1. 引言
在全社会以降低碳排放,减少对石油能源的依赖,进而实现绿色可持续发展为目标的背景下,新能源汽车凭其环保节能、电动化等特点迎来了发展的黄金期 [1] [2]。作为新能源汽车动力来源的锂离子电池包,其品质的优劣关系着新能源汽车的大规模应用,而电池充放电过程所产生的热问题是决定整车在续航安全以及寿命等方面的关键因素 [3] [4] [5]。因此需要对电池的热管理系统进行设计与优化,进而使得锂动力电池处在一个合适的运行温度范围尤为重要 [6]。
现阶段,相关研究学者主要聚焦于电池热管理系统冷板材料的选取,冷板结构的设计与优化以及冷却介质热物性的研究,以充分挖掘外部硬件在电池冷却过程中的潜力 [7]。风冷的冷却方式因技术较为成熟,也是目前部分热管理系统所采用的一种冷却手段 [8]。Zhou [9] 等提出了一种基于空气分配管以适用于圆柱形锂电池模组的新型风冷策略,通过在不同放电倍率下改变入口压力、分配管尺寸等参数展开实验研究,结果表明:分配管的孔径和行数的增加有利于降低电池最高温度以及提高温度均匀性。Zhang [10] 等提出了一种基于平行空冷模型结构中添加扰流板以增强冷却效果的策略,研究了扰流器的数量和角度对电池散热的影响。结果表明:适当调整扰流板的角度以及高度对冷却性能有显著的提高。相比风冷,液冷可以通过控制冷却液流量、入口温度等参数以实现对动力电池温度更精确的控制。Wang [11] 等使用水冷铜管对方形电池组进行冷却实验并分析了其表面的温度分布,发现当单体电池生热功率低于10 W时,此方案能将电池表面温度维持在40℃以下。Huo [12] 等设计了一款微通道电池液冷板,通过控制微通道数量、流向以及入口流量等参数研究电池冷却以及温度分布情况。结果表明:通道数以及流量的增加可以降低电池最高温度及提升温度均一性,但流量过大增加了系统能耗同时冷却效果提升不明显。Gao [13] 等设计了一种表面附有柔性石墨的铝制平管的电池液冷散热结构,对电池的温度变化速率以及均匀性等参数进行了研究,发现柔性石墨的应用明显提高了电池组的温度均匀性。此外,利用相变材料对电池进行冷却的技术有着冷却速率快、效率高的特点。张国庆 [14] 使用石蜡/石墨相变复合材料对电池模组进行了散热试验,实验发现使用相变材料的热管理系统的冷却效果要优于风冷以及液冷。由于电动汽车电池热管理系统相变材料多采用石蜡,受限于成本以及系统可靠性等因素,相变材料热管理系统尚未规模应用 [15]。
综上所述,虽各种冷却方式的电池热管理系统已被开发与应用在电动汽车上,但动力电池热管理系统仍需要不断优化以助力电池适应更复杂的温度工况。本文以容量为10 Ah的方形电池包为研究对象,设计了流道结构不同的两种液冷板,通过模型的建立及冷板在冷却液不同入口流量下电池被冷却效果的仿真,研究电池的温度场的最大值与最大温差及液冷板能耗等相关参数,以此为依据进而对液冷板开展优化。
2. 锂电池生热理论与模型计算
2.1. 锂电池充放电原理
锂电池的特点在于其单位体积容量大且循环寿命长,是目前新能源汽车动力来源的主要选择。其充电时锂离子从正极脱嵌,经电解质游离通过隔膜嵌入至负极,同时电子经外部电路到达负极。电池的充放电过程由下式所示。
正极反应式:
(1)
负极反应式:
(2)
总反应式:
(3)
锂电池放电过程与充电过程相反,锂离子从电池负极脱嵌,经隔膜与电解液重新镶嵌到正极,电子从外电路到达正极。式中M表示正极的金属元素,例如Ni,Mn和Co等。
