1. 引言
生产系统在运行过程中,由于受到内外部环境因素的影响,会出现退化现象,从而对生产有效性造成不利影响。为了提高生产系统的运行效益,必须对生产和维修进行合理规划。生产和维修规划是制造过程中非常重要的管理流程,将它们联合处理可以降低运行成本,提高收益。Jafari等(2015) [1] 研究了经济生产批量和预防性维修的联合优化问题。Guo等(2022) [2] 在考虑缺货损失的情况下,研究了生产批量和非周期预防性维修联合优化问题。Hosseini等(2020) [3] 在综合各类成本基础上,提出生产批量和维修周期优化方案,使长期运行单位时间平均成本最小。Bouslah等(2018) [4] 针对多部件串联系统,提出一种集生产、质量和维修计划联合控制的经济模型。Peng等 [5] 利用更新理论计算退化系统的长期平均成本,提出基于状态的维修方案,并确定最佳的生产批量。Cheng等(2018) [6] 建立了基于状态维修和经济生产批量联合优化模型,通过确定生产批量、库存和维修阈值,使单位时间总成本最小。Zheng等(2021) [7] 针对生产系统的退化,以成本最小为目标,提出基于状态维修的经济生产批量模型。Khatab等(2019) [8] 提出了一种生产质量与基于状态维修相结合的优化模型,以确定最优的检查周期和退化阈值水平。以上研究大都仅考虑了生产批量的优化问题,而生产计划的制定,除了批量还要考虑生产进度或生产率,以尽可能少的成本达到期望的生产效果。Bouslah等(2013) [9] 以批量和生产率为决策变量,建立了相关成本最小化问题的随机动态规划模型。制定生产计划是一项复杂的任务,包括多个与生产阶段相关的决策问题,如产能与需求相匹配、批量大小、维修方案,同时考虑较低的成本或较大的利润等。本文以批产品生产及系统维修为研究对象,在分析系统随机退化过程对产品质量和运行状态影响的基础上,考虑预防性维修和纠正性维修两种维修方案,通过确定最佳的批量和生产率,使生产系统在单位时间内平均收益最大。
2. 问题描述及模型假设
2.1. 问题描述
考虑产品的生产加工过程,由于受磨损、劣化、应力等诸多因素影响,生产系统会出现退化现象,退化量是随机变量且与系统运行时间有关。当累积退化量达到阈值时,系统发生故障。系统退化会影响加工的产品质量,退化程度越高,产品的不合格品率越大。生产企业对加工的产品进行全检,将合格品以固定价格在市场上销售,不合格品作报废处理。以批量产品的生产为研究对象,在生产过程中,根据退化量是否达到阈值,系统的运行可能会出现两种情形:1) 退化量小于阈值,系统没有发生故障;2) 退化量达到阈值,系统发生故障。考虑两种维修方案,如果系统没有发生故障,则在生产加工结束时,进行预防性维修,以修复系统已有的退化,否则进行纠正性维修。为了实现生产效益最大化,需要在综合考虑各类成本的基础上,制定最佳的批量和生产率决策方案。
2.2. 模型假设
1) 产品以批为单位组织生产,固定的生产成本忽略不计;
2) 产品的市场需求率为固定常数。生产过程中,只有合格品销往市场且不允许缺货,次品作报废处理;
3) 系统退化是单调递增的随机过程,且服从伽马过程。随着系统的退化,次品率会增加 [6];
4) 系统只有在加工运行时才可能退化,停机维修时不发生退化。当退化达到临界阈值时,系统故障并停止运行;
5) 预防性维修成本与退化量有关,纠正性维修成本为固定常数。两类维修均可使系统恢复到初始状态,即修旧如新;
6) 预防性维修和纠正性维修的时长均为随机变量,且服从威布尔分布 [4]。
3. 模型构建
生产运行过程中,系统在t时的累积退化量
为随机变量,且服从伽马分布,其概率密度为:
。系统退化对加工的产品质量产生不利影响,在t时的次品率
是退化量
的指数函数 [10],其表达式为:
,其中
是零退化时的次品率,
为非负常数。基于生产经济性考虑,同时也有利于合理组织生产和维修资源,提高过程管理的有效性。在生产加工前,生产部门需要确定生产批量Q和生产率P,以实现生产效益最大化。
根据生产过程中系统的运行状态,分两种情形分别计算涉及的各类成本损失。
3.1. 情形1:系统没有发生故障
在批量产品加工完成时,由于系统没有发生故障,故批量产品能够被全部生产,生产加工的计划时长为
,系统的累积退化量
。此时,对系统进行预防性维修,修复已有的退化。将系统从开始生产到销售或维修结束记作一个生产周期,则一个生产周期内涉及的各类成本包括:次品报废成本
、库存成本
、预防性维修成本
、缺货损失
和产品检验成本
。故,总成本为:
(1)
1) 次品报废成本
在一个生产周期内,生产的次品总数由生产率P及次品率
决定,且为随机变量,其表达式为:
。故,次品报废成本可表示为:
,其中
为单位次品报废成本,
