1. 引言
随着科技的不断发展,金属在当今社会的需求量和使用量不断增加,但在金属材料的使用过程中,不可避免地会发生磨损、断裂和腐蚀等失效形式,其中由于金属腐蚀导致材料失效的比例占42% [1] [2],为延长金属使用寿命,降低成本,金属腐蚀问题逐渐被人们关注。表面涂层技术由于方法简单、成本低廉等特点,是目前应用最广泛的防腐手段之一。近年来,学者发现在涂层中加入锌粉会大大提高涂层的防腐性能,“锌涂层”也因其良好的耐蚀性受到广泛关注。性能优异的防腐涂层需要具备良好的物理阻隔性、电化学性能及附着力等 [3] [4] [5]。因此,本文综述了含锌有机涂层的物理屏蔽性、电化学防腐性、自修复性、失效模型以及结合强度五个方面,并展望了含锌有机涂层在防腐涂层领域未来的发展方向。
2. 锌粉在有机涂层中的应用
2.1. 锌的电化学特性
锌的电化学特征在防腐中极为重要,主要表现为:较低的电动势,较大的析氢过电位,腐蚀产物对涂层的自修复行为 [6] [7]。锌的腐蚀是一个电化学过程,锌充当阳极被氧化,阴极则为氢离子或溶解氧的还原,整个过程可以用化学式表示:
阳极:
(式1)
阴极:
或
(式2)
式1的能斯特方程 [4] 为:
(式3)
Zn的标准电位为−0.763 VSHE,Fe的标准电位为−0.448 VSHE,锌的电极电位比铁的更低,锌会先于铁发生氧化反应,锌和钢基材形成原电池,钢基材受到保护不会被腐蚀。
2.2. 锌粉在有机涂层中的分布
锌粉在涂层中的分布状态和颜料体积浓度(PVC)与临界颜料体积浓度(CPVC)的比值有关。颜料体积浓度(PVC)定义为在干涂层中颜料所占的体积分数,当PVC为某一个值时,在颜料紧密堆积的空隙间中,刚好填满树脂,此时的PVC则被称为临界颜料体积浓度(CPVC) [8] [9]。
(式4)
式中:Va涂料中颜料体积;Vb涂料中基料体积。
PVC和CPVC之比称为比体积浓度(Δ) [9] [10]:
(式5)
当
时,PVC小于CPVC,此时涂层存在连续的树脂基料,锌粉分散在树脂之中,锌粉与锌粉之间直接接触的概率减小;当
时,PVC刚好等于CPVC,则锌粉紧密堆积的所形成的空隙恰好被树脂填满,锌粉完全浸润在树脂之中,锌粉之间接触完全;当
时,PVC大于CPVC,则此时涂层中由锌粉堆积所形成的空隙不能够被树脂填满,锌粉出现絮凝现象,但彼此完全接触,此时涂层中存在大量空气。
涂层中锌粉的不同分布状态会对涂层的防腐性能和机械性能产生不同的影响。
2.3. 含锌有机涂层的分类
锌粉在涂层中的干膜占比是一个必要的因素,根据其他研究发现当锌含量较低时,部分涂层会具有更好的屏蔽效果,但是这样就削弱了阴极保护性能。这类锌涂层,因为锌含量较低所以这些涂层被称为低锌涂层,低锌涂层的比体积浓度
。随着锌粉的含量增加,当含量高于65%时,被称为富锌涂层 [11]。因此,一些标准是根据锌含量来划分富锌涂料,美国钢结构涂料协会SSPC-Paint20 [12] 将锌含量分为三个级别:干膜中锌粉的质量分数不少于85 wt%的为第一级,干膜锌粉质量分数介于77 wt%和85 wt%的为第2级,第3级为干膜锌粉质量分数介于65 wt%和77 wt%之间;中国化学工业标准HG/T 3668-2009的规定为:富锌涂层金属锌含量在非挥发组分中的占比不少于80 wt%为1类,金属锌含量占比不少于70 wt%为2类,金属锌含量占比不少于60 wt%则为3类;国际标准化组织ISO 12944-5规定,富锌涂层中非挥发组分的锌含量应大于等于80 wt% [13]。
