1. 原材料检验
入厂验收检测
依据DL/T438的规定 [1],电站锅炉管道原材料入厂验收应进行如下检验:
1) 钢管按不同材质规格抽查20%在两端500 mm范围进行超声检测,发现缺陷应扩大检查,并在钢管两侧端部进行表面无损检测,分层缺陷超声检测按BS EN 10246-14执行(0~500 mm区段的分层缺陷按U2级别验收、距焊缝50 mm附近的分层缺陷按U0级别验收),其他类型缺陷超声检测按GB/T5777执行。P92钢管在两端500 mm范围100%进行超声检测,P91钢管在两端500 mm范围按钢管数量抽查30%,发现分层缺陷时扩大检查,检测及验收要求同上。
2) 带纵缝的再热冷段管道,按不同材质规格件数抽查20%,对抽查的管道纵缝按长度的10%进行超声、磁粉检测,必要时进行射线检测,执行NBT47013.3、NBT47013.4、NBT47013.2。
3) 对管件抽查10%进行无损检测,超声检测按DL/T718执行,夹层缺陷按本节第1)条执行,磁粉检测按NBT47013.4执行。
2. 制造质量检验
2.1. 制造厂自检
按照TSG11的要求 [2],锅炉范围内管道及主要连接管道在制造单位应进行检验,可以是制造厂内部自检机构进行检验、也可以由制造厂委托有资质的单位进行检验。管道制造质量无损检测方法有射线、超声、磁粉、渗透等方法,当超声检测采用TOFD检测时,应与脉冲反射法超声检测组合进行,以两者检测结果综合判定,检测标准执行NB/T47013,锅炉范围内管道及主要连接管道的无损检测要求如下:
1) 焊缝射线检测技术等级不低于AB级,焊缝质量等级不低于Ⅱ级;
2) 焊缝超声检测技术等级不低于B级,焊缝质量等级不低于Ⅰ级;
3) 焊缝TOFD检测技术等级不低于B级,焊缝质量等级不低于Ⅱ级;
4) 焊缝磁粉和渗透检测检测时,焊缝质量等级不低于Ⅰ级。
焊缝无损检测应在外观检查合格后进行,检测时机如下:
1) 有延迟裂纹倾向的材料,焊缝无损检测应在焊后24 h后进行;
2) 有再热裂纹倾向的材料,焊缝无损检测应在最终热处理完成后进行磁粉或渗透检测。
管道焊缝检测方法及比例如下:
1) 外径 > 159 mm或壁厚 ≥ 20 mm的管道环焊缝,应进行100%射线或超声检测;
2) 壁厚 < 20 mm的管道环焊缝应采用射线检测,壁厚 ≥ 20 mm时可以进行超声检测;
3) 超声检测时宜采用可记录的超声检测方法,否则应附加20%的局部射线检测。
2.2. 制造质量第三方检验
DL/T612、DL647标准要求对锅炉产品制造质量进行第三方监督检验 [3] [4],该检验是在制造厂已对锅炉产品质量安全性能作出保证的基础之上,由建设单位委托有资质的检验单位对锅炉产品制造质量进一步进行检验,行业内称之为“锅炉制造质量安全性能检验”。该检验不属于法定监督检验,属于委托检验范畴,该检验可以在安装现场管道吊装前进行,也可以前移至制造厂,便于发现缺陷后的及时处理。
DL647对锅炉范围内管道及主要连接管道的第三方监督检验无损检测要求如下:
1) 对管道及管件宏观检查,内外表面不允许有裂纹、腐蚀等缺陷;
2) 对管道制造焊缝宏观检查,按不同规格材质各抽查1条焊缝进行无损检测,根据管道规格参数确定具体无损检测方法。
DL/T438对锅炉范围内管道及主要连接管道的第三方监督检验无损检测要求如下:
1) 对管道及管件宏观检查,焊缝质量符合DL/T869要求,钢管和管件表面质量符合GB/T5310和DL/T695要求;
2) 对组配管道的对接焊缝和管座角焊缝数量的10%进行无损检测抽查,表面检测按NB/T47013.3、NB/T47013.4执行,超声检测按DL/T820执行;
3) 主蒸汽管道和再热热段管道上的堵板采用锻件时,堵板与管道对焊前应对堵板100%超声检测和磁粉检测,对焊后应对焊缝进行100%超声检测和磁粉检测;
