1. 引言
随着轨道客车生产技术的快速进步与发展,不锈钢材料在车体制造领域大量使用 [1],301L系列奥氏体不锈钢冷硬板具有良好的耐大气腐蚀性能和成型性、优良的表面质量以及成本低等特点 [2],用于制造车体外墙、边梁、横梁、侧梁、门柱、端柱、侧柱等 [3],成为轨道客车用不锈钢的主流材料。301L系列奥氏体不锈钢冷硬板在制作车体时经过弯曲、冲压等塑性变形后,不再进行表面喷涂工艺,因此对表面质量要求非常严格,整个表面不允许有严重影响观感度的缺陷。
301L系列奥氏体不锈钢冷硬板生产过程表面极易产生振纹缺陷,既影响产品表面质量,也增加轧辊损耗。针对振纹问题,国内外学者做了大量研究工作,如Wu等研究了轧制力波动对振纹缺陷的影响 [4];王庆军等分析了轧辊磨削过程振纹产生原因及控制措施 [5];周家林等研究了单辊驱动四辊冷轧平整机第6阶固有频率的第五倍频颤振以及轧制工艺参数对振纹振动频率的影响与抑制 [6]。目前,研究基本集中在振纹缺陷宏观特征分析以及轧机、平整机等设备发生振动的原因分析,而对振纹缺陷微观特征分析缺乏、不锈钢冷硬板生产过程中振纹缺陷产生流程研究空白,并且由于问题的复杂性,至今对冷硬板的振纹缺陷缺少可行有效的抑制方法。基于此问题,本文对轨道客车用301L不锈钢冷硬板轧制过程中出现的振纹缺陷进行了宏观、微观、频率特征分析,确定了产生流程,明确了产生的直接原因,通过现场工艺改进,有效控制振纹缺陷,最终产品表面质量得到客户认可。
2. 材料生产工艺
轨道客车用301L不锈钢的化学成分见表1所示,其冷轧产品按抗拉强度等级划分为LT、DLT、ST、MT、HT共5个等级 [7],其中MT、HT两项强度等级属于冷硬板产品,主要采用二十辊可逆冷轧机轧制 [8],双轧程生产。
生产工艺流程:热轧原料→热线(退火、酸洗)→二十辊可逆冷轧机(第一轧程轧制)→冷线(脱脂、退火、酸洗)→二十辊可逆冷轧机(第二轧程轧制)→冷线(脱脂、酸洗)→精整→打捆入库。
为了保证性能与板形,第二轧程冷线工序只脱脂不退火,通过控制总变形率来保证性能,MT、HT两项强度等级产品总变形率 £ 25%,总道次一般为1道次,区别与普通产品50%以上变形量的多道次轧制,振纹缺陷产生在MT、HT冷硬板第二轧程轧制过程中。
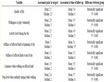
Table 1. Chemical composition of stainless steel 301L for railway vehicle
表1. 轨道客车用301L不锈钢的化学成分
3. 振纹缺陷的特征及原因分析
3.1. 振纹缺陷的宏观特征分析
现场对振纹缺陷的形貌进行分析,具有以下特征:轧件上下表面均有与工作辊轴向平行、间距相等、贯穿钢带宽度方向的明暗相间条纹缺陷,明暗条纹间距为3~5 mm,见图1(a);轧制振纹产生前后,带钢沿轧制方向无明显厚度差;轧制过程中带钢表面一旦产生振纹,更换新工作辊继续轧制无法消除;产生振纹后拔出工作辊,侧光观察可以发现工作辊表面具有与轧件相同特征的振纹缺陷;冷线工序脱脂处理后,轧件表面振纹的形貌特征未发生变化,见图1(b)。
(a)
(b)
Figure 1. Vibration marks defect. (a) Overall morphology of defect on rolling; (b) Overall morphology of defect after degreased
图1. 振纹缺陷。(a) 轧制过程中缺陷总体形貌;(b) 脱脂后缺陷总体形貌
3.2. 振纹缺陷的微观特征分析
利用蔡司EVO 18扫描电子显微镜对振纹缺陷明暗条纹表面形貌进行62、200倍数放大观察,结果见图2所示。由图2观察发现,振纹缺陷暗纹处微观孔洞明显较明纹处多,暗纹处较多的微观孔洞可以对光进行大量吸收使视觉上产生暗纹,明纹处较少的微观孔洞对光吸收较少使视觉上产生明纹。因此,明暗纹区域对光吸收量不同导致人观察时出现了明暗色差缺陷,振纹缺陷明暗相间条纹是带钢表面微观孔洞多少差异的结果。
(a)
(b)
(c)