随着富锌涂层的研究和发展,逐渐开拓了“锌保护”的新领域 [14]。1975年瑞士开发出一款冷涂锌涂层,该产品中锌含量约为93 wt% [15],近30年来,冷涂锌涂层发展迅速,并最终定义为干膜中锌含量高于90 wt%,以阴极保护作用为主的单组分富锌涂层 [16],又称为高锌涂层或冷镀锌涂层,高锌涂层的比体积浓度
。
3. 含锌有机涂层的防腐性能
3.1. 锌涂层的物理屏蔽性能
锌涂层中常用微米或纳米级锌粉作为填料,锌粉有球状和鳞片状两种形状。球状锌粉因为自身尺寸小,会形成无规紧密堆积的状态,此时锌粉与锌粉完全接触表面积较小,存在堆积空隙,树脂会充满这个空隙,形成致密的结构。当涂层涂覆在钢基材上,涂层会阻隔腐蚀介质与钢基材的直接接触,减缓腐蚀介质向钢基材侵蚀的速率,钢基材得到保护;鳞片状锌粉的片层结构会加大锌粉的接触表面积,产生的向下的作用力使得锌粉紧密堆叠,形成更致密的屏蔽保护层,腐蚀介质的侵蚀路径会被延长,提高了涂层的屏蔽能力,如图1所示。
同时,当
时,锌粉不能完全浸润在树脂之中,锌粉堆积出的部分空隙会由空气填充,形成多孔隙结构,锌涂层在喷水保养期间,会被氧化形成氧化锌及其水合物,堆砌锌粉间隙中形成“封孔”现象,物理屏蔽性能有所提高。
Arianpouya [17] 等人研究了少量纳米锌或纳米粘土对富锌涂料的腐蚀性能的影响,他们认为纳米锌和纳米粘土颗粒可通过改善屏蔽性能来提高富锌涂料的耐腐蚀性。Arman [18] 等人研究了用云母氧化铁(MIO)和Al代替锌颗粒对富锌环氧涂层的耐腐蚀性的影响,结果表明锌粉被取代后的涂层的耐蚀性能增强。
(a)
(b)
Figure 1. Corrosion path diagram of corrosive medium. (a) Spherical zinc powder; (b) Scaly zinc powder
图1. 腐蚀介质的侵蚀路径图。(a) 球状锌粉;(b) 鳞片状锌粉
3.2. 含锌有机涂层的电化学防腐性能
高导电性的锌粉紧密排列,相互堆叠形成高效的导电路径。在腐蚀介质穿透有机涂层引起基体腐蚀现象的初期,代替钢基材成为被腐蚀的主体,发生阳极反应失去电子,从而保护作为阴极的钢基材。但随着锌涂层中更多的锌粉被消耗,腐蚀程度加快,直至钢基材裸露在环境中,锌涂层的电化学防腐作用消失。
附着在钢基材上的锌涂层要发生电偶反应,需要符合以下三个条件:1) 涂层中的锌粉之间需要相互电接触;2) 锌颗粒与钢基材之间存在电接触;3) 锌颗粒与钢基材之间需要存在连通的电解基质 [15]。在有机锌涂层中,锌粉/锌粉、锌粉/钢基材存在的不是直接接触的情况,锌粒上会包裹一层树脂,只有当
,即
时,锌粉/锌粉才会相互形成电子传输通道,涂层此时才能充当阳极进而保护作为阴极的钢基材。而富锌涂层和高锌涂层的锌含量较多,基本能够满足锌粉间的电接触需求,能够与钢基材形成原电池。
因此,Li [19] 等人试图在
的低锌涂层中,通过添加石墨烯来连接锌颗粒,结果表明石墨烯低锌涂层具有优异的防腐性能,无需大量锌粉紧密堆积,有效的提升了锌粉的利用率。石墨烯/氧化石墨烯具有高导电性,理论上能够与锌颗粒之间形成电导通路,但是石墨烯与锌粉之间是如何桥接的还存在很大争议。
3.3. 含锌有机涂层的自修复性能