。
由于对
,都有
。在
的条件下,记
其中
由伽马过程的独立增量性,得
,从而
(2)
其中
为上不完全
函数。
对式(2)两边同时求微分,得:
,
又,
。带入
右边表达式中,得:
(3)
故,次品报废的平均成本为:
(4)
其中
为情形1下生产的平均次品总数。
2) 库存成本
在生产过程中,为了满足市场需求,将合格品以市场需求率D发往市场,多余的产品将积压库存,从而产生库存成本。由于次品直接作报废处理,故本文不考虑次品的库存问题。另外,在生产加工结束后的系统维修期间,产品仍以速率D发往市场,由于清空库存需要时间,故还需要考虑生产加工结束后的库存成本。因此,将库存成本分为生产过程中库存成本和生产结束后库存成本两部分。
在生产过程中,
时的合格品产出率为
。因此,在t时的库存速率为
。故,生产过程中的库存成本可表示为:
(5)
其中
为单位时间库存成本,
为随机变量。
对式(5)两边同时求期望,得出生产过程中的平均库存成本为:
(6)
在生产过程结束时,产品的库存数等于合格品总数减去已销售产品数。此时的库存数达到最大,其最大平均库存数为:
,销售清空最大库存的平均时长为:
。因此,在生产过程结束后,销售清空最大库存的平均库存成本为:
(7)
故,平均总库存成本为:
。
3) 预防性维修成本
预防性维修是在批量产品生产加工结束时进行,维修成本与系统的退化量
有关。由于退化程度越高,将会给修复退化造成更大的难度。因此,本文假设预防性维修成本是退化量
的线性函数,即
,其中
和a为非负常数。在
的条件下,由于
,所以,预防性维修的平均
成本为:
(8)
4) 缺货损失
在生产结束时停机进行预防性维修,停机的时间取决于预防性维修的时间
。另外,库存产品被销售清空的平均时间为
。分两种情况:a) 如果
,在库存产品被销售清空前,已完成预防性维修,缺货的产品数为0;b) 如果
,在库存产品被销售清空后,预防性维修还将延续时长
,故缺货的产品总数为
。因此,缺货损失可表示为:
(9)
其中
为单位产品缺货损失。
设预防性维修时长
服从威布尔分布,其概率密度为
。对式(9)求期望,得平均缺货损失为:
(10)
5) 检验成本
在情形1下,批量产品能够全部被生产加工,由于执行全检,故检验成本
等于单位产品检验成本
和批量Q的乘积,即
。
3.2. 情形2:系统发生故障
当系统发生故障时,通过纠正性维修使系统恢复至初始状态。故障的发生取决于退化量是否大于故障阈值L,由于退化是随机的,所以故障发生的时间是随机的,故障前产品的次品率也是随机的。为了能够对这种高度随机的生产模型进行求解,本文采用近似的处理方法,首先确定系统故障的平均时间,然后据此求解各类成本、生产利润和周期时长。
假设在
时,退化量
首次大于L。记
是系统故障时已运行的时长,即
。则,在
内系统发生故障的条件下,
的分布函数为:
(11)
的期望为:
. (12)
在系统发生故障的情况下,一个生产周期内涉及的各类成本包括:次品报废成本
、库存成本
、纠正性维修成本
、缺货损失
和产品检验成本
。故,总成本为:
. (13)
1) 次品报废成本
在情形2下,一个生产周期内的平均生产时长为
。因此,次品报废成本可表示为:
(14)
由于
,且当
时,
。故在
的条件下,有:
(15)
其中
,
由伽马过程的独立增量性,
。从而
(16)
于是,
。
代入式(15),求得在
的条件下,有:
(17)
对式(14)两边同时求期望,得次品的平均报废成本为:
(18)
其中
为情形2下生产的平均次品总数。
2) 库存成本
与情形1类似,库存分为生产过程中库存和生产结束后库存两部分。在生产过程中,库存成本可表示为:
(19)
故,生产过程中的平均库存成本为:
(20)
当系统故障时,生产停止运行。此时,最大的平均库存产品数为:
。与情形1类似,在生产过程结束后,销售清空最大库存的平均库存成本为:
(21)
故,总库存成本为:
(22)
3) 纠正性维修成本
在系统发生故障时,通过纠正性维修对其进行彻底修复,将纠正性维修成本记为常数
。
4) 缺货损失
由于系统发生故障后,立即进行纠正性维修。因此,停机的时间取决于纠正性维修持续的时长
和库存产品被销售清空的时间
。
设纠正性维修时长
服从威布尔分布,其概率密度为
。与情形1类似,平均缺货损失为:
(23)
5) 检验成本
在情形2下,批量产品被部分生产,检验成本
等于单位产品检验成本
和生产的产品总数
的乘积,即
,
为随机变量。故,平均检验成本为:
(24)
4. 平均利润模型
生产加工的合格品按需求率全部发往市场销售。在情形1下,平均销售的产品总数为:
;在情形2下,平均销售的产品总数为:
。记单位产品的销售价格为R,则,一个生产周期内获得的利润是销售额和总成本的差,平均利润为:
