摘要:
为实现镀锌线工艺全流程的数据监控,确定最佳控制参数,改善带钢表面质量,某镀锌线引进IBA公司的QDR系统进行全流程的数据采集,QDR系统同现场传感器设备,L1和L2系统搭建网络架构,建立通讯连接,依赖其数据采集板卡,模拟量和数字量信号选择及处理等技术,实现大量数据的接收、存储、解析以及显示,数据采集具备实时性好、准确率高、抗干扰能力强及参数灵活配置等特点,在工业现场取得了较好的应用效果,为镀锌线优化控制参数,提升产品质量提供了数据支撑。
Abstract:
In order to realize the data
monitoring of the whole process of the galvanizing line, determine the best
control parameters and improve the surface quality of the strip steel, a
galvanizing line introduces the QDR system of IBA company for the whole process
of data acquisition. The QDR system establishes a network architecture and
communication connection with the on-site sensor equipment, L1 and L2 systems,
and relies on QDR data acquisition board, analog and digital signal selection
and processing technology. It realizes the reception, storage, analysis and
display of a large amount of data. The data acquisition has the characteristics
of high real-time, high accuracy, strong anti-interference ability and flexible
parameter configuration. It has achieved good application results in the
industrial field, and provides data support for optimizing the control
parameters of the galvanizing line and improving the product quality.
1. 引言
冷轧镀锌线工艺流程复杂,对质量影响因素较多,任何一个工艺环节参数的波动都会对镀锌质量产生较大影响,而通过对生产参数采集,根据各项参数的波动变化,对带钢表面质量进行再调整和再优化,并确定最佳工艺参数,从而改善带钢质量有着非常重要的意义 [1]。目前工业网常用的数据采集方法有OPC数据采集,DCS式数据采集等,性能好,速率快,可靠性高的新型采集板卡也在不断出现 [2],为工业自动化和网络化提供了最佳的解决方案。
国内某钢厂“以工艺参数采集为中心,以过程质量控制为导向”作为出发点和落脚点,力求提高对关键工艺参数和过程质量控制的管理水平。该厂某镀锌线以引进IBA公司的过程质量数据采集系统(Quality Data Recording,以下简称QDR)为基础,同主产线基础自动化系统(Basic Automation System,以下简称L1)和过程控制化系统(Process Control System,以下简称L2)分别建立通讯连接,进行数据采集,匹配和分析。QDR用于高速采集,在线显示和分析来自SIMATIC自动化系统、传动系统的模拟信号和数字信号,依据QDR最快1 ms的总线采集技术,保证现场数据采集的时效性和精准性,将影响生产质量的工艺数据信息以曲线和报表的形式展现给技术人员和操作人员,保证了用户基于数据提高成品质量,提高了企业智能化水平。
