1. 引言
真空断路器作为电力系统中常用的开关设备之一,其稳定运行直接影响电网运行的稳定性和供电的可靠性 [1] [2] [3]。随着真空断路器长时间运行,部分器件不断磨损,真空度下降,将导致设备出现故障,从而产生不必要的灾难。经统计,由真空断路器引发的事故每年均有发生,主要为机械故障和电气故障引起,其中机械故障占比95% [4] [5]。传统检修方法采取人工定期检修的方式,在规定时间对设备进行逐一排查,无论断路器是否存在问题,都需要对断路器进行检修,极大地浪费人力、物力、财力,并存在重装后发生新故障的未知风险 [6]。
针对真空断路器在检修过程中存在的诸多问题,许多学者进行了相关研究。谭家明等对真空断路器机械振动进行监测,通过振动变化分析机械故障原因 [7];陈景翠等基于拉曼散射的测温原理,实现了真空断路器触头的精准测温 [8];张龙等采用角位移传感器获取断路器触头行程轨迹曲线,并用中值滤波算法对曲线轨迹进行去噪、平滑处理,通过曲线变化,预警故障发生 [9] [10];白云飞等采用B⁃spline拟合和最小二乘法对分合闸行程曲线进行分段拟合 [11];袁欢等采用激光诱导等离子体光路复用技术监测真空断路器的真空度 [12]。以上研究虽然都可以在一定程度上反映断路器的运行状态,但是单一特征量的监测并不能准确判断出设备故障的类型,如:只监测分、合闸线圈电流能够反映电磁铁老化、线圈老化、磁铁堵塞等问题,但不能计算触点刚分、刚合点速度等机械特性,只监测断路器设备振动信号,可以反映螺丝松动、保护罩破裂、弹簧损坏、主轴卡涩等问题,但却不能反映电磁铁老化、线圈老化、磁铁堵塞等问题。
针对现有研究中的不足,为了能够全方位准确的监测设备运行状态,及时判断发生故障风险的等级和发生故障的原因,精准掌握断路器工作状态,本文提出一种新颖有效的真空断路器在线监测系统。该系统采用现代传感器技术,对断路器的运行进行在线监测。与此同时,一种高效的特征值评估体系被建立,将该体系与上位机实时绘制的监测曲线相配合,实现对真空断路器发生故障风险等级的评估,同时通过上位机绘制的信号曲线分析故障发生的原因,确保故障发生时能够及时维修。
2. 真空断路器在线监测系统整体设计
真空断路器在线监测系统主要由信号产生模块、数据采集模块、数据处理模块、上位机信息储存模块、故障分析模块与风险评估模块、报警模块组成。监测系统流程如图1所示。真空断路器在运行时,自动记录在线监测的数据,主要包括:分合闸线圈电流、触点压力、动触点运动行程、设备机械振动程度。通过实时数据与机械特性评估体系的历史数据对比,结合经验与理论,判断断路器存在发生故障风险的等级以及发生故障的可能原因。
3. 系统硬件电路设计
真空断路器硬件电路主要包括:信号产生电路、调理电路、AD转换电路、RS232通讯模块、电源模块、驱动模块。当真空断路器运行时,信号采集电路采集信号,经过调理电路和AD转换电路处理后,将数据发送给单片机。其系统硬件框图如图2所示。
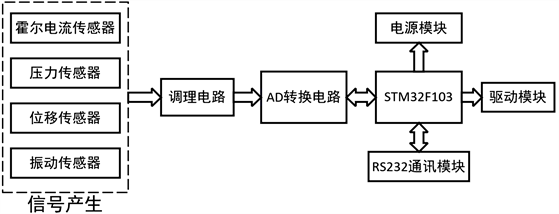
Figure 2. Block diagram of system hardware
图2. 系统硬件框图
3.1. 分合闸线圈电流信号采集
真空断路器是以电磁铁作为一级控制元件,当线圈中有电流时,电磁铁产生磁通,铁心受到电磁力的作用吸合,完成分合闸动作。线圈中电流检测可以有效的分析断路器的分闸、合闸时间、线圈通电时间、铁心运动状态。本系统采用磁平衡式霍尔电流传感器测量真空断路器线圈中的电流,经过100 Ω电阻R17将电流信号转换为2.5 ± 0.625 V的电压信号,在经过隔离、滤波、放大将电压信号转换成0~3.3 V电压,电路如图3。
