1. 引言
随着轨道交通车辆设计与制造技术的发展,铝合金材料在轨道交通车辆上的应用越来越广泛。据统计 [1] [2],目前铝合金材料用量占整车总质量约30%,时速80 Km以上城轨车辆车体的制造基本采用铝合金板材、型材拼焊的技术方案。轨道交通常用铝合金包括6005A、6082、5083、7020等 [3] [4] [5],这些材料的应用极大地推动了轨道交通车辆的轻量化。
随着车辆运行速度的提高和车辆功能需求逐步增加,在车辆轻量化与结构安全双重需求的背景下,车辆设计、制造等方面的要求逐步提高,同时车辆结构的服役性能也受到了广泛关注 [4] [5]。在实际应用过程中,铝合金材料或结构不可避免地会受到焊接热、残余应力、外加载荷和腐蚀环境等因素的影响 [5] [6] [7]。因此,合金材料的力学性能、耐蚀、抗疲劳等性能等直接决定了结构服役寿命。
前期的应用经验表明,Al-Zn-Mg系合金尽管强度较高,然其焊接接头的抗应力腐蚀性能较差,大量的应力腐蚀开裂案例也见诸报道,因而限制了该系列合金的应用 [8] [9] [10] [11] [12]。因此,针对焊接结构件的故障机理、受力情况及疲劳寿命等方面进行研究,探明结构的失效机理,对拓宽该系列合金的应用,保障列车结构安全等方面具有重要意义。本文以城轨车辆用某型铝合金框架结构故障件为研究对象,探明了该结构的故障原因,同时结合材料组织性能和有限元分析,揭示了该故障结构的失效机理。本文的研究结果可为轨道交通用铝合金结构的设计与制造提供有益参考。
2. 试验材料与方法
2.1. 试验材料
本文的研究对象为城轨车辆某型铝合金框架结构故障件,该结构为铝合金圆管拼焊而成,经一段时间(约2~3年)服役后,发现该结构件上出现2处裂纹,裂纹位于该结构件的转角处,与焊缝位置相近,如图1所示,为便于后文描述,将左侧裂纹标识为裂纹1,右侧裂纹标识为裂纹2。该结构件所用材料为Al-Zn-Mg合金,其化学成分如表1所示。
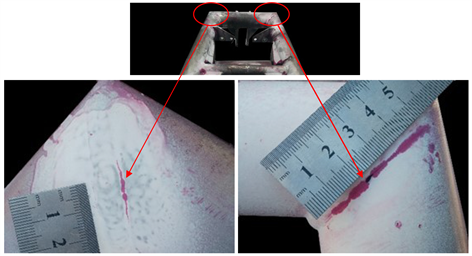
Figure 1. Sketch of failure locations of the failure structure
图1. 故障件及故障位置示意图
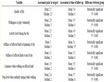
Table 1. Chemical compositions of the based alloy of the failure structure
表1. 故障件材料的化学成分
本文针对该结构件故障位置展开微观组织检测分析,同时针对该件未发现故障的位置开展了力学性能和微观组织检测分析。此外,为深入研究该故障件的故障机理,针对该结构件及其服役工况开展了有限元计算。
2.2. 研究方法