4) 对P91/P92制造焊缝按数量的20%抽查,表面检测按NB/T47013.4、NB/T47013.5执行,超声检测按DL/T820执行。必要时可根据缺陷情况采用TOFD方法对可疑小缺陷进行跟踪检查和记录,TOFD检测执行DL/T1317。
2.3. 制造质量监督检验
按照特种设备制造监督管理要求,制造单位应根据不同制造合同批次分别在属地特种设备监督管理部门进行备案,并接受制造监督检验,符合要求的出具监督检验报告和监督检验证书。
按照TSG11的要求,锅炉范围内管道及主要连接管道的制造质量监督检验有关无损检测部分,主要对射线检测底片质量、缺陷评定记录或可记录超声检测记录及缺陷评定进行抽查,至少抽查无损检测数量的20%,包括每种无损检测方法,且包含可疑部位返修部位,一般情况下不进行现场无损检测抽查。
3. 安装质量检验
3.1. 安装单位自检
按照TSG11的要求,安装单位对锅炉范围内管道及主要连接管道的安装质量的无损检测方法、时机、比例和2.1节一致,执行标准为NB/T47013。
安装单位自检时,射线和超声检测都执行电力标准,这就与TSG11的要求不一致。特别是安装单位要接受市场监督管理局进行的安装监督检验,在发现缺陷情况下,标准不一致可能导致缺陷评定结果差异。
3.2. 安装质量第三方检验
一般情况下,安装单位按要求自检,建设单位不会委托第三方进行安装质量检验;但有时候建设单位为了进一步确保安装质量,会委托有资质的第三方检验机构进行抽检,无损检测比例及检测标准按合同约定执行。
3.3. 安装质量监督检验
按照特种设备安装监督管理要求,建设单位应向特种设备监督管理部门报备,并接受安装监督检验,符合要求的出具监督检验报告和监督检验证书。
按照TSG11的要求,锅炉范围内管道及主要连接管道的安装质量无损检测资料的检查和2.3节一致,且需要进行现场无损检测抽查,每种管道至少抽查安装焊缝数量的1%。
电站锅炉施工质量同时受国家能源局监管,按照《火力发电工程质量监督检查大纲》的要求,锅炉水压试验前监督检查要对安装焊缝进行无损检测抽查,表面检测执行NB/T47013,射线和超声检测执行电力标准,但抽查比例未做明确规定。
4. 投运后的检验
4.1. 投运后的金属监督检验
机组投运后的金属监督检验按照DL/T438的要求进行,锅炉范围内管道及主要连接管道的无损检测要求如下:
1) 对于主蒸汽、热段管道等P91/P92类管道,首次A修或B修,对焊缝进行无损检测,重点关注制造和安装检测质量相对较差、有过返修的焊缝,抽查数量不低于10%;
2) 对于累计运行时间 ≥ 10万h的主蒸汽管道和再热热段管道,弯管为非中频弯制的应予以更换,不具备更换条件时应加强监督,对其外弧面进行磁粉检测和中性面内壁进行超声检测;
3) 对于低合金耐热钢及碳钢管道,首次A修或B修,对焊缝进行无损检测,重点关注制造和安装检测质量相对较差、有过返修的焊缝,抽查数量不低于10%;
4) 对于再热冷段管道,首次A修或B修,对制造和安装检测质量相对较差、有过返修的管件和焊缝进行无损检测,对焊缝按管道根数抽查20%,对抽查的焊缝按其长度的10%进行无损检测;
5) 与管道相联的小口径管,每次A修或B修对其管座角焊缝抽查不低于20%的比例进行宏观检查和表面检测,至少5个,至10万h完成100%检测,10万h后重点检查前期发现缺陷的管座角焊缝;
6) 对于弯头/弯管、阀门、三通、异径管等管件,每次A修或B修对其抽查数量不低于10%,对弯头/弯管外弧侧,阀门、三通、异径管外表面进行磁粉检测;
7) 后续A修或B修,无损检测抽查部位为之前未检测部位,在3至4次A修周期内完成全部主管道管件和焊缝的无损检测。表面检测执行NB/T47013.4、NB/T47013.5执行,超声检测执行DL/T820。
4.2. 投运后的定期检验