2. 系统架构
按照工艺流程,该镀锌线从入口开卷,清洗、退火、镀锌、光整、拉矫、钝化、涂油,出口卷曲,包括锌层测厚仪,油膜测厚仪,切边剪,测宽仪,测厚仪等单体设备,每段工艺流程都有重要和关键参数,如生产速度、各段张力、锌层厚度、炉区温度、炉区露点、锌锅温度、光整拉矫延伸率、活套套量、切边量等,这些参数直接影响最终产品质量,同时也反映了设备的使用及维护情况,对设备本身也是一个良好的监控 [3],经统计,上述关键性参数共计127项,这些参数均要进行数据采集。
现场硬件方面,首先要配置关键设备的传感器,这些参数经现场传感器如接近开关,光栅,高温计,编码器等就近连接到ET200S的数字量输入模块,此时完成了传感器到ET200S的连接 [4]。通过ET200S的通讯功能模块就近将各个ET200S或具有PROFINET接口的设备串联起来,再连接到OBT,再通过光纤传输到OBT,再连接到PLC。通过PLC上CPU集成的PROFINET网,将各PLC连接起来,完成现场数据到PLC的采集 [5]。完成数据的第一步采集工作,系统架构图如图1所示。
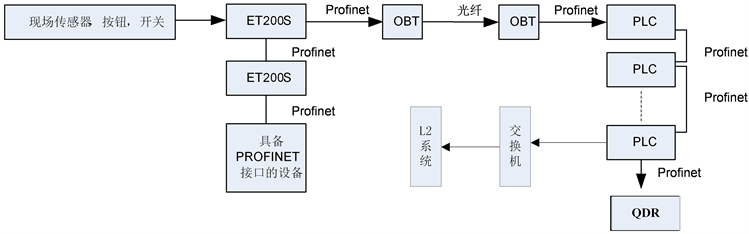
Figure 1. Overall architecture of data acquisition
图1. 数据采集整体架构图
L1系统中的PLC模块采用SIMATIC S7-1500,该模块具有新型的背板总线技术,采用高波特率和高效传输协议,信号处理速度更快,系统响应时间更短,且可扩展性强,采用“顺序扫描、不断循环”的工作方式,为数据采集提供了极大的时效性和准确性 [6]。按照工艺流程和功能需求,该镀锌线PLC共配置了6个CPU模块,配置情况如表1所示,不同区域的测量值分别接入各自区域的CPU内,QDR采集板实时读取SIMATIC S7-1500中各种变量。
该镀锌线QDR共配置四个数据采集单元(ibaBM-PN)板卡,这些采集板卡分别与上述入口段,工艺段,出口段和物料跟踪的CPU通讯,为满足实际生产节奏,采用10 ms的采样频率,定义128个数字量和112个模拟量 [7],SIMATIC用户程序循环记录测量值并将它们写入PROFINET接口卡。通过程序在一个周期内将数据通过PROFINET传输到QDR接口板,即可建立PLC至QDR的数据采集 [8]。数据连接网络图如图2所示。
3. QDR系统配置
3.1. 建立通讯连接
在QDR系统,首先进行硬件配置,监测已经连接的硬件,通过TCP/IP协议建立与PLC的连接,配置S7的IP地址,选择上述四个S7机架上要采集信号的CPU,依次添加S7对象,建立通讯连接。该系统可诊断所有的连接,配置完成后,可查看所有已经建立连接的详细信息。依次将上述四个数据采集单元与对应CPU建立连接后,可以进行下一步工作。
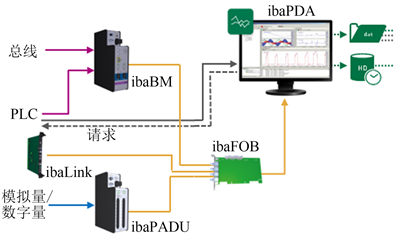
Figure 2. QDR internal data acquisition connection diagram
图2. QDR内部数据采集连接图
3.2. I/O配置
QDR系统可以接受模拟量信号和数字量信号,网络连接建立完成后,需根据采集信号在CPU中的地址进行信号选择 [9]。一般情况下,来自不同数据源的信号,选择分在不同的区域,结合成易于识别的分组,本镀锌线共建立4个信号分组,为EN,PR,MTR和EX,分别为入口段,工艺段,物料跟踪和出口段的工艺信号,如炉区温度,锌锅温度,锌层厚度,气刀压力等信号在工艺段信号分组,带钢宽度,带钢厚度,涂油量,油膜厚度等信号放在出口段工艺分组,将127个参数项分别配置在上述四个分组。该种信号配置方式灵活简单,后期可根据实际需求不断增加新的信号。
