1. 前言
铜冶炼生产电解过程中会产生一定量的铜阳极泥,其中的银含量随铜精矿中含银的变化而有所变化,该厂含量为10%~20%。目前,铜阳极泥已经成为贵金属(金、银、铂、钯)以及稀散金属(硒、碲)的主要来源 [1]。铜阳极泥提取金银等贵金属的工艺主要分为火法和湿法 [2]。其中湿法冶炼的主要流程为铜阳极泥经焙烧除硒后低酸分铜,氯化分金,然后氨浸分银,分银后液用水合肼还原得到粗银粉原样的混合溶液,粗银粉原样固液分离后获得含银98%左右的粗银粉。粗银粉经转炉除杂后浇铸成银阳极板,银阳极板电解后得到含银99.99%左右的成品银锭。
本文以冶炼厂稀贵车间为例,选取过滤洗涤干燥机作为粗银粉原样的固液分离设备并进行研究试验。沉银后的粗银粉原样固液分离后获得粗银粉和沉银后液。常规的固液分离手段有离心,过滤等。
使用离心机过滤,生产效率过低、操作环境恶劣;使用板框压滤机过滤,生产效率提高、但操作环境依旧恶劣。为提高生产效率,满足生产需要,大部分企业选用板框压滤机对粗银粉原样进行固液分离但板框压滤机在压滤过程中有氨气逸散至环境中,生产中通过密闭压滤机封闭,依靠压滤机房上部的抽风机将压滤过程中溢出的氨气抽离,送至环集烟气系统。
采用板框压滤机进行固液分离存在以下不足:其一,压滤过程中氨气逸出的瞬时气流量过大,导致操作房内较长一段时间空气中氨气浓度过高,需工人在其中进行岗位操作,工人无法进行操作。其二,沉银反应釜的下部出料口水平高度为1 m,压滤机的进料口水平高度为7.5 m,同时粗银粉与水的亲和度并不高,粗银粉原样由沉银反应釜输送至压滤机过程中出料困难,沉银反应釜至压滤机管道堵塞现象严重,需要经常对出料管进行拆卸清洗,加大了工人的劳动强度。
社会的发展,各行业对环境保护的观念日益增强,采用板框压滤机作为固液分离设备优存在着诸多问题,亟需寻找一种新设备新工艺,替代板框压滤机作为粗银粉原样的固液分离设备。受医药行业药粉密闭过滤方式的启发,现将所获得的粗银粉原样溶液置于密闭容器中,通过多次加压洗涤过滤的方式,使固液分离过程在密闭环境中进行,可以从根源上控制氨气逸散的问题。
2. 工艺原理
氨浸分银的基本原理是基于氨与银离子能形成稳定的
络离子而进入溶液:
分银在室温下进行,氨浓度为8%~10%,按Ag ≤ 30 g/L确定投料量,搅拌4 h,整个反应在容积为20 m3的反应釜中进行。反应完成后,进行固液分离,液体作为银还原工序的原料。
氨浸液用水合肼(联氨)还原,得到品位98%以上的银粉:
[2]
水合肼添加量为理论用量的2倍 [3],常温还原,还原时间30 min,整个反应在反应釜中进行。还原完成后,进行固液分离,反应釜中粗银原样的固体含量约为6%。目前该厂的固液分离方法为板框压滤机压滤,采用板框压滤机进行固液分离,本次试验采用过滤洗涤干燥机作为改进工艺中所选设备,在保证生产效率的同时,尝试解决板框压滤机存在的不足。
某冶炼厂针对沉银后粗银粉原样的固液分离手段进行了改进,固液分离由板框压滤机压滤改进为采用过滤洗涤干燥机分离,固液分离后所获取的产物为粗银粉及沉银后液,98%左右的粗银粉经转炉除杂后浇铸成银阳极板;沉银后液通过回收系统脱氨塔制取氨水后,返回分银系统继续使用。改进前后的工艺流程图如图1所示:
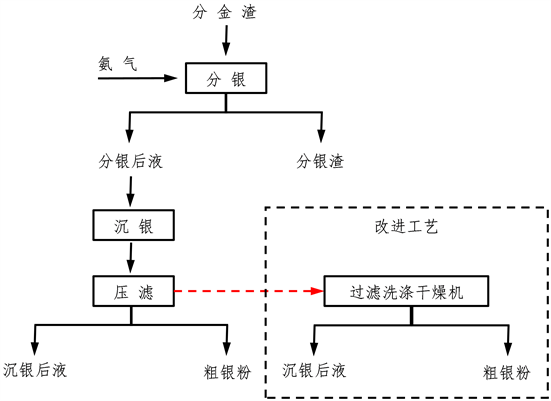
Figure 1. The flow chart of the production process of coarse silver powder in a smelter
图1. 某冶炼厂粗银粉生产工艺流程图
3. 试验过程
3.1. 可行性研究