2.2. 锂电池热物性参数
本文选用容量为10 Ah的方形软电池包作为研究对象,考虑到动力电池包的密封性,将电池与冷板之间的热传导作为电池与外界换热的唯一方式进行简化。因动力电池在工作中生热速率会随着其功率输出的不同而动态变化,故可将电池的传热模型视为存在动态变化的内热源的非稳态导热过程 [16],由于电池内部的各种材料物性以及堆叠方式不同,其导热系数也呈现出方向性,故其在x、y、z三个方向上的导热系数λx、λy与λz以及导热微分方程分别如下所示。
(4)
其中,q代表电池生热的内热源项,W/m3;
(5)
(6)
式中,Li与λi分别为电池的第i层材料的厚度与导热系数,m,W/(m·K);L为沿x方向上总长度,m。通过计算得到电池在xyz方向上的导热系数分别为2.31 W/(m·K),4.73 W/(m·K)与4.73 W/(m·K)。
(7)
电池的平均密度ρ由电池包质量m与其体积Vb比得到,由式(7)所示,经计算ρ = 2138 kg/m3。
电池的等效比热容c通过电池内部各材料质量进行加权计算得到,如式(8)所示。
(8)
式中:ci为电池的第i种材料的比热容,J/(kg·K);mi为第i种材料的质量,kg。经计算c = 1158 J/(kg·K)。
因此,结合被测锂电池性质,虽电池单体在一致性上存在一些差别,但仍可对相关热物性参数进行计算。电池材料相关热物性参数如表1所示。
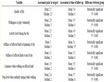
Table 1. Thermophysical parameters of the lithium battery materials
表1. 锂电池各材料热物性参数
本文所研究的单体锂电池在xyz方向上的尺寸分别为:13.5 mm × 65 mm × 132 mm。示意图如图1所示。
2.3. 锂电池生热速率的确定
由式(11)所示,电池生热速率与温度及其总内阻相关。对于锂电池而言,其内阻阻值Rt与电池荷电状态soc与其自身温度T相关 [17],故需确定关于电池内阻的表达式。基于文献 [18] 对方形电池包的研究,其放电时电池总内阻与温度以及soc的关系如式(12)所示。
(9)
式中,Rt为电池总电阻,Ω;s为电池的荷电状态soc,数值范围0~1;T为电池温度,K。
在恒流放电状态下,电池的soc随电流与时间的乘积呈线性变化,故根据Cheng [19] 对电池soc的研究,相关计算式如下所示。
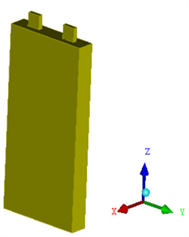
Figure 1. Simplified model of single lithium battery
图1. 单体锂电池的简化模型
(10)
式中,st与st+1为t时刻前后的电池soc值;I为放电电流,A;t为放电时间,s;Cs为电池额定容量,Ah。
对电池进行仿真计算时,由于电池发热速率的瞬态变化,需对热源进行编写UDF文件以对随放电的进行而变化的热源进行定义。UDF文件由下所示。
#include udf.h
#define V 0.00011583 //电池体积,m3;
#define I 10 //放电电流,A;
#define H 10 //电池额定容量,Ah;
DEFINE_SOURCE(heat_source,c,t,dS,eqn)
{
real soc,resistance,T_K; //soc为电池剩余容量状态值;resistance为电池内阻,Ω;T_K为电池温度,K;
