1. 引言
车架是汽车的关键承载部分,它主要由横梁和纵梁组成。大多数部件都会固定在车架上,如驾驶舱、动力装置、储油装置和货物等。在汽车静止和行驶的过程中,车架一般会受到很多力和载荷的作用,最终会导致车架产生变形。出于对安全性和舒适性的考虑,因此我们有必要对货车车架进行有限元分析,判断其是否满足刚度和强度的要求,以及是否会引起共振。
智淑亚 [1] 等人对车架的刚度理论进行了介绍,基于CATIA对车架结构进行三维建模,通过ANSYS软件进行仿真并对其结果进行分析,判断其刚度和强度是否在设计范围内。王维伟 [2] 等人通过Hypermesh对车架进行建模并分析满载时车架变形和应力情况,在此基础上,使用Optistruct进行优化设计,设计出车架轻量化的最优解。金璐 [3] 通过有限元分析研究车架在几种工况下的位移和应力情况,为车架的设计和优化改进都提供了依据。于志新 [4] 等人通过对车架进行模态分析并得到共振频率和对应的振型图,为避免共振提供了一定的理论依据。
本文主要研究的是某货车车架在几种基本工况下,对车架施加载荷和不同的约束,通过静力学分析,求解出其对应的最大位移值、最大应力值和固有频率值,判断其刚度和强度是否超过材料所承受的极限值,以及是否会发生共振现象。
2. 材料与方法
本文研究的是某货车车架,其使用材料为B550L,材料属性如表1所示。
对于该货车车架的有限元分析,本文提供的研究方法如下:
1) 研究该货车车架结构在不同满载工况下的受力情况;
2) 利用UG建立三维模型并导入ANSYS进行有限元分析,确定不同工况下的变形与应力情况;
3) 通过有限元分析的方法,对该车架进行自由模态的仿真,可以模拟出该车架前12阶的固有频率以及其对应的振型图,判断其是否会发生共振现象。
3. 结构分析与模型建立
3.1. 结构分析
研究对象是边梁式货车车架,该车架采用槽型钢板,前后等宽,7根横梁位于2根纵梁之间,它们通过焊接连接在一起,两两横梁之间有一定的距离,横梁和纵梁截面均设计为槽型结构。车架长7700 mm,宽863 mm,高150 mm。车架结构简图如图1所示。
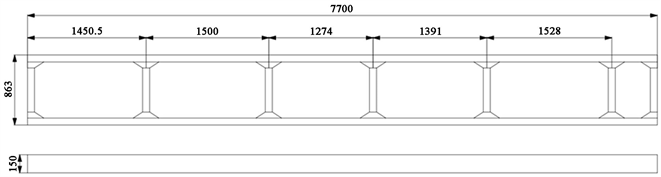
Figure 1. Structure diagram of the frame
图1. 车架结构简图
3.2. 模型建立
货车车架的小零件比较多,因其对整个车架强度和刚度的影响较小,为便于分析,简化车架某些不重要的部位 [5]。通过UG建立三维模型如图2所示。
在ANSYS的Design Moderer模块中完成印记面的操作 [6],将车轮的4个接触面在纵梁的各个位置表示出来,再在Static Structural模块中对车架进行四面体网格自动划分,该车架网格划分的结果为75,321个节点和32,797个单元,通过节点数和单元数发现自动网格划分满足精度要求。图3为车架有限元模型图。

Figure 3. The finite element model diagram of the frame
图3. 车架有限元模型图
4. 静力学分析
4.1. 车架所受载荷处理
第1根横梁主要承受驾驶舱的载荷,第2根横梁主要承受动力装置的载荷,第3根横梁主要承受储油装置的载荷和部分货物的载荷,第4、5、6、7根横梁上主要承受货物的载荷。驾驶舱、动力装置以及储油装置的载荷都可以简化成集中载荷作用在各自的横梁上,而货物的载荷可以简化为均布载荷作用在第3、4、5、6、7根横梁上 [7]。表2为各部件的载荷,图4为载荷加载示意图。
4.2. 货车典型工况下的车架分析
4.2.1. 弯曲工况