金相制样首先在构件上相应位置取样,经不同粒度砂纸打磨、抛光后,采用Olymbus光学金相显微镜观察裂纹形貌,随后经kaller试剂腐蚀再重复观察,以确定裂纹与晶粒组织之间的关系;扫描电镜显微组织试样的制样程序与金相组织观察一致,显微组织的观察采用Zessis M10扫描电镜观察,加速电压为120 KV;断口试样经超声波清洗后直接置于电镜中观察;透射电镜试样依次经人工减薄、机械减薄至70~85 μm后,进行电解双喷减薄穿孔。双喷电解液配比为:30% HNO3 + 70% CH3OH,电解电压为25 V,采用定时向电解槽中加入液氮的方法使电解温度维持在−25℃左右。透射电镜组织分析在FEI TECNAI G2 20分析电镜上进行,加速电压为200 KV。
晶间腐蚀根据GB/T7998-2005《铝合金晶间腐蚀测定方法》标准,试样采用松香将非实验面包覆,将主实验面在 57.0 g/L NaCl + 10 mL/L H2O2溶液浸泡中6 h后,沿横截面切开,按金相制样程序制样,再观察最大腐蚀深度。
有限元分析采用hypermesh 2021软件建模和前处理;在仿真建模过程中,分别按静强度工况(加速度,纵向3 g,横向1 g,垂向1.5 g)和疲劳工况(载荷幅值35 N,叠加幅值3.8 N,载荷周期0.37 s) [13] 施加载荷。采用ANSYS mechanical软件对该构件工作过程中的应力分布情况和疲劳寿命进行仿真计算。
3. 结果与讨论
3.1. 失效分析
3.1.1. 断口分析
为分析2处裂纹的断裂类型,分别从两处裂纹贯穿位置取断口试样,采用扫描电镜进行对断口进行观察,所得结果分别如图2和图3所示。从图2中可见,裂纹1断面可见明显呈贝壳状纹路,将局部视场放大后,可见呈周期性分布的纹路,这种特征与合金疲劳断面的疲劳贝纹线和疲劳辉纹特征相吻合。此外,在裂纹1对的断面放大视场可见部分腐蚀产物。
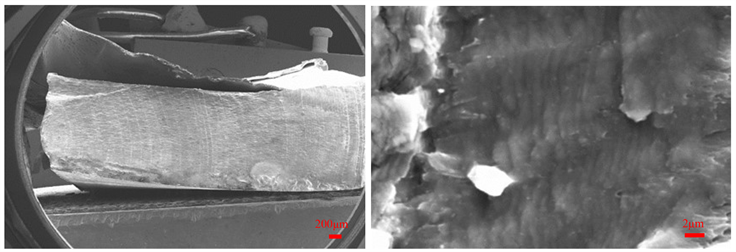
Figure 2. SEM micrographs of the fracture surface of crackle 1
图2. 裂纹1断面扫描电镜分析结果
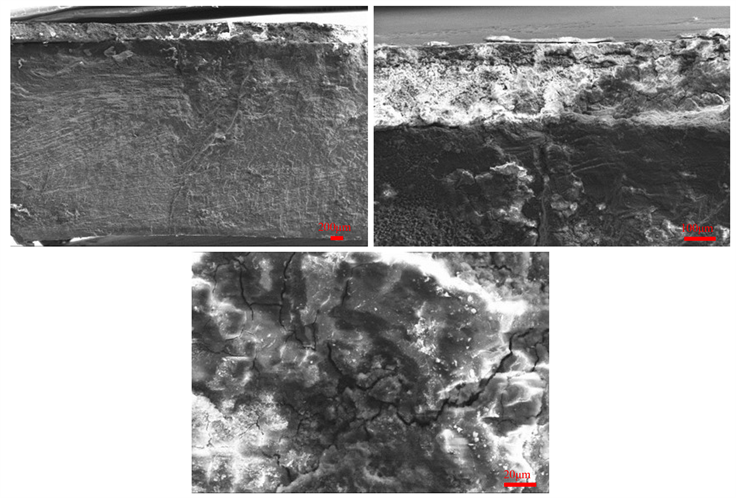
Figure 3. SEM micrographs of the fracture surface of crackle 2
图3. 裂纹2断面扫描电镜分析结果
从裂纹2的断面上来看,在低倍视场上可见呈河流状的断面特征,仔细观察可见这些河流状的纹路近似指向断面次表层某一点,初步判断该处断裂也与疲劳断裂相关。通过对逐级放大的视场进行观察可见,裂纹2断面发生了较严重的腐蚀,同时可见部分二次裂纹。
通过对裂纹1、裂纹2的断面分析可知,2处裂纹均与疲劳断裂相关,同时可见明显的腐蚀痕迹,可初步判断该框架结构的故障与合金的腐蚀疲劳开裂紧密相关。
3.1.2. 金相组织分析