real source,ts; //source为电池热源,W/m3;ts为电池放电时间,s;
T_K=C_T(c,t); //获取电池的热力学温度;
ts=RP_Get_Real(flow-time); //获取电池的放电时间;
soc=1-(I*ts)/(3600*H);//计算电池剩余容量状态值;
resistance=1632*(1.867*soc*soc-2.404*soc+3.697)*exp(-0.0025*T_K); //计算对应soc的电池总内阻值;
source=(resistance*I*I+0.00026*I*T_K)*(1/V); //计算电池的单位体积热源;
dS[eqn]=0;
return source;
}
3. 锂电池液冷板模型的建立与分析
3.1. 液冷板结构的设计
本文采用间接式液冷方案对锂电池单体进行液冷仿真。电池与冷板表面相接触,放电时热量通过热传导的方式传递至冷板,经由流经嵌入冷板中的管路的冷却液以对流的方式将热量带走,以实现电池冷
(a) 液冷板串行结构 (b) 液冷板并行结构
Figure 2. Schematic diagram of two channel structures of liquid cooling plate
图2. 液冷板的两种流道结构示意图
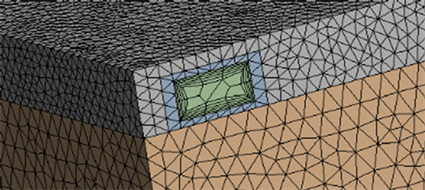
Figure 3. Schematic diagram of calculation domain grid of battery liquid cooling plate
图3. 电池液冷板部分计算域网格示意图
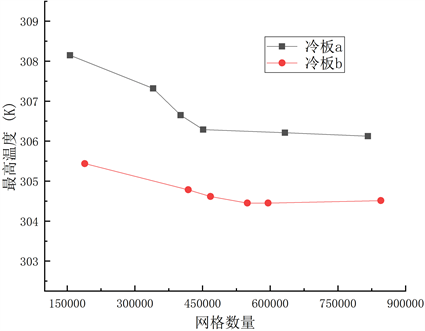
Figure 4. Verification of grid independence of two kinds of cold plate structures
图4. 两种结构冷板的网格的无关性验证
却的目的。因此,液体管路结构的设计与优化对冷板的冷却性能有着重要影响。本文针对容量为10 Ah的锂电池设计了串行结构冷板(下文简称冷板a)与并行结构冷板(下文简称冷板b),冷板在长宽的尺寸方面与电池保持一致,具体结构如图2所示。
3.2. 电池与液冷板的网格划分
将在Geometry中对液冷板以及电池建立的三维模型导入mesh工具中进行网格的划分,仿真过程中网格精度对计算的收敛、目标数据的准确性有着较大影响,故需对流体域需设置较高精度的网格以及一定的边界层数量,液冷板以及电池模型因结构相对简单,可设置尺寸较大网格以对总体网格数量加以控制。液冷板部分计算域网格划分情况如图3所示。
为保证仿真结果的准确性,消除因网格划分的差异对计算结果的影响,本文对两种模型采用6种不同数量的网格进行仿真验证。如图4所示。对应的串行与并行液冷板,网格数量分别为40.12万与46.71万时,电池最高温度Tmax不随网格数量的增加而变化,故认为此网格数量下的计算结果是准确的。
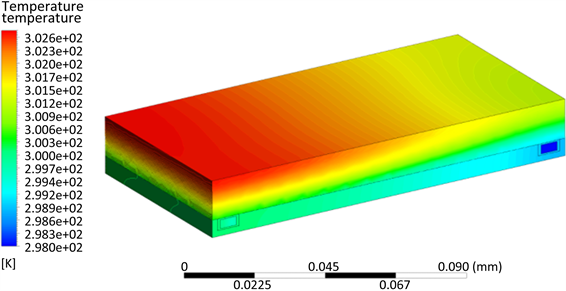
Figure 5. Temperature field distribution of battery under cold plate cooling of serial structure at the flow 1.62 × 10−3 kg/s
