1. 引言
滚动轴承长期在高速、重载及恶劣环境下工作,其性能会随着磨损而发生退化,但轴承仍然可以继续工作。因为轴承的早期磨损一般难以察觉,往往发现时,轴承已发生严重磨损或失效,所以针对轴承早期故障的监测,有利于及时发现异常,并采取相应措施来消除异常,避免造成更大的损失 [1]。
近年来,利用振动特征信号对滚动轴承状态监测是防止机械故障最常用的方法,振动是滚动轴承应用最为广泛的性能指标。由于套圈、滚动体与保持架之间存在的多种间隙,使得组成是轴承正常运转的前提条件,使得轴承运行过程中不可避免发生振动。主要采用了时域、频域和时频域等技术,但轴承振动信号复杂、不平稳、噪声大,很难监测出轴承的故障。故需要引入一种新型的基于静电感应原理的航空器性能状态在线监测技术,此项技术最早在1970年左右由美国空军技术研究所发起,用于对航空发动机气路监测 [2] [3] [4]。Harvey等 [5] 同时使用磨损区域静电传感器和润滑油路静电传感器对滚子轴承进行加速磨损实验,同时对轴承内圈预置故障,研究表明磨损区域静电传感器准确得到了故障位置而润滑油路静电传感器也在油路中检测到带电磨粒,证明静电感应适用于轴承的磨损区域的状态在线监测。国内针对航空发动机尾气静电监测,左洪福团队在静电监测技术方面进行了一系列研究。文振华等人 [6] [7] 根据发动机气路特点,设计出气路系统的静电传感器。张营等人 [8] 提出了一种基于谱插值的去噪方法。刘若晨等人 [9] [10] [11] 对滚动轴承和齿轮箱进行静电在线监测试验,结果表明静电在线监测技术能够监测滚动轴承和齿轮箱的性能退化状况。
基于静电理论分析 [12],本文提出针对监测对象的特点和磨损区域的位置,来研究滚动轴承的故障诊断,利用本文方法可以验证选取合适的静电传感器监测滚动轴承部件的状态,判断出滚动轴承发生故障以及故障程度的可运用性。
2. 静电监测原理
摩擦主要研究是有接触、有相对运动的两个物体间的相互作用、变化的一门学科。滚动轴承运行时,产生摩擦,引起摩擦起电、表面荷电以及磨粒荷电等因素,会使滚动轴承在磨损的过程中产生大量的静电信号。静电监测基于静电感应原理,产生的静电与探极感应面接触时,将会产生相反电位的电量,并将电子重新分配,从而使传感器探极内增加的电量得到平衡,通过信号调节产生相应可测量的输出信号,如图1所示。

Figure 1. Electrostatic schematic diagram of wear area
图1. 磨损区域静电原理图
3. 滚动轴承静电监测实验平台
3.1. 静电监测实验平台
以滚动轴承为研究对象,搭建滚动轴承静电监测实验平台,如图2所示。实验平台主要由3相异步电机、联轴器、传动轴、夹具、磨损区域静电传感器、滚动轴承、轴承座、磁粉制动器、传动带等组成。
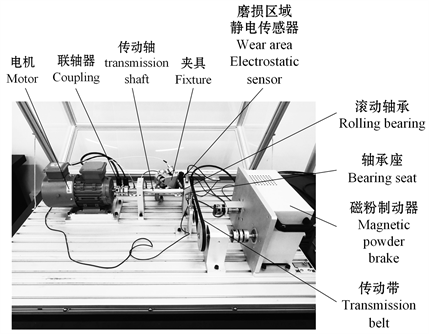
Figure 2. Rolling bearing monitoring experiment platform
图2. 滚动轴承监测实验平台
通过上述搭建的滚动轴承监测实验平台,对滚动轴承进行静电监测,然后对静电传感器监测到的静电信号进行信号分析。静电监测实验步骤如下:滚动故障轴承通过电机转动发生磨损,产生静电信号,通过磨损区域静电传感器对静电信号进行采集。然后将静电传感器采集的静电信号传输到信号放大器中,对信号进行放大,随后由数据采集卡进行A/D转换,数字化静电信号。最后,在静电监测系统的中生成滚动轴承故障波形图,监测步骤如图3所示。

Figure 3. Electrostatic monitoring process of rolling bearing
图3. 滚动轴承静电监测流程
3.2. 磨损区域静电传感器
磨损区域静电监测技术是通过将静电传感器固定在部件的磨损区域处,获取监测部件摩擦区域的带电信息,由带电信息发现部件的磨损状况。磨损区域静电传感器如图4所示。

Figure 4. Electrostatic sensor in wear area
图4. 磨损区域静电传感器
其中探极感应面用于感应磨损区域电荷的变化,通常由紫铜制成;绝缘层材料通常采用聚四氟乙烯,其作用是保证感应电量的可靠性,避免感应电荷的外泄;屏蔽层主要由金属制成,通过将屏蔽层接地,能够有效屏蔽外界的信号;图中螺母和螺纹的作用主要是将传感器与所测对象安装在一起并固定;后端盖内含有信号调理电路,与探极和信号输出端相连;信号输出端用于输出信号调理电路处理过的静电信号。
3.3. 滚动轴承试验件