为进一步研究2处裂纹的性质,分别从2处裂纹未贯穿位置取横截面样进行金相组织分析,所得结果如图4和图5所示。从图3中可见,试样横截面上裂纹1从焊缝处起始,沿热影响区向试样内部扩展。从裂纹扩展路径与晶粒组织的位置关系来看,裂纹路径主要呈穿晶开裂特征,同时也可见少量的沿晶开裂。而从裂纹2的横截面上来看,该处发生了较严重的局部腐蚀,同时可见少量网状晶界,此外还可见主裂纹周边存在二次裂纹。结合断口组织特征分析,该铝合金框架结构故障类型为环境腐蚀和疲劳耦合作用引起的开裂。
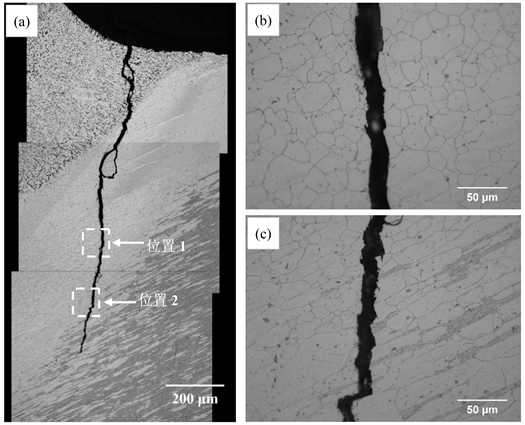
Figure 4. Optical micrograph of crackle 1
图4. 裂纹1及其周边金相组织
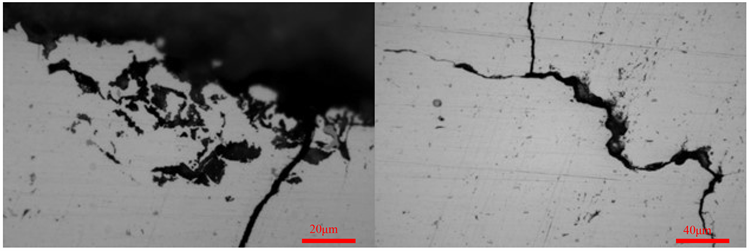
Figure 5. Optical micrograph of crackle 2
图5. 裂纹2及其周边金相组织
3.2. 材料的组织性能分析
3.2.1. 微观组织
为研究该铝合金框架结构开裂的微观机理,从该试件上未裂位置取样进行光学金相组织和透射电镜显微组织分析,所得结果如图6所示。从图中可见,试件材料的表层分布着一层约200 μm厚的粗晶层,同时在局部位置还可观察到局部腐蚀。从金相组织的观察结果来看,一方面,由于粗晶层内部的晶界均大角度晶界,不利于Al-Zn-Mg合金的耐腐蚀性能;另一方面,可直接观察到材料表层发生的局部腐蚀现象,这些腐蚀坑是应力集中的区域,容易发展成为裂纹源。此结果进一步佐证了该框架构件的裂纹与环境腐蚀作用紧密相关。
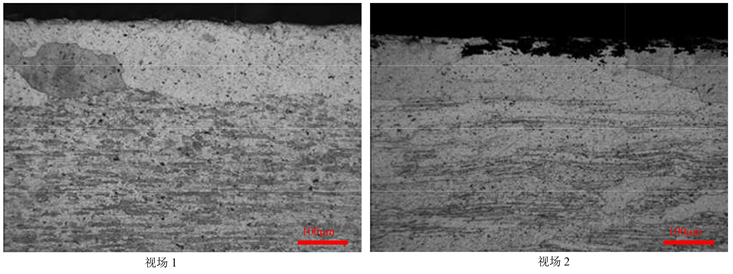
Figure 6. Optical micrograph of the alloy
图6. 未裂位置材料光学金相组织
分别在开裂位置和未裂位置取样进行透射电镜显微组织分析,值得说明的是,开裂位置取样在距离裂纹1 mm处平行于裂纹取样。所得的观察结果如图7所示。从图中可见,未开裂部位合金晶粒内部可观察到大量呈弥散分布的析出相,这些析出相尺寸分布在5 nm~20 nm范围内;其晶界上可见明显呈连续分布的析出相。而在开裂位置样品晶内几乎观察不到析出相的衬度,在晶界位置可见粗大且连续分布的析出相,这种特征不利于材料的耐蚀性能;而从失效位置与焊缝的关系来看,裂纹均处于焊接热影响区,从上述结果可推断,由于焊接热影响,晶内析出相可能在焊接过程中重新溶入了基体,而晶界位置又在焊接冷却过程中,重新析出了粗大的析出相。这种特征,显然是对强度与耐蚀性能均有较大不利影响。因此,该构件的失效的微观机理在于焊接热输入较大,导致热影响区材料析出相溶解,同时在随后的冷却过程中,在温度较高的阶段,晶界处析出粗大的析出相,同时由于焊接接头在较短时间内就冷却到了室温,大量晶内的溶质原子还来不及析出,使得该处强度较低、耐蚀性较差。
3.2.2. 晶间腐蚀性能