图5. 流量为1.62 × 10−3 kg/s时串行结构冷板冷却下的电池温度场分布
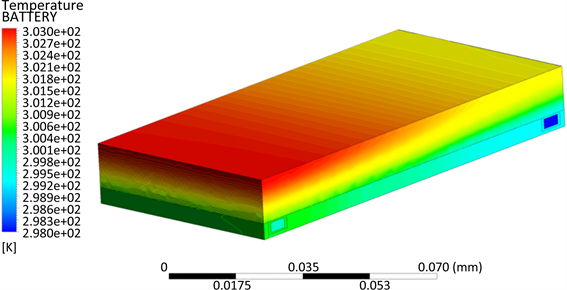
Figure 6. Temperature field distribution of battery under cold plate cooling of parallel structure at the flow 1.62 × 10−3 kg/s
图6. 流量为1.62 × 10−3 kg/s时并行结构冷板冷却下的电池温度场分布
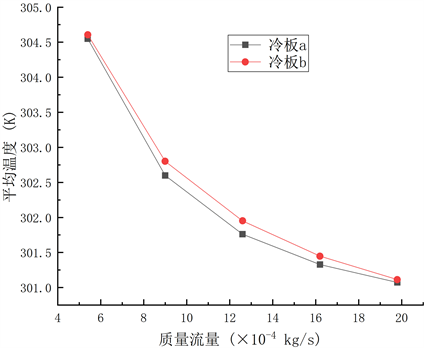
Figure 7. Variation of average volume temperature of battery with coolant mass flow
图7. 电池平均温度随冷却液质量流量的变化
4. 结果与讨论
为研究两种结构的液冷板对锂电池单体冷却效果的影响,通过改变液冷板入口质量流量Qm,分析不同质量流量下电池温度场的体平均温度Taver、最高温度Tmax与最大温度差ΔTmax,以及冷却液进出口压差ΔP以对液冷板的冷却性能进行评价。通过分析单体电池被冷却效果,以对液冷板进行优化。
4.1. 冷却液质量流量对电池体温度参数的影响
在电池温度313K,冷却液进口温度298K的初始条件下,进行不同质量流量下的电池单体冷却仿真计算。电池体积加权平均温度随冷却液质量流量的变化如图7所示。如图7所示,随着质量流量的增大,电池的平均温度逐渐降低,流量大于9 × 10−4 kg/s时,温度曲线斜率逐渐降低,降低的幅度逐渐减小。这是由于流量增大固然增大了冷却液与冷板的对流换热系数,但换热后期随着电池与冷板温差减小,减弱了换热强度从而使得电池降温幅度降低。流量为1.62 × 10−3 kg/s时串行与并行结构冷板冷却下的电池温度场分布如图5与图6所示。
不同流量下,冷板a冷却下的电池单体均温略低于冷板b,其差值在流量为1.26 × 10−3 kg/s时最大,为0.23 K。由此可得,串行结构冷板对电池的降温效果要优于并行结构冷板。
电池单体最高温度与最大温差随冷却液质量流量变化如图8所示。电池单体经两种流道结构冷板的冷却,其最高温度与最大温差都随冷却液流量的增加逐渐降低,且冷板a冷却下的两个温度参数皆略低于冷板b,这是由于在冷却液质量流量相同时,并行结构的冷板b每个流道中所流经的流量不均匀,不同流道的换热强度也有所不同,进而使得冷却后的电池温度场差异性增大,而冷板a出于串行结构的原因,流道内流动强度统一,进而使得前后换热效果均一性更好。由此可得采用冷板a同时适当增大冷却液流量可提升电池温度均匀性。如图所示,质量流量在5.4 × 10−4 kg/s至9 × 10−4 kg/s之间时,冷板a冷却下的电池最高温度与最大温差下降斜率最大,分别从307.03 K降低至304.67 K、5.62 K降低至4.67 K,相比于冷板b,最高温度低于后者0.37 K至0.15 K,最大温差低于后者0.45 K至0.83 K。由此得,从电池温度均匀性考虑,串行流道结构的液冷板要优于并行结构。
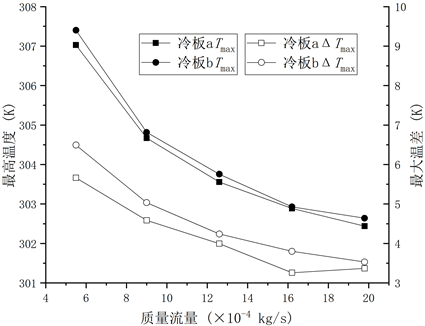
