1. 引言
PIPESIM软件是Schlumberger公司开发的一种集油藏动态优化、单井分析优化、管网设计优化等于一体的工程应用软件,可以对油藏开发到地面处理(包括注水的整个生产系统)进行稳态模拟,是目前油气田开发和生产的公认软件之一,软件内部涵盖了丰富的流体物性包和多种多相流计算方法,极大地提高了计算的准确性和科学性。
本文主要介绍管网模拟分析模块在海外某油田站外集输系统中的应用,以辅助站外集输系统的管径优选 [1] [2]。该油田原油比重大、气油比高,站外集输系统包含单井管线和集输干线,均为两相流输送管线 [3],是一个比较典型的站外集输系统 [4],对其他原油站外集输系统的管径优选具有一定的指导意义。
2. 建立计算模型
油气集输系统的设计优化包含两个层面:一是油气集输管网形态 [5] 优化,即井和井之间、井和站之间的拓扑连接形式 [6] 的对比选择;二是集输管网运行参数优化,比如单井和集输管线管径优选、井口背压校核、进集中处理站的温度计算等。首先需要建立管网模型,然后结合实际情况建立目标函数和相应的约束条件,最后利用PIPESIM软件进行水力计算、热力计算最终确定最佳工艺参数 [7]。
油气集输管网的拓扑形态主要有两种,即星式管网连接形态和树状管网连接形态。对这两种连接形式的选取应从投入成本和集输系统可靠性两个方面进行考虑 [8]。通常来说,星式管网连接形态具有可靠性高,投资大的特点;而树状管网的连接形态具有投资小,可靠性低的特点。结合本区块各单井实际情况采取二级星形管网拓扑布局,拟建联合站1座,计量站3座,由于各油井的产液量和计量站的集液量不均,建站位置偏向产液量、集液量较大的油井或偏向油井密度较大的区域,这些产液量较大的油井和计量站之间的连接管道长度相对缩短,运行损耗降低 [9]。根据设计思路,将所有的单井、单井管线、集输干线搭建在模型中,完成模型的物理连接,如图1所示 [10]。
建立计算模型时 [11],依次定义环境参数、选择水力方程、选择热力方程、设定黑油模型,需输入如表1所示的初始条件,包括流体物性参数,单井管线和集输干线的管径、壁厚、粗糙度、长度,总传热系数,管道埋深处的地温,井口温度、进站压力等数据 [12],其中井口温度和进站压力是整个模拟过程的关键约束条件,计算完成后的井口背压不得低于井口最大允许回压2 MPag,进站温度不得低于最低允许进站温度(本项目要求高于凝点以上5℃) [13]。
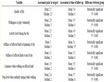
Table 1. Initial conditioning value
表1. 初始条件取值
3. 结果分析及优化
3.1. 管径比选
管径比选通过计算所得的井口背压、管线流速、侵蚀速率比等参数判断所选管径是否合适,其中背压是由管线末端进站压力反推计算得出的,计算公式如下 [14]:
(1)
(2)
其中
为井口背压,
为进站压力,
为管线沿程摩阻损失(mm3/s),
为达西摩擦因子(无量纲),
为管线长度(m),
为管线内径(mm),
为管线流速(m/s),
为重力加速度(m/s2),
为管线输量(m3/s)。
流速一般指气液均相流速,由管径和气液总输量决定,计算公式如下 [14]:
(3)
其中
为管线流速,
和
分别为液体体积输量和气体体积输量(m3/s),A为管线截面积(m2)。两相流管线中的速度须大于3 m/s,以便减少下游分离设备的冲击,这对沿程高差变化较大的长距离输送管道尤为重要。
侵蚀速率比指管线均相流速与侵蚀速率的比值,为有效防止管壁被侵蚀,要求均相流速不能超过计算出的侵蚀流速,即该比值须小于1。侵蚀速率的计算方法如下 [15]:
(4)
其中,
为管线侵蚀流速(ft/s),
为经验常数(无量纲),
为气液均相密度(l b/ft3)。对于不含固体的流体进行保守取值,连续输送时
,间歇输送时
,本项目取
。
1) 单井管线管径比选
以单井FH-K至1号集输站的单井管线为例进行管径比选 [16],该管线全程长1600米,沿线起伏高程差约为9.8米。以井口背压为目标函数,输入2寸~12寸不同的管径尺寸进行比选分析 [17],得到如表2和图2所示的结果。本项目的井口背压不能超过2 MPag,可以看出6寸以上的管径对应的井口背压均小于2 MPag,且侵蚀流速比均满足规范要求,再结合单井管线的最小允许流速(3 m/s),最终选择6寸的单井管线。按此原则依次比选各单井管线的管径 [18]。
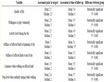