为进一步研究材料本身的耐腐蚀性能,对材料进行了晶间腐蚀性能检测分析,所得结果如图8所示。从图中可见,在本文的试验条件下,该材料表面发生了明显的局部腐蚀,腐蚀坑内可见一定网状晶界,最大腐蚀深度约为94 μm,其耐晶间腐蚀等级为3级。
3.3. 有限元分析
采用有限元对该框架结构的静强度和疲劳寿命进行仿真计算分析,所得结果如图9和图10所示。从图9可见,该结构所受最大应力的位置出现在该结构的焊接转角处,其最大应力约为126 MPa,应力集中位置与实际开裂位置吻合较好;图10为该框架结构焊缝疲劳寿命分布,从图中可见,在疲劳载荷工况下,最小寿命同样也出现在焊接转角处,其最小寿命约为105.2次,约合74万Km,与该框架结构的实际寿命(2~3年)基本相符。
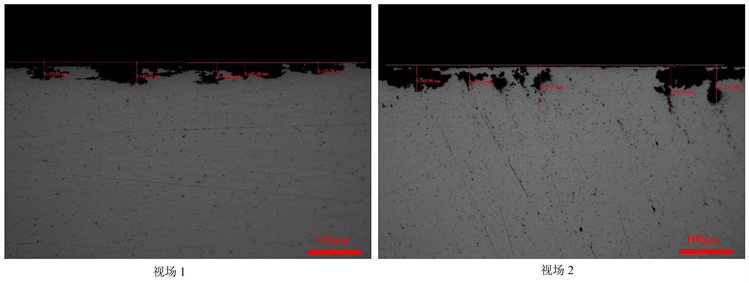
Figure 8. IGC micrograph of the no cracking location
图8. 未裂位置晶间腐蚀照片
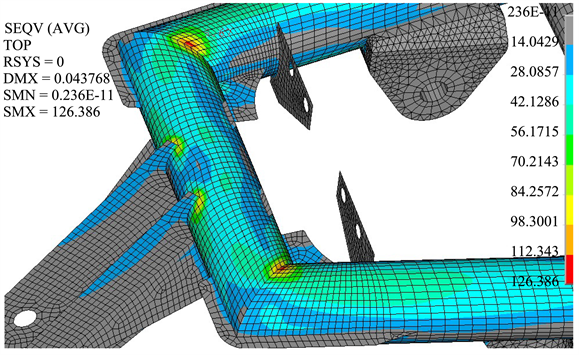
Figure 9. FEM results of statistic strength
图9. 结构静强度工况有限元分析结果
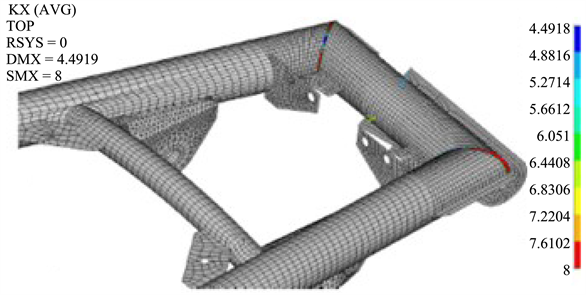
Figure 10. FEM results of fatigue life of the structure
图10. 结构疲劳寿命有限元分析结果
4. 结论
本文针对城轨车辆某型铝合金框架结构故障件进行了分析,采用光学显微、扫描电镜等手段分析了结构件失效机理;同时针对未开裂位置的材料进行了组织性能分析,最后采用有限元仿真分析方法研究了该结构的应力分布与疲劳寿命,得到如下结论:
1) 扫描电镜和金相检测结果表明,故障件断口可见疲劳辉纹,开裂位置可见较严重的局部腐蚀,主裂纹穿晶开裂特征明显,同时可见少量沿晶开裂和二次裂纹。因此可以判定本文所述铝合金框架结构故障类型为环境腐蚀和疲劳耦合作用引起的开裂,即腐蚀疲劳失效。
2) 未开裂位置检测分析结果表明,试件材料耐晶间腐蚀等级为3级,最大腐蚀深度约94 μm。其原因在于材料表面存在约200 μm厚的粗晶层,同时其晶界析出相呈连续分布,这些特征均不利于材料耐腐蚀性能。
3) 有限元分析结果表明,应力集中位置、疲劳最低寿命位置与实际开裂位置吻合较好,最大应力约126 MPa,最低寿命约105.2 km,与实际寿命基本吻合。
4) 该构件的失效的微观机理在于焊接热输入较大,导致热影响区材料析出相溶解,同时在随后的冷却过程中,由于温度较高晶界处析出粗大的析出相,同时由于冷却时间相对较短,大量晶内的溶质原子还来不及析出,形成晶内析出相较少,而晶界粗大析出相连续分布的组织特征。这种特征的强度较低耐蚀性较差,因而在疲劳载荷和腐蚀环境的作用下容易失效。
NOTES
*通讯作者。