摘要: 在拉伸载荷下对6082-T6铝合金预制不同程度的塑性损伤量,并对各试样进行了非线性超声检测,研究了6082-T6铝合金相对非线性系数
β'与残余塑性变形量R
p之间的变化关系;利用XRD-WH方法,对不同塑性损伤试样的位错密度进行了估算,探讨了位错演化和非线性系数的关系。结果表明:在非线性超声检测中,随着塑性损伤的加剧,非线性系数
β'首先增长相对缓慢,随后显著增加;随着塑性损伤程度的加剧,位错密度逐渐增加,加强了非线性响应,使相对非线性系数
β' 增加。
Abstract:
The plastic damage amount of 6082-T6 aluminum alloy prefabricated in different degrees was studied under tensile load, and the nonlinear ultrasonic test was carried out on each sample. The change relationship between the relative nonlinear coefficient of 6082-T6 aluminum alloy and the residual plastic deformation amount Rp was studied. By means of XRD-WH method, the dislocation density of samples with different plastic damage was estimated, and the relationship between dis-location evolution and nonlinear coefficient was discussed. The results show that: in the nonlinear ultrasonic testing, the nonlinear coefficient increased slowly in the first place with the increase of plastic damage, and then increased significantly. With the increase of plastic damage, the dislocation density increases gradually, which strengthens the nonlinear response and makes the relative nonlinear coefficient increase.
1. 引言
工业机械设备的服役环境是复杂多样的,在工业机械设备被广泛应用的同时,其安全服役性能也需要得到保障。因此,除了优异的设计和优良的加工外,还需要对机械零部件中的关键构件的服役状态进行有效的监测评估,由此各种无损检测法应运而生。不损坏被测材料,也能对其进行性能和状态的检测,这是无损检测的主要特点。目前常用的技术主要有:x射线检测技术 [1] [2]、超声检测技术 [3] [4]、磁粉检测技术 [5]、声发射技术 [6] 以及涡流检测技术 [7] [8],不同种类的无损检测方法都有不同的应用领域及适合其检测的缺陷种类 [9] [10] [11]。然而传统无损检测技术都有一个致命的局限,即只能检测介质中的宏观缺陷,例如裂纹和气孔等,对于微米或者纳米级的缺陷并不敏感 [12]。有关非线性超声技术的众多理论和实验研究显示 [13] [14] [15] 该技术能够有效表征材料工程构件早期损伤过程中内部微观结构的变化,有望成为一种有效的早期损伤检测技术。本文基于非线性超声技术,对拉伸载荷下造成不同程度塑性损伤的6082-T6铝合金进行了非线性超声检测,探究铝合金的相对非线性系数
