1. 引言
电子封装材料承载电子器件及互连外电路,对电子器件起到辅助散热、密封、机械支撑和信号传输的作用 [1]。当前,电子器件向小型轻质化与高集成化快速发展,这使电路芯片单位面积的发热量急剧增大,若散热环境不佳,芯片容易因过热而失效,同时若芯片与封装材料之间热膨胀系数不匹配,也会引起热应力疲劳从而导致芯片的失效 。因此,为了适应电子器件的发展,防止芯片在运行过程中失效,电子封装材料中最关键的部分即基板材料,应具备高的热导率、与芯片半导体材料(目前主要是Si和GaAs)相匹配的热膨胀系数、密度小、机械强度高、可加工性好、密封性好、低廉的成本以及可回收利用这些特性 [2]。
电子封装材料经历了陶瓷基、塑料基、金属基以及复合材料的发展过程。表1所示为几种材料的优缺点比较 [3]。塑料基材料的密度较小、介电性能较好、价格低廉,但热导率不高、介电损耗高、脆性大、热膨胀系数与半导体材料(Si)不匹配,仅可满足一般的封装技术要求。陶瓷基封装材料的密度较小、热导率(TC)较高、热膨胀系数(CTE值)匹配,是一种综合性能较好的封装方式,但其成本较高,仅适用于高级微电子器件的封装,如航空航天及军事领域。金属基封装材料的热导率较高、机械强度高、加工性能好,但热膨胀系数不匹配,成本较高。复合材料将各基体优良的性能与增强体进行优势互补,可以解决单一成分基体存在的不足,目前,先进的复合材料主要分为含碳均质、金属基、聚合物基、碳/碳复合材料和先进合金材料五种 [4],其中以金属基复合材料应用最广,其将金属基优良的导热性与增强基低膨胀特性相结合。
作为热匹配复合材料用于封装的主要是铜基和铝基。铝的密度为2.7 g/cm3,熔点为660℃,热膨胀系数为23.03 × 10−6/K,热导率为237 W/(m·K)。铝的密度较小,有很强的可加工性,熔点较低,因而对设备的要求相对较低,可以通过复合不同性质的增强体调节物理和力学性能,制备出与芯片半导体相匹配的复合封装材料,与铜基体相比,铝基体更适应轻量化的要求,故铝基复合材料在电子封装领域的研究已成为热点。
铝基复合材料将金属的高导热性与陶瓷的低热膨胀性相结合,能满足多种功能特性及设计要求,具有高导热、低膨胀、高刚度、低密度、低成本、制备工艺灵活、基体合金多样化等综合优异性能,是当今电子封装领域的研究热点。目前正在研究的应用于电子封装材料的高导热、低膨胀金属基复合材料主要有:SiCp/Al,金刚石/Al,Si/Al,C/Al,BeO/Al,等。这其中SiC/Al作为工艺成熟、成本低廉的一种复合材料,应用最为普遍 [3]。本文介绍了以铝为基体的复合电子封装材料的特点,增强体包括SiC、金刚石、Si、C等,同时介绍了相应的制备方法及应用 [5]。
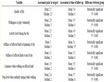
Table 1. Comparison of four electronic packaging
表1. 电子封装常用材料对比
2. SiCp/Al复合材料
在铝基复合材料中,SiCp/Al复合材料综合Al和SiCp的热物理性能优点,具有较高的热导率、较低的热膨胀系数、高机械强度、低密度以及良好的导电性等,几乎满足了理想的电子封装材料应具备的特性,因此,该材料是目前研究最热门的封装材料 [6]。SiC陶瓷的热导率很高,热膨胀系数较低,电绝缘性能良好,强度高,但SiC介电常数太高,限制了其在高频的应用,仅适用于低频封装。
2.1. 研究现状及应用
