1. 引言
变速器作为汽车“三大件”之一,其静力学性能与整车性能密切相关。特别是在新能源汽车快速发展的今天,变速器的NVH性能更是各大汽车厂商以及广大新能源汽车客户所关注的重点 [1] [2]。然而变速器箱体的刚强度是其NVH性能的基础,因此在变速器的开发过程中其箱体刚强度分析比以往更加重要。Edmund Stilwell和Riza Jamaluddin等人通过CAE软件分析了某款汽车驱动桥壳体的刚度和强度,并从中得出了壳体结构与驱动桥内齿轮啸叫的关系 [3];Abbes等采用声固耦合的办法对齿轮箱在时变刚度激励作用下的声辐射进行了分析 [4]。
目前,在使用有限元软件进行变速器箱体的刚强度分析过程中,还存在一定的不足,主要集中在载荷加载过程、施加约束过程以及箱体连接过程中。钟尚江等通过直接耦合轴承座孔内壁网格节点于中心一点,并以中心点作为加载点的方法进行加载 [5]。这种加载方法会使得轴承座孔内圈刚度过大,且受力过于均匀,会产生较大的误差;彭显昌等通过计算轴承座孔与轴承外圈之间可能的接触区域,然后在该区域添加均布载荷 [6]。这种加载方式较为准确但是仍不能保证接触区域完全正确,且均布载荷区域内载荷会比实际载荷更平均,同时需要更多繁琐的计算过程;张楠等人通过在螺栓孔位置添加耦合关系模拟箱体间的螺栓连接 [7]。该方法简便快捷且计算结果易收敛,但是未考虑螺栓预紧力对箱体结构造成的影响,容易忽略部分需优化的薄弱区域。
本文使用Abaqus软件,对变速箱进行刚强度分析,阐述在刚强度分析的加载过程、施加约束过程以及箱体连接过程中使用不同方法而产生的影响,并优化不完善的分析步骤。
2. 加载方式的影响
使用有限元分析软件进行新能源汽车变速箱的刚强度分析时,需要兼顾计算效率及收敛性,因此通常不会考虑内部零件,仅对变速箱箱体进行刚强度分析。这种做法不可避免的会使分析结果出现一定的误差。然而在传统的分析工程中,研究人员们可能会使用耦合轴承座孔内壁网格节点于一点的方式加载;或计算轴承座孔与轴承外圈之间可能的接触区域,并在该区域添加均布载荷的方式加载。以上这些加载方式都不够完善,导致进一步加重误差。
本文在加载过程中通过添加轴承外圈,将轴承外圈的内壁网格节点耦合于中心作为加载点进行加载,同时在轴承外圈的外壁网格与轴承座孔内壁网格之间添加接触约束,通过轴承外圈将力传递给变速箱,如图1所示。
(a) 无轴承外圈
(b) 添加轴承外圈
Figure 1. Bearing seat hole loading mode diagram
图1. 轴承座孔处加载方式示意图
以受载最大的轴承座孔为例,对比分析两种不同加载方式所得到的轴承座孔处的应力分布情况。如图2所示,在未引入轴承外圈时,轴承座孔内圈的应力分布均匀,在X-Z平面的各方向上没有明显差异;而引入了轴承外圈之后,轴承座孔处出现了明显应力分布不均情况,轴承座孔内壁沿−Z方向受压,这是由于该轴承座孔主要受到沿−Z方向的载荷所致,符合加载条件;且该轴承座孔在进油口处出现了较明显的应力集中现象,表明该轴承座孔处的进油口位置存在一定的不合理性,需要进行进一步的优化处理。
(a) 无轴承外圈
(b) 添加轴承外圈
Figure 2. Stress distribution at bearing seat hole under different loading methods
图2. 不同加载方式下轴承座孔处的应力分布
同样以该轴承座孔为例,对比分析两种不同加载方式下的变速箱箱体变形量情况。如图3所示,在使用无轴承外圈的加载方式时,轴承座孔周围各个方向上的位移量相差不大,变形较均匀;且由于该加载方式的原因,轴承座孔处的刚度明显增加,导致最大变形量相较于引入了轴承外圈的加载方式减小了23%;而使用添加轴承外圈的加载方式时,由于−Z方向受载最大,因此箱体在该轴承处沿−Z方向的变形最为严重,且由于轴承座孔应力分布不均,其周边的位移量也呈现出与应力分布情况相符的不均匀变形。
