1. 引言
铝合金由于其密度低、强度高和导热性好的特点,被广泛应用于航空、汽车、高铁等现代工业 [1]。压铸是指将高温熔融金属以高速、高压充入型腔,然后迅速冷却凝固,在短时间内生产出产品的工艺过程,是一种接近净成形的热加工制造工艺 [2]。压铸模具可以在短时间内大量生产形状复杂的铝合金制品,由于其高生产效率,对于成本竞争激烈的铝合金零部件生产来说是必不可少的 [3] [4]。
长时间工作后,压铸模具会出现各种不同程度的损坏,例如:与高温熔融金属接触,因高速、高压的流体流动而造成的熔化损坏;因反复加热和冷却而产生的热疲劳导致的热裂损坏等。受到熔体损伤的模具需要定期拆卸和维护,这会导致生产效率下降。降低维修频率可有效提高生产效率并降低成本,如何延长压铸模具的寿命并提高产品质量引起了各国研究人员的关注 [5] [6] [7]。
Gavariev R.等 [8],分析了熔化工艺的结晶速率,以及模具成型表面的周期性重复温度和冲击载荷等因素导致的模具缺陷。Shahane S.等 [9],通过机器学习和三维数值模拟的结合,基于有限体积的数值求解器用于确定温度–时间的历史,并将输入与输出相关联以实现低压铸件的多目标优化。Fiorentini F.等 [10],通过确定压铸模具中主要承受高温和高热梯度的区域,并通过增材制造,使用共形通道来设计和分析更有效的冷却系统。Kanyo J.等 [11],通过在模具中引入陶瓷成分以实现更多的化学惰性结构,以减轻与模具的反应,以减少化学诱导的缺陷。Paiva J.等 [12],对两种不同结构的纳米复合AlTiN和AlCrN涂层的磨损性能进行了评价,并得出结果:AlCrN/Si3N4纳米复合涂层具有最佳性能,该涂层具有硬度、附着力、焊接行为、抗氧化性和应力状态的最佳组合。
通过对主要文献的分析可见:部分学者采用了工艺分析、数值模拟、机器学习、冷却系统优化等手段来进行压铸工艺和模具的优化;部分学者通过引入新材料、纳米涂层等方法来强化模具性能。以上方法,由于各种原因目前还较难在工业中实际应用。
本文研究了工业中更容易实施的抛丸、渗氮法在压铸模具表面处理中的应用。在本研究中,制备了经过SB (Shot Blasting抛丸)、N (Nitriding渗氮)组合处理的压铸模具,并进行了压铸实验。研究了模具表面处理对金属融流过程以及制成品的影响。结果表明:模具经过SB-N-SB表面处理后,可有效提高模具的耐用性和制成品的质量。
2. 实验方法
如图1(a)所示,压铸模具是采用4Cr5MoSiV1模具钢制成的,压铸成品为ADC12铝合金材料的L170 × W60 × H3 mm平板状铝件。为评估喷丸(SB)和气体渗氮(N)工艺对压铸模具性能的影响,我们准备了3套模具:1) 未经处理的模具;2) 经过喷丸→渗氮工艺处理,以下简称SB-N模具;3) 经过喷丸→渗氮→喷丸工艺处理,以下简称SB-N-SB模具。使用这3套模具,在合模力70吨的压铸机上,在表1所示的条件下进行压铸实验。
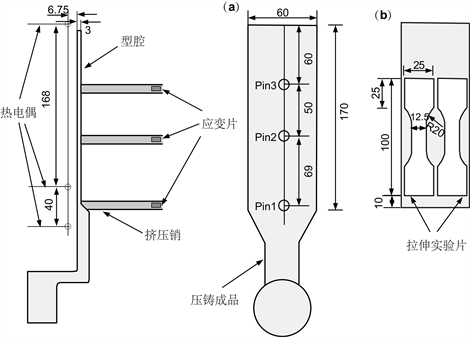
Figure 1. (a) Cavity, extrusion pin and strain gauge of die casting mold; (b) Shape and sampling position of tensile test piece
图1. (a) 压铸模具的型腔、挤压销与应变片;(b) 拉伸试验片的形状和取样位置
如图1(a)所示,在三个挤压销的根部安装应变片,将热电偶插入动模侧至距型腔面6.75 mm的位置。当金属被熔化时,通过应变片感测、捕捉熔融金属的流入过程。另外,实际生产时一般会使用稀释的水溶性脱模剂对模具进行喷涂,以利于脱模。本实验中为了控制变量,每种模具的5次压铸实验,均是在不使用脱模剂的情况下进行的。对于得到的压铸成型品,使用工业X射线CT装置(TOSCANER-32 300μFD)进行断面的组织观察。此外,如图1(b)所示,每个成型产品通过线切割切出两个拉伸试验片,并通过万能材料测试机测量拉伸强度。