国外一批公司较早地开始研究和开发AlSiC电子封装材料,极大地推进了复合材料的开发和应用 [7]。目前,国外研究生产AlSiC复合材料的代表企业有Thermal transfer Composites,LLC (TTC)公司,DWA公司、Polese公司、Ceramics Process Systcrns (CPS)公司 [8] [9] [10] [11]、PCC Advanced forming Technology (PCC-AFT)公司和美国铝业(Alcoa)公司 [12]、Osprey金属公司、Aerospace Metal Composites (AMC)公司、日本Denka电化株式会社、日本田岛株式轻金属会社和德国DMC2公司 [13]。另外,Ixion Thermal Materials公司研制了70% SiC/Al复合材料;M.SchÖbel等 [14] 用搅拌铸造法制备了60% SiC/Al复合材料;Lanxide公司采用无压浸渗法制得SiC/Al复合材料,并可达到净成型效果,产品性能优良。
国内对SiCp/Al复合材料研究起步较晚,重要科研院所、单位机构对AlSiC复合材料的研究主要处于研发阶段 [15] [16]。自20世纪80年代以来,国内学者们在制备工艺等基础研究方面已可媲美国外水平。黄俊等 [17] 采用无压浸渗法制得体积分数为50%~70%的β-SiCp/Al复合材料,热导率高达170 W/(m·K),热膨胀系数达6.6 × 10−6/K~9.7 × 10−6/K;刘庆芬 [18] 采用粉末冶金法制得50%vol.β-SiCp/Al复合材料,TC值为124 W/(m·K),CTE值到8.86 × 10−6/K,满足封装材料热物理性能要求。
尽管可以制得高质量、高性能的SiCp/Al复合材料,但涉及实际电子封装应用时,产品的尺寸却达不到相应的精度要求,近净成型工艺尚不成熟,产品的制造成本高,离商业化生产还有很长一段距离。且尚未形成完整的(设计–制备–加工–应用–评价)技术链,在军事、国防应用方面相差不大,民用方面受制于成本应用较少 [19]。
2.2. 制备方法
合理选择制备工艺对复合材料的性能至关重要,在电子封装中,SiC体积占比为55%~80%的SiCp/Al复合材料才能满足要求。SiCp/Al复合材料常用的制备方法有粉末冶金、无压浸渗、压力浸渗、共喷沉积、等离子喷涂法、挤压铸造和气体压力渗透。
2.2.1. 粉末冶金法
粉末冶金法先将铝基体颗粒或粉末和增强体SiC颗粒或粉末混合,制成复合坯料,再烧结成型,该方法的路线示意图如图1所示。粉末冶金法制备温度低,界面反应相对较少,可避免界面上硬脆相的产生,同时,该方法可准确调控增强体颗粒的体积分数,体积分数可高达75%;增强颗粒可选范围宽。
美国的DWA公司采用粉末冶金法生产55%vol.SiCp/A1复合材料,成型产品后续加工简单,密度为2.99 g/cm3,热导率达 220 W/(m·K) [20]。
史艳艳 [21] 改进了传统的粉末冶金法,在热压烧结温度上升过程中增加预压工艺来代替冷压坯工艺,简化了制备工艺,缩短周期。研究表明,在烧结温度为690℃,烧结压力为30 MPa保温1 h的工艺条件下制得的体积分数为70%的β-SiCp/Al复合材料,热导率高达157.4 W/(m·K),热膨胀系数达8.2 × 10−6/K,满足封装要求。

Figure 1. Preparation of SiCp/Al Composites by powder metallurgy
图1. 粉末冶金法制备SiCp/Al复合材料的路线
2.2.2. 无压浸渗法
无压浸渗法是熔融液相自发渗入含孔预制体,冷却后获得复合材料的方法。该方法最先由美国的Lanxide公司开发。因制备工艺简单,没有外界压力参与,设备简单方便操作,成本较低,兴起后成为国内外研究热点,如崔岩等 [22] 在氮气保护气氛下制备了60%vol. SiCp/A1复合材料,热导率大于180 W/(m·K),热膨胀系数8.35~8.78 × 10−6/K,性能优异。为使浸渗过程顺利进行,金属熔体与增强相颗粒必需满足:高温下基体与强化相有良好的润湿性;增强相预制体内含有均匀分布且相互连通的多孔通道;基体金属一般熔点偏低,组成相之间化学反应产物容易去除或对有益于提高材料性能。
