1. 引言
高压柱塞泵被广泛应用于石油化工行业,用于介质输送,是典型的往复式接触密封。填料密封是应用最早的密封技术之一,广泛应用在阀门、往复机械、液压气动装置、部分旋转机械及釜等装置中,因为在使用过程中填料与往复或旋转轴直接接触,容易发生磨损,因此填料的摩擦磨损成为影响填料密封可靠性、耐久性和稳定性的主要因素 [1] [2] [3]。在使用过程中因为密封件受力不均匀以及密封环境差导致密封件磨损快,使用寿命短,严重影响了化工行业的连续生产,给工厂带来巨大的不便以及经济损失。因此,研究改善柱塞泵用密封圈润滑性能、密封性能,延长其使用寿命,减少生产中因密封泄漏导致的非计划停车具有重要意义。
2. 往复填料密封的基本原理
V型密封圈往复填料密封结构如图1所示,密封圈被安装在填料函内,由于填料具有弹性,在用填料压盖的压紧后,密封圈会产生径向变形与轴之间会因变形产生接触压力。活塞杆在外力驱动下做往复运动,活塞杆外行程过程中介质腔内的液体会附着在活塞杆表面形成一层液膜,液膜大部分会被密封圈刮离活塞杆表面,但不可避免的会有一层很薄的液膜被随活塞杆进入介质腔外,而活塞杆内行程时又会将外行程带出的液体全部或者部分带回介质腔,当活塞杆内行程可以将外行程带出的液体全部带回时就不会产生泄漏 [4]。
图1(a)中,1——填料函;2——活塞杆;3——支撑环;4——V1密封圈;5——V2密封圈;6——V3密封圈;7——压环;8——填料压盖。图1(b)中,δi——内圈过盈量;δo——外圈过盈量;γ——唇口角度。
在正常状态下,V型密封圈存在一定过盈量,其内径尺寸小于活塞杆直径,外径尺寸大于填料函内径,这样装配后便能产生一定的变形。但由于支撑环的支撑作用,这种变形只发生在V型密封圈唇部的尖端,即使不施加压紧力也能密封一定的压力。当密封压力升高时,唇尖的形状改变会继续加大,接触压力也会随之增大,其密封压力也会随之升高。
(a) 密封结构
(b) V型密封圈截面
Figure 1. Schematic diagram of V-ring seal of plunger pump
图1. 柱塞泵V型填料密封结构示意图
3. 往复过程液膜厚度及泄漏量理论计算
3.1. 几何模型
本节所研究的活塞杆密封如图2所示,其中图2(b)为动密封面液膜分布及接触区域的接触压力p随x的分布曲线示意图。初始过盈条件下密封件产生的初始变形是十分之几毫米,而截面之间的液膜厚度仅为十分之几微米,流体膜所产生的变形对密封面的接触压力影响很小,即密封圈与活塞杆直接接触和中间有一层流体膜,其界面的接触压力应该是相同的。弹性流体动压模型的一个基本假设,就是接触压力的分布规律与界面间流体膜的压力分布规律相同。

Figure 2. Piston seal and dynamic sealing surface liquid film pressure distribution
图2. 活塞杆密封示意图及动密封面液膜压力分布
3.2. 数学模型
为了活塞杆往复过程中内、外行程的液膜厚度,需要通过对动密封面接触区域进行流体力学分析。依据弹性流体动压模型的基本假设:液膜压力与密封面接触压力相同,可以通过逆向求解Reynolds方程得出油膜厚度分布。
本文应用一维Reynolds方程,预测接触区域的液膜厚度:
(1)
式中:p——接触区域液膜压力,MPa;
h——液膜厚度,μm;
U——活塞杆往复速度,m/s;
——密封介质粘度,cP。
因为假定液膜压力与该位置处所对应的接触压力相同,并且通过有限元计算可以得到密封面的接触压力分布,因此p是已知量。则可以根据公式(1)反向求解获得液膜厚度h,即逆向求解Reynolds方程,得到
(2)
式中:
——压力最大点的膜厚度,也是
处的膜厚度。
如图2所示,B为介质压力分布曲线靠近介质侧的拐点,定义
,根据理论计算空气侧膜厚
为:
(3)