3. 结果和讨论
3.1. 应变曲线分析
图2显示了在压铸实验过程中,从3个挤压销底部的应变片得到的应变曲线。在图中箭头所示的液态熔融金属的注入时间点,3套模具对应曲线的畸变都会瞬间增加,说明熔融金属的流入过程均能被捕捉到。另外,在所有模具中,随着注射时间的推移,最靠近浇口的Pin1的应变曲线恢复较慢,而Pin2和Pin3远离浇口,在短时间内即恢复正常。因为Pin2和Pin3离浇口较远,金属熔流至此时速度较为缓慢,注射压力较小。
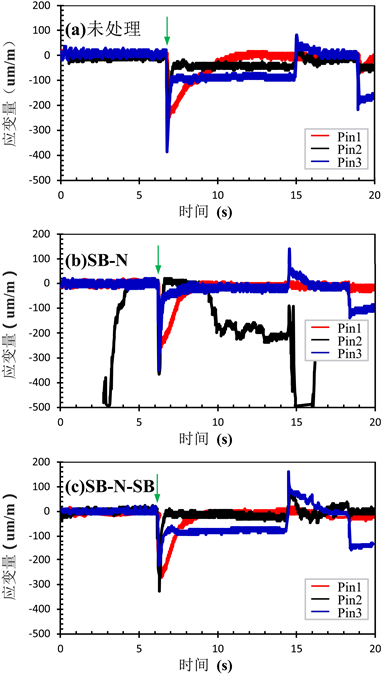
Figure 2. Strain curve of the strain gauge at the bottom of the extrusion pin
图2. 挤压销底部应变片的应变曲线
图3给出了未经处理的模具在注射过程中,Pin1、Pin2、Pin3的应变曲线(为观察清楚,取6.6~7.1 s时间段进行放大操作)。可以看出,离浇口最远的Pin3应变曲线首先发生变化,然后是中间的Pin2,最后是Pin1。其中Pin1曲线发生了失真,因为熔融金属被填充并且注射压力被充分施加,销被挤压变形。在压铸中,液态熔融金属从浇口的远侧填充,因此压力从Pin3开始依次施加。如图3所示,在每个销的位置,峰值变化的时间差值定义为:Pin3和Pin2之间的差值为t1;而Pin2和Pin1之间的差值为t2。对于3种模具,汇总在一起的图如图4所示。未经处理的模具t1和t2都较长,而SB-N模具和SB-N-SB模具依次变短。从该结果发现,与未经处理的模具相比,通过应用复合表面处理,注射过程中熔融金属的流动性得到了有效提高。

Figure 3. Time difference of strain peaks during injection in untreated mold
图3. 未经处理的模具中注射过程中应变峰的时间差
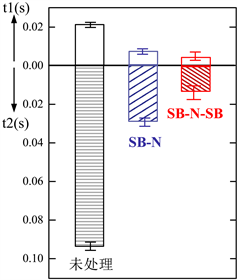
Figure 4. Time difference comparison of strain peaks
图4. 应变峰的时间差比较
图5显示了注射过程中,在每个挤压销位置的最大应变值的比较结果。对于远离浇口的Pin2和Pin3位置,3种模具几乎没有区别,说明压力传播性能较好。但是对于未经处理的模具,在Pin1处应变值明显较小,说明压力传播性能较差。
此外,由于应变峰的宽度可以表示施加压力的时间,如图6所示。可以看出,相较而言,经过复合表面处理的模具压力持续时间更长,尤其是在距离浇口最远的Pin3处更明显。相反,在浇口侧的Pin1处,经过表面处理的模具压力持续时间略短。说明经过表面处理后,保压性能也有所提升。
当填充的铝熔融金属凝固时,不会传递来自柱塞的压力,因此可以推测,由于经过表面处理使得在Pin3处凝固延迟,压力传播和可持续性得到改善。原因是,喷丸使表面变粗糙,模具与熔融金属的接触面积减少,热阻增加,另外渗氮对也对热导率有影响。
模具表面径向的传热系数h,可由公式(1)表示 [13]:
(1)
对于模具材料和铸件材料的固相和液相条件,通过传热方程,可以得到随时间变化的温度分布,如式(2):
(2)
在公式(2)中,如果k与温度无关,可以将该方程的右侧写成式(3)。
(3)
模具经过表面处理后,熔融金属的保温性和流动性得到改善,较高温度的熔融金属充满型腔,凝固时间较长(延迟),改善了压力传播。
3.2. 缺陷与抗拉强度检测