2.2.3. 压力浸渗法
压力浸渗法制SiCp/A1复合材料就是熔融金属Al液在压力作用下渗入SiC预制骨架中,首先需要制好增强体SiCp预制件,其次是在外界压力参与下渗入基体金属熔体,随后冷却获得复合材料。采用该方法制备复合材料,必须控制好参数,主要有SiCp预热的温度、加入Al液的温度和加压大小等。工艺优点是操作简单,容易制得高体积含量的SiCp/A1复合材料,产品稳定性好,制备周期短,相对密度高,缺点是对设备和模具要求严苛,制品形状有较大的限制,费用昂贵 [23],尤其是小型薄壁的零部件,制造困难,成本偏高 [24]。利用压力浸渗法制备的AlSiC复合材料,材料组织均匀致密,有害物质、气孔夹杂量少。
2.2.4. 共喷沉积法
共喷沉积法是Siager在1969年开发的,随后Osprey-Metals有限公司应用此方法进行工业化生产。共喷沉积法是将雾化后的金属液滴与颗粒在惰性气氛中通过专用喷嘴同时喷入并沉积在模具衬板上,冷凝后获得复合材料的方法。制备SiCp/Al复合材料时,雾化获得Al液滴很关键,它决定了液态金属雾化液滴的大小和尺寸分布。同时增强体SiCp颗粒加入的方式加入量和加入速度直接决定了SiCp/Al复合材料中SiCp的含量和分布。共喷沉积法生产工艺简单易掌握,生产效率高,可通过控制工艺参数有效控制界面化学反应,增强体颗粒均匀分散程度,还可以减少氧化,但需要后续二次加工 [25]。
2.2.5. 等离子喷涂法
等离子喷涂法采用压缩电弧作为热源,等离子体受激励产生等离子弧高温,高温将基体熔化后经孔道高压压缩后呈高速射流喷射到基板表面,冷却并沉积得到目标材料。等离子喷涂制备复合材料的优点是成型速度快、周期短、涂层材料结合强度高,但喷涂设备昂贵,且喷涂的复合材料有大量孔隙,存在残余应力,限制了进一步应用和发展 [26]。目前,国内外学者仍在对实际应用方面进行研究,主要存在SiCp与Al界面润湿差、需二次加工、成分均匀性不佳以及不能精确控制SiCp含量的问题,应在SiCp的表面改性技术、精准控制强化相SiCp含量、开发近净成型工艺以及提高SiCp/Al复合材料成分均匀性方面进行进一步研究。
3. 金刚石/Al复合材料
金刚石具有高热导率、高弹性模量以及低热膨胀系数,同时,金刚石稳定性好、半导体禁带宽、耐磨损 [27],是自然界已知的最坚硬的材料。金刚石与铝性能差异巨大,将两者进行复合,不仅可以充分发挥铝金属的优势,还能发挥金刚石独有的特性,与金刚石/Cu复合材料相比,金刚石/Al复合材料因密度更小更有利于器件的轻量化,因此,金刚石/Al复合材料是理想的第四代复合电子封装材料 [28]。
3.1. 研究现状
BEFFORT等 [29] 采用液压浸渗后挤压成形的方法成功制备出金刚石/Al复合材料。但基体与增强相润湿性差及不同传质方式导致的界面结合问题,极大地削弱金刚石在复合材料中的作用。金刚石与Al的润湿性极差,在1000℃时铝对人造金刚石的浸润角是150˚,难以直接制备出致密度较高的复合材料,而孔隙的存在显著降低材料的热导率 [30]。因此,需要对金刚石进行表面改性或对基体进行合金化处理,但此类处理会增加界面热阻或促进界面反应。因此,如何在提高金刚石与金属润湿性的同时,减小界面热阻,获得稳定的高性能复合材料是国内外学者不断研究的课题。
MIZUUCHI等 [31] 将复合粉末采用放电等离子烧结的方式成功制备了致密度高达99%以上、热导率为552 W/(m·K)的金刚石/Al复合材料。
3.2. 制备方法
目前,金刚石/Al复合材料已在电子封装领域得到小批量应用。金刚石/Al复合材料的制备方法主要包括粉末冶金法与熔渗法,粉末冶金法包括放电等离子烧结法和真空热压烧结法,熔渗法包括无压浸渗法、气压浸渗法和挤压浸渗法。
3.2.1. 超高压烧结法