Figure 2. Microscopic features of bright-dark stripes for vibration marks. (a) Overall morphology of defect (left dark right bright); (b) Microscopic features of dark stripes; (c) Microscopic features of bright stripes
图2. 振纹缺陷明暗纹的微观形貌。(a) 振纹缺陷总体形貌(左暗右明);(b) 振纹缺陷暗纹微观形貌;(c) 振纹缺陷明纹微观形貌
3.3. 振纹缺陷频率特征分析
带钢表面振纹缺陷的间距为3~5 mm,产生振纹时工作辊轧制线速度一般为0.80 m/s,带入公式(1)可以得出振动频率为160~266 Hz,属于第三倍频颤振。
轧机的振动与振纹缺陷特征存在如下关系式:
(1)
式中,ω为振纹纹距,mm;ν为工作辊轧制线速度,m/s;f为振动频率,Hz。
对正常轧制与发生振动的两种状态下轧机轧制速度的时域信号做FFT变换,图3为振动前后轧制速度频谱,如图3(a)所示,正常轧制时峰值频率在110 Hz左右,在100~250 Hz频段存在丰富的随机瞬态振动。如图3(b)所示,振动产生时频谱与正常轧制时频谱图不同,一是振动的频率更加集中,二是振动时频率峰值出现在170~200 Hz。这也证明了该振动振颤频率为170~200 Hz,属于第三倍频颤振。
(a) (b)
Figure 3. Spectrum of speed with normal rolling and vibration marks. (a) Spectrum of speed with normal rolling; (b) Spectrum of speed with vibration marks
图3. 振动前后轧制速度频谱。(a) 正常轧制时轧制速度频谱;(b) 振动时轧制速度频谱
3.4. 振纹缺陷的产生原因分析
二十辊可逆冷轧机轧制301L不锈钢冷硬板产生振纹时,轧机系统瞬间震动强烈,持续1 s左右,该特征正好与第三倍频颤振特点相同,第三倍频颤振以突发性为特征,往往在几秒中内集聚大量能量使振幅迅速发散,并伴有较大噪声。
对比分析振动前后不同速度波动情况,图4为振动产生前后速度波动变化曲线,其中S11为轧制速度(红色波动线),C10为入口带钢速度(蓝色波动线),C90为出口带钢速度(绿色波动线),由图4可知,04:00:00时间之前为正常轧制状态,S11轧制速度波动范围0.885~0.901 m/s,速度关系为C90 > S11 > C10,即轧件出口速度大于轧制速度,轧制速度大于轧件入口速度,轧制变形区前后滑均正常,处于稳态轧制过程。大约04:00:10时S11轧制速度开始大幅波动,波动范围为0.865~0.920 m/s,是正常轧制时S11速度波动幅值的7倍,并且出现了S11与C90速度重合相同的现象,即轧件出口速度与轧机速度值相同,轧制前滑被后滑所取代,轧机工作辊与带钢之间发生打滑现象,此时工作辊与带钢表面都产生初始振纹缺陷。由此可知,轧制打滑造成轧制变形区瞬时失稳,产生振动现象。
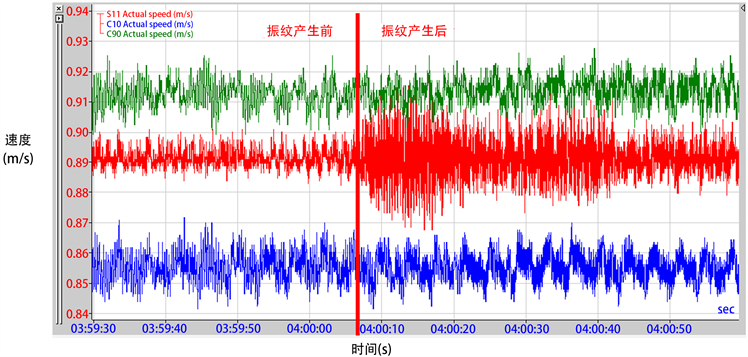
Figure 4. Characters of speed with normal rolling and vibration marks
图4. 振纹缺陷产生前后速度变化特征
为了研究振纹缺陷明暗条纹与轧制变形区(见图5所示)的关系,现对成品厚度4.0 mm的301L冷硬板轧制振纹缺陷与变形区几何尺寸进行分析。
轧制变形区的接触弧长轧制延伸后的长度公式 [9]:
(2)
式中,R为轧辊半径,h1为轧件入口厚度,h2为轧件出口厚度,
为绝对变形量。
现场测试了振纹明暗条纹的间距,见图6所示,振纹间距为4.0 mm左右,并将该钢卷生产过程对应的工艺参数
、
、
、
带入公式(2)计算出
,见表2所示,
为4.002 mm,与实测值基本相同,说明振纹缺陷的一组明暗条纹是轧制过程中工作辊表面的明暗纹通过接触弧长转印到钢带表面形成的。

Figure 5. Diagram of deformation zone in rolling