因为在最大液膜压力处液膜厚度最薄,假设在该位置处在活塞杆与密封圈之间液膜厚度方向上,液膜厚度呈线性分布,即从活塞杆表面液膜速度U到密封圈表面速度为0。在密封界面之外的空气侧整个液膜全部附着在活塞杆上,其速度与活塞杆运动速度一致均为U。根据质量守恒定律,活塞杆直径为d,活塞杆外行程过程带出液体的体积流量为:
(4)
同理,活塞杆在内行程过程中带回液体量,也取决于接触压力分布曲线在空气侧的拐点处的最大压
力梯度
。内行程带回液体量为:
(5)
如果
小于
时,则在活塞杆每个往复行程中都会产生泄漏量。如果活塞杆行程长度为H,则每个往复产生的泄漏量为:
(6)
从公式(6)中可以看出,想要保持较低的泄漏量或者不泄露,需要使
大于
,也就是说需要保证内行程过程中靠近介质侧的接触压力分布曲线最大斜率大于外行程过程中靠接空气侧的接触压力分布曲线最大斜率。
越大,外行程带出液体量越少,
越小,内行程带回液体能力越强。
4. 有限元计算
4.1. 模型简化
柱塞泵填料密封结构如图1所示。由于所受结构和受力完全轴对称,往复密封在大行程时可以看成稳态,所以可以将其可以简化为静态二维轴对称模型(图3),其中活塞杆与密封圈、填料函与密封圈之间及各密封圈之间和密封圈与支撑环、压环之间均定义为摩擦接触 [5]。
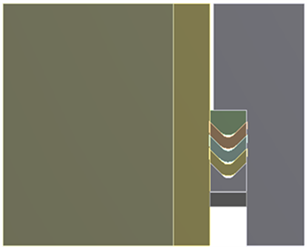
Figure 3. Two-dimensional axisymmetric finite element model of piston rod packing seal
图3. 活塞杆填料密封二维轴对称有限元模型
活塞杆填料密封的各结构参数如下:
活塞杆直径——85 mm;
填料函内径——100 mm;
外过盈量δo——0.1 mm;
内过盈量δi——0.1 mm;
唇口角度γ——0˚。
其中活塞杆、填料函、填料压盖为钢,密封圈材料为聚四氟乙烯(PTFE),PTFE在小应变时可以看作线弹性材料 [6],各材料特性参数见表1。
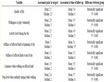
Table 1. Structural parameters of each component
表1. 各组件材料参数
4.2. 网格划分
对有限元模型进行网格划分,并改变网格尺寸对其进行网格无关性检验,最终网格划分如图4所示,网格数量为52,854个。
(a) 总体网格
(b) 密封圈节点坐标编号
Figure 4. Mesh of the model
图4. 模型的网格划分
4.3. 边界条件及加载
根据柱塞泵实际工作过程中活塞杆的工作状态,考虑内行程工况和外行程工况。外行程为介质吸入过程,介质腔内介质压力可以忽略不计,只需在预紧安装状态对活塞杆施加外行程方向位移;内行程工况将介质从腔体中泵出,根据泵的实际参数,介质腔内介质压力为14 MPa,内行程工况需在预紧状态上,首先在密封面上施加14 MPa的流体压力渗透载荷,之后再对活塞杆施加内行程方向的运动。
4.4. 计算结果
根据动密封面的接触压力分布曲线,可以判断其是否可以实现密封状态,并且可以对动密封面的润滑状态以及往复过程中的泄漏量进行理论计算。图5分别为V1、V2、V3密封圈动密封的接触压力分布曲线。各行程中各密封圈接触压力最大值均大于所需要密封的介质压力,可以实现密封。
(a) V1密封圈
(b) V2密封圈
(c) V3密封圈
Figure 5. Contact pressure distribution curve of sealing surface
图5. 密封面接触压力分布曲线
根据其接触压力分布曲线,曲线纵坐标为接触压力的数值,横坐标为对应的节点坐标,在实际模型中任意两节点之间的实际距离均为0.2 mm,可以计算出对应的内、外行程接触压力分布曲线ωB、ωE,其结果如表2所示。
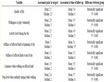