超高压烧结 [32] 是制备金刚石复合材料较为理想的一种工艺。该工艺直接将混合料放入高温高压烧结炉中,在两面或者六面顶压机的作用下同时加热加压。此过程中一般保持压强大于2 GPa,温度为大于1000℃,但主要是以高压为驱动力促进烧结。在烧结过程中,压头从多个方向同时对腔体内的合成块施压以提高合成块的松装密度,以静压方式增加合成块的实际压力,然后对样品加热使其致密化。在超高压力下,合成的样品相对密度极高,而且不会出现金刚石在高温烧结过程中可能出现的同素异构转变现象,还可能促进金刚石颗粒之间的键接,有助于得到高热导率和低膨胀的金刚石复合材料。总之,超高压烧结法制得的产品致密度很高、性能优异,但此法对设备要求很高、成本昂贵,只适合制备简单形状的制品,而且产量不高。
He等 [33] 以高温高压法制备出了Cu-Zr/金刚石复合材料,通过调节Zr含量在界面处形成ZrC促进了铜基与金刚石的界面结合,获得的复合材料热导率高达677 W/(m·K)。Ekimov等 [34] 在8 GPa、1900~2100 K条件下,探究了金刚石颗粒尺寸对金刚石/铜复合材料导热性能的影响,在金刚石为200 μm时,制备出热导率最高可达900 W/(m·K)的复合材料。Kidalov等 [35] 通过高温高压法,在6~6.5 GPa,1000℃~2000℃下制备出了金刚石/碳复合材料,发现由纳米金刚石制备的复合材料热导率在10 W/(m·K)以下,而由微米级金刚石制备的复合材料热导率可高达500 W/(m·K)。Yoshida等 [36] 以金刚石和铜粉为原料,在1420~1470 K温度范围内,4.5 GPa压强下,制得金刚石/铜复合材料,其中金刚石体积分数为50%~80%。研究表明:金刚石体积分数或颗粒尺寸不同时,金刚石/铜复合材料有不同的热膨胀性能和热导率。并且指出界面热阻是影响金刚石复合材料热导性能的重要因素。
3.2.2. 放电等离子体烧结
放电等离子烧结 [37] 技术开始于20世纪90年代,是将陶瓷或金属粉末等装入石墨模具中,通过上下模冲和通电电极把特制的烧结电源以及设定的压制压力作用至烧结粉末上,并经过放电活化、热塑性变形及冷却等过程获得优秀性能材料的一种新烧结技术。其中,等离子体是指解离出的高温导电气体,原子和气态分子活化程度极高。放电等离子体烧结也就是利用这些等离子体来进行烧结的。SPS技术具有如下特点:升温速度很快,脉冲电压超过某一定值时,粉体间绝缘层被击穿,产生放电现象,能够净化粉体表面,有助于快速烧结,从而抑制了晶粒的再生长,组织结构可控,可在较低温度下烧结,环保节能等。通过调整烧结工艺及复合材料组成,可在较短时间内制备出高致密度复合材料。图2所示为放电等离子体烧结示意图。

Figure 2. Schematic diagram of spark plasma sintering
图2. 放电等离子体烧结示意图
Zhu等 [38] 首先通过气相沉积法在金刚石表面镀上一层Al膜,然后通过SPS技术在1163 K下制备出金刚石/Cu复合材料,在金刚石体积分数为50%时,复合材料热导率为565 W/(m·K)。他们同样制备出金刚石/Si(Ti)复合材料,结果表明,Ti的添加有利于提高材料致密度和热导率,当金刚石体积分数为60%时,复合材料热导率达525 W/(m·K),其在573 K下的热膨胀系数为1.643 × 10−6/K。Zhang等 [39] 以SPS技术制备出镀钛金刚石/Cu复合材料,Ti层厚度为285 nm,结果表明镀钛能有效提高金刚石复合材料导热性能,通过在表面形成TiC层,使复合材料热导率达到493 W/(m·K)。
3.2.3. 热压烧结
热压烧结 [40] [41] 是对装入石墨模具中的粉体施加压力并同时加热获得致密复合材料的烧结过程,压制与烧结同时进行,即通过调节压力使坯体变形及经过通电产热促进烧结。与无压烧结相比,热压烧结的优势在于烧结温度低,界面反应可控,复合材料致密度高,但其加热过程、冷却过程时间相对较长,不适合制备形状过于复杂的样品。