图5. 轧制变形区示意图
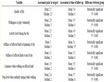
Table 2. Contact arc lengths on rolling interface
表2. 轧制变形区的接触弧长
综上可知,振纹缺陷产生流程是:轧制变形区发生瞬时打滑,打滑时工作辊表面与轧件表面产生初始振纹缺陷,打滑停止后轧机正常轧制,工作辊表面已产生的振纹缺陷在轧制过程中转印到带钢表面,形成明暗相间条纹。因此,轧制打滑是振纹产生的直接原因。
3.5. 轧制打滑的影响因素分析
由轧制打滑因子计算公式(3)知,在相同的润滑工艺与工作辊尺寸的条件下,道次绝对变形量、摩擦系数、前后张力对打滑起着不同程度的影响,其中摩擦系数直接受到轧制速度与工作辊换辊工艺的影响,因此,最终影响打滑的因素是道次绝对变形量、前后张力差、轧制速度、换辊工艺。
(3)
式中,
为打滑因子;
为中性角;f为摩擦系数;Δh为道次绝对变形量;R'为工作辊考虑压扁后的半径;TH为后张力;Th为前张力;P总轧制压力。其中
越接近0.5,越容易出现打滑。
由公式(3)还可看出,在其他因素不变的情况下,道次绝对变形量与打滑因子呈正比关系,即道次绝对变形量越大,打滑越容易发生,越容易产生振纹。实际生产过程中301LHT冷硬板设计总变形率18%左右,采用1道次轧制容易产生打滑振纹,主要原因是道次绝对变形量过大导致打滑产生振纹。301LMT冷硬板设计总变形率8%左右,成品厚度规格 ≥ 4.0 mm的冷硬板采用1道次轧制时也容易产生打滑振纹,主要原因是由于成品厚度厚,其绝对变形量较大,为了保证板形前后张力不能过大,此时仍然是道次绝对变形量对打滑起决定性作用。
轧制后前张力差(
)随着轧制压力的减小对打滑影响增大,进而影响了轧制振纹的产生。实际生产过程中,为了保证板形,301L冷硬板成品道次轧制压力较小,此时轧制前后张力差对轧制打滑振纹的影响较大。
通过对现场实际生产情况的跟踪发现,过快的轧制速度和使用指数加降速模式进行加减速都更容易产生打滑振纹,主要原因是高速轧制时摩擦系数会明显降低,过快的加减速会加大轧制过程的不稳定性,两者都会增大打滑振纹产生。
现场跟踪发现,采用已轧制未重新磨削的旧工作辊生产301L冷硬板也容易产生打滑振纹,主要原因是旧工作辊粗糙度明显降低,只有新工作辊粗糙度的一半,粗糙度降低增大了打滑的概率。
4. 工艺改进及效果
4.1. 工艺改进
根据上述影响轧制振纹缺陷工艺因素的分析,采取规范轧制道次及道次变形率工艺、优化轧制前后张力差、减小轧制速度与规范头尾加减速、完善工作辊换辊工艺四项措施进行改进。
1) 根据不同的强度等级和成品厚度规格,规范301L冷硬板轧制道次与变形率工艺。其中301LHT冷硬板和成品厚度规格 ≥ 4.0 mm的301LMT冷硬板采用两道次轧制,成品厚度规格 < 4.0 mm的301LMT冷硬板采用一道次轧制。采用二道次轧制301LHT冷硬板的首道次变形率 £ 15%,采用两道次轧制301LMT冷硬板的首道次变形率 £ 5%。
2) 一道次轧制的301L冷硬板轧制前后张力差 £ 50 KN;二道次轧制的301L冷硬板第一道次轧制前后张力差100~400 KN,第二道次轧制前后张力差 £ 50 KN。
3) 轧制速度优化为£0.80 m/s,头尾加减速采用“少量多次”方式。
4) 工作辊换辊工艺方面,第一道次必须使用新工作辊,禁止使用旧工作辊或已携带振纹缺陷的工作辊。
4.2. 实施效果
通过对301L冷硬板表面振纹缺陷产生原因分析以及制定实施改善措施,振纹缺陷不合格率由10%降低到0%。
5. 结论
1) 轨道客车用不锈钢冷硬板表面振纹缺陷明暗相间条纹是带钢表面微观孔洞多少差异的结果,振动频率为170~200 Hz左右,属于第三倍频颤振。
2) 轧制变形区发生瞬时打滑,工作辊表面与轧件表面产生初始振纹缺陷,打滑停止后工作辊表面已产生的振纹缺陷在轧制过程中转印到带钢表面,形成明暗相间条纹,轧制打滑是振纹缺陷产生的直接原因。
3) 轧制道次绝对变形量、轧制前后张力差、轧制速度工艺、工作辊换辊工艺是打滑振纹缺陷产生的关键影响因素,通过优化轧制工艺和完善换辊工艺,可以有效抑制打滑,控制振纹缺陷的产生。