1. 引言
油水分离水力旋流器因其处理量大,处理速度快,分离效果好等优点广泛用于众多企业中。旋流器是将流体的直线运动转为强旋转湍流运动,同时湍流结构具有各向异性 [1],旋流器内部油相的迁移运动和分布与结构参数联系紧密。目前,其结构参数单因素影响及其机理研究日趋成熟,且推导出一系列理论和数学模型 [2] [3] [4] [5]。因整体结构因素间存在相互制约与配合关系,上述关系会改变湍流性能,且对旋流器分离性能影响巨大,此类关系目前少有研究报道。旋流器油相浓度分布可充分反映旋流器分离性能,但在试验测定方面存在局限性,然而采用CFD方法可较好地模拟油相分布状况。本文对单锥型水力旋流器结构参数水平安排正交试验,利用RSM模型与两相混合模型结合方法,进行数值模拟,探讨旋流器内部油相浓度的分布状况及影响因素强弱关系 [6] [7] [8]。
2. CFD计算模型建立及初始条件
2.1. 几何模型与试验安排
单锥型水力旋流器主要结构参数为:入口水力直径、溢流口水力直径、柱段直径、柱段长度、锥段长度、底流口水力直径等。固定柱段直径为40 mm,底流口水力直径10 mm。采用双切向入口形式,采用六面体网格提高计算的精度,模型网格见图1所示。
对参数入口水力直径、溢流口水力直径、柱段长度、锥段长度分别安排代号A、B、C、D。因素水平参照单锥水力旋流器结构尺寸,在此之上左右各取一组水平,构成三水平等差数列。按照有交互作用的三水平四因素选取正交表L9(34),即可满足试验要求,其任意两个元素的交互作用为另外两列。因素水平见表1所示,正交试验设计安排见表2所示,(A × B)表示A因素与B因素之间的交互作用,其它同理。
2.2. 初始条件
依据工况条件作为模拟的条件,设定处理量Q = 1.08 m3/h,连续相为水,密度ρ = 998.2 kg/m3,粘度μ = 1.003 mPa·s;分散相为油,密度ρ = 831.4 kg/m3,粘度μ = 8.265 mPa·s。入口的含油分率为10%,将油滴的平均粒径设为40 μm,并且在入口处两相间不存在滑移速度,两个出口均按照充分发展处理。
3. 油相浓度分布分析
在旋流器中,分散相的油滴迁移主要受离心力、向心浮力、流体介质阻力、Magnus力,以及由于径向方向上的速度波动引起的力。由于在流动的过程中,油滴径向沉降速度连续变化,受力均随之变化,油滴从器壁向轴心移动的状态也不一。轴心的油浓度越高,说明油滴向轴心迁移的趋势就越大,同时被分离掉的机率也就越高。利用正交实验表L9(34),本次选取两个指标进行分析,分别为柱段轴心含油浓度与锥段轴心油相浓度。
3.1. 柱段油相浓度分析
柱段是油水分离的预分离部分,其将流体的直线运动转化为旋转运动,在柱段内流体的流动形式非常复杂,能量损耗占有一定的比重。选取每组试验中柱段中间截面含油浓度作参照对比,得浓度分布曲线,试验最高浓度数值列于表3,极差分析列于表4。
根据表4数据,将极差值R按照大小顺序排列,得到如下旋流器结构参数交互作用对柱段轴心含油浓度影响关系强弱排列如式1所示:
式(1)
依据式1,在影响柱段轴心含油浓度单一因素中,锥段长度作用最为明显,而柱段长度作用最小。从交互作用来看,入口水力直径与柱段长度的协同作用起到的效果较大,而溢流口水力直径与锥段长度的协同作用最小(图2)。柱段作为油水预分离部位,以及锥段所分离出油相的返液通道,其油相浓度分布主要依赖于返液油量。对于有着必要能耗损失的旋流设备而言,存在入口与柱段最低的能耗组合,可把较多的能量转嫁给锥段,进一步的提高油滴被分离的几率及油相浓度。