Figure 8. Variation of maximum temperature and maximum temperature difference of battery with coolant mass flow
图8. 电池最高温度与最大温差随冷却液流量流量的变化
4.2. 两种液冷板结构对压差影响的对比
除了冷板对电池的冷却效果,冷却液的进出口压差ΔP因关系到冷却液循环泵的能耗,也是对冷板综合性能评价的重要指标。两种流道结构的冷却液进出口压差等于进口总压与出口总压的差值,随着质量流量的变化趋势如图11所示。显然,两种结构下的压差皆随着进口流量的增而增大。此外,串行结构下的压差明显要高于并行结构,在流量为1.26 × 10−3 kg/s时压差分别为41.22 Pa与14.58 Pa,后者仅为前者的35.37%,流量增至1.98 × 10−3 kg/s,此时压差分别为96.55 Pa与26.83 Pa,这一比例降低至27.85%。这是由于入口面积不变的情况下,质量流量与流速呈正比,而其流动压力损失又与流体速度的平方正相
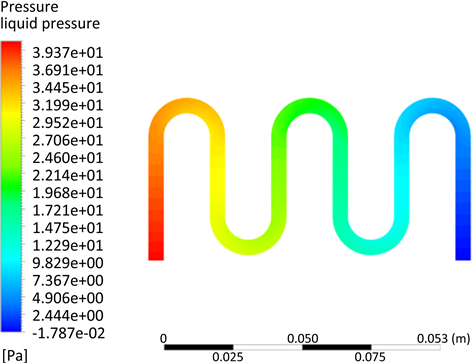
Figure 9. Pressure drop of cooling medium in cold plate of serial structure at the flow 1.26 × 10−3 kg/s
图9. 流量为1.26 × 10−3 kg/s时串行结构冷板中的冷却介质压降

Figure 10. Pressure drop of cooling medium in cold plate of parallel structure at the flow 1.26 × 10−3 kg/s
图10. 流量为1.26 × 10−3 kg/s时并行结构冷板中的冷却介质压降
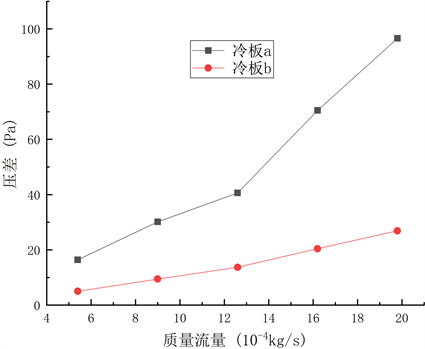
Figure 11. Variation of pressure drop at inlet and outlet of coolant with coolant mass flow
图11. 冷却液进出口压降随冷却液流量的变化
关,串行结构冷板在局部弯管数量和单管长度方面均大于并行结构冷板,致使局部阻力损失与沿程阻力损失之和增大,从而在能耗上要高于并行结构。流量为1.26 × 10−3 kg/s时,两种结构冷板流体域的压力云图如图9与图10所示。由前文可得,串行结构冷板冷却下的单体电池温度均匀性并未比并行结构情况下有较大提升,综合冷板能耗以及对电池冷却的能力,由上述可得并行流道结构的冷板有着更好的性能。
4.3. 针对液冷板的优化
根据上文分析,为提升电池温度场均匀性,针对冷板b冷却电池的最大温差大于冷板a这一问题,需要对冷板b进行优化。因石墨具有优良的导热性质,导热系数高达151 W/(m·K),且具有小密度的特点,故添加0.6 mm厚的石墨板在电池与冷板之间,对冷板进行优化以提升电池的温度场均匀性。如图12所示,冷板优化后被冷却的电池最高温度略低与优化前,冷却液流量为1.26 × 10−3 kg/s时,优化前后的最高温度分别为303.76 K与303.27 K,后者比前者降低了0.49 K。此外,经过优化后电池温度场的最大温差相比优化前有着明显的降低,流量为5.4 × 10−4 kg/s时冷板优化前后电池的最大温差分别为6.49 K与4.51 K,降幅达到30.51%。这是由于石墨具有较高的导热系数,并且较传统的铜铝等金属导热材料有着密度小质轻的特点,在小幅度增加液冷板体积与质量的情况下,依靠石墨三维方向良好的导热性能,使得电池高温区热量能及时地传导至冷板的低温区,进而进行高效地换热以提升电池的温度均匀性,同时提高冷板的冷却能力。流量为5.4 × 10−4 kg/s时图13与图14分别为添加石墨前后电池温度场云图对比,通过将数据与云图对比可得,在电池与液冷板之间添加石墨使得电池的温度均匀性得到明显的提升。