Table 2. The ωB, ωE of contact pressure curve
表2. 接触压力曲线ωB、ωE数值
从表2,可以看出活塞杆在外行程过程中,活塞杆上附着的液体依次通过V1、V2、V3密封圈与活塞杆之间的动密封面。因为ωB2大于ωB1,所以,通过V1密封圈之后剩余的液膜不能完全通过V2密封圈,ωB3小于ωB2,所以,通过V2密封圈之后剩余的液膜可以完全通过V3密封圈被带到空气中。活塞杆外行程带出液体量,只需要计算其通过V2密封圈的液体量即可。
同理,根据表2,活塞杆在内行程过程中,带回液体量取决于通过V3密封圈的液体量。
所以,其在每个往复行程产生的泄漏量为:
根据分析,可以看出导致其产生泄露的主要原因是内行程过程V3密封圈靠近空气侧的接触压力分布曲线ωE数值过大,内行程带回液膜厚度较小。
4.5. 试验验证
为了验证本文中所建立有限元模型的准确性,搭建了如图6所示的试验装置,通过微型拉压力传感器测量指定部位处的填料密封表面的接触压力数值,通过对三组不同结构参数密封圈数值模拟计算的接触压力和试验测量结果进行对比,各组数据误差均小于20%,证明了本文所搭建的有限元模型和采用该模拟方法得到的计算结果可以认为准确。
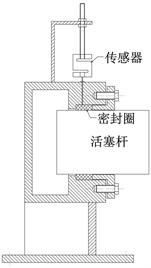
Figure 6. Contact pressure measuring device for the sealing ring
图6. 填料密封接触压力测量实验装置图
5. 结构参数对V型密封圈密封性能的影响
5.1. 外过盈量对V型密封圈密封性能的影响
为了研究V型密封圈外过盈量对密封圈力学性能和密封性能的影响规律。计算了密封圈的动密封面接触压力分布曲线的ωB、ωE,以及往复过程中活塞杆附着液膜厚度及泄漏量具体数值,研究了当V型圈内过盈量为0.1 mm,唇口角度为0˚时,外过盈量分别为0 mm、0.1 mm、0.2 mm时,密封圈的液膜厚度及泄漏量随外过盈量的变化规律。
外过盈量分别变为0 mm时,内、外行程接触压力分布曲线ωB、ωE,其结果如表3所示。
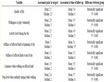
Table 3. The ωB, ωE of contact pressure curve
表3. 接触压力曲线ωB、ωE数值
根据表3,经计算活塞杆外行程带出液体厚度为0.354 μm;活塞杆内行程带回液体厚度为0.347 μm;其在每个往复行程产生的泄漏量为0.00187 ml。
外过盈量分别变为0.2 mm时,根据其接触压力分布曲线可以计算出对应的内、外行程接触压力分布曲线ωB、ωE,其结果如表4所示。
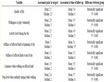
Table 4. The ωB, ωE of contact pressure curve
表4. 接触压力曲线ωB、ωE数值
根据表,经计算活塞杆外行程带出液体厚度为0.232 μm;活塞杆内行程带回液体厚度为0.168 μm;其在每个往复行程产生的泄漏量为0.0171 ml。
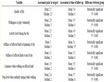
Table 5. Changes of liquid film thickness and leakage with external interference
表5. 液膜厚度及泄漏量随外过盈量变化
从表5可知,本节研究的三组不同外过盈量的密封圈,均无法实现完全密封,在往复过程中均存在一定的泄漏量。活塞杆内、外行程所附着的液膜厚度均随外过盈增大而变薄。对于往复柱塞泵,液膜厚度越薄,往复过程中的活塞杆的润滑效果就越差,反之,液膜厚度越厚,密封的润滑效果也就越好。但当密封介质中含有硬质颗粒时,就需要根据硬质颗粒的直径,选择适宜的外过盈量,保证液膜厚度小于介质中硬质颗粒的直径,以减少颗粒进入导致密封面快速磨损,因为在密封中,磨粒磨损要比摩擦磨损严重的多,较大的外过盈量虽然会加大密封面的摩擦磨损,但是对延长密封的使用寿命是有利的。当密封介质中不含有硬质颗粒时,则需要选择较小的外过盈量,以保证密封圈良好的润滑效果。