该厂选用一台容量为20 L的小型过滤洗涤干燥机现场试验,验证可行性。进料方式为负压进料;进料后加水并通过搅拌桨对粗银粉原样进行洗涤;洗涤完成后通过正压进行固液分离;最后从设备夹层通入蒸汽进行干燥处理。以下为详细过程:
1) 粗银粉原样取样分析,确定其化学成分,含水及氨氮含量;过滤洗涤干燥机顶部连接一根黑皮橡胶管(见图2),在负压状态下,粗银粉原样通过橡胶管加入到洗涤干燥机中,每次加料10 kg。
2) 加料完成后向过滤洗涤干燥机中通入清水12 L,搅拌洗涤5分钟后通风将水过滤出,滤液体积基本为12 L。然后再通水搅拌洗涤过滤,共洗涤3次,洗涤过滤过程中对滤液取样检测分析。
3) 过滤完成后,通蒸汽2小时烘干物料。
4) 取出物料并取样送检化验。
5) 对比干燥方式对试验结果影响,取同批次粗银粉原样重复步骤1、2,通空压风45分钟吹干物料,取出物料并取样送检化验。
6) 另取粗银粉原样2批次后分别重复步骤1~5。
将试验过程中产生的样品送样后的化验数据见表1~4。
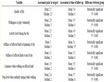
Table 1. Filtration and washing test data of coarse silver powder A
表1. 粗银粉原样A过滤洗涤试验数据
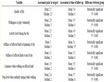
Table 2. Coarse silver powder B filtration and washing test data
表2. 粗银粉原样B过滤洗涤试验数据
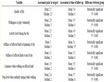
Table 3. Coarse silver powder C filter washing test data
表3. 粗银粉原样C过滤洗涤试验数据
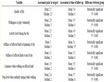
Table 4. The removal rate of ammonia nitrogen after the crude silver powder was filtered and washed as it was
表4. 粗银粉原样过滤洗涤后氨氮去除率
3.2. 结果分析
1) 本轮试验共历时10天,共取了3批次粗银粉原样进行试验,编号粗银粉原样A、B、C,不同粗银粉原样经第一次过滤洗涤后粗银粉原样中氨氮被去除80%左右,三次洗涤完成后,氨氮的去除率基本在90%以上,结果表明经三次洗涤过滤后,粗银粉原样中的氨氮已基本去除。试验前,粗银粉嗅觉检验有明显的氨气味,三次洗涤后,粗银粉中已嗅不到氨气味,与试验数据相符。
2) 过滤后的粗银粉在在后续的银电解过程中,对其产品电银粉的合格率有影响的杂质元素主要是铜、碲、铋、铅和锑 [4] [5],结果表明过滤洗涤过程对粗银粉中经济产物银的含量基本没有影响,但同时对杂质的去除也无明显作用,理论上粗银粉中主要的杂质元素在这种含量下,也基本上不溶于水,与试验现象相符。有少量的银随着每次洗涤到了滤液中。因此洗涤次数不宜过多,过多的洗涤次数会延长作业时间,增加生产成本,降低银的直收率。
3) 在第一组试验时,出现了电机烧毁事件;后第三组试验时又出现了电机停止转动约1小时,后自动恢复正常,期间对搅拌桨的高度进行了调整。经分析认为物料密度过大、重量集中,将搅拌桨压死了。因此在实际生产中,如物料加入量过大、搅拌桨深入物料过深等都可能会导致电机烧毁,故建议设备选型时对电机进行额外的功率加大处理。