(25)
另外,在情形1下,一个生产周期的时长可表示为
,这是一个随机变量,对
求期望,得情形1下一个生产周期的平均时长为:
(26)
情形2下,一个生产周期的时长可表示为
。
故,情形2下一个生产周期的平均时长为:
(27)
因此,一个生产周期的平均时长为:
(28)
综上所述,一个生产周期内,单位时间获取的平均利润为:
(29)
5. 数值计算
假定某产品的市场需求一直比较稳定,在生产加工过程中,系统随着运行逐渐发生退化,退化服从伽马过程。根据退化量是否达到故障阈值,分别采用预防性维修和纠正性维修两种方案,维修时长服从威布尔分布。以批量产品为单位组织生产。为了制定最佳的生产计划,先确定模型参数值,如表1所示。
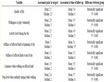
Table 1. Model parameters and their values
表1. 模型参数及其取值
根据式(29),寻找最优的ERT及对应的Q,P,寻优算法步骤如下:
Input:
,
,D,
,
,
,a,
,
,
,
,
,
,
,
,
,
,R。
Step 1:设置Q和P的搜索范围
,
;
Step 2:令
,
;
Step 3:分别计算
;
Step 4:根据式(25)、(28)、(29)分别计算
、
和ERT;
Step 5:记录ERT及Q,P;
Step 6:如果
,则令
,
,并返回Step 3;
Step 7:如果
,则令
,
,并返回Step 3;
output:输出最大的单位时间平均利润
及对应的Q,P。
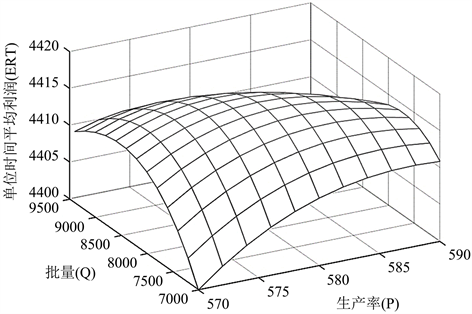
Figure 1. The effect of batch and productivity on average profit per unit time
图1. 批量、生产率对单位时间平均利润的影响
批量、生产率对单位时间平均利润的影响关系如图1所示。由图1知,单位时间平均利润ERT的最大值是存在的。将表1中的参数值代入式(29),采用for循环遍历搜寻方法,遍历网格内的所有的参数点,找到全局最优解,通过MATLAB编程计算得:最佳批量
,最佳生产率
,单位时间平均利润
。
6. 灵敏度分析
为了进一步分析模型参数变化对最佳决策方案的影响,作灵敏度分析如下。
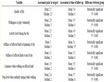
Table 2. The influence of L on decision variables
表2. L对决策变量的影响
由表2知,当故障临界阈值L减小时,最佳批量
逐渐减小,最佳生产率
逐渐增大,计划生产加工的时长
逐渐减小,单位时间平均利润ERT逐渐减小。
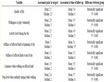
Table 3. The influence of ch on decision variables
表3. ch对决策变量的影响
由表3知,当单位时间库存成本
增大时,最佳批量
先逐渐减小,然后逐渐增大,最佳生产率
逐渐减小,计划生产加工的时长
逐渐增大,单位时间平均利润ERT逐渐减小。
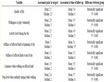
Table 4. The influence of cs on decision variables
表4. cs对决策变量的影响
由表4知,当单位产品缺货损失
增大时,最佳批量
逐渐增大,最佳生产率
保持不变,计划生产加工的时长
逐渐增大,单位时间平均利润ERT逐渐减小。
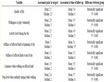
Table 5. The influence of cre on decision variables
表5. cre对决策变量的影响
由表5知,当单位次品报废成本
增大时,最佳批量
逐渐减小,最佳生产率
保持不变,计划生产加工的时长Δ逐渐减小,单位时间平均利润ERT逐渐减小。
7. 总结
本文研究了在市场需求率不变的情况下,生产计划和维修方案的决策问题。讨论了系统的随机退化过程对运行状态及产品质量的影响,根据退化是否导致系统故障,分别采用预防性维修和纠正性维修两种方案。为了能够对这种高度随机的生产模型进行数值求解,通过计算各类成本的均值及生产周期的平均时长,提出以批量和生产率为决策变量的平均利润模型。灵敏度分析讨论了模型参数对决策变量和单位时间平均利润的影响。研究表明:故障阈值、单位时间库存成本的变化对最佳批量、最佳生产率都有较大影响;单位产品缺货损失、单位次品报废成本的变化对最佳批量的影响较大,对最佳生产率没有影响。