Zhang等 [42] 研究了镀W层对热压烧结金刚石/Cu复合材料热导性能的影响,发现在含Cu-W双层结构复合材料中热导率达695 W/(m·K),高于仅含Cu单层结构复合材料的热导率386 W/(m·K)。Chu等 [43] 以真空热压烧结方式在980℃、42 MPa条件下制备出了Cu-Zr/diamond复合材料,热导率为615 W/(m·K)。Schubert等 [44] 以铜硼合金和铜铬合金为基体材料,选择粒径为120 μm的金刚石,通过热压烧结制备出热导率达450~500 W/(m·K)的金刚石/铜复合材料。发现热压烧结过程可以使金刚石与各金属在界面处形成过渡的碳化物,有助于改善金刚石与铜的界面结合情况,使复合材料的热导性能上升。
3.2.4. 浸渗法
浸渗法 [45] 主要包括压力、气压及无压浸渗法三种。压力浸渗法一般是将熔点低膨胀颗粒材料制成预制件,而后通过机械应力推动低熔点金属液进入预制件来制备金刚石复合材料;与压力浸渗法相比,气压浸渗是通过惰性高压气体起推动金属液进入预制件的作用而非机械应力,气压一般为1~10 MPa;无压浸渗法是另一种可以制备高体积分数颗粒增强复合材料的方法,与压力及气压法相比,其浸渗过程中不加压,在惰性气体或还原性气体中,金属熔体依靠反应润湿或毛细管力等作用浸入预制件凝固得到复合材料 [46]。
Li等 [47] 以气压浸渗法制备出镀钛金刚石/Cu复合材料,复合材料热导率可达716 W/(m·K),50℃下的热膨胀系数仅为5.8 × 10−6/K。Kang Q等 [48] 采用真空压力浸渗法制备了镀Cr金刚石/Cu复合材料,研究发现在金刚石表面形成了Cr7C3层,获得的复合材料热导率达562 W/(m·K),热膨胀系数为7.8 × 10−6/K,适合用作热沉材料。
3.2.5. 低温常压烧结法
低温常压烧结法 [49] 是较为常用的复合材料制备方法,一般是通过球磨等方法将基体粉末与金刚石混合均匀,冷压成型,得到坯件,最后经过常压烧结获得较致密复合材料。此方法的主要特点在于:对金刚石及基体材料的选择性较广,可任意选择两者间的比例、尺寸、形状,也可实现近净成型;但其制备较为复杂,工艺条件如烧结温度、时间、成型压力等对材料性能及致密度等影响较大。
Raza等 [50] 以常压烧结法制备出金刚石/Cu复合材料,选择未镀覆、镀Cu、镀Cr三种形式金刚石与Cu复合,在525 MPa下冷压成型,900℃烧结2 h,制备的复合材料热导率值分别为275 W/(m·K)、284 W/(m·K)和312 W/(m·K)。高凯 [51] 以常压法制备出了金刚石/陶瓷多晶复合材料,并探究了Na2O、CaO、MgO等添加剂对复合材料性能的影响,结果表明在常压下制备的复合材料具有较低的介电常数和介电损耗。目前,常压法常用于制备磨削工具用金刚石/金属和金刚石/陶瓷复合材料。
4. Sip/Al复合材料
在航空航天领域中,轻质是非常重要的考察特性,因此,高硅铝合金具有的轻质、良好的热导性能以及低热膨胀系数等优点,使Sip/Al复合材料在航空航天领域受到极大关注,也是应用前景广阔的电子封装材料之一。
4.1. 研究现状
超高硅铝合金因其具有的显著优势在国际上得到了较多的研究。欧洲、美国以及日本在超高硅铝合金复合材料研发上有着明显的技术优势。其中,瑞典的Sandvik公司利用喷射成形工艺已经生产出Si-Al系列合金,其Si硅含量可在30%~70%之间按需制备。并通过致密化处理得到了性能良好的商业化产品。Sandvik公司已经通过喷射沉积与致密化技术制备出了70Si-Al合金,其CTE值为7.4 × 10−6/K,室温TC值达到120 W/(m·K),密度 < 2.6 g/cm3,是性能优良的电子封装材料,Grant等利用喷射沉积技术制备出了Al-70Si合金材料 [52]。