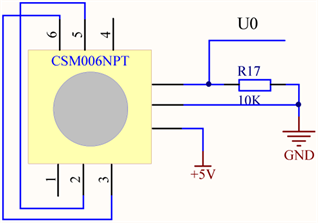
Figure 3. Peripheral circuit of Hall current sensor
图3. 霍尔电流传感器的外围电路
3.2. 触头接触压力信号采集
为保证断路器能够快速断开线路,触头闭合时必须得有一定的接触压力,保证分闸操作时,触头能够快速弹开,实现快速切断故障电路,更好的保护电力系统。本系统采用高精度电阻式应变片传感器BF1K-2GB搭建的全桥电路来检测触头压力,桥臂的四个应变片电阻值均为1 K,最大应变极限为2%。电桥平衡时(无应变发生)没有信号输出,发生应变电桥失衡输出应变信号。设电阻的相对变化率为ΔR31/R31、ΔR32/R32、ΔR33/R33、ΔR34/R34。电路的四个应变片组成两个差动工作组即全桥电路时,电阻相对变化率之和存在式1。全桥电路如图4,其中R31、R34贴在一侧,R32、R33贴在另一侧组成差动工作片,其形变大小均为ΔR,但极性相反。通过此方式可以有效的提高测量精度、实现温差的自动补偿,其输出电压存在公式2。
(1)
(2)
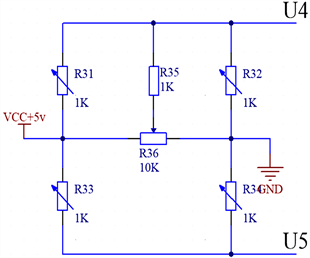
Figure 4. Full bridge differential measurement circuit
图4. 全桥差动测量电路
3.3. 触头行程信号采集
真空断路器触头运动行程反映触头的刚分、刚合点的速度以及实时位置等机械参数,通过对触头行程的实时监测,可以判断故障类型及位置 [13]。本系统采用电阻式位移传感器KTM-50Lmm监测触头的行程,输出信号为电压信号,经过调理电路输出0~3.3V电压。
3.4. 机械振动信号采集
利用振动信号对断路器运行状态进行监测与故障分析是一种常见的方法 [14] [15]。设备在运行过程中产生的振动情况可以判断设备的运行状态。因此针对于设备机械振动信号的采集尤为重要。本系统采用ADXL001-70BEZ振动传感器来采集真空断路器在运行过程中设备的振动频率,该传感器具有体积小、功耗低、低噪声的优点,传感器采集到的信号经过调理电路处理发送给上位机。上位机利用振动信号实现实时监测设备运行状态。
3.5. 真空度在线检测电路
为实现在线监测真空断路器的真空度,本文采用耦合电容法对真空断路器的真空度进行监测,利用电容放电所产生的的电信号来检测真空灭弧室的真空度 [16]。由放电原理真空室真空度降低时,带电粒子会积聚触头附近,很容易与屏蔽罩之间形成击穿电压放电产生强电场,而且随着真空度下降,屏蔽罩内气体分子数逐渐上升,在强电场作用下气体分子出现强电离现象,带电粒子在强电场作用下高速运动,因此放电现象越来约明显,放电电流逐渐增大 [17]。如图5所示,C12为带电触头和屏蔽罩之间的电容,C13为屏蔽罩与耦合电容传感器之间的电容,C14为耦合电容传感器内部电容。当真空度降低时,工频电压从零点升至某一值时,即真空度度为一个临界值时,等值电容C12被击穿放电,C12、C13、C14构成放电击穿回路,回路中电荷发生动态转移而从新分布,此时C13输出信号将发生变化,此信号变化反应的就是真空度变化,等效电路如图6。
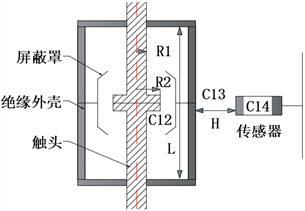
Figure 5. Schematic diagram of coupling capacitance method
图5. 耦合电容法原理图
