沿墩身横、纵方向两条中心线位置在翻模下口精确安放水平尺,用全站仪进行测量,用此位置的日照偏差,作为待施工墩身部位模板的日照偏差,在模板中线调整中予以消除,以达到克服温差影响的目的。
4.5. 风力、机械振动和施工偏载控制
风力、机械振动和施工偏载对墩身轴线的影响是随机的、无序的。为尽可能的消除以上因素造成的影响,本工艺施工时采用刚度大的模板以提高模板整体的抗弯、抗扭强度;在墩身混凝土浇筑时,严格监控施工过程,确保混凝土从模板四边均衡下料,从而防止混凝土出现偏压,造成模板倾斜。
4.6. 薄壁墩身外观的控制
高墩施工时采用分阶段施工的工艺方法,使得立模、浇注次数较多,这也容易引起墩身外观质量问题。为了提高墩身成型时的外观质量,本标段在墩身施工时进行了有益的探索,并进行总结,形成了本标段的外观控制标准,主要采取了以下措施:
1) 在施工时对配合比进行优化,保障原有配合比、坍落度及强度条件下,利用增加粉煤灰和减水剂的方式,来使混凝土颜色更均匀,和易性更好。
2) 水平施工缝处理:均留下一道水平施工缝,当混凝土终凝前,由人工在内外模外侧,由近及远绕周圈凿除墩身的两个节段间施工缝处的表面浮浆并清扫干净,对接缝处使用玻璃胶和橡胶皮。
3) 混凝土浇筑:浇筑前在两节段模板间和模板下部嵌塞海绵条以防漏浆。浇筑时按每层30 cm、固定的顺序和方向进行分层浇注,并采用插入式振捣棒进行星型振捣。具体振捣要求为每次移动间距不超过振动器作用半径的1.5倍;与侧模保持5~10 cm的距离;插入混凝土深度为5~10 cm;严格遵守快插慢拔要求,避免振动棒碰撞模板、钢筋及其他预埋件。
4) 夏季时在下午或夜晚温度较低时进行混凝土浇注施工,浇注后混凝土面应低于模板面10 cm,以保证混凝土面的连续性。
5) 模板翻升到位后,对模板接缝处采用10 mm的海绵胶皮处理确保接缝严密。
6) 养护方面:墩身在未拆模前,要经常使模板保持湿润,拆模后立即用薄膜进行覆盖,并要求每3~6小时洒水一次,养护时间不少于7天。
7) 拆模后及时修复表面缺陷,保证墩身颜色一致、棱角分明。
5. 总结
中铁北京局静兴高速公路标段在进行高墩施工时采用了翻模法薄壁空心墩技,施工过程优化了模板受力设计、模板验算和施工组织等方法对翻模法薄壁空心墩施工工艺进行了优化与提高,重点解决了模板的受力设计及验算难点,并规范了施工中的质量控制要点。经研究表明上本文采用的模板受力结构设计及模板要点计算结果符合墩身实际施工要求(已进入下一阶段),本工程所用模板受力结构模型及受力验算要点均是可行的,本标段按上述计算结果设计的模板是安全有效的,在施工过程中有效的规避了模板质量问题,可以作为本标段模板尺寸受力验算标准。本标段采用本文提出的翻模薄壁墩施工工艺进行正常施工时,每3~4天完成一节混凝土浇筑(4.5米),施工速度可达到1.3米/天,施工速度提高显著,达到了支架和模板用量少,节约管理成本的目的,且墩身质量控制要点更加明确,提高了施工质量增大了施工的安全性,有效克服了高墩施工难度大的缺点。本本标段施工工艺为翻模薄壁墩工程提供了有效的借鉴方法,对高速公路高墩施工发展有着深远的影响。