涂层表面因为受到外部机械力作用而受到损伤后,金属基材暴露于外环境之中,暴露部位由于腐蚀电流的加快通过更易被外环境腐蚀,锌与外环境作用产生的腐蚀产物将会缓慢生长最终形成腐蚀产物层,填补涂层缺陷并阻碍腐蚀介质与金属基材的直接接触,这就是锌涂层的自修补作用原理。我们认为当涂层存在缺陷时,金属基材与腐蚀介质直接接触发生腐蚀,铁失去电子形成Fe2+和Fe3+;锌粉与金属界面直接接触的区域,是由锌粉发生氧化反应失去电子形成Zn2+,电子流向基材表面发生还原反应;由于腐蚀环境的不同,会产生不同腐蚀产物,其中ZnO和Zn(OH)2为多孔、无定形状态 [20],γ-Fe2O3、γ-FeOOH、α-FeOOH等腐蚀产物可以形成较为稳定的保护膜,在含氯的环境中,会有腐蚀产物Zn5(OH)8Cl2·H2O [16] [21] 的生成,能提高涂层的耐腐蚀性能。
3.4. 含锌有机涂层防腐性能等效模型
目前国内外已经广泛使用电化学阻抗谱(EIS)来研究涂层的防腐性能和失效过程 [22] [23] [24] [25] [26]。含锌有机涂层的腐蚀防护性能也可以建立不同的模型应用EIS进行处理研究。
在进行EIS测试时,通常将涂覆了锌涂层的金属基材浸泡于3.5%的NaCl溶液中进行测量,模拟海水环境对锌涂层防腐性能的影响。在浸泡初期,电解质还没有渗透到锌涂层与金属基材的界面处,此时锌涂层起到一个物理屏蔽作用,锌涂层等同于一个“纯电容”,其典型等效电路模型如图2(a),Rs为溶液电阻,Rc为涂层电阻,Cc为涂层电容。
随着浸泡时间的增加,电解质溶液会逐渐渗入到锌涂层/金属基材界面,并会在界面处开始腐蚀金属基材并引起局部涂层鼓泡甚至脱落,如果是低锌涂层则电解质溶液大多会直接与金属基材形成腐蚀反应微电池,但如果是富锌涂层,则会引起锌的腐蚀从而避免了金属基材的腐蚀。此时就可以在阻抗谱图上观察到两个时间常数,并且涂层还未形成肉眼可见的宏观小孔,这个阶段称为浸泡中期,低锌涂层的典型等效电路模型如图2(b),富锌涂层的电路模型如图2(c)所示,Rp为微孔电阻,Rt为电子转移电阻,Cdl为双电层电容。而对于高锌涂层而言,除了会出现两个时间常数外,还由于涂层中存在的大量锌粉会阻挡电解质溶液渗入涂层/金属基材的界面,传质过程会变成界面腐蚀反应的决速步,阻抗谱会因此出现Warburg阻抗(W),高锌涂层典型的等效电路模型如图2(d)所示。
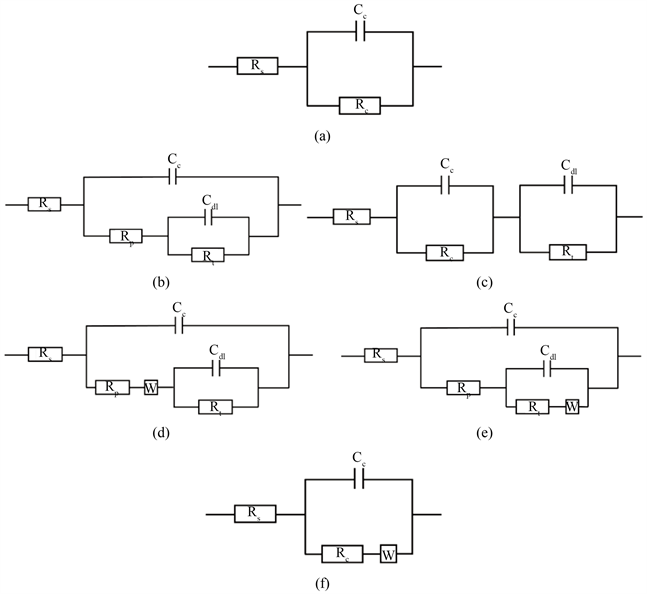
Figure 2. Common equivalent circuit model diagram of zinc coating failure process. (a) Initial stage of zinc coating soaking; (b) Mid-soaking period of low zinc coating; (c) Mid-soaking period of zinc-rich coating; (d) Mid-soaking period of high zinc coating; (e) Zinc coating after soaking; (f) Zinc coating expiration period
图2. 锌涂层失效过程常见的等效电路模型图。(a) 锌涂层浸泡初期;(b) 低锌涂层浸泡中期;(c) 富锌涂层浸泡中期;(d) 高锌涂层浸泡中期;(e) 锌涂层浸泡后期;(f) 锌涂层失效期