由交流点位与真空度关系理论可知,当屏蔽罩内表面间的自由行程λ为触头到屏蔽罩的10倍时,只考虑触头与屏蔽罩之间的电荷电流。此时存在公式3、4。
(3)
(4)
其中:H为耦合电容传感器到绝缘外壳的距离R1为导杆半径、R2为触头半径、L为绝缘外壳长度。
经计算C12、C13值分别为24pF、4pF。耦合电容传感器选用4800 pF和耐压为200 V的精密电容作为试验传感器,得到在真空可标定范围的电压的最大值为2 V。输出信号经过滤波放大处理后发送给单片机,这所用调理电路原理和上述基本相同这里不在复述。为验证真空度检测电路的有效性。通过机械泵控制真空室的真空度如图7。启动真空泵,通过调节真空阀、放气阀控制使真空灭弧室的真空度达到不同值,在灭弧室两端加交流电压,通过传感器进行实时检测电压值变化。传感器检测电压值如表1。
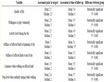
Table 1. Relationship between vacuum degree and sensor
表1. 真空度与传感器关系表
试验中每改变一次压强,记录真空度读数和耦合电容传感器的电压值,将数据导入MATLAB中进行曲线拟合,得到曲线拟合函数式5和拟合曲线图8。将该公式作为该型号断路器能够反映真空度和屏蔽罩电位变化的关系公式,将其作为比较基准,用来计算机在线监测。
(5)
3.6. 信号调理电路
3.6.1. 滤波电路
上述设计的传感器检测电路在测量中常常参杂许多噪声信号,影响测量的精度,因此常常需要消除噪声信号的干扰。本系统所用传感器输出电压信号的频率均低于100 Hz,因此设计一个二阶低通滤波器,滤去频率超过100 Hz的高频干扰。二阶低通滤波器的传递函数为式6,式中Aup为通带增益,ω0为截止角频率,Q为品质因数,其值为0.707。ω0的值由式7确定,f0由公式8确定。该电路具有元件少、增益稳定、频率范围宽等优点,C7、C9、R15、R16构成反馈网络可以有效的消除信号中的杂波,提高测量精度。具体电路设计如图9所示。
(6)
(7)
(8)
为验证电路的有效性,应用Multisim对低通滤波电路进行仿真分析。仿真电路设计如图10所示,仿真结果如图11所示。根据图11的结果可以分析出,对于频率高于100 Hz的电压信号逐渐降低最终变为0。该仿真结果表明该电路能够有效的消除高于100 Hz的信号,说明该电路可以在元件少、增益稳定、频率范围宽的基础上有效的完成对噪音等杂波的过滤,输出精确的电信号。

Figure 10. Simulation analysis of filter circuit
图10. 滤波电路仿真分析
3.6.2. 线性光电隔离电路
在完成对杂波的过滤后,为保护电力设备,需要隔离外部设备和电路控制单元,同时消除接地回路干扰,提高响应速度 [18]。常规光电隔离电路由于非线性传输特性,电信号在传输过程中会发生较大变化,导致测量结果出现问题。为解决这一问题,本系统设计一种线性负反馈光电隔离电路,电路结构如图12所示。
该电路采用两个运算放大器、两个光电耦合器构成,两个TLP-521输入端串联组成差分负反馈电路来补偿光电耦合器的非线性电流传输特性。图中U1A为反馈级,配合一对TLP521来补偿光电耦合器的非线性电流传输特性,U2A作为输出缓冲级,提高带载能力。电路设计原理如下。
对于理想放大器。由虚短可知,存在公式9、10。假设发光二级管流过的电流为I,由光电耦合器的电流传输特性存在式11、12。
(9)
(10)
(11)
(12)
式中I为流过发光二级管的电流,
、
为流过三极管的电流,g1、g2为电流传输系数。由于两个光电耦合器型号相同,因此g1 = g2。