国内对超高硅铝合金的研究工作起步比较晚,主要集中在一些大学与科研机构之中。李超等 [53] 采用喷射沉积与热压相结合的方法成功制备出Si-30% A1合金,合金经致密化工艺处理后,其室温热导率为110 W/(m·K),400℃时材料CTE值低于10 × 10−6/K,但是材料力学性能较差。
杨培勇等 [54] 采用粉末冶金液相烧结工艺制备出了A1-50% Si合金是发现,压力的增加可以有效提高合金材料的热导率,但是过高压力会对Si粉产生破碎作用,造成界面增多,使界面热阻上升,降低材料热导率。虽然国内外对超高硅铝合金的热物理性能和制备工艺进行了比较多的研究,但很少有学者通过引入第三组元的方式从整体上改善材料的力学性能与机械加工性能,降低材料的生产成本的研究还比较少。
4.2. 制备方法
目前,Sip/Al复合材料的主要制备方法有无压浸渗法、真空加压法、加压浸渗法、粉末冶金法和喷射沉积法。
4.2.1. 熔炼铸造法
熔炼铸造作为常规的合金制备方法,具有设备简单,成本低的显著优势。对于铝硅合金材料,其组织中的初晶硅与共晶硅的尺寸和形态在很大程度上决定了材料的性能。
组织中还会出现较多的缩松缩孔现象,力学性能较差。行之有效的解决方法是通过加入P等变质剂细化初生硅,并在工艺上通过电磁搅拌等方式来得到较好的合金性能。但是这种方式对设备要求高、工艺复杂、生产成本较高。而且工艺过程不易控制,生产效率低 [55]。
4.2.2. 喷射沉积法
喷射沉积法是由英国斯旺西大学的Singer教授在1968年提出 [56],在20世纪末由英国Osprey metals公司在工业上实现生产的。通过喷射沉积法制备高硅铝合金的主要过程为:1) 熔料。将铝硅原材料在感应炉中加热成熔体,通过导流管将熔融的铝硅合金液导出。2) 气体破碎雾化。利用高速惰性气体冲击液流,使液流被破碎形成细小固态、半固态和液态颗粒分布的射流。3) 沉积。在高速气体的作用下,破碎的射流会在基板上沉积,形成一层层铺展、融合,并最终凝固得到组织细小、各向同性的致密坯体。高硅铝合金喷射沉积形成的组织主要是由ɑ (Al)基、硅颗粒以及少量孔洞组成。喷射沉积技术的主要优势在于其快速凝固的特性和真空条件的外部环境,可以大大减少晶粒生长的可能性,并且降低颗粒氧化程度,得到在Al基体中均匀分布Si相颗粒的材料组织。其次,喷射沉积法可以不受材料本身固溶极限的限制,提高Si相在Al基体中的固溶度。但是该方法制备的坯锭存在一定的孔隙,无法直接应用,必须经过后续加工如热等静压等工艺,才能得到良好性能的材料。工艺参数复杂,主体设备及辅助机械昂贵,材料成型困难、产品致密性差,另外,在制备过程难以控制,喷射的金属液滴不稳定,增强体颗粒在沉积过程中失态流动,造成有效结合率较低,原材料损失大,难以实现大规模生产。
4.2.3. 熔体浸渗法
熔体浸渗法主要包括压力浸渗(挤压铸造)、无压浸渗和真空压力浸渗三种工艺。该工艺的优点是工艺相对简单,能够近净成形。缺点是压力浸渗增强相制备困难,成本较高 [4]。
1) 压力浸渗法。
压力浸渗技术即为在外力作用下,将金属液压入增强相骨架,使其良好结合的工艺。其主要是针对于基体与增强相润湿效果差,难以通过二者之间的毛细作用力进行浸渗的复合材料。压力浸渗方法主要优点是生产周期短、工艺简单、产品稳定性好,对材料之间润湿要求不高。但是对于高硅铝合金来说,制备Si骨架成本较高,难以做出孔隙均匀的增强相。另外,在压力浸渗过程中,预制件常会因为压力过大而出现开裂、溃散等现象。生产成本高,只适合于生产小型零件。
2) 无压浸渗法。
