1. 引言
热轧钢带表面出现的质量缺陷类型主要包括氧化铁压入、辊印、划伤、异物压入、夹杂线和翘皮等缺陷,其中翘皮缺陷的数量和尺寸成为影响冷轧产品表面质量的重要影响因素。翘皮类缺陷经过酸洗、冷轧后一般难以消除,尺寸较小时,冷轧产品表面多会形成条状类缺陷,对于表面要求较高的产品,严重影响成品外观质量;尺寸较大时,冷轧产品表面会遭到破坏,严重时甚至会造成断带,严重影响下游客户的生产效率。
翘皮缺陷的形成原因涉及炼钢、连铸、热轧工序,且形貌多样化、呈发生几率高且易于批量爆发的趋势,生产中控制较为困难。王国栋 [1] 等人详细讨论了由氧化铁皮的压入、铸坯中的气泡、铸坯表面或边部开裂、侧压定宽机参数的调整不当以及结晶器卷渣等原因造成的翘皮缺陷的特征。庞启航 [2] 等人研究了IF钢热轧板的翘皮缺陷产生的主要原因是板坯边角部与芯部温差过大,在热轧过程中发生不均匀变形而导致的。刘靖群 [3] 等人对长条片状翘皮缺陷、断续侧翻线状翘皮缺陷和点状边部翘皮缺陷的形成原因进行了分析。
目前,热轧带钢表面质量的稳定性已经成为制约产品质量保证的重要因素,典型性翘皮特征多为沿带钢长度方向开口,呈长条片状,面积较大,一般长宽分别在100 mm、5 mm以上,严重时长度可达500~600 mm,带钢上下表面均有可能存在,无明显钢种特异性;同时在生产中也出现了一些非典型性翘皮的表面缺陷,由于他们的特征与成因具有一定的相似性 [4] [5] [6] [7] [8],根据其形貌特征称之为“马蹄状起皮”。结合本厂生产实践,热轧钢带产品主要以钢卷状态供给冷轧作原料,该类缺陷已经严重影响轧钢合格率,为保证产品质量只能降级处理,影响公司效益和信誉;同时也影响了冷轧产品表面质量,严重影响下游客户使用效果。故针对此类缺陷的形成原因进行分析。
2. 马蹄状起皮缺陷基本情况
经统计,该类马蹄状起皮缺陷出现在Q235B,坯型主要集中在165 * 620 mm,缺陷比例严重时可达到10.01%,严重影响产品表面质量,产品生产的工艺流程为炼钢→连铸→加热→粗轧(5连轧)→精轧(8连轧)→层冷→卷取。
化学成分见表1所示,成分控制符合判定标准。根据缺陷的数量和形貌特征,缺陷的一般规律为头部点状伴随黑色“拖尾”形状,缺陷与基体相连,无明显翘起起皮现象,与轧制方向平行,分布于整个带钢上表面,无明显位置分布规律,边部较中间数量偏多,长度集中在17~128 mm,宽度5~30 mm。经冷轧工序验证,该类缺陷冷轧后在板面形成银白色条状缺陷,断续分布,长度不一,出现位置与热轧带基本对应。具体形貌如图1所示。
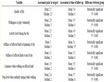
Table 1. Chemical composition (wt%)
表1. 化学成分(wt%)
3. 实验部分
3.1. 研究方法
采用型号AbrasiMet250金相切割机截取马蹄状起皮缺陷的横截面试样,尺寸为5~10 × 2 mm,取样位置如图2所示。依次使用400目→1200目→2000目砂纸研磨后,使用2.5 μm抛光剂进行粗抛,再以1.0 μm抛光剂进行精抛,最终使用清水进行精抛,去除表面残留物质。金相组织采用4%硝酸酒精腐蚀,腐蚀时间10 s,最终采用Axio Imager. A1m金相显微镜观察金相组织,采用EVO-15扫描电镜对缺陷部位的的形貌和微区成分进行分析。
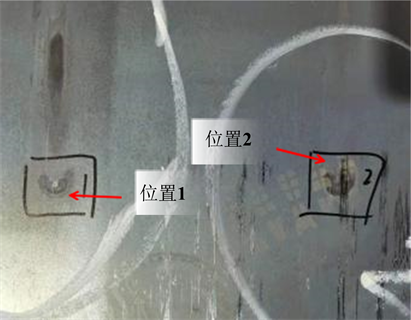
Figure 2. Schematic diagram of sampling location
图2. 取样位置示意图
3.2. 金相检测分析