按照TSG11的要求,投运后的锅炉应进行定期检验,定期检验是对在用锅炉当前安全状况是否满足要求而进行的符合性抽查,包括运行状态下的外部检验、停机状态下的内部检验和水压试验。电站锅炉外部检验每年进行一次;电站锅炉内部检验一般每3至6年进行一次,可结合锅炉检修进行,首次内部检验在投运一年后进行。锅炉内部检验中,锅炉范围内管道及主要连接管道有关无损检测的要求如下,执行NB/T47013:
1) 对安全阀管座及疏水排气取样等管座角焊缝进行表面无损检测抽查;
2) 对主蒸汽、热段管道对接焊缝按20%进行超声和表面无损检测抽查,对弯头/弯管外弧面按20%进行表面无损检测抽查,且各不少于1个;
3) 对主给水管道、再热冷段管道及蒸汽主要连接管道对接焊缝按10%进行超声和表面无损检测抽查,对弯头/弯管外弧面按10%进行表面无损检测抽查,且各不少于1个。
5. P91/P92钢焊缝常见缺陷及无损检测
5.1. P91/P92钢焊缝常见缺陷
超(超)临界电站锅炉苛刻的蒸汽参数对于P91/P92钢的高温力学性能和抗氧化特性提出了更高的要求。为了更好地保障该类材料的后续服役安全,对其焊接接头质量问题如何进行检测和缺陷如何处理显得尤其重要。
P91/P92钢在国内常用的焊接方法有钨极氩弧焊、焊条电弧焊和埋弧焊。这三种焊接方法虽然不同,但是一般均遵循控制热输入的原则,即应用小线能量、薄焊层、多层多道焊技术来焊接。由于这类钢是高铬合金,所以管道焊接根层应采取内壁充氩等防氧化措施。P91与P92钢的焊接工艺非常接近,这与两者的基本性能相近有关。但实际操作中还是要注意焊接工艺虽然相近但并不相同,不能互换。特别是层间温度必须注意,实践表明P92钢焊接过程中对层间温度的敏感性要高于P91钢,当层间温度在300℃之上时,层间出现裂纹的可能性就会增大。P91/P92钢焊工厂化预制焊接缺陷出现的概率情况见表1、表2。
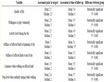
Table 1. Common defects and probability of P91 weld
表1. P91焊缝常见缺陷及概率
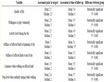
Table 2. Common defects and probability of P92 weld
表2. P92焊缝常见缺陷及概率
P91/P92钢焊缝在制造、安装和使用阶段经实际检测发现缺陷的概率比较见表3。
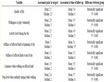
Table 3. Probability of defects in each link of P91 / P92 weld
表3. P91/P92焊缝各环节缺陷出现的几率
5.2. P91/P92钢焊缝缺陷产生的原因
夹渣、气孔:可能产生的原因是现场焊接工艺执行不严,具体表现为焊条烘干不足、焊接过程中层间温度控制不精确 [5]。安装期间存在赶工期及雨季等状况,也是造成以上缺陷遗存的一个原因。
未熔合:可能产生的原因是焊接时电流过小或焊速太快,因热量不够使母材坡口或先焊的焊缝金属未得到充分熔化;或选用的电流过大,使后半根焊条发红而造成熔化太快,在母材边缘还没有达到熔化时焊条的熔化金属已覆盖上去;或焊件散热速度太快,起焊处温度低;母材坡口或前一层焊缝金属表面有锈或脏物。
冷裂纹:可能产生的原因是焊材选择不当或未进行有效烘干、未对焊件进行预热或预热温度低于规定值、焊后热处理方式选择不当 [6]。
热裂纹:可能产生的原因是热裂纹的产生于焊接工艺有关,预热与焊道间温度过低,由于管道壁厚大,一般焊接处的温度要低于热电偶的温度,导致部分焊接过程中实际层间温度低于标准要求;部分焊道熄弧处弧坑未填满,导致在焊道熄弧处产生裂纹;层间清理不干净,夹杂物与焊缝金属结合紧密,将增大焊道金属熄弧处热裂纹倾向 [7]。