5.2. 内过盈量对V型密封圈密封性能的影响
同理研究V型密封圈内过盈量对密封圈力学性能和密封性能的影响规律。使用有限元方法计算了V型圈外过盈量为0.1 mm,唇口角度为0°时内过盈量分别为0 mm、0.1 mm、0.2 mm的密封圈的力学性能和密封性能。
表6为不同内过盈量时往复过程中活塞杆表面附着液膜厚度及泄漏量。
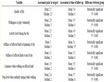
Table 6. Changes of liquid film thickness and leakage with internal interference
表6. 液膜厚度及泄漏量随内过盈量变化
从表6可知,本节研究的三组不同内过盈量的密封圈,均存在一定泄露量无法完全密封,其活塞杆内、外行程所附着的液膜厚度均随内过盈增大而变薄。因此,密封圈内过盈量尺寸的选择与外过盈量相同,需要考虑介质中硬质颗粒的影响。当密封介质中含有硬质颗粒时,应根据颗粒直径选择适宜的内过盈量,防止颗粒进入密封面中。但当密封介质中不含有硬质颗粒时,则选择较小的内过盈量,可以保证密封系统优良的润滑性能。
5.3. 唇口角度对V型密封圈密封性能的影响
为了研究V型密封圈唇口角度对密封性能的影响规律。以往复过程中活塞杆附着液膜厚度及泄漏量为密封性能评价指标,研究了当V型圈内、外过盈量均为0.1 mm,唇口角度分别为为0˚、2˚、4˚时密封圈的力学性能和密封性能。
表7是不同唇口角度时往复过程中活塞杆表面附着液膜厚度及泄漏量。从表中可以看出,外行程过程活塞杆表面附着液膜厚度基本不随唇口角度改变,内行程过程液膜厚度随唇口角度增大而增加,密封圈的密封能力不断增强。
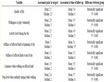
Table 7. Changes of liquid film thickness and leakage amount with lip angle
表7. 液膜厚度及泄漏量随唇口角度的变化
从表7可知,唇口角度增大可以有效增大活塞杆内行程过程中带回液体量,减少密封中的泄漏。对于本例中,当密封圈唇口角度为2˚时就可以实现完全密封。在工程中如果密封有比较严重的泄漏问题,或者由于介质毒性等原因不允许密封发生泄漏时,可以通过增大唇口角度的方式来减少泄漏。可以通过只增大V3密封圈唇口角度即可增大活塞杆带回液体量,同时也不会影响V1、V2密封圈的润滑效果性能。
6. 结论
本文采用有限元方法计算了内、外圈过盈量和唇口角度等结构参数对V型密封圈接触压力分布的影响规律,并通过理论计算得到了不同结果参数对活塞杆表面液膜厚度和往复过程泄漏量的影响规律,得到主要结论如下:
1) V型密封圈内、外过盈量增大其带出、带回的液膜厚度均随着减薄,因此,当密封介质中不含硬质颗粒时,内、外圈过盈量应尽量小以保证密封面良好的润滑效果;当密封介质中含有硬质颗粒,则需要增大内、外圈过盈量,以保证液膜厚度小于硬质颗粒直径,减少硬质颗粒对密封圈的磨损。
2) 唇口角度增大,活塞杆内行程带回液体的能力显著增强,因此,增大唇口角度来减少往复过程中的泄漏量,对于本文计算唇口角度为2˚时即可实现完全密封。
3) 在工程中可以根据不同需求和各结构参数的影响规律对密封圈进行组合使用,增大V3唇口角度,可以增大活塞杆带回液体量减少泄露,又不会影响V1、V2密封圈动密封的润滑效果。对于含有硬质颗粒的介质,只增大V1密封圈的内、外过盈量,阻止颗粒进入第一道密封圈,同时也不会影响V2、V3密封面的接触压力分布。
参考文献