(a) 无轴承外圈
(b) 添加轴承外圈
Figure 3. Deformation of the box under different loading methods
图3. 不同加载方式下的箱体变形
对比分析上述刚强度分析结果,并结合工程实际后,可知在加载过程中添加轴承外圈,能够更准确的模拟变速箱的实际受载情况,有效减小由加载过程而产生的误差。
3. 接触的影响
轴承座孔与轴承外圈之间通常是通过过盈配合实现连接,刚强度分析的过程中,通过在轴承座孔与轴承外圈之间添加接触对来模拟轴承座孔与轴承外圈的连接。
在Abaqus中可通过添加接触对模拟实际工程问题中涉及面与面或部件与部件之间的接触关系。如果在这些接触面之间存在摩擦,就会产生相应的剪力来阻止部件之间的相对滑动。接触条件是一种不连续约束,因为只有当两个面正在发生接触时才会产生约束,因此一旦接触消失,约束也就随之消失,所以这种约束时不连续的,它允许力从模型的一部分传递到另一部分 [8]。
3.1. 接触对的主从面设置
接触算法中包括主面与从属面的区分。主面与从属面的区别在于:在计算过程中允许主面的节点嵌入从面网格中,而从属面的节点无法嵌入主面网格中。因此,为了获得更加准确的刚强度分析结果,应该正确选择主面和从属面。
本文的接触对是轴承外圈与轴承座孔,轴承外圈材料硬度大于变速箱,因此选择轴承外圈表面为主面,轴承座孔表面为从面,较硬材料的网格不能被较软材料网格嵌入。
3.2. 接触容差的设置
使用软件进行刚强度分析时,其本质上也是采用了有限元分析方法。即将一个连续体离散成有限个微小单元的组合体,节点作为连接单元把离散后的各个微小单元体重新连接为一个整体 [9]。求解过程中,先对不同区域内的单元进行单独求解得到区域的近似值,然后推导求解得出整体的结果 [10]。其求解步骤如下:
离散后的单元内每个节点的位移函数关系可表示为:
(1)
其中:
——单元内任意点的位移向量
——形状函数矩阵
——节点位移向量
单元应变与节点位移的关系可表示为:
(2)
其中:
——单元应变向量
——几何矩阵
根据单元应变可求得单元应力:
(3)
其中:
——单元应力向量
——惯性矩阵
带入式(1)得:
(4)
建立单元节点载荷和节点位移之间的关系式,即单元的刚度方程,从而推导出单元的刚度矩阵:
(5)
(6)
其中:
——单元刚度矩阵
——等效节点载荷列向量
最后建立整体平衡方程:
(7)
其中:
——整体载荷向量
——整体刚度矩阵
——整体节点位移向量
引入边界条件即可求得整体刚度矩阵,进而求得所有节点位移、节点应力。
由于有限元法的特性,部分曲面在离散过程中不可避免的会产生一定的形状误差,这就使得在本该接触的两个面之间可能会形成一定的间隙,如图4所示。
(a) 有限元法产生的形状误差
(b) 接触面间的空隙
Figure 4. Diagram of shape error
图4. 形状误差简图
然而在添加接触对时,两个表面之间分开的距离称为间隙,当两个表面之间的间隙变为零时,在分析过程中即施加了接触约束。接触面之间能够传递的接触压力的量值没有任何限制,当接触面间的接触压力变为零或负值时,两个接触面分离,并且接触约束被移除 [8]。由于形状误差的存在,使得相互接触的两个面间可能存在间隙,这就导致部分区域未产生接触约束,从而使得某些面接触区域变为线接触或者点接触,产生计算误差。
为避免上述问题的发生,轴承外圈与轴承座孔间添加接触约束时,需要设置一定的接触容差。接触容差表示在一定的误差范围内,两个不接触的面视为接触状态,从而保证轴承座孔和轴承外圈保持面接触状态。