如图3和图4所示,位置1缺陷深度70.89 μm,位置2缺陷深度81.08 μm,缺陷整体深度均小于0.01 mm,靠近钢带表层位置并具有一定延展性,同时缺陷处存在脱碳及铁素体晶粒粗大现象,基体组织为铁素体 + 珠光体 + 少量贝氏体。
(a) 左,100×
(b) 右,500×
Figure 3. Position 1 metallographic structure of cross section at defect position
图3. 位置1缺陷位置横截面金相组织
(a) 左,100×
(b) 右,500×
Figure 4. Position 2 metallographic structure of cross section at defect position
图4. 位置2缺陷位置横截面金相组织
3.3. 扫描电镜与能谱分析
能谱分检测结果表明,如图5和图6所示,缺陷处仅存在O和Fe元素,未见其他异常元素。分析认为该缺陷并非夹杂物引起,结合金相组织情况,缺陷附近存在晶粒粗大现象,为高温状态下产生。
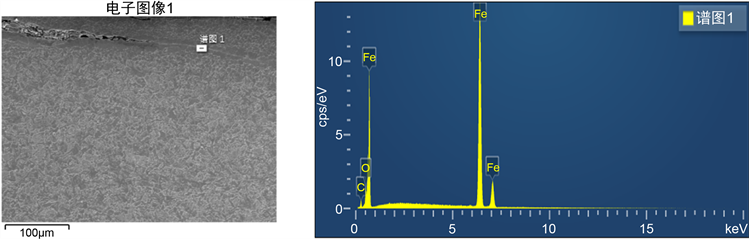
Figure 5. Position 1 energy spectrum analysis result of defect position
图5. 位置1缺陷位置能谱分析结果
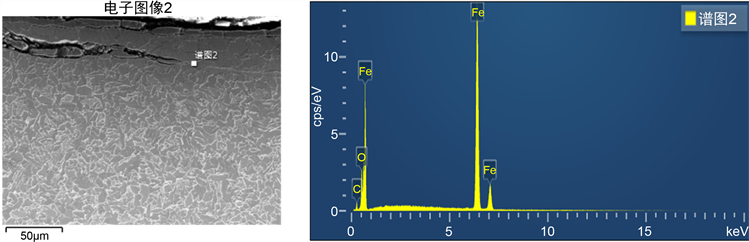
Figure 6. Position 2 energy spectrum analysis result of defect position
图6. 位置2缺陷位置能谱分析结果
经检测,缺陷部位存在O和Fe元素,缺陷内部存在已被氧化,不是由于夹杂物引起的。缺陷附近存在晶粒粗大现象,为高温状态下产生,说明铸坯本身裂纹在后续的轧制中,可造成缺陷扩大产生起皮。
3.4. 加热工艺分析
由表2可见,本批次生产的Q235BL铸坯在炉时间为612 min,存在高温条件下长时间待轧情况。钢坯在高温长时间加热时,极易产生过热现象,钢坯产生过热现象主要表现在钢的组织晶粒过分长大变为粗晶组织,从而降低晶粒间的结合力,降低钢的可塑性。过热板坯轧制时会产生大裂口和剥落;邻近过热的部分出现细裂纹,细裂纹在进一步轧制时会变成结疤。钢的过热温度为1200℃~1350℃之间。有研究表明 [9] [10],在长时间热轧情况下,需将炉温降低至900℃以下。
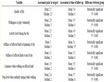
Table 2. The control of heating temperature
表2. 加热温度控制
3.5. 铸坯质量分析
观察炉甩铸坯情况,如图7所示,炉甩铸坯内弧表面良好,横截面有不同程度的中间裂纹、中心线
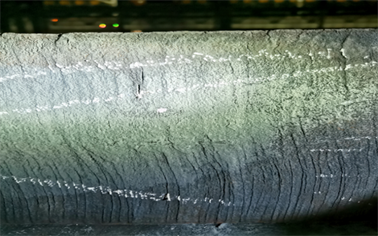
Figure 7. The photo of casting slab cast by furnace
图7. 炉甩铸坯照片
裂纹和三角区裂纹,其中中间裂纹主要位置在铸坯内弧、近表面位置。为确认铸坯皮下裂纹深度和形貌,取炉甩铸坯做低倍样进行检测,取铸坯上表面1 cm厚铸坯进行酸洗,酸洗后可见,如图8所示,内弧侧(铸坯上表面)距离边部30 mm处有1处纵裂;外弧侧(铸坯下表面)边部及中部均有不同程度裂纹。继续对铸坯表面进行处理,使用铣床铣去铸坯表面2 mm后观察缺陷形貌,内弧侧、外弧侧铸坯质量正常,无明显缺陷。因此,铸坯的皮下裂纹位于铸坯表层位置。
4. 结语
通过对条状缺陷样品进行金相组织、微观形貌及成分以及铸坯质量分析,认为该类马蹄状起皮缺陷产生的原因为铸坯皮下裂纹在后续的轧制过程中因轧钢加热工艺的异常导致进一步扩大形成。针对以上原因,可从减少连铸坯皮下裂纹及优化加热工艺控制来进行改善。