由图8分析可知,存在公式13、14。
(13)
(14)
由式9~15得到式15。由公式15得到输入电压与输出电压只与R26、R28有关,但由于电阻存在温差特性,阻值随温度变化如公式16,式中ΔR为电阻随温度的变化量。为实现隔离电路输入输出1比1,必须存在R26 = R28且电阻温度特性一致,即公式17结果为1。
(15)
(16)
(17)
4. 真空断路器在线监测系统软件设计
4.1. 整体软件设计
系统主控制器为核心数据采集管理中心,由ARMcortex-m3架构处理器STM32F103VET7进行数据采集和分析,搭载SWM61850-MINI协议转换卡、声光报警装置,不保存数据,数据全部上传保存到触摸屏中。触摸显示屏为数据管理中心,进行处理、分析、管理、显示、存储数据。与主控制器间通过RS232进行通信。系统上电后,首先是相关寄存器、定时器、计数器初始化,进入主程序,对输入信号进行周期扫描,系统判断是否有数据输入,如果有数据,将数据发送给上位机进行故障分析和状态评估,若有问题发出相应的警报,找到问题所在。具体流程如图13所示。
4.2. 特征量选取与状态评估体系的建立
特征量能够反应断路器运动状态,本文主要选取特征量有:分合闸线圈带电时间T1、T2、分合闸铁心运动时间T3、T4、触头稳定位移X、触头稳定压力F。基于选择的特征量建立评估体系Q = [P1, P2, P3, P4],通过各个特征量之间在某一段时间的变化来评估设备出现风险的等级。其中P1代表初差值在±0%~±6%,P2代表初差值在±6%~±10%,P3代表初差值在±10%~±15%,P4代表初差值大于15%且小于−15%。P1、P2、P3、P4分别对应设备状态,运行良好状态、注意状态、异常状态、严重状态。初差值计算公式如式18,其中最大规定值为设备出厂的实验值。本文建立的真空断路器特征量状态评估体系见表2。
(18)
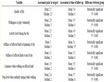
Table 2. State evaluation system of vacuum circuit breaker
表2. 真空断路器状态评估体系
5. 实验检测与故障分析
采用VSV-12型断路器搭建模拟实验平台,对真空断路器在线监测系统的性能进行检测。该设备主要技术参数如下:t分 ≤ 20 ms,t合 ≤ 35 ms、X = 20 cm、触头之间接触压力在3800 ± 400 N、分闸线圈的通电时间应小于42 ms、合闸线圈通电时间应小于50 ms、分闸铁心运动时间为8 ms、合闸铁心运动时间为12ms。使用实验平台模拟真空断路器工作过程中的常见故障,在线检测系统对故障信号进行采集。根据采集的数据绘制测试曲线,曲线如图14~17所示。在线检测系统根据测试曲线,分析故障发生的位置。同时诊断系统根据上位机绘制的曲线提取状态特征点,通过事先建立好的特征状态评估体系进行风险等级评估,发出警报。
图14(a)为在线监测系统三种情况下断路器分闸过程的电流时间曲线。图中在0~t1时间内,线圈开始通电,电流逐渐上升。在t1~t2时间内,铁心开始运动,运动速度很小,产生的反电动势也很小,因此线圈电流逐渐变小。在t2时刻铁心运动停止触发锁钩,弹簧开始释放能量带动触点开始运动,此时分闸动作开始,到t3时刻结束分闸。在t3~t4时间内,缓冲设备开始工作,减小分闸运动造成的机械振动,快速稳定系统。从t4时刻开始,线圈电流断开,电流迅速减小直到为0。
