1. 引言
随着国内经济实力的提升和科学技术的发展,谐波减速器已在空间机构、工业机器人、精密医疗器械等各类高精设备中得到广泛应用,但其核心部件柔轮在椭圆波发生器和轴承的作用下发生周期性弹性变形,从而使柔轮齿和刚轮齿进行相互啮合,实现传动,很容易发生疲劳断裂,因此对如何使谐波减速器在空间中使用寿命更高,更精密、重量更轻,有着十分迫切的需求。
目前,因理论计算和实验求解困难,国内外对于柔轮结构应力的研究主要通过仿真进行求解,Li等 [1] 提出了新的数学模型和数值方法,开发了进行加载齿接触分析(LTCA)的程序,实现了对接触力的分析。Pacana等 [2] 通过理论计算和仿真分析,对柔轮的应力进行了分析,并进行了实验验证,得出了转动角与应力的关系。谐波减速器中柔轮的主要失效形式为疲劳断裂,占总失效比例约60%,其中在齿圈和筒底处的等效应力最大,最容易发生失效。为了提高谐波减速器的啮合性能,减少应力集中等传动问题,国内外学者对柔轮的结构进行了很多的研究改进。Wang等 [3] 在力学分析和有限元分析的基础上,研究了短柔样条的应力计算方法。分析了不同设计参数下的应力,为设计提供了参考。Yang等 [4] 利用偏轴向载荷指标研究了齿轮齿面载荷分布不均匀性的影响。分析了不同因素对局部轴向载荷的影响。高海波 [5] 使用APDL语言建立等效接触模型,优化了结构参数,但只分析了静力学问题,没有分析负载情况下的变化规律,且没有考虑筒体和齿之间的厚度变化过程。张渝爽等 [6] 对柔轮结构加入切入圆弧,对所设计的新结构进行有限元分析,证明新结构能够改善应力集中,但改变应为角度,影响了结果的准确性。邢静忠等 [7] 计算了不同工况下柔轮的应力规律,并对比筒形和礼帽形柔轮不同参数对于应力的影响,董慧敏等 [8] 运建立APDL参数化接触模型,用正交试验法和零阶方法优化得出最终的最优参数。
本文首先建立双圆弧齿廓,基于所设计的齿廓建立精确的柔轮三维模型,进行装配,建立不同筒长、齿宽、倒角、壁厚、圆角装配体模型,分析这些单因素对于柔轮应力的影响,筛选出影响最大的三个结构参数,选用标准二阶响应面为响应面类型,选用BBD为DOE实验样本采集方法,对所生成的不同样本组合进行高效快速的分析求解,最终求解的参数既能减少柔轮的最大等效应力,又能实现空间中小型轻量化的要求,为空间中使用的谐波减速器设计和相关研究提供参考。
2. 柔轮双圆弧齿廓的建立
柔轮双圆弧齿廓是由两个偏心圆的一部分和与这两个偏心圆的切线组成,齿廓的结构图如图1所示,AB段为凸圆弧部分,CD段为凹圆弧部分,BC段为两圆弧的切线部分,对于柔轮各部分建立参数方程如下:
AB段的参数方程
(1)
BC段切线段的参数方程
(2)
CD段的参数方程
(3)
由上面提到的与两圆弧相切,所以关系可以列出如下公式:
(4)
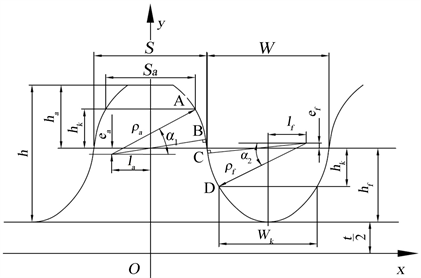
Figure 1. Double-arc tooth profile of flexspline
图1. 柔轮双圆弧齿廓
式中
、
分别为凸、凹齿圆心偏移量,
、
分别为凸、凹齿圆心移距量,
、