Figure 2. Oil fraction of column section
图2. 柱段含油分率
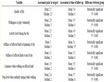
Table 3. Test value of oil concentration in column axis
表3. 柱段轴心含油浓度试验值(v/v %)
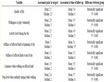
Table 4. Range analysis of oil concentration in column axis
表4. 柱段轴心含油浓度极差分析
根据上述极差分析结果,可确定最优组合为:A3B1C3D2。为了更好地考察各因素与试验指标间的关系,将反映各因素与试验指标间关系的折线图示于图3,可直观反映因素的影响次序及最优水平。
3.2 锥段含油浓度分析
锥段是旋流器的主要分离阶段,该部分的流体的旋转速度增强,油滴在此受到的离心力增大。选取每组试验中锥段中间截面含油浓度作参照对比,得浓度分布曲线,试验最高浓度数值列于表5,极差分析列于表6。
根据表6数据,将极差值按照大小顺序排列,得到如下旋流器结构参数交互作用对锥段轴心含油浓度影响关系强弱如式2所示:
式(2)
依据式2,在影响柱段轴心含油浓度单一因素中,锥段因素作用同样最为明显,依次是入口的水力直径影响,溢流口水力直径影响,同样柱段因素作用仍为最小。从交互作用来看,溢流口水力直径与柱段长度的协同作用起到的效果较大,而入口水力直径与锥段长度的协同作用最小。锥段作为油水分离的
主要阶段,其长度与分离效率和浓度以及能耗成正比,锥段分离出来的油在向溢流口流动过程中,途径

Figure 3. Factor index line chart (column section)
图3. 因素指标折线图(柱段)
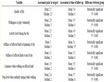
Table 5. Test value of oil concentration in cone section
表5. 锥段含油浓度试验值(v/v %)
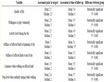
Table 6. Range analysis of oil concentration in column section
表6. 柱段含油浓度极差分析
柱段和溢流段,溢流口越大,溢流含水量则增加,对油芯柱扰动也增加;柱段越长,则油柱越稳定;锥段耗能随着长度增加而上升,则溢流与柱段所获得能量减小,因此溢流口及柱段长度的协同作用对锥段的油浓度较为明显。
根据上述极差分析结果,可确定最优组合为:A3B1C3D2。为了更好地考察各因素与试验指标间的关系,将反映各因素与试验指标间关系的折线图示于图5,可直观反映因素的影响次序及最优水平。
根据极差分析结果,对于柱段与锥段所确定的最优组合为同一组,即为第七组试验,图6所示。第七组形成了均匀的油芯结构,从图4可以看出,在柱段以及锥段前部部分形成了稳定、均匀的油芯柱,说明油滴在锥段前半部分均已分离完成,向溢流口流动,有利于油水分离。
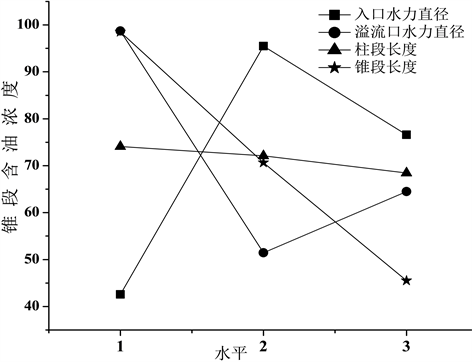
Figure 5. Factor index line chart (cone section)
图5. 因素指标折线图(锥段)

Figure 6. Oil concentration distribution in the Test 7
图6. 试验7含油浓度分布
4. 结论
1) 对柱段与锥段轴心含油浓度而言,其影响因素最优组合同为一组,说明结构参数变化对两者影响趋势相同。
2) 在旋流器柱段区域,结构参数的交互作用对轴心含油浓度影响占主体优势;位于锥段处轴心含油浓度主要受溢流口的水力直径与柱段长度交互作用的影响,柱段长度影响,以及入口水力直径影响的支配。