无压浸渗法可以理解为在高温下利用液态金属的毛细润湿作用渗入预制件,从而获得复合材料。此方法是20世纪90年代由美国Lanxide公司开发的一种独特的工艺。该方法适用于润湿性较好的基体和增强体。因操作简单、设备要求不高,非常适合制备具有高体积分数低热膨胀系数的电子封装材料。但是对于Si-Al合金,由于铝与硅颗粒之间的润湿性很差,铝液无法完全浸入Si增强相当中,常常在复合材料中出现大量孔洞,材料机械性能较差。
3) 真空压力浸渗法。
真空压力浸渗法是利用大气压力来促进液体金属与增强体的结合 [57]。其第一步是制备增强相预制件。第二步为是将增强相预制体放入模具内,抽真空并通保护气氛,然后施加5~10 MPa的压力将熔融金属液体压入模具中,直至金属液体完全浸透预制件,冷却后即可得到金属基复合材料。该方法最大的优点是克服了压力浸渗和无压浸渗的缺点,成形压力变化范围大,适用面广,可直接成形,且受增强相材料的形状、尺寸、含量等限制少,可制成近净形构件,但是该方法存在对浸渗设备要求比较高、工件尺寸受限制以及生产效率低等缺点,不适合高硅铝合金科学探索与批量化生产。
4.2.4. 粉末冶金法
粉末冶金法是制备非连续增强型金属基复合材料的一种基本方法,被称为“绿色制备工艺”。粉末冶金法的主要优势在于:1) 可以根据需要对材料成分进行设计,对增强体尺寸要求较低,实现材料热物理性能的调整;2) 增强体和基体种类选择范围较宽,粉末烧结温度可控,可最大限度降低基体与增强体之间的界面反应的不利影响。在实践过程中发现,在通过粉末冶金方式制备高硅铝合金材料时,需要注意增强体的加入量,当加入量过多时,会造成材料冷压、热压成型困难,材料机械性能较差 [58]。
5. 其他铝基复合材料
5.1. C/Al复合材料
碳纤维增强金属基复合材料易于切削加工,在电子封装领域有极大的应用潜力,但是其较差的热导性能极大地限制其发展。碳纤维增强铝基复合材料具有轻质、高强、低热膨胀系数等符合理想电子封装材料要求的特性,但是其界面反应显著,在制备或服役过程中会导致复合物热物理性能降低。
为充分利用石墨纤维优异的理化性能,近年来逐步在以石墨纤维为增强体的基础上与金属材料复合,开发出新型金属基复合材料,大大拓展了石墨纤维材料的应用范围。石墨泡沫、高导热石墨纤维、碳纳米管、天然鳞片石墨等高导热与低热膨胀的石墨系材料尝试作为增强体进行了一定研究,但石墨泡沫、碳纳米管与天然石墨生产工艺复杂,生产成本较高,不能大规模应用 [59] [60] [61]。
5.2. AlN/Al复合材料
AlN陶瓷具有多方面优质的性能,例如高导热、高绝缘性等,然而其成本高、工艺难度大。基于陶瓷绝缘层的金属基板(IMS)因结合了金属与陶瓷的优点而受到关注,例如Al-AlN基板兼具高热导率、绝缘性与反射率。然而由于Al与AlN之间热膨胀系数差异大,结合强度不高,高速率沉积AlN困难,而使得该技术未能得到有效应用。
李明鹤等 [62] 采用磁控溅射法在阳极氧化预处理过的铝板上沉积氮化铝薄膜,制备氮化铝–铝复合基板。制备的氮化铝为非晶态,抗电强度超过700 V/μm,阳极氧化铝抗电强度达75 V/μm。他通过射频磁控溅射在硅片、光学玻璃上沉积氮化铝薄膜,对金属铝基底进行阳极氧化预处理以解决金属铝与氮化铝结合强度差的问题,在阳极氧化预处理过的铝基底上沉积氮化铝薄膜制备铝基氮化铝薄膜,结果表明,基体各项性能均得到提升,值得深入研究 [63]。
6. 展望
电子器件的发展带动电子封装材料高速发展,尽管目前以SiCp/Al、金刚石/Al、Sip/Al为代表的铝基复合电子封装材料已得到部分应用,但这些材料本身存在的缺点如难加工、热导率低等日益显现,阻碍了其大规模应用。因此,未来的铝基复合材料还应着眼于实际服役条件,可采取纳米级材料作为增强相,开发更加匹配电子器件的电子封装材料。
基金项目
湖南省科技人才专项——湖湘青年英才(2019RS2067),湖南省创新平台与人才计划——湖湘青年英才(2021RC3140)。
NOTES
*通讯作者。