分别为凸、凹齿圆弧半径,S为凸齿节线轮齿厚,W为凹齿节线齿槽宽,
为齿根高,k为公切线的斜率,b为截距,t为齿根到横坐标的距离,具体参数大小根据经验公式得出。
3. 柔轮几何和仿真模型的建立
3.1. 柔轮的几何模型
本文采用传统的杯型柔轮,并通过调研国内外先进谐波减速器公司发现,具有高效传动性能的谐波减速器的齿圈前沿可以使用齿圈前后一定角度的倒角代替,此种方法可以减少应力集中问题。柔轮齿数为200,根据谐波减速器的运动的规律,则刚轮齿数为202,取模数m为0.3。在建模的过程中,为了能够体现柔轮真实的仿真结果,减小误差,不对柔轮轮齿进行简化,但波发生器含有轴承,包含的接触过多,所以简化为外圈为椭圆,内圈为圆的圆环。简化后的波发生器的长轴比柔轮内径长,能够实现过盈配合,结构图如图2所示。
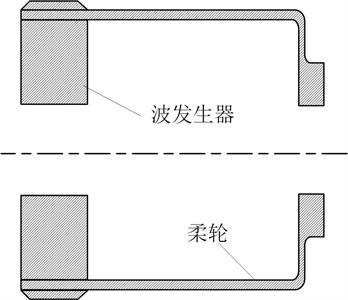
Figure 2. Structural diagram of flexspline
图2. 柔轮结构示意图
3.2. 柔轮的有限元模型
将在solidworks中建立的模型导入到Ansys Workbench中,对于装配体各部件材料的设置如表1所示,定义波发生器为刚性体,和柔轮进行刚柔耦合,定义柔轮和波发生器为摩擦接触,摩擦系数设置为0.15,接触刚度为0.1,将波发生器的外表面设定为目标面,柔轮内表面设定为接触面。对各部件材料进行赋予,统一设置网格大小为1.5 mm,约束柔轮筒底自由度,因波发生器与柔轮为过盈配合,为了减少非线性条件的影响,需要打开大变形开关,进行仿真分析。
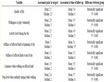
Table 1. Finite element model material setting
表1. 有限元模型材料设置
根据以上参数对柔轮的最大等效应力应变进行仿真求解,求解结果如图3、图4所示,由图可知,柔轮的最大变形量为0.36016 mm,最大等效应力值为567.75 MPa,仿真的结果显示最大等效应力的位置主要发生在齿圈前后端的齿根处。
4. 柔轮各结构参数对柔轮应力的敏感度分析
柔轮受交变力的作用下,容易发生疲劳断裂,对以上所设计的双圆弧齿廓谐波减速器的尺寸是否符合许用应力的要求,需要对筒长、壁厚、齿宽、倒角、圆角这五个关键参数进行分析,研究各个参数对于其工作性能的影响,根据各参数的经验公式,确定其取值范围,研究不同的关键参数对于柔轮的最大应力的影响,并设定两条路径,其中齿圈前后端的最大等效应力变化情况相似,所以取一条路径即可代表,定义path 1为柔轮齿圈方向;通过研究发现,虽然筒体圆角并非最大应力位置处,但有时也会出现应力集中现象,则设定path 2在筒体圆角处,通过这两条路径寻找参数变化时应力变化规律。
4.1. 筒长L对柔轮应力的影响
保持原有设计尺寸不变,改变柔轮的筒长,分析筒长为30、36、42、48、54、60 mm时对柔轮的最大应力值的影响规律,最大应力值的部分分析结果如图5所示,得出最大接触应力发生的位置均处于波发生器长轴处柔轮的齿圈后端与筒体交界处的齿根位置。