4. L2系统数据采集
L1与L2系统之间的数据通讯,是数据采集与显示功能实现的必要条件之一,二者以报文的形式进行通讯,每条报文包含报文头,报文体。其中报文号是唯一的,根据报文号匹配相应的报文内容,常用于查询解决通讯异常,数据错误等问题。
该镀锌线中,上述采集的127项数据采用报文的形式发送,为每2 s触发一次。发送方为L1系统DB块,L1系统将所有测量值地址统一写入DB块,该DB块与L2系统建立通讯连接,报文号设置为5190,报文内容为钢卷ID号和上述关键性工艺参数,其钢卷ID由L1系统在钢卷上线时生成,具有唯一性。焊缝跟踪由CPU里MTR的模块负责完成,该模块是实现在线测量值匹配至钢卷的关键环节,直接确定了每个时间点,每个测量值匹配的准确性 [10]。
考虑到程序编写的模块化和标准化,L2系统编写了不同功能的程序进程,其中测量值收集功能由MVA进程实现,该进程主要负责数据通讯与数据处理。为统计测量数据的整体分布趋势和偏离程度,每项工艺数据均计算出最大值,最小值,平均值和方差。MVA进程在收到测量值报文后,会实时与上一时刻的最大值,最小值进行比较,计算更新每项工艺数据的上述四项值。L2系统采用ORACLE数据库,数据库建立PCOIL_QUAILTY数据表,将上述工艺数据存储至该表,并实时更新。
当钢卷剪切完成后,L1系统将剪切信号发送至L2系统,L2系统生成成品卷卷号,将全线采集的数据匹配至成品卷上。
5. 数据显示
5.1. QDR系统数据显示
QDR系统数据保存形式为.dat,由于信号点多,采集频率高,该产线专门配置了数据存储服务器,能够满足产线大量数据的存储。QDR由按时间采集的数据形式转化为按带钢长度方向显示,为1 m一个点进行显示,提供了采集数据在整个带钢方向上的变化趋势,技术人员可按照卷号查询相关工艺值,针对不同工况,分析和优化相关数据。图3展示了沿带钢长度方向,0~500米范围内炉区速度和炉区各段温度的变化趋势,带钢速度在79.80~80.00 m/min之间波动,较为稳定,但预热段和直燃段温度波动较大,最大值达到15℃,炉区加热温度波动大可能会造成带钢的瓢曲,此时可进一步查看可能引起温度波动大的因素的QDR曲线,如烧嘴功率变化,煤气流量变化等进一步分析原因。
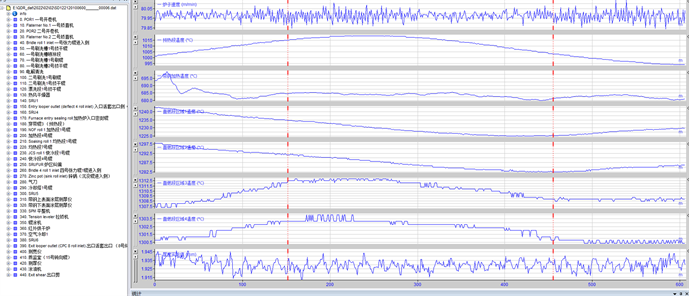
Figure 3. Display curve of QDR system data
图3. QDR系统数据显示曲线
5.2. L2系统数据显示
L2系统采集的数据最终通过报表的形式进行显示,该报表以成品卷卷号作为ID,显示了127项工艺项的最大值,最小值,平均值和方差,技术员可以查看生产过程中的各项参数,该种方式反映了每个工艺数据在生产过程中的波动程度和偏离程度,对于提高数据稳定性,稳定带钢质量有着重要的研究意义 [11]。图4为报表格式及部分内容。

Figure 4. Display of acquisition data report
图4. 采集数据报表显示
6. 结论
本文以IBA公司的QDR数据采集技术为基础,从系统架构及配置,数据处理,数据显示三个方面进行了设计,按照工艺流程,分别将产线关键工艺数据经相关传感器进行采集,通过以太网通讯传输给PLC,QDR系统对模拟量和数字量进行信号选择和信号采集配置 [12],网络通讯高效稳定,信号配置灵活方便,以每米一个点进行数据的曲线显示,L1通过报文通讯将数据实时发送给L2系统,L2通过MVA进程分别计算各个工艺项的最大值,最小值,平均值和方差,最终以报表的形式显示。该系统实现了镀锌产线关键工艺数据的实时采集和显示,满足了对过程质量的监控,为进一步优化控制参数,提高产品质量提供了数据支撑,同时,提高了钢铁企业的过程控制自动化水平,实现了生产的全流程数据共享 [13]。