4) 表1中的2组试验,均用的厂家提供的滤布,后由于其出现了破损,在表2和表3中的试验均用的本厂生产用的滤布,滤孔比厂家提供的滤布要大。从3个表滤液中的金属含量对比,滤孔的大小对过滤效果有一定的影响,且试验做完拆卸滤布时,可发现滤板上有少量透过滤布的物质。
5) 整个试验过程中,滤布共出现了4次破损,并导致了出液管堵塞。针对滤布破损现象,为了试验顺利进行,将滤布由滤板内圈固定改为了滤板外圈固定,并将搅拌桨最低限位升高至与滤布保持约10 mm的距离,其目的都是使搅拌桨更远离滤布。调整后,有一部分物料无法用搅拌桨刮出来,需要手动出料。结合物料易透过滤布的现象,进行技术论证后,建议在工业生产时,将底部滤板和滤布过滤的形式,改为烧结板过滤的形式。
4. 工业运行
试验完成后,经研究认为其具备工业投产的条件,改造地点为沉银反应釜旁的一块空地,将其下挖4 m后,作为过滤洗涤干燥机的安装地点。
现有生产情况为平均每天出料3反应釜,高峰期4反应釜。反应釜中物料量17 m3,其中正常情况下的固体含量0.7~1.1 m3。拟选择2台DN1600规格的过滤洗涤干燥机,分次安装。其具体参数为:公称过滤面积2 m2、内直径1600 mm、筒体高度1000 mm、公称容积2.79 m3、使用容积2.23 m3、滤饼设计高度300 mm、桨叶提升高度350 mm、滤饼设计体积0.6 m3、搅拌电机功率11 kw、设备净重5159 kg、设备总高4358 mm。
根据前期试验结合现场情况,对过滤洗涤干燥机进行了部分调整:
1) 由于蒸汽干燥存在易结垢的缺点,本工况通风干燥更具优势,因此取消了蒸汽干燥的功能;
2) 考虑到银粉密度大,搅拌桨易压死,将电机功率由11 kw调整为22 kw,搅拌桨极限提升高度由350 mm调整为700 mm;
3) 为更好的搅拌、充分洗涤,以及出料更彻底,搅拌桨由正时针旋转改为带正反转。
4) 过滤装置由滤布改为烧结板,更耐磨损。
5) 进水方式由顶部水管进水改为分3个360˚喷头安装在过滤洗涤干燥机顶部,并将喷头对着过滤洗涤干燥机内壁,在满足银粉洗涤需求的同时,在进水时顺便洗涤内壁,减缓结垢。
5. 结论
本次课题试验完成后,对原设计用于医药行业的过滤洗涤干燥机进行了一系列调整,成功的用在了工业生产中,投产运行三个月后,完全取代了老的压滤机系统。优点及不足如下所示:
1) 现场环境得到了改善,由于过滤洗涤干燥机的工作是在全密闭的环境下进行,从根源上解决了氨气散排的问题。
2) 劳动强度降低。板框压滤机作业,需人工拉板,人工配合铲料,以及工艺设计带来的故障率高,经常需要将反应釜底部的打料泵拆开清理。过滤洗涤干燥机虽然作业时间有所延长,但作业动作基本上全部是按按钮以及开关阀等,劳动强度大大降低。
3) 生产成本降低。沉银后液通过回收系统脱氨塔制取氨水后,返回分银系统继续使用,过滤洗涤干燥机投入使用后,返系统氨水量提高,新投入氨水量降低了20%。
4) 单釜作业时间延长。压滤机单釜作业时间约1小时,过滤洗涤干燥机选型时考虑到现场空间、资金投入结合工艺需求,选型较小,进料时间相对较长,需1小时左右,因此单釜的作业时间延长至2小时。
5) 考虑密闭需要,过滤洗涤干燥机底部排料系统使用绞盘式阀门,阀门开关时需用人工进行开关,作业强度较大,后期待改造成自动开关阀门或开关更方便的阀门。
6. 展望及未来
随着社会的不断发展,全面加强生态环境保护,对工业生产排放的要求日趋严格,过滤洗涤干燥机和老设备相比,在改善现场环境、降低劳动强度、精细化管理方面都具有重要意义。贵金属生产存在体量小 [6]、各厂工艺不统一、保密性要求高等特点,和钢铁冶炼、铝冶炼、铜冶炼等相比,存在交流少、智能化程度低、小作坊式生产普遍等局限性,后续还需借鉴别的行业,引进更多的新设备、新思路和新技术。