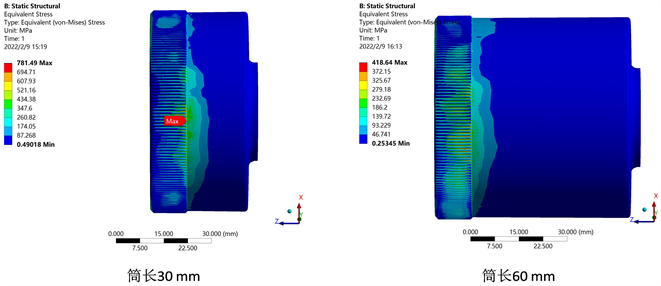
Figure 5. Stress diagrams of different cylinder lengths
图5. 不同筒长的应力图
将其对结果的变化趋势绘制如图6所示,观察曲线的变化值,可以得出,筒长的变化对柔轮应力的影响较大,柔轮的最大等效应力、齿圈与筒底处的应力值均随筒长的增加呈下降趋势,其中最大等效应力和齿圈处的应力下降趋势较快,筒底圆角处的等效应力也呈下降趋势,但较为平缓。
当筒体长度较小时,因波发生器与柔轮属于过盈配合,在筒体末端处的张角较大,导致应力值较大,同时因为张角的扩大使其与刚轮的啮合面积减小,导致传动效率降低,更易发生疲劳断裂失效,所以对于柔轮筒长的设计应保持与内径比0.6以上的范围,此时柔轮的最大等效应力的降低趋势处于较平缓的状态;但虽然筒体长度越长,应力值越小,过长的筒体会使柔轮的扭转刚度与强度下降,且在空间中的尺寸不能过大,需要轻量化处理,所以在设计的过程中要同时兼顾两者。

Figure 6. Transformation curve of maximum stress with cylinder length
图6. 最大应力随筒长变换曲线
4.2. 光滑筒体壁厚δ1对应力影响
保持原有设计尺寸不变,改变柔轮的壁厚,分析壁厚为0.34、0.4、0.46、0.52、0.58、0.64时对柔轮的最大应力值的影响规律,将分析结果的变化趋势绘制如图7所示,观察曲线的变化值,可以得出,当柔轮筒体壁厚增大时,最大等效应力先上升后下降,齿圈与筒体圆角的最大应力基本保持不变,柔轮光滑筒体壁厚在0.34~0.4区间内,最大等效应力是增大趋势,在0.4~0.64区间时,最大等效应力开始降低,整体的曲线较为不平滑。
在设计柔轮时,因柔轮齿的齿根圆半径要大于光滑筒体半径,故齿圈处的壁厚要大于光滑筒体壁厚,柔轮的光滑筒壁厚度影响着柔轮的刚度大小和承载能力,当壁厚较小时,柔轮所能传递的扭矩较小,当壁厚较大时,光滑筒体厚度变大,使柔轮能够产生的变形量减少,所以其受到的应力也会减少,但容易受周期性变形时产生破坏,影响其运行状态,所以选择合适的壁厚是比较重要的。
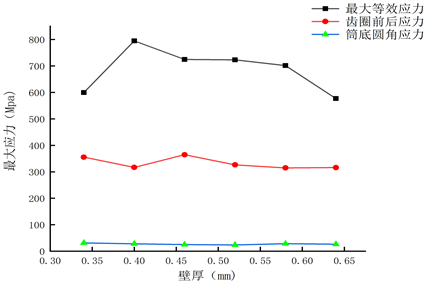
Figure 7. Transformation curve of maximum stress with wall thickness
图7. 最大应力随壁厚变换曲线
4.3. 齿圈宽度b对柔轮应力的影响
保持原有设计尺寸不变,改变柔轮的齿宽,分析齿宽为6、8、10、12、14、16时对柔轮的最大应力值的影响规律,最大应力值的部分分析结果如图8所示,其中最大应力发生的位置不变。
将分析结果的变化趋势绘制如图9所示,观察曲线的变化值,可以得出,当柔轮齿宽增大时,最大等效应力不断上升,齿圈的最大应力急剧上升,筒体圆角处的最大应力先下降后上升。