与残余塑性变形量
之间的变化关系,有利于推动非线性超声无损检测技术应用于铝合金工程结构。
2. 材料及实验方法
2.1. 实验材料
试验材料为6082-T6铝合金,出厂状态为12 mm厚T6热处理轧制板材。拉伸断裂过程的应力应变曲线如图1所示,力学性能如表1所示,化学成分如表2所示。
2.2. 试验方法
2.2.1. 试样加工
6082-T6铝合金拉伸试样从板材切割加工而成,共切取S1-S7 7根试样,试样长度方向平行于轧制方向。加工尺寸如图2(a)所示,平行段横截面积为240 mm2,平行段为50 mm。机械加工后于200℃保温2 h以消除应力,并用砂纸逐级打磨。利用DNS3000型号拉伸试验机对试样进行拉伸,根据拉伸位移量预制塑性变形。拉伸卸载后,各试样对应的残余塑性变形量
(卸载后伸长量与原长的比值)如下表3所示。拉伸断裂之前,试样会发生明显颈缩,塑性变形量4.77%的S7试样出现了明显颈缩,已经接近断裂,而塑性变形量4.32%的S6试样未出现颈缩,说明颈缩发生在4.32%~4.77%之间,拉伸试样如图2(b)所示。
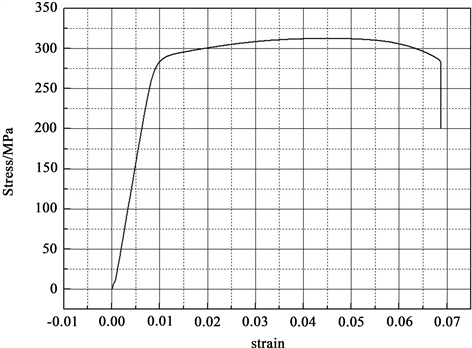
Figure 1. Stress strain curve of 6082-T6 aluminum alloy
图1. 6082-T6铝合金应力–应变曲线
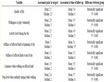
Table 1. Mechanical properties of 6082-T6 aluminum alloy
表1. 6082-T6铝合金力学性能
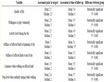
Table 2. 6082 chemical composition of aluminum alloy
表2. 6082铝合金化学成分(wt%)
2.2.2. 超声非线性检测
非线性超声检测系统示意图如图3所示。
实验系统采用的硬件及各项参数设置如下:发射探头采用中心频率为2.5 Mhz的窄带压电换能器(2.5 MHz,SIUINDT汕头超声直探头,2.5Z14N),接收探头采用中心频率为5 MHz的宽带压电换能器(5 MHz,SIUI NDT汕头超声直探头,5Z14N),它们的有效辐射面积一致,为了保证激发信号脉冲与反射信号脉冲不相互重叠,根据式样厚度12 mm,激发信号的脉冲周期数为10。示波器采样频率设置为2.5 G/s,采样模式选择平均模式,平均次数设置为示波器的最高参数,512次。为了使测试过程中耦合条件引入的误差降到最小,采用机油作为耦合剂,探头和试件用特定的夹具进行固定,并使用压力传感器测量夹具与探头接触面之间的压力,保证每次测试的压力尽量一致。
在进行拉伸试验之前,将拉伸试样的平行段平均分成5段,将每一段的中心设为测试点,如图4所示,对每一段的中心点进行非线性超声纵波离线检测,每个测点测量3次。
(a) 加工尺寸示意图
(b) 经过拉伸实验后的试样
Figure 2. Schematic diagram of tensile specimen
图2. 拉伸试样示意图
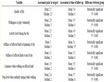
Table 3. Residual plastic deformation Rp of each sample after tensile unloading
表3. 各试样拉伸卸载后残余塑性变形量Rp
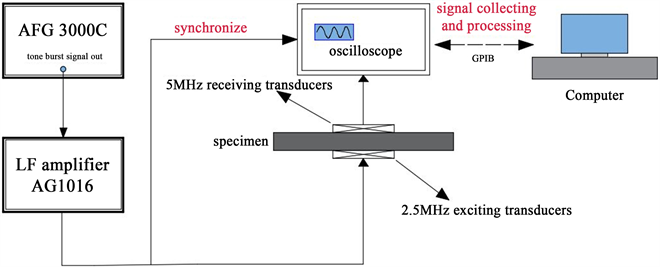
Figure 3. Block diagram of nonlinear ultrasonic longitudinal wave experiment system
图3. 非线性超声纵波实验系统框图