通过在滚动轴承上预置某种典型故障,进行故障模拟,如滚子、内圈、外圈,研究不同转速、负载和不同故障、故障程度条件下的故障轴承静电信号。实验所用滚动轴承均为深沟球轴承6204-2Z,主要有不同故障轴承和不同故障程度的轴承,分别是正常轴承,轻度、中度、重度故障的滚子轴承、内圈轴承及外圈轴承,如图5所示。其中轻度代表缺口宽度为1 mm,中度代表缺口宽度1.5 mm,重度代表缺口宽度为2.5 mm。
4. 实验结果分析
4.1. 不同故障程度监测信号分析
静电传感器采集到的静电信号,信号数据量仍偏大,为了使监测部件的故障参数更好地被发现,对故障参数进行特征参数提取。本文采用时域参数方法进行特征提取,常用的特征参数指标包括均方根值、峰值指标、峰峰值等。通过提取静电信号的峰值指标,来比较故障程度不同时,磨损区域静电传感器对正常轴承和不同故障轴承监测能力的区别。峰值指标
反映峰值在波形中的极端程度,表达式如下:
(1)
式中:
为静电信号的均方根值,
为静电信号的最大值的绝对值。
对不同故障程度轴承静电信号峰值指标参数特征提取后,为比较各种故障程度的故障轴承峰值指标变化,由峰值指标生成箱型图,如图6所示。箱型图中上界线和下界线分别代表峰值指标的最大值和最小值,黑色破折线为峰值指标的中位值,白色空心矩形为峰值指标的平均值,黑色实心菱形为峰值指标异常点,相对于样本整体异常值较少,可忽略。从图6(a)观察可得,正常轴承的峰值指标在0附近,同时观察图6(b)、图6(c),可见正常轴承的峰值指标参数始终在0附近。图6(a)中轻度滚子故障轴承的峰值指标范围在2.10~2.87之间,中值为2.46,平均值为2.48;中度滚子故障轴承的峰值指标范围在2.13~3.28之间,中值为2.63,平均值为2.66;重度滚子故障轴承的峰值指标范围在2.54~4.72之间,中值为3.37,平均值为3.42。通过观察整体中值和平均值变化趋势,可知峰值指标随着轴承故障程度的增大而增大。
(a)
(b)
(c)
Figure 6. Monitoring of bearings with different fault degrees by the same sensor. (a) Roller fault bearing; (b) Inner ring fault bearing; (c) Outer ring fault bearing
图6. 同一传感器对不同故障程度轴承的监测。(a) 滚子故障轴承;(b) 内圈故障轴承;(c) 外圈故障轴承
4.2. 不同尺寸探极监测信号分析
为了验证探极尺寸不同时静电传感器的监测能力的区别,选用探极直径6 mm、8 mm、10 mm、12 mm、14 mm的磨损区域静电传感器,分别对同一故障程度的轴承进行监测。5种探极尺寸传感器如图7所示。
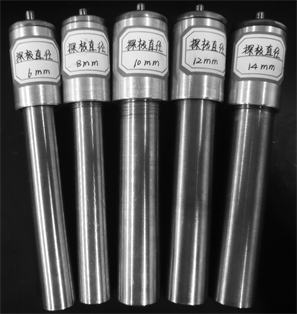
Figure 7. Five sensors with different probe sizes
图7. 5种探极尺寸不同的传感器
为了能够更加直观地观察不同静电传感器监测能力的区别,对原始信号进行去噪,然后对去噪过的信号提取峰峰值参数。研究不同探极尺寸的静电传感器对轻、中、重三种不同故障程度的不同故障轴承的监测能力区别。峰峰值
含义是监测信号一个周期内信号的极差,表示信号范围越大,传感器的灵敏度越好。通过比较不同探极直径尺寸的静电传感器的监测范围,可以得出探极尺寸不同时传感器监测效果的差异,表达式如下:
(2)
式中:
为静电信号的最大值,
为静电信号的最小值。
图8,图9,图10分别为轻度、中度、重度的滚子、内圈、外圈故障在不同静电传感器监测下的静电信号峰峰值的箱型图,图中的上下界限线为峰峰值的最大值和最小值,虚线为峰峰值的中位值,白色方形为峰峰值的平均值,黑色菱形为异常的峰峰值,可忽略。图8为轻度的滚子、内圈、外圈故障在不同传感器监测下的静电信号峰峰值,图8(a)中观察可得,探极直径为6 mm的静电传感器监测信号的峰峰值范围在0.15~0.20 mV之间,中值为0.172 mV,平均值为0.174 mV;探极直径为8 mm的传感器监测信号的峰峰值范围在0.17~0.22 mV之间,中值为0.182 mV,平均值为0.188 mV;探极直径为10 mm的传感器监测信号的峰峰值范围在0.16~0.23 mV,中值为0.190 mV,平均值为0.195 mV;探极直径为12 mm的传感器监测信号的峰峰值范围为0.16~0.24 mV,中值为0.192 mV,平均值为0.197 mV;探极直径为14 mm的传感器监测信号的峰峰值范围在0.16~0.24 mV之间,中值为0.197 mV,平均值为0.199 mV。通过比较,可得出静电传感器探极直径增大时,监测信号峰峰值的中值和平均值也在增大,图8(b)和图8(c)中也得出此规律。
