1. 前言
船体结构用钢(以下简称“船板”),指按船级社建造规范要求生产的用于制造船体结构的钢材。船板主要用于船舶和海上油气钻采平台。因其特殊的使用环境,要求钢材除了具有较高的强度外,还要具有良好的韧性、抗疲劳性、耐海水腐蚀性、抗层状撕裂性、焊接性、冷热加工性。
宝武集团鄂城钢铁有限公司(以下简称“鄂钢”)船板认证体系中涉及的船板级别包括一般强度结构钢B、D、E级和高强度结构钢DH36、EH36级船板。完成认证的船级社有中国(CCS)、德国(GL)、法国(BV)、挪威(DNV)、英国(LR)等多家船级社。船板钢认证是鄂钢产品认证工作开展以来,工作难度最大、技术含量最高、实物准备最繁琐、机械试验最多的产品认证之一。
2. 生产工艺总体设计思路
2.1. 产品的性能要求
船板除要求具有较高强度外,还必须有良好的低温冲击韧性、焊接性能和抗冷弯性。因此,“低碳、高锰、微合金化”的化学成分设计思路是当今许多生产厂家所采用的 [1] [2] [3]。同时,还需要通过优化控轧控冷工艺进一步提高船板的强韧性。
2.2. 成分设计原则
2.2.1. 五大元素控制要求
从船板强度方面考虑,C、Mn是提高强度的主要元素,Mn作为常用的固溶强化元素,大部分固溶于铁素体,可以提高抗拉强度和屈服强度,还可以增大奥氏体过冷能力,具有轻微细化铁素体晶粒的作用;从焊接性能和韧性方面考虑又需要控制较低的碳当量和C含量,同时碳含量的下限值又不能设置太低,以防止钢水在冶炼过程中过氧化,一般设计考虑C含量需大于0.10%。另外,C与Mn高易产生偏析。综合考虑,C、Mn含量应控制在适宜范围。
Si在钢中几乎全部溶于铁素体,可显著提高抗拉强度和屈服强度,但是Si控制过高会降低钢板的焊接性能和延伸率。因此,一般将Si控制在0.30%以下。
S、P是常见的有害元素,钢中的S、P及气体含量直接影响钢的塑性和韧性以及易产生偏析。若S、P含量较高,会影响轧制工艺的制定,不利于控轧的进行,因此应最大限度地降低S、P含量。
2.2.2. N、O、H的控制
对于N的控制比较困难,主要手段为转炉冶炼前期去N、控制使用含N原材料以及避免钢水与空气的直接接触而产生增N。RH炉虽有良好的脱气功能,但脱N能力很有限。
对于O的控制,主要手段为在LF炉精炼炉加入Al丸(线)、铝渣脱氧剂等,完成沉淀、扩散脱氧,其次利用RH的脱气能力进一步去除钢中的O。
对于H的控制,一是要控制原材料水分带入,二是利用RH的脱气能力有效去H。统计表明,鄂钢转炉钢水经RH炉处理后,可将H含量控制在1.5 ppm以下。
2.2.3. 微合金化元素的选择和控制
常见的微合金元素有Nb、Ti、V,均能通过细化晶粒和沉淀强化作用,提高钢的力学性能。从细化铁素体晶粒的效果看,Nb > Ti > V。研究表明,Nb较Ti,V更能显著提高奥氏体的再结晶终止温度,扩大奥氏体未结晶区,通过控轧使铁素体晶粒细化,从而改善钢的综合力学性能。
对于高级别船板,可在钢中添加Ni,主要目的是提高钢的低温冲击韧性和塑性,并能够阻止奥氏体向珠光体或马氏体转变,有利于奥氏体残留。
根据微量元素的作用,最终确定在EH36级船板中添加微合金元素Nb完成细化晶粒作用,添加合金元素Ni,以提高其低温冲击韧性和塑性。
2.2.4. Ca处理
通过对钢水进行Ca处理,并控制钢液中w(Ca)/w(Al) > 0.1,可以使不规则的氧化铝夹杂变为液态球形夹杂12 CaO∙7Al2O3。同时随着Ca的加入,钢水凝固过程能避免生成长条状的MnS夹杂,而生成球状的CaS,改善了钢的各向异性 [4]。
2.3. 成分设计
根据船板入级的规定,采用相似的成分设计、相同的制造方法、相同的交货状态的材料,经船级社同意可选取具有代表性的材料以高代低,因此鄂钢选择EH36作为高强度船板认证的代表性材料。根据船级社规范的要求,并结合国家标准GB 712-2011,确定EH36级船板的熔炼成分见表1,其力学性能要求见表2。