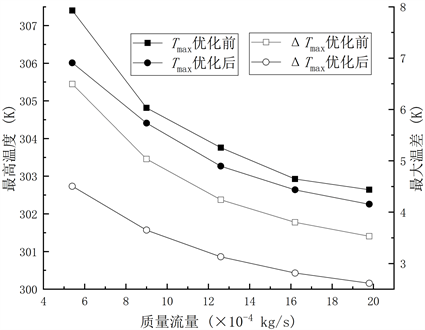
Figure 12. Variation of maximum temperature and maximum temperature difference of battery with coolant flow before and after structural optimization
图12. 结构优化前后电池最高温度与最大温差随冷却液质量流量的变化
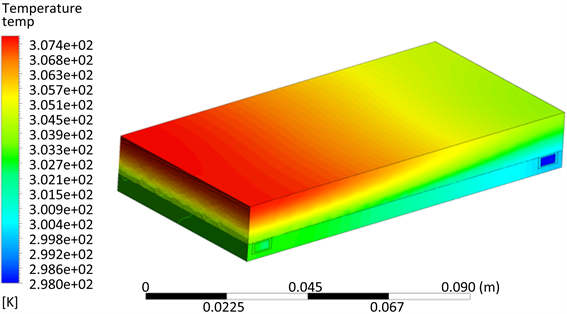
Figure 13. Temperature field distribution of battery under cold plate cooling of parallel structure at the flow 5.4 × 10−4 kg/s
图13. 流量为5.4 × 10−4 kg/s时并行结构冷板冷却下的电池温度场分布
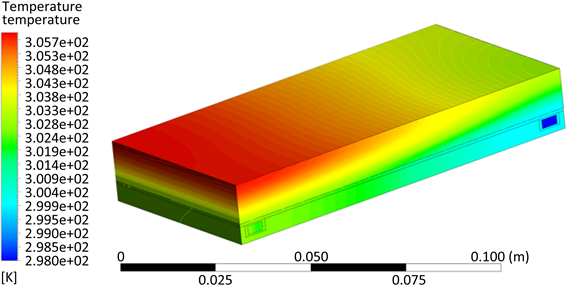
Figure 14. Distribution of battery temperature field under cooling of cold plate of optimized parallel structure at the flow is 5.4 × 10−4 kg/s
图14. 流量为5.4 × 10−4 kg/s时优化后的并行结构冷板冷却下的电池温度场分布
5. 结论
为研究与优化电池液冷板冷却性能,以使得电池保持健康的工作温度状态,本文提出了两种流道结构的液冷板,通过数值模拟软件对此冷却结构进行仿真计算,并根据计算结果的分析对液冷板进行优化,结论如下:
1) 以冷却液温度298 K以及电池温度313 K的初始条件,在不同流量下对两种结构液冷板冷却电池的温度场进行仿真分析,得到冷板a在对电池的降温效果要优于冷板b,且冷板a冷却下的电池温度场的均匀性上要比冷板a略高,但因冷板b在冷却液进出口压差的能耗降低方面上具有较大优势,综合能耗与电池冷却效果,故选择冷板b的并行流道结构针对温度均匀性对其进行优化。
2) 为提升并行结构冷板冷却下的电池温度场的均匀性,采用厚度为0.6 mm石墨板放置于电池与冷板之间以促进电池与冷板间导热的进行。不同冷却液流量下,在不增加额外能耗的情况下,优化后电池温度场最大温差与最高温度均较优化前有所降低。冷却液流量为1.26 × 10−3 kg/s时,优化前后的最高温度分别为303.27 K与303.76 K,降低了0.49 K,优化前后电池的最大温差分别为4.24 K与3.11 K,降幅达到26.59%,故说明此优化方式对电池温度均匀性有明显的提升作用,采用优化后并行流道结构的液冷板能在保证较低能耗的情况下兼顾对电池的冷却效果,本文同时为电池液冷板并行流道设计提供了部分依据。