1. 引言
边裂缺陷指板带边缘沿长度方向的单侧或两侧出现破裂呈裂口状 [1],包括热卷原料边部开裂,或者经冷轧轧制后边裂,两者均对下游客户使用效果产生不良影响,包括损伤辊面、影响成材率和使用性能等,严重时甚至断带。冷轧边裂缺陷是严重制约卷板中冷轧基料用途产品的重要因素,降低因冷轧边裂导致的降级率迫在眉睫。
前人已对板带冷轧后边裂进行了研究。王健 [2] 等人通过对SPHC冷轧板带出现边裂的研究发现,板带边部晶粒较粗大,且存在三次渗碳体是造成边裂的主要原因。宋进英 [3] 等人研究了夹杂物引起的边裂,钢板边部脱碳严重引起的边裂,横向冷却不均匀引起的边裂和聚集的气泡引起的边裂。李波涛 [4] 研究了SPHC钢板卷边裂原因,分析认为铸坯的加热不当造成铸坯过热、过烧,使边部晶粒异常长大,并且局部晶界产生缩孔是导致边裂的主要原因。
近期,下游客户反馈Q195冷轧基料用途卷板,经冷轧后存在边裂现象。本文对冷轧缺陷边裂的产生原因进行了分析,通过开展精轧工序的优化试验,在一定程度上减少了冷轧后出现边裂的现象。
2. 冷轧边裂缺陷基本情况
经统计,该类冷轧后边裂缺陷出现在Q195,坯型主要集中在200 * 940 mm和200 * 1020 mm,客户采取裁边后(裁边宽度为7~10 mm左右)进行冷轧加工工艺,采用单机架生产模式由原料厚度3.0 mm经6道次轧制到0.18~0.39 mm,变形比为89%~94%。严重时客户降级率可达到7%,严重影响客户使用效果。产品生产的工艺流程为炼钢→连铸→加热→粗轧→精轧(7连轧)→层冷→卷取。
化学成分见表1所示,成分控制符合判定标准。冷轧边裂缺陷分布的一般规律为边裂分布位置在冷轧成品卷芯60 mm,单侧出现占比65%,且操作侧频率高于传动侧,少量双侧均会出现,裂口深度1.5~2 mm,严重时达到3 mm。结合客户生产工艺,对应热轧卷板位置为尾部40~50 m范围内。具体形貌如图1所示。
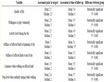
Table 1. Chemical composition (wt%)
表1. 化学成分(wt%)
3. 实验部分
3.1. 研究方法
采用型号AbrasiMet250金相切割机截取距离钢带边部90 mm范围内横截面试样,每个位置尺寸为30 * 8 mm,取样位置如图2所示。依次使用400目→1200目→2000目砂纸研磨后,使用2.5 μm抛光剂进行粗抛,再以1.0 μm抛光剂进行精抛,最终使用清水进行精抛,去除表面残留物质。金相组织采用4%硝酸酒精腐蚀,腐蚀时间10 s,最终采用Axio Imager. A1m金相显微镜观察金相组织。

Figure 2. Schematic diagram of sampling location
图2. 取样位置示意图
3.2. 金相检测分析
如图3和图4所示,操作侧距离边部15 mm范围内为全厚度混晶组织,晶粒均匀性较差;传动侧距离边部10 mm范围内为全厚度混晶组织,晶粒均匀性较差。
(a) 左,距边部5 mm,200×
(b) 中,距边部10 mm,200×
(c) 右,距边部15 mm,200×
Figure 3. Metallographic structure of operation side
图3. 操作侧边部金相组织
(a) 左,距边部5 mm,200×
(b) 中,距边部10 mm,200×
(c) 右,距边部15 mm,200×
Figure 4. Metallographic structure of transmission side
图4. 传动侧边部金相组织
3.3. 边部粗晶及混晶形成原因
精轧过程冷却水种类主要包括机架间冷却水、防剥落水、逆喷水等,通过现场调查发现,Q195系列冷轧基料生产控制模式中机架间水投入自动模式(一般数量为F1~F3),且F1和F2机架间冷却水量较大,边部接触水量较多,冷却速度较快。钢带尾部F1抛钢后,防剥落水未及时关闭,防剥落水冲浇钢带尾部,导致钢带尾部冷却速度较快。
高温带钢边部位置属于二维传热,边部热损失较主体位置快,因而导致带钢边部及近边部表层的相变先于中间部分发生,带钢在两相区(α + γ)终轧时,奥氏体和已转变的部分铁素体会同时变形。变形后的奥氏体在随后的冷却转变中,由于再结晶和相变使得变形潜能得到消除或部分消除;而变形后的铁素体,由于其变形潜能无法通过相变或再结晶消除而留在组织中。这些变形潜能以畸变能或亚结构等形式存在于铁素体之中,相当于带钢表面(带钢表面由于温度较低而处于铁素体状态)留有一定的冷加工硬化,在后续冷却的过程中,容易发生晶粒粗化及边部混晶现象。经理论数据查询,Q195低碳钢两相区温度为800℃~875℃,对应现有终轧温度880℃,结合现场实际温度测量,F1~F3精轧阶段温降对边部粗晶形成有较大影响。
4. 改善措施
4.1. 减少机架间冷却水使用试验
试验钢种:Q195,试验规格:3.0 * 927 mm,通过调整轧制速度及精轧入口温度≤1040℃,终轧温度设定900℃,轧制过程投入F1机架间冷却水,防剥落水F1~F3,逆喷水F6、F7,同时机架间冷却水边部水嘴进行封堵,封堵数量为8个。
金相检测结果如表2所示:钢带尾部6 m取样位置边部粗晶范围≤ 50 mm,操作侧全厚度方向混晶16 mm;传动侧无全厚度方向混晶,边部粗晶范围控制较前期有明显改善;钢带尾部24 m取样位置边部粗晶范围< 25 mm,操作侧及传动侧均无全厚度方向混晶现象。
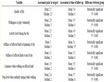
Table 2. The metallographic structure of the edges of reducing the use of cooling water between racks
表2. 减少机架间冷却水使用试验方案边部金相组织检测情况
4.2. 关闭防剥落水使用试验
试验钢种:Q195,试验规格:3.0 * 1010 mm,针对F1抛钢后,防剥落水冲浇尾部现象,进行关闭F1~F3防剥落水试验,与开启F1~F3防剥落水进行比对。
金相检测结果如表3所示:钢带尾部6 m取样位置边部粗晶范围≤ 30 mm,粗晶范围进一步缩小,操作侧及传动侧均无全厚度方向混晶现象。
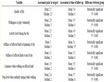
Table 3. Metallographic structure of closing the anti stripping water
表3. 关闭防剥落水边部组织检测情况
5. 结语
以上试验结果表明,通过减少机架间冷却水使用,钢带尾部6 m处边部粗晶范围可缩减至50 mm范围内,全厚度混晶范围≤ 16 mm,钢带尾部24 m处全厚度混晶现象。在此基础上,关闭F1~F3防剥落水试验,钢带尾部6 m处边部粗晶范围可缩减至30 mm范围内,无全厚度混晶现象,有效改善冷轧后边裂缺陷。
以上两种方案试验卷,经冷轧试用后,冷轧边裂现象得到明显改善,0.20~0.25 mm厚度:改善前降级边缘(1~1.5 mm)占比15.38%,达到降级标准占比7.69%;改善料降级边缘占比7.59%,较之前下降7.79%,达降级标准1.27%,较之前下降6.42%。