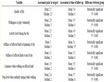
Table 1. Chemical composition of class EH36 hull structural steel
表1. EH36级船板的化学成分
注:要求残余元素Cr ≤ 0.20%、Mo ≤ 0.08%、Cu ≤ 0.30%。要求气体元素N ≤ 0.0050%,O ≤ 0.0030%,H ≤ 0.00018%。
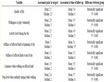
Table 2. Requirements for mechanical properties of hull structural steel
表2. 船板力学性能要求
2.4. 船板生产工艺流程
铁水预处理→130 t转炉→LF钢包炉→RH真空炉(Ca处理)→板坯连铸→加热→轧制→精整
3. 冶炼过程关键工艺及主要措施
3.1. 低P冶炼技术
转炉模拟双联法操作,脱P期供氧强度为0.8~1.2 m3/(mint),高枪位操作保证良好的化渣、抑制碳氧化及控制熔池升温速度,脱P期温度控制在1460℃以内,处理时间约9 min,低温脱P期脱P效率可达85%,脱P结束后快速化渣升温,转炉冶炼周期控制在22 min内。终点P可控制在0.012%以内。
3.2. 低N冶炼技术
N虽然能够与微合金元素Nb形成Nb(C、N)产生强化作用,但过高的N含量对于船板钢是有害的。转炉兑铁冶炼至钢水经精炼到连铸浇铸,钢中的N含量会逐渐增高。要控制钢中N含量,分析了钢中N的来源及N在转炉冶炼中的变化规律,核心是降低钢水终点N含量。通过使用低N废钢、合金,限制出钢温度 ≤ 1630℃,避免终点过氧化及后吹,终点N含量可控制在≤38 ppm,达到了低N冶炼的控制目标。
3.3. 二次精炼工艺
LF采用CaO-SiO2-Al2O3三元渣系,渣中Al2O3含量控制在20%~30%的范围,能够促进化渣,进行快速造渣。另外,富含的Al2O3还原渣有疏松和泡沫特性,反应面积大,可提高渣中的O离子活度。通过加入Al丸、铝渣脱氧剂等完成扩散脱氧。Al2O3富含的还原渣中,铝酸钙熔点低,对钢液的粘附力大,迅速从钢液中浮出;且CaS能很好地润湿铝酸钙,并一起浮出钢液,从而降低钢中夹杂物含量。在造渣过程中遵循“快、白、稳”的原则,并配合合理的吹氩搅拌工艺。在精炼后期,利用其良好的动力学及热力学条件完成钢水的深脱S,精炼结束S含量可降至0.004%以下。
以下是精炼末期炉渣成分及LF出站前钢水自由氧含量,见表3。
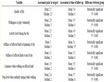
Table 3. Slag composition and oxygen content at the end of LF refining
表3. LF炉精炼末期渣成分及氧含量
对于EH36级船板,LF处理结束后需进行RH炉真空处理,进一步提高其纯净度。目的在于使钢质纵向和横向机械性能均匀,提高其延伸率、断面收缩率和冲击韧性。高强度船板EH36级在真空处理时还需进行微Ti处理,进一步提高其深冲性能。
考虑到生产节奏的控制,RH炉真空周期一般在40 min以内,极限真空度设计为<67 Pa,且极限真空保持时间在10~15 min。为保证处理效果,Al丸及Ti合金加入时机,净循环时间,最佳循环流量的控制是关键。经循环处理后,钢中的[H]可降到1.5 ppm以下,钢中[O]可降至25 ppm以下。统计分析发现,最终H含量近似地与处理时间成直线关系,因此,如果适当延长循环时间,H含量还可以进一步降低。
3.4. Ca处理及夹杂物控制