在设置了接触容差后,分析轴承座孔处的应力分布情况。如图5所示,轴承座孔内壁在平行于内壁方向应力分布均匀,表示该接触区域属于面接触;而在未设置接触容差时,该轴承座孔内壁上出现了几处明显的应力集中区域,这表明这部分区域很有可能是发生了点接触,与实际情况不相符。此外由于这些应力集中区域的出现,导致了轴承座孔处的局部应力明显增加,该区域的最大应力值相较于设置了接触容差时的应力最大值增大了35%。
(a) 无接触容差
(b) 有接触容差
Figure 5. Stress distribution at bearing seat holes under different contact tolerance settings
图5. 不同接触容差设置下轴承座孔处的应力分布
对比分析有无设置接触容差的刚强度分析结果可知,在接触对之间添加接触容差可以更好的模拟轴承外圈与轴承内孔之间的接触状态,从而减小误差。
4. 连接方式的影响
变速箱的刚强度分析过程中,研究人员为了提高计算效率和收敛性,通常会在螺栓孔位置处添加耦合关系模拟螺栓连接,也就是直接将左右箱体螺栓孔处的网格节点耦合于中心一点。这种连接方法简单快捷,但是会使得螺栓孔处的局部刚度过大,且使用该方法连接的箱体更近似于左右箱体不可分离的一体式箱体部件。因此在条件允许的情况下,可以添加螺栓模型并施加螺栓预紧力模拟螺栓连接。从而获得更加精确的刚强度分析结果,避免忽略部分薄弱区域。
本文添加螺栓模型模拟螺栓连接的步骤大致如下:首先导入划分好网格的螺栓模型,完成螺栓的材料、属性赋予后将螺栓部件装配到箱体部件上;螺栓连接的局部区域包括了螺栓帽与箱体的接触以及两箱体之间的接触,需要按上文所述的方法添加接触约束;在螺栓的螺纹与箱体螺纹孔之间需要添加绑定约束模拟螺纹连接;最后在螺栓截面位置施加螺栓预紧力,如图6、图7所示。
如图8,对比分析箱体在不同连接方式下的应力分布情况后,可以明显看到当添加了螺栓模型并施加螺栓预紧力之后,箱体的整体应力显著提高,特别是在靠近螺栓处的箱体边缘位置。这是由于实际的螺栓连接需要较大的预紧力,这会对箱体产生很大的压应力,导致箱体在受力过程中,其上表面与侧表面之间产生较大的拉应力所致。而通过直接耦合的方式连接两箱体时,由于两箱体的螺栓孔位置可视为一个整体,局部刚度大,因此不会使箱体边缘位置产生较大应力。如图8(a)所示,箱体上表面的悬置安装孔处出现了较大的应力集中,这是采用直接耦合的方式连接箱体时很容易忽略的薄弱区域,需要对其进行相应的优化处理。
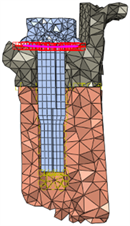
Figure 6. Schematic diagram of local contact and binding constraint of bolt connection
图6. 螺栓连接局部接触、绑定约束示意图
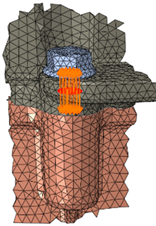
Figure 7. Schematic diagram of bolt preload
图7. 螺栓预紧力示意图
(a) 添加螺栓模型模拟螺栓连接
(b) 直接耦合螺栓孔模拟螺栓连接
Figure 8. The stress distribution of the box under different connection modes
图8. 箱体不同连接方式下的应力分布情况
5. 结论
根据分析结果可得以下结论:
1) 加载方式的不同,会对变速箱刚强度分析结果产生显著影响。
2) 在加载过程中添加轴承外圈,可以有效避免由于直接耦合所造成的轴承座孔局部区域刚度增加,降低了由于加载导致的计算误差。
3) 在轴承座孔表面与轴承外圈表面的接触约束中添加接触容差,可以防止由有限元固有特性而产生的计算误差。
4) 螺栓附近的箱体边缘可能会出现较明显的应力集中,直接耦合螺栓孔的连接方式可能忽略这部分薄弱区域,添加螺栓模型模拟连接可有效避免该问题。
NOTES
*第一作者。
#通讯作者。