而图9,图10分别为中度、重度的滚子、内圈、外圈故障在不同传感器监测下的静电信号峰峰值。发现图9和图10也满足以上规律,因此,可以得出轻度、中度、重度的滚子故障、内圈故障和外圈故障,在不同探极直径的磨损区域静电传感器的监测下,当探极直径越大,峰峰值的中值和平均值都在不断增大,即探极直径越大,静电传感器的灵敏度越高,其监测效果也越好。
(a)
(b)
(c)
Figure 8. Monitoring of slightly faulty bearings by sensors of different probe sizes. (a) Roller fault bearing; (b) Inner ring fault bearing; (c) Outer ring fault bearing
图8. 不同探极尺寸传感器对轻度故障轴承的监测。(a) 滚子故障轴承;(b) 内圈故障轴承;(c) 外圈故障轴承
(a)
(b)
(c)
Figure 9. Different probe size sensors monitor moderately faulty bearings. (a) Roller failure bearing; (b) Inner ring faulty bearing; (c) Outer ring faulty bearing
图9. 不同探极尺寸传感器对中度故障轴承的监测。(a) 滚子故障轴承;(b) 内圈故障轴承;(c) 外圈故障轴承
(a)
(b)
(c)
Figure 10. Monitoring of severely faulty bearings with sensors of different probe sizes. (a) Roller failure bearing; (b) Inner ring faulty bearing; (c) Outer ring faulty bearing
图10. 不同探极尺寸传感器对重度故障轴承的监测。(a) 滚子故障轴承;(b) 内圈故障轴承;(c) 外圈故障轴承
综上,不同故障程度的不同故障的滚动轴承,在不同探极直径尺寸的静电传感器的监测下,随着静电传感器的探极直径增大,提取降噪后的静电信号的峰峰值的中值和平均值也在不断增大。表明探极直径尺寸越大,静电传感器灵敏度越高,其监测效果越好。
4.3. 传感器有效视场分析
为了验证各个磨损区域静电传感器的有效视场,分别将5种探极直径不同的静电传感器,通过夹具分别由最靠近轴承的位置慢慢远离轴承,直到静电传感器无法感应到轴承产生的静电信号为止,此时探极感应面与轴承之间的距离即为磨损区域静电场传感器的有效视场。反复进行此实验,取多组实验结果的平均值作为各个传感器的有效视场,传感器有效视场,如图11所示。从图中可知,静电传感器的探极直径越大,对应的有效视场也越大。故在对故障轴承进行监测时,选用探极直径越大的传感器监测效果会越好。但是静电传感器探极直径越大,采集到的静电信号所受到的背景噪声干扰越多,这会导致静电传感器监测到的静电信号失真。因此通过增大传感器探极直径的方法来增大静电传感器有效视场的同时,需要综合考虑监测的对象和监测所处的环境。
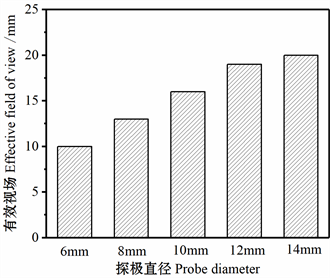
Figure 11. The effective field of view of different sensors to monitor the faulty bearing
图11. 不同传感器监测故障轴承的有效视场
综上所述,静电传感器的监测效果与故障轴承的故障程度和探极直径的大小都有关。滚动轴承故障程度越大,静电传感器监测效果越明显,而静电传感器探极直径越大,静电传感器的监测效果也越明显,且有效视场会随着静电传感器探极直径的增大而增大,即监测的有效区域增大。一定程度上验证了磨损区域静电传感器的监测性能对滚动轴承故障监测的可行性。
5. 结论
本文研究了基于静电感应原理的滚动轴承故障监测性能分析。通过搭建滚动轴承静电监测平台进行实验,由实验可知:同一探极尺寸的传感器,监测不同故障程度的滚动轴承,得出滚动轴承故障程度越大,传感器监测效果越好;选用不同探极直径尺寸的静电传感器,监测相同故障程度的滚动轴承,得出静电传感器探极直径越大,静电传感器的灵敏度越大;静电传感器探极直径尺寸不同时验证静电传感器的有效视场,得出静电传感器探极直径尺寸越大,静电传感器的有效视场也越大。综上可知静电传感器监测滚动轴承状况,能够判断出滚动轴承发生故障以及故障的程度。
基金项目
国家自然科学基金(51705221)、常州市科技支撑项目(CE20175027)、江苏理工学院研究生科研与实践创新计划项目(XSJCX20_44)、“江苏省政府留学奖学金”项目资助。