钢中加入钙量应该控制在生成C12A7和C3A之间的区间,相关研究资料表明,铝镇静钢进行钙处理,要求[Ca]/[Al]为0.09~0.14,是达到对夹杂物充分改质变性的基本条件。船板钢中[Al]控制在0.025%左右,为达到[Ca]/[Al]为0.09~0.14,需将钢种[Ca]控制在0.002%~0.004%之间,喂入钙线后保证软吹时间 ≥ 12 min,促进夹杂物进一步上浮。
3.5. 连铸参数配置
钢水采用二次精炼工艺,钢水纯净度可以得到保证,船板钢连铸工艺关注重点为铸坯表面质量,为有效控制纵裂发生,开浇炉拉速比较重要,据有关资料介绍:高的浇注速度将促进裂纹形成。统计数据表明,其主要原因是拉速升高以后保护渣的消耗量减少,导致坯壳润滑不良,造成铸坯表面纵向裂纹。对于船板钢生产,为弥补开浇炉保护渣熔化速度慢而导致消耗量不足的问题,实行了开浇炉降速操作(即开浇炉拉速低于典型拉速),提高保护渣消耗量。经过降速操作,连铸板坯表面纵裂发生率维持在较低值。
为控制铸坯边部裂纹,主要采取以下措施:
1) 合理分配二冷水分布,在铸坯矫直前对板坯角部实行弱冷,可以减少铸坯的角裂的发生。
2) 在板坯连铸机浇钢过程中,二冷配水变化的迟缓效应导致降拉速时铸坯强冷,铸坯产生角裂的几率增加。
3) 优化铸坯断面设计,控制轧制宽展比可减少板坯角部裂纹向钢板宽面扩展。
中包覆盖剂选用含MgO的碱性覆盖剂。EH36级船板选择中碳钢保护渣。中间包内留钢8~10 t停浇来控制中间包下渣。
3.6. 控轧控冷
在加热炉中均热温度控制在1200℃~1240℃,加热时间3~4.5 h。粗轧采用高温大压下量轧制,板坯轧制至最终成品厚度的2.5~4倍,开轧温度控制在1050℃~1100℃范围,累计压下率 > 60%。精轧开轧温度 ≤ 900℃,累计压下率 > 40%,终冷温度控制在650℃~780℃。经控冷后,可获得均匀的细晶粒组织,保证优良的力学性能 [5]。
4. 实践应用效果
4.1. 钢水纯净度
通过中包取样,做N、O、H、P、S成分全分析,EH36级船板控制情况见表4。
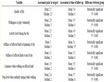
Table 4. Total analysis of N, O, H, P and S components
表4. N、O、H、P、S成分全分析
4.2. 力学性能
对成品取样分析后,EH36级船板强度和延伸率见表5,其纵向冲击功见表6。
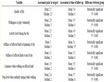
Table 5. Mechanical properties of high-strength hull structural steel
表5. 高强度船板力学性能
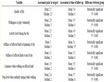
Table 6. Longitudinal impact test of high-strength hull structural steel head (thickness 50 mm)
表6. 高强度船板头部纵向冲击试验(厚度50 mm)
4.3. 无损探伤及落锤试验
经无损探伤检验,轧材探伤合格率100%,钢质纯净度控制得比较好。
落锤试验是船板认证试验项目中的一项重要内容,要求测出船板的无塑性转变温度,即NDT温度,它是船板的主要韧性指标之一,同时也是其诸多性能指标中较难满足的一项。经检验,高强度船板EH36级落锤试验中NDT温度−55℃,落锤试验检测合格。
5. 结论
1) 鄂钢船板认证工艺经产品性能检测完全满足船板认证要求,生产工艺实践可用于实际船板生产。
2) 合理的成分设计及冶炼过程钢水纯净度的控制是关键,将钢中P、S、O、N、H总量控制在较低水平,不仅是钢质纯净度的保证,也可有效控制铸坯偏析带的形成。并通过合适的Ca处理工艺可有效控制脱氧夹杂物的形态,提高产品质量。
3) 合理的连铸工艺是钢坯表面质量的保证。通过开浇炉限制拉速及合理的二冷工艺,铸坯纵裂发生率及边裂发生率均控制在较低水平。