Figure 4. Schematic diagram of test point location
图4. 测试点位置示意图
3. 实验结果与讨论
3.1. 塑性损伤检测结果与分析
不同塑性损伤试样平行段各处的非线性系数变化情况如图5所示。
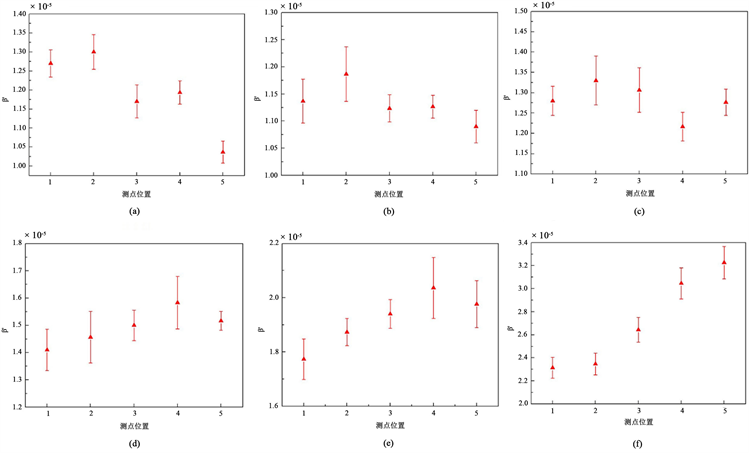
Figure 5. Variation of nonlinear coefficients of parallel sections of different plastic damage specimens: Rp (%) = (a) 0.89; (b) 1.51; (c) 2.34; (d) 3.74; (e) 4.32; (f) 4.77
图5. 不同塑性损伤试样平行段各处非线性系数变化情况:Rp (%) = (a) 0.89;(b) 1.51;(c) 2.34;(d) 3.74;(e) 4.32;(f) 4.77
可以看出,对于同一试样,非线性响应在平行段的各不同位置并不一致,且相对非线性系数
存在明显峰值。对于不同损伤程度试样,相对非线性系数
峰值在平行段的不同位置上的分布多次出现在测点2和测点4,即试样S7发生颈缩而即将断裂的位置。为了验证拉伸过程,相对非线性系数
峰值和断裂位置之间的联系,对S6和S7试样加载拉断,发现试样最终断裂处都在相对非线性系数
出现的位置附近。
为了研究相对非线性系数
与塑性损伤程度之间的关系,以S2~S7每个试样损伤程度最高的局部区域作为研究对象,选取了每个试样相对非线性系数
的峰值作为表征。相对非线性系数
峰值与塑性损伤的关系如图6所示。
通过拟合曲线可以看出,随着塑性损伤的加剧,相对非线性系数
缓慢增加到某一水平,随后显著增加,对于
值最大的S7试样,非线性系数
约为S1试样的3.16倍。
3.2. 位错密度估算结果
通过X射线衍射分析仪,使用铜靶(波长1.5418 Å),在30˚~90˚
角度范围内进行测量,并基于XRD-WH方法对不同塑性损伤的6082-T6铝合金进行位错密度估算,研究位错密度对相对非线性系数的影响。6082-T6铝合金不同塑性损伤程度试样的x射线衍射图谱如图7所示。由图可知,随着塑性损伤的改变,衍射峰发生了明显变化。
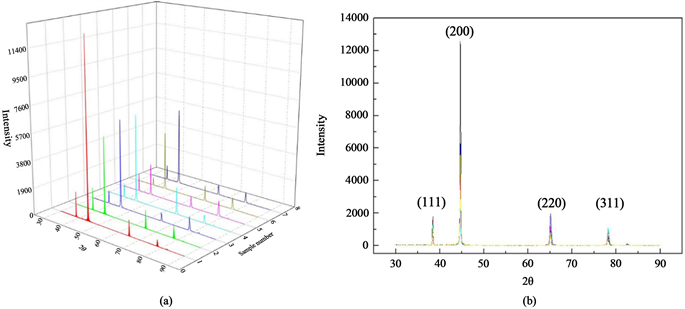
Figure 7. XRD patterns of different plastic damage of 6082 aluminum alloy: (a) Three-dimensional pattern; (b) Crystal plane pattern
图7. 6082铝合金不同塑性损伤的XRD图谱:(a) 三维图谱;(b) 晶面谱
将测试数据导入到Highscore软件,提取各个试样的
、
,计算所得各试样的位错密度值如表4所示。随着塑性损伤的加剧,位错密度呈明显的增大趋势,结合非线性超声测试结果,可以看到相对非线性系数与位错密度的变化呈正相关关系。
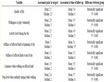
Table 4. Estimation of dislocation density of different plastic damage samples
表4. 不同塑性损伤试样的位错密度估算
4. 结论
在非线性超声检测中,随着塑性损伤的加剧,非线性系数
首先增长相对缓慢,随后显著增加,塑性变形量
值最大的S7试样,相对非线性系数
约为S1试样的3.16倍。表明铝合金的塑性损伤过程中非线性超声比线性超声更加适用于检测评价铝合金的塑性损伤。同时,针对塑性损伤过程,利用XRD-WH方法做了位错密度估算,分析了其微观组织的演化,探讨了微观组织–非线性超声系数–材料宏观力学性能的关联。随着塑性损伤程度的加剧,位错密度逐渐增加,加强了非线性响应,使相对非线性系数
增加。