图7为压铸成型品经过X射线CT观察的缺陷分析结果。在各图中,下侧为浇口侧,大的缺陷(铸腔)聚集在上排气口侧。此外,一些缺陷聚集在浇口附近,小缺陷聚集在中间部分。排气口侧出现较大的缺陷,是出现了一定程度的欠铸现象,因为铸件壁较薄,型腔内气压较高且排气不畅。改进措施为提高熔融金属的流动性,改进浇注设计,并改善排气条件。

Figure 7. Defect detection results observed by X-ray CT. (a) Untreated mold; (b) SB-N mold; (c) SB-N-SB mold
图7. X射线CT观察到的缺陷检测结果。(a) 未经处理的模具;(b) SB-N模具;(c)SB-N-SB模具
为进行拉伸试验,对于每种模具的产品,均制备了如图1(b)所示的拉伸试验片。试验结果示于图8。在未经处理的模具产品中,样品的拉伸强度值接近ADC12的标准强度为310 MPa。SB-N模具产品因样品而异,但平均最大强度比未处理模具大。而SB-N-SB模具的产品中,所有样品的拉伸强度都超过了未处理模具的产品,最高提升17%,平均提升约10%,说明产品质量得到明显提升。
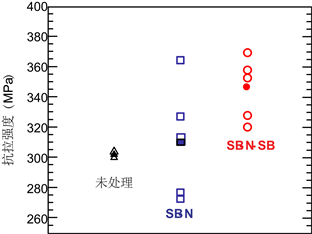
Figure 8. Tensile strength of die-casting test pieces
图8. 压铸试验片的抗拉强度
3.3. 微观结构观察
这些试件在浇口附近的显微组织如图9所示,截面取厚度中心。可以看到,初生α枝晶的尺寸和间距以及它们之间的Al-Si共晶结构的尺寸没有显著差异,微观结构并无明显不同。因此,图8中抗拉强度的差异,主要受图7中缺陷的大小和数量影响。并且在图7中,表示缺陷大小的色条的比例不同,(a)最大,其次是(b)和(c)。在表面处理模具中,图6中的压力持续时间被均衡,并且如图5所示,即使在Pin1中也稳定地施加压力,从而减少了缺陷(压碎)。
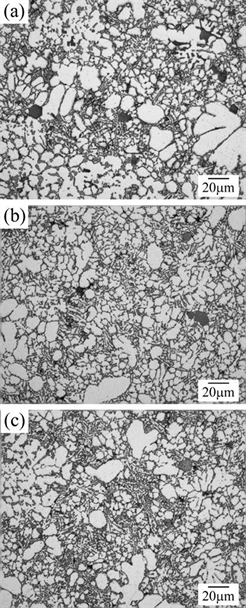
Figure 9. Microstructure of die-cast specimens. (a) Untreated mold; (b) SB-N mold; (c) SB-N-SB mold
图9. 压铸试样的微观结构。(a) 未经处理的模具;(b) SB-N模具;(c) SB-N-SB模具
4. 结论
制备了未经处理的模具、SB-N模具和SB-N-SB模具,并进行了ADC12铝件压铸实验,以评估渗氮和喷丸处理相结合的表面处理方法对压铸过程和制成品的影响。通过分析安装在三个挤压销上的应变计得到的应变曲线,研究了对熔融金属流入和凝固过程的影响。并且,对得到的压铸成型品进行了X射线陷检测、拉伸强度试验和微观结构观察,得到以下结论:
1) 通过在挤压销的底部安装应变片并压铸,可以检测注射时的应变峰值,并检测各销位置处峰值上升的时间差和压力持续时间。
2) 在复合表面处理模具中,观察到应变峰值的时间差较小,可见熔融金属的流动性得到改善。并且排气侧的压力持续时间变长、凝结被延迟,因为复合表面处理后模具的保温性提高,并改善了压力传播特性。
3) 所得ADC12铝压铸成型品的抗拉强度在复合表面处理模具中较高,但微观结构无显著差异。X射线CT观察显示,经复合表面处理的模具,其压铸成型品缺陷尺寸小,数量少,强度有所提高。这主要是由于压力传播的改善,减少了破碎缺陷。
4) 压铸模具经SB-N-SB复合表面处理后效果最好,压铸件抗拉强度平均提高约10%,不仅可以提高模具的耐用性,还能有效提高制成品的质量。
基金项目
浙江省教育厅校企合作“访问工程师”项目(FG2020314);台州市科技局科研项目(2003gy38)。