此工况就是车架在满载时处于静止的状态,表3是该工况各个支撑点的边界条件,图5是求解出来的位移云图结果,图6是求解出来的应力云图结果。由图5可知该车架的最大位移值约为4.8 mm,图中红色区域表示弯曲变形较大的地方,主要集中在中部两根横梁上,还有车架中部的纵梁上;由图6可知该车架的最大应力值为129.15 MPa,最大应力点在右后轮的接触面处。设计该车架的钢板厚度为12 mm,一般规定车架的最大许用挠度值不大于设计钢板厚度的1.5倍,所以该车架最大许用挠度值是18 mm,当最大许用挠度值大于变形量时,刚度满足要求;安全系数是材料的屈服强度极限值与最大应力值的比值,安全系数大于1表明强度符合要求。通过上述分析,最大许用挠度值18 mm大于最大位移值4.8 mm,所以该车架刚度要求得到满足;屈服强度极限值400 MPa大于最大应力值129.15 MPa,安全系数约为3.1,所以该车架强度符合设计要求。
4.2.2. 扭转工况
为了模拟该工况,将左前轮的所有自由度都不约束并置于悬空 [8],表4是该工况各个支撑点的边界条件,图7是求解出来的位移云图结果,图8是求解出来的应力云图结果。由图7可知该车架的最大位移值约为5.0 mm,图中红色区域表示弯曲变形较大的地方,主要集中在中部两根横梁上,还有车架中部的纵梁上;由图8可知该车架的最大应力值为138.72 MPa,最大应力点在右后轮的接触面处。通过上述分析,最大许用挠度值18 mm大于最大位移值5.0 mm,所以该车架刚度要求得到满足;屈服强度极限值400 MPa大于最大应力值138.72 MPa,安全系数约为2.88,所以该车架强度符合设计要求。

Figure 5. Displacement nephogram under bending condition
图5. 弯曲工况位移云图
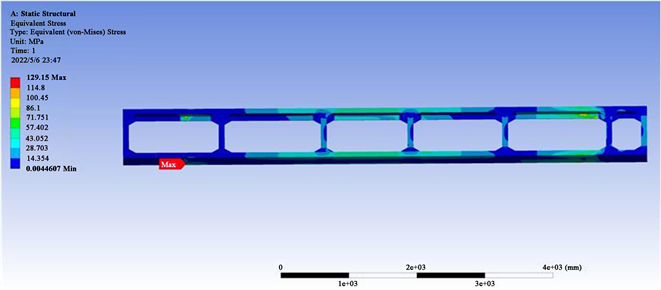
Figure 6. Stress nephogram under bending condition
图6. 弯曲工况应力云图
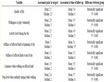
Table 3. Boundary condition of bending condition
表3. 弯曲工况边界条件
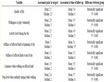
Table 4. Boundary condition of torsion condition
表4. 扭转工况边界条件
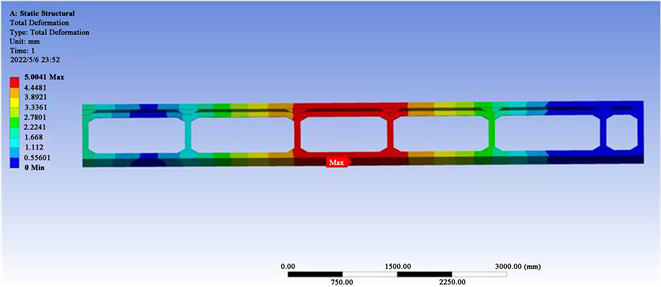
Figure 7. Displacement nephogram under torsional condition
图7. 扭转工况位移云图
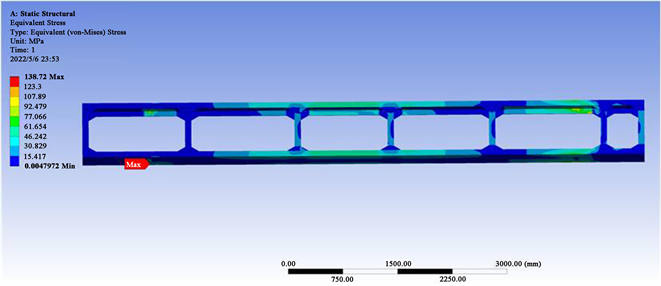
Figure 8. Stress nephogram under torsional condition
图8. 扭转工况应力云图
4.2.3. 紧急制动工况
当汽车在紧急制动的情况下,为了准确模拟该工况,需要在车架施加一个加速度在进行分析 [9],加速度值设为6860 mm/s2,表5是该工况各个支撑点的边界条件,图9是求解出来的位移云图结果,图10是求解出来的应力云图结果。由图9可知该车架的最大位移值约为5.1 mm,图中红色区域表示弯曲变形较大的地方,主要集中在中部两根横梁上,还有车架中部的纵梁上;由图10可知该车架的最大应力值为140.63 MPa,最大应力点在右后轮的接触面处。通过上述分析,最大许用挠度值18 mm大于最大位移值5.1 mm,所以该车架刚度要求得到满足;屈服强度极限值400 MPa大于最大应力值140.63 MPa,安全系数约为2.84,所以该车架强度符合设计要求。