图14(a)中黑色曲线为断路器正常工作时的波形。故障波形A线圈通电时间变短、电流变小,根据分析是由于铁心空行程导致的。故障波形B线圈通电时间变长,根据诊断分析是由于线圈老化导致线圈通电时间过长、电流过大。图14(b)为断路器合闸电流时间曲线,故障波形C电流开始通电时线圈通电时间短,是由于操作电压过低导致的。故障波形D线圈电流上升较慢且通电时间比较长,经诊断分析是由于传动机构卡涩导致。在线监测系统在对数据进行采集后,该系统再根据状态评估体系对各时刻真空断路器的运行状态进行评估,评估结果如表3所示。
(a) 分闸
(b) 合闸
Figure 14. Current time curve of opening and closing process
图14. 分闸、合闸过程电流时间曲线
图15为在线监测系统对断路器合闸过程触头压力进行监测后绘制的曲线。将数据采集之后,系统将使用评价体系对真空断路器的运行状态进行评估,并告知实验人员。在图15中,黑色为断路器正常工作时压力曲线。根据断路器技术参数,为保证触头运动速度,触头压力应在3.4~4.2 KN。故障波形E触头闭合时压力过大是因为电机在合闸过程中转速过快导致的,压力过大会导致触点受到损坏。故障波形F压力在稳定时不足3.0 KN,经诊断是因为传动机构卡涩,导致触头压力不足。
图16为真空断路器分闸、合闸的位移时间曲线,在线监测系统通过曲线的稳定值可以判断设备运行情况。例如系统在运行过程中是否出现传动机构卡涩、电机转速是否正常、触点是否发生变形和损坏、以及分闸、合闸刚分、刚合点的速度。
(a) 合闸位移曲线(b) 分闸位移曲线
Figure 16. Contact pressure curve
图16. 触头压力曲线
图17为机械振动信号检测曲线。系统同样会依据状态评价体系对当前运行状态进行评价,进而给出设备运行的风险等级。图17(a)为断路器正常工作时的振动曲线,包含几个关键时间段,10~15 ms为铁心冲击锁钩时刻,弹簧释放能量,带动触点运动,15~25 ms为动触头运动过程,此时设备振动较小,为分闸状态,25~30 ms断路器触头向分闸最高点运动,此时由于弹簧释放能量没有结束,触头往复运动,设备出现较大振动。从30 ms到45 ms,缓冲系统在工作,设备振动逐渐减小。图17(b)为故障曲线,由图中曲线可以得出,从铁心运动开始就存在持续大幅度的振动,根据在线系统的诊断,此时设备存在较多问题,如设备外壳出现松动以及设备缓冲装置处于不工作状态。
(a) 机械振动波形(b) 机械振动故障波形
Figure 17. Mechanical vibration and fault waveform
图17. 机械振动及其故障波形
根据上述故障分析,真空断路器在线监测系统可以有效的完成对真空断路器实时运行状态进行在线监测。在系统中。上位机采集数据并提取每次故障的状态正特征值,进行风险等级评估。每隔一段时间进行一次风险评估,出现问题发出相应警报。
6. 结论
本文设计了一种真空断路器在线监测系统,利用现代传感器技术对真空断路器的运行状态进行实时监控。根据诊断系统分析故障发生的原因以及位置,同时配合状态评估体系评估设备风险等级。工作人员通过上位机实时监测曲线和风险评估等级进行及时的维修,实现人工定期检修到实时检修的转变。本文采用多种传感器监测设备运行状态,模拟真空断路器常见故障,根据数据曲线分析设备出现故障的原因以及出现风险的等级。实验结果表明,该系统运行稳定、实时性好,能够有效地实现在线监测,具有应用前景和参考价值。
基金项目
辽宁省教育厅科学研究经费项目(NO. LJKZ0510);国家自然科学基金项目(51975081)。
NOTES
*第一作者。
#通讯作者。