柔轮的齿圈是柔轮非常重要的部位,其发生弹性变形后部分齿与刚轮产生啮合,随着齿宽的增加,最大等效应力会逐渐变大,最大应力处为齿圈与光滑筒体接触产生的应力集中,过宽的齿宽会急剧增大柔轮的内部应力,而过窄的齿宽会使整个装配体的传动效率降低,所以在设计的过程中,应适当地减少齿宽,以满足其疲劳强度。
4.4. 圆角半径R对柔轮应力的影响
保持原有设计尺寸不变,改变柔轮的圆角半径,分析圆角半径为0.3、0.5、0.7、1.0、1.2、1.5时对柔轮最大应力值的影响规律,将分析结果的变化趋势绘制如图10所示,观察曲线的变化值,可以得出,柔轮圆角半径对于最大应力影响很小,随着圆角半径的增加,柔轮最大等效应力值缓慢增大,齿圈的应力值缓慢减小,筒底圆角处的最大应力值基本不变。
在圆角设计的过程中应考虑光滑筒壁厚度,为使圆角的结构更加均匀,最好与其保持相同水平。
4.5. 不同的倒角角度θ对应力影响
保持原有设计尺寸不变,改变柔轮的倒角角度,分析倒角角度为10、22、34、46、58、70时对柔轮最大应力值的影响规律,部分分析结果如图11所示,其中最大应力发生的位置不变。
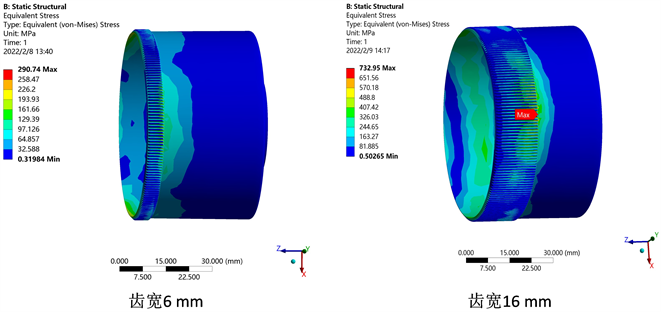
Figure 8. Stress diagrams of different tooth widths
图8. 不同齿宽的应力图
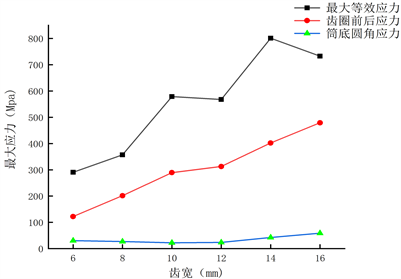
Figure 9. Transformation curve of maximum stress with tooth width
图9. 最大应力随齿宽变换曲线
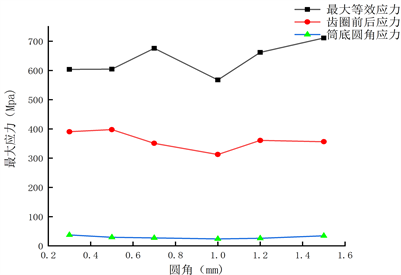
Figure 10. Transformation curve of maximum stress with fillet
图10. 最大应力随圆角变换曲线
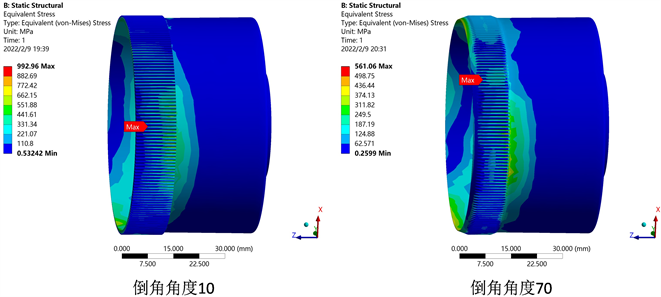
Figure 11. Stress diagram of different chamfer angles
图11. 不同倒角角度的应力图
将分析结果的变化趋势绘制如图12所示,观察曲线的变化值,可以得出,当柔轮倒角角度增大时,最大等效应力不断下降,倒角角度在22~34时急剧下降,其余保持平稳并有所下降,齿圈的最大应力先下降,达到平稳处有所上升,筒体圆角处的最大应力基本保持不变。
分析的结果说明倒角的使用能够有效降低柔轮的最大等效应力,减小柔轮所受的交变应力,增加其使用寿命,倒角角度过小时,齿圈后端的齿与光滑圆筒壁接触增加,壁厚也随之增加,最大等效应力很大,在设计倒角角度的过程中,应注意其角度不易过小。
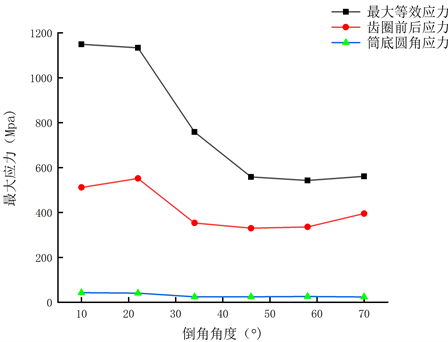
Figure 12. Transformation curve of maximum stress with chamfer angle
图12. 最大应力随倒角角度变换曲线
5. 多目标优化分析
根据以上单因素参数对于柔轮应力的分析后,并经过灵敏度分析后,得出筒长L、齿宽b和倒角角度θ对最大等效应力的影响最大,且因为在空间中使用的原因,对参数的取值范围进行适当缩减,取