IV型开裂:可能产生的原因是P92钢焊接时其热影响区中承受温度在Ac1~Ac3之间的不完全正火区的金属会发生部分奥氏体化。处于这些温度区间的金属的沉淀强化相不能完全溶解,在随后的热处理中未溶解的沉淀相发生粗化,从而造成这一区域材料的强度降低,形成软化区。情况恶劣时在软化区会出现IV型裂纹,降低蠕变强度 [8]。
5.3. 无损检测方法的选择
1) 表面缺陷检测:对于P91/P92钢管道焊缝表面优先选用磁粉检测,与此类钢产生的裂纹特性有关,一般是微小裂纹;推荐使用反差增强剂,使用规范更利于观察细小裂纹类缺陷;优先选用220 V交流电磁轭进行磁化(避开便携式电源的缺点)。
2) 内部缺陷检测:
难点:外在结构原因(弯头、三通、变径、削薄等);内在结构原因(内倒角、内错口、内咬边等);缺陷类型原因(面积型缺陷、细小裂纹等);结构变形波的识别。
检测方法:射线检测(可记录);脉冲反射法超声检测(经验性);TOFD检测(可记录,缺陷测高优势);超声相控阵检测(可记录,效率高)。
每种检测方法都具有优缺点,应根据实际情况选择最佳的检测方法或组合方法。
6. 缺陷处理
按照TSG11的要求,对于检验发现的缺陷,使用单位应当按照合于使用的原则进行处理,合于使用的原则见表4。
1) 对缺陷进行分析,明确缺陷性质,缺陷位置及对锅炉安全经济运行的危害程度,以确定是否需要对缺陷进行消除;
2) 对于重大缺陷处理,使用单位应当采用安全评定或者论证等方式确定缺陷处理方式。
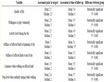
Table 4. Principle of defect treatment for use
表4. 缺陷处理合于使用的原则
7. 分析讨论
根据TSG11的规定,锅炉部件在制造、安装阶段,制造厂和安装单位进行的无损检测都应执行NB/T47013标准;在安装阶段,电站锅炉安装质量同时受到国家能源局的监管,按要求其射线与超声检测应执行相应的电力标准。
采用不同标准可能对检验结果带来差异,例如超声检测采用不同标准情况下使用的对比试块人工反射体尺寸不一致,两者存在一定差异,且两者灵敏度差异不能简单通过理论计算获得,实际对比与理论值存在较大差异 [9]。因此在发现缺陷时,如采用不同标准时检测结果存在差异,为保障设备安全,评定结果应以质量等级差的为准。
制造质量的第三方检验,DL/T438标准比DL647规定更具体化。按照DL/T438要求,制造质量的第三方检验,超声和射线检测执行DL/T820、DL/T821标准,表面检测执行NB/T47013标准。
TSG11属于特种设备安全技术规范,原则上其等级要高于电力行业标准,但国家能源局同样对电力建设行使质量监督检查的权力,因此两者并不矛盾,均应按其要求进行相关检验。因此,安装单位为了同时接受双方监督检验,射线和超声检测往往会按不同标准分别出具检测报告。
投运后金属监督检验,TSG11对其无损检测执行标准无规定,一般按照电力标准进行检测;投运后的锅炉定期检验(内部检验)中的无损检测按照NB/T47013标准执行。
8. 结论
制造阶段,锅炉范围内管道制造质量,制造厂自检和制造质量第三方检验分别采用NB/T47013标准和DL/T电力标准,第三方检验内容DL/T438标准比DL647规定更具体化。
安装阶段,锅炉范围内管道焊缝的无损检测应按照TSG11的规定,应执行NB/T47013标准;电站锅炉安装质量同时受到国家能源局的监管,按要求其射线与超声检测应执行相应的电力标准。两者并不矛盾,均应按其要求进行相关检测,并分别出具检测报告。
投运阶段,管道金属监督检验按照电力行业标准进行无损检测,锅炉定期检验中管道的无损检测按照NB/T47013标准执行。
采用不同标准对检测结果造成差异带来争议时,应对缺陷从严评定;对于P91、P92类高温高压蒸汽管道,焊缝内部缺陷应采用超声相控阵等先进无损检测技术,尽可能明确缺陷性质,对缺陷的处理应采用合于使用的原则,给出合理的处理方案。