当锌涂层被渗入的电解质溶液进一步腐蚀,涂层形成宏观孔隙,出现锈点,这个阶段被称为浸泡后期。此时,渗入进涂层中的电解质溶液的浓度梯度以及完全消失,高浓度的电解质溶液会加快界面处的腐蚀反应,从而形成新的扩散层向金属基材内部渗透,其典型的等效电路模型如图2(e)所示。随着浸泡时间继续增加,涂层孔隙率急剧增多,涂层开始大面积起泡脱落,涂层已经丧失作为阻挡层对于金属基材的保护作用,此时的阻抗图谱信息完全来自于电解质对基材的腐蚀行为,即基材作为阳极发生的电化学腐蚀反应,锌涂层失效。此时的典型的等效电路模型如图2(f)所示。
4. 含锌有机涂层的结合强度
当腐蚀介质渗透含锌有机涂层到达涂层/金属基材界面区域时,含锌有机涂层与金属基材的结合力的强度大小直接反映出腐蚀介质在界面区形成新的扩散层的速度和进一步向金属基材侵蚀的速度。因此,含锌有机涂层与基材的结合强度是评价含锌有机涂层耐蚀性的重要影响因素。
含锌有机涂层常用的树脂是环氧树脂和丙烯酸树脂。环氧树脂是化学结构中含有两个及以上的环氧基的一类高分子低聚物的统称 [27],其中应用最广泛的双酚A型环氧树脂的结构式,如图3(a)所示。当环氧树脂作为涂层基料被涂覆在钢基材上时,环氧树脂中的环氧基、羟基会与金属表面的游离键结合形成共价键和氢键,从而使涂层和钢基材结合更加紧密。同时,固化剂中的氨基会与钢基材表面的羟基形成共价键,最终在涂层/钢基材界面形成亚氨基,增强涂层与金属的结合力 [28]。其中双酚A型环氧树脂由于存在伞状的双酚核结构 [29],分子旋转受到空间位阻的限制,分子内的羟基相互吸着也更为困难,因此,树脂中会有更多的极性基团与金属表面结合,涂层的附着力相应增强。
通常将丙烯酸酯、甲基丙烯酸酯及苯乙烯等乙烯基类单体为主要原料合成的共聚物称为丙烯酸树脂 [30] (图3(b)),它与环氧树脂相似,结构中存在的羧基存在极性,在接触金属基材时会产生偶极–偶极力,羧基还会与金属基材表面结合形成共价键和氢键,增强涂层的附着力。Jiang、Tae [31] [32] 等人将丙烯酸树脂进行改性,制备有机硅丙稀酸树脂,树脂结构中存在的硅烷会水解生成的硅醇基团,分子间的-Si-OH-会逐渐形成硅氧共价键-Si-O-Si-的交联,并会进一步与金属基材的游离键结合形成-Si-O-Si-Fe-键,以此来增强涂层的附着力。
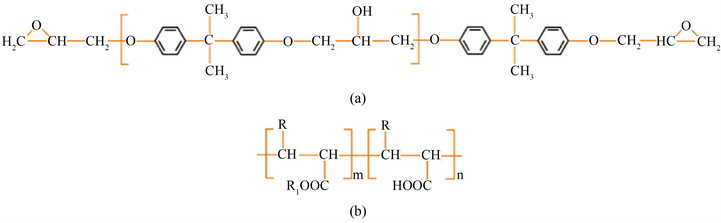
Figure 3. (a) Structural formula of bisphenol A epoxy resin; (b) Structural formula of acrylic resin
图3. (a) 双酚A型环氧树脂的结构式;(b) 丙烯酸树脂的结构式
5. 展望
在含锌有机涂层的防腐机理中,电偶保护是第一位的,屏蔽保护是第二位的。因此,今后对于锌涂层耐腐蚀性能的提高可以考虑在保证足够的电偶作用的情况下尽可能地提高屏蔽保护性能。综上所述,含锌有机涂层的电偶保护与涂层的CPVC、锌粉的形状以及锌粉的分布等有关;很多学者 [33] [34] [35] 基于对提高锌涂层物理屏蔽性能的考虑,在锌涂层中掺杂适量的石墨烯,以此减少锌粉的用量,用于改善涂层的屏蔽性能,结果表明涂层防腐性能提高。但是石墨烯是如何与Zn桥接,如何形成稳定的电导通路,石墨烯在锌涂层中的分布状况以及石墨烯在涂层中的防腐机理等问题还需要进一步研究探讨和理论支持。
未来含锌有机涂层必将向着低VOC的要求发展前进,如果能够解决石墨烯在含锌有机涂层中的理论问题,开发石墨烯–锌涂层将成为整个涂料工业发展的新方向。
NOTES
*通讯作者。