,
,
。通过参数化筒长、齿宽和倒角角度后,设计柔轮的最大变形,最大应力和质量为多目标的输出参数,有限元分析后进入workbench DOE优化设计界面,选择BBD为响应面构建方法,因BBD对于样本点取值更加均匀,且可以控制单一参数的值,生成13组样本点,并通过这13组样本点对影响曲线进行拟合。
首先需要确定约束条件,对于柔轮应力的确定,需要满足最大等效应力能够保证柔轮在空间中的正常运转,即在许用应力的范围内,则约束条件为:
(5)
式中K为安全系数。
二阶函数模型如下式所示
(6)
建立多目标优化数学模型为
(7)
含有两个变量的等式约束关系,可以转化为驱动变量表示。
建立目标函数为
(8)
其中
即为输出变量。
5.1. 优化结果分析
通过对单一变量的分析,可得倒角越大,筒长越长、齿宽越窄,最大等效应力值越小,但若以此设计,最终的柔轮会不符合空间苛刻的使用条件,所以对于其加入轻量化处理,以最大变形量的值最小,最大等效应力的值最小,质量最小和约束条件,这些矛盾补偿进行优化求解,选用标准二阶响应面为响应面方法,对于BBD所生成样本点仿真出的数据进行分析求解,通过软件分析得出三组最优的参数方案,如表2所示。
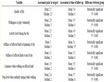
Table 2. Optimal combination scheme
表2. 最优组合方案
5.2. 优化前后柔轮的输出量变化
以上三种通过设定求解方法得出的样本值不利于加工,所以取筒长为41 mm,齿宽为11 mm,倒角角度为50度,重新建立双圆弧柔轮模型,并进行装配后得出仿真结果,与仿真前的结果进行对比,如表3所示。其中,优化之后的柔轮最大变形量降低0.2%,最大应力值降低25.6%,质量降低了3.2%。在兼顾了三个优化目标和约束条件下,取得了较好的优化结果。
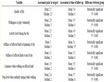
Table 3. Comparison of flexspline output before and after optimization
表3. 优化前后柔轮输出量比较
优化后的结果如图13、图14所示:
6. 结论
本文利用Ansys workbench对单因素结构参数对双圆弧齿廓柔轮等效应力的敏感性进行分析,并通过敏感性分析结论对柔轮进行多目标优化,将优化前后的模型进行比较,得出的结论如下:
1) 在柔轮的结构参数中,筒体长度对最大等效应力的影响最大,其次为齿宽和倒角角度,光滑筒壁厚度和筒底圆角半径对等效应力几乎没有影响,在进行柔轮的设计中,提供了优先考虑的变量。
2) 筒长越长,柔轮的应力值越小,但所占空间越大,且描述分析了各个参数对于双圆弧柔轮的影响规律,为柔轮的优化设计提供了依据。
3) 使用BBD对结构优化后,得出对于柔轮的最佳参数为筒长41 mm,齿宽11 mm,倒角角度50度,优化后的结果比初始设计柔轮最大变形量降低0.2%,最大应力值降低25.6%,质量降低了3.2%,既有效地减少了柔轮的应力,提高了其工作寿命,又使其更加小型轻量化。