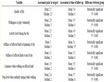
Table 5. Boundary conditions of emergency braking conditions
表5. 紧急制动工况边界条件
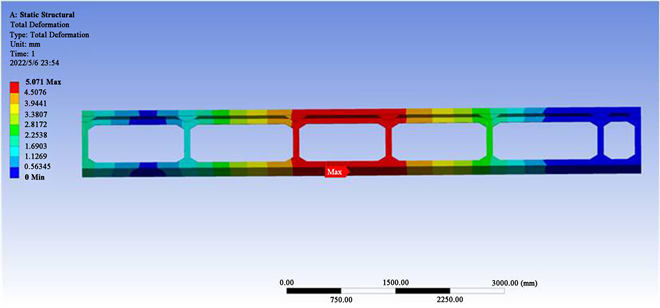
Figure 9. Displacement nephogram under emergency braking condition
图9. 紧急制动工况位移云图
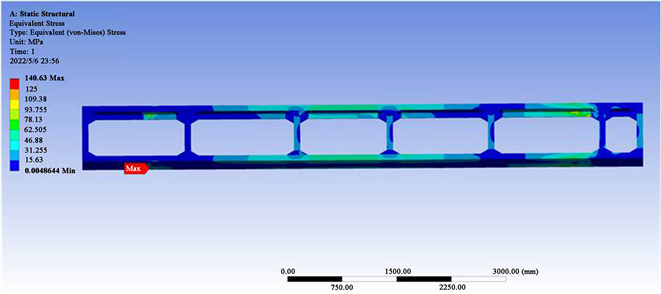
Figure 10. Stress nephogram under emergency braking condition
图10. 紧急制动工况应力云图
5. 模态分析
考虑到货车在行驶过程中可能会发生共振,因此有必要对该车架进行模态分析,本文研究的模态分析是自由模态,与载荷和约束均无关。考虑到前6阶是刚体模态,其固有频率都是0,故将前12阶的固有频率和其对应的振型图都仿真出来进行对比分析 [10]。7~12阶模态振型图如图11所示,7~12阶固有频率如表6所示。
由图11可知7~12阶的振型图和对应的固有频率值,第7阶固有频率值为281.15 Hz,主要受到扭转振动;第8阶固有频率值为627.98 Hz,主要受到弯曲振动;第9阶固有频率值为834.97 Hz,主要受到扭转和摆动的组合振动;第10阶固有频率值为979.81 Hz,主要受到车架前后端的扭转振动;第11阶
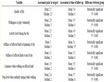
Table 6. 7~12 orders natural frequency
表6. 7~12阶固有频率
固有频率值为1367.9 Hz,主要受到扭转和摆动的组合振动;第12阶固有频率值为1739.3 Hz,主要受到摆动振动;图中对应的变形值并不是真实变形量,因此没有任何的参考意义的。由表6可知,各阶次都对应一个固有频率,第7阶固有频率为281.15 Hz,为7~12阶的固有频率最小值,第12阶固有频率为1739.3 Hz,为7~12阶的固有频率最大值,所以固有频率值随着阶次的增加而越来越大;7~12阶固有频率的范围在281~1740 Hz之间,汽车行驶的一般路面激励多在20 Hz以下,货车怠速情况下发动机的激励频率大约在30 Hz,正常速度行驶传动轴引起的激励频率大约50 Hz,所以固有频率最小值远远大于上述任何一个激励频率,因此该货车车架不会出现共振,即设计合理。
6. 结论
本文通过UG建模,使用有限元分析方法,获得了该货车车架在不同工况下的位移值、应力值和自由模态下的固有频率值与振型图,得到如下结论:
1) 从弯曲、扭转和紧急制动工况下计算结果的位移值和应力值可知,该货车车架的刚度和强度均满足设计要求。从各个工况的位移云图和应力云图可知,车架的薄弱环节在中部两根横梁上以及纵梁的中部上,可以为以后车架的优化改进提供依据。
2) 通过自由模态分析的结果可知,1~6阶为刚体模态,固有频率为0;7~12阶模态的固有频率随着阶次的增加而增加,固有频率的范围在281~1740 Hz之间,均远远超过激励频率,不会发生共振现象,故该货车车架符合设计要求。
3) 通过静力学分析与模态分析,该货车车架结构符合设计要求,为以后的货车车架设计与优化均提供了一定的理论依据。