Table 2. Single well pipeline pipe diameter comparison results
表2. 单井管线管径比选结果
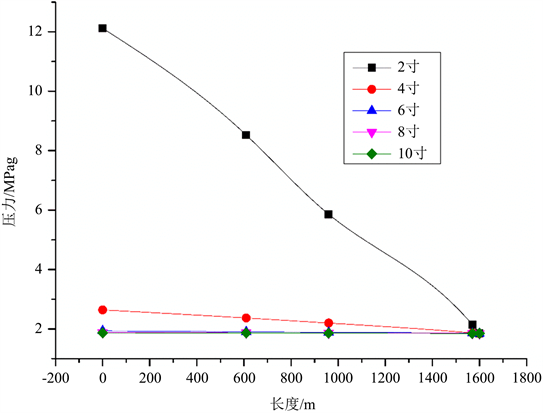
Figure 2. Pressure changes along the line of different single well pipe diameter change
图2. 不同管径单井管线沿线压力变化
2) 集输干线管径比选
以2号集输站至中心处理站的集输干线为例进行管径比选 [19],该管线全程长13,900米,沿线起伏高程差约为8.3米。本项目集输干线一般选用12寸、14寸和16寸三种规格,故只进行12寸、14寸和16寸的比选,其他项目根据项目情况进行比选。初选12寸管径,运行模型后,连进2号集输站的各个井口回压以及集输干线的液体流速、侵蚀速率等运行参数见表3,各单井管线和集输干线的沿程压力变化如图3,可见单井背压均已超井口最大允许回压2 MPag,且集输干线的流速过高。
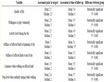
Table 3. Key parameter running results of 12 inch trunkline
表3. 12寸集输干线关键参数运行结果
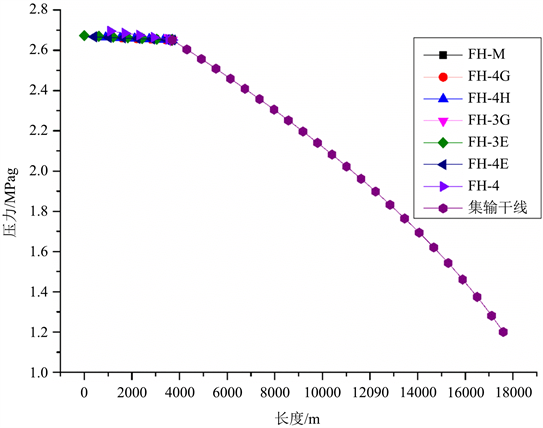
Figure 3. Pressure changes along the line of 12 inch trunkline
图3. 12寸集输干线沿程压力变化
再选14寸管径,运行模型后,连进2号集输站的各个井口回压以及集输干线的液体流速、侵蚀速率等运行参数见表4,各单井管线和集输干线的沿程压力变化如图4,可见单井背压均低于井口最大允许回压2 MPag,且集输干线流速和侵蚀流速等均满足规范要求。
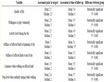
Table 4. Key parameter running results of 14 inch trunkline
表4. 14寸集输干线关键参数运行结果
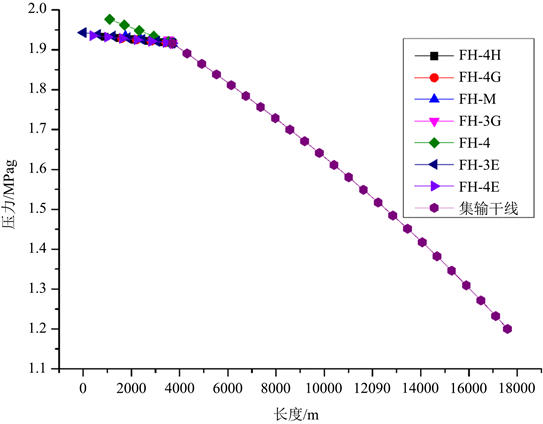
Figure 4. Pressure changes along the line of 14 inch trunkline
图4. 14寸集输干线沿程压力变化
最后选16寸管径,运行模型后,连进2号集输站的各个井口回压以及集输干线的液体流速、侵蚀速率等运行参数见表5,各单井管线和集输干线的沿程压力变化如图5,单井背压虽然均低于井口最大允许回压2 MPag,但背压处于1.5~1.65 MPag区间,且集输干线流速过低,没有充分利用井口能承受的背压,另外管径选取过大,也会增加线管投资等。
通过比较上述单井的井口回压、管线流速和侵蚀流速选择集输干线的管径。选择12寸集输干线时,单井的井口背压超过规定的最高压力2.0 MPag,集输干线的流速过高;选择16寸集输干线时,单井井口背压、集输干线流速过低;选择14寸集输干线时,单井井口背压、集输干线流速均合适;所以2号集输站至中心处理站的集输干线最终选择14寸 [20]。
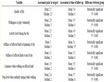
Table 5. Key parameter running results of 16 inch trunkline
表5. 16寸集输干线关键参数运行结果
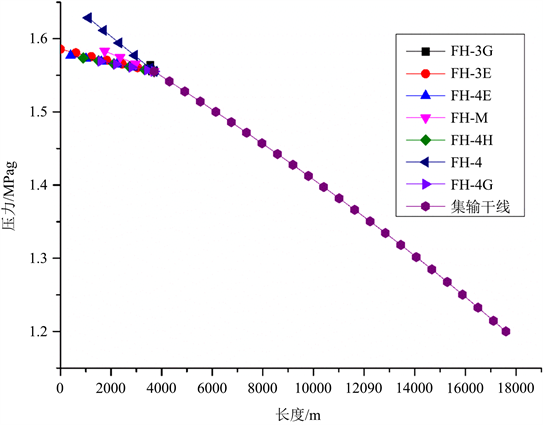
Figure 5. Pressure changes along the line of 16 inch trunkline
图5. 16寸集输干线沿程压力变化
4. 结论
本文主要对海外某油田站外集输系统进行稳态模拟,该油田原油比重大、气油比高,站外集输系统包含单井管线和集输干线,均为两相流输送管线。通过PIPESIM软件完成单井和集输管线管径优选、井口背压校核、进集中处理站的温度计算、水力条件和热力条件敏感性分析等,以辅助站外集输系统的设计优化。模拟发现对集输管网的热力计算影响较大的参数是含水率和季节地温,即含水率为0%的冬季工况是热力计算最严苛的情况,而对集输管网的水力计算影响较大的参数是含水率和气油比,即气油比为1400、含水率为20%的工况是热力计算最严苛的情况。该系统是一个比较典型的站外集输系统,其集输管径的优选,对其他原油站外集输系统的模拟优化具有一定的指导意义,可为油气管道的安全运行提供保障。