1. 引言
近五年来,页岩气调查评价项目探明页岩气地质资源量超40 × 1012 m3,技术可采资源量约9 × 1012 m3,经济可采资源量约5 × 1012 m3,页岩气发展潜力巨大 [1]。随着页岩气开采深入,地面集输系统页岩气管道腐蚀问题越来越受到关注。各种原因产生的管道腐蚀容易造成金属管道腐蚀失效,影响页岩气的安全生产,造成严重的经济损失。某页岩气平台出气管道发生天然气泄漏燃烧,现场开挖调查结果为管道焊口开裂。为研究探明其开裂原因,所以系统地分析该失效管段理化性能,为针对性的管道运行防控措施提供技术支撑。
2. 概述
2.1. 气田情况概述
某页岩气平台出站管道规格为D168.3,材质为L360N无缝钢管,设计压力8.5 MPa。管道于近年正式进气投运生产,管道运行压力4.5~5 MPa。
该段管道输送气质以CH4为主,CH4含量97.86%,CO2含量1.468%,其气质分析结果见表1。
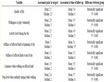
Table 1. The component of the perforation in certain shale gas platform
表1. 某页岩气平台气质组分表
2.2. 管道失效情况概述
某页岩气平台出站管道出现天然气泄漏燃烧,经关闭该平台来气并进行氮气置换该管道内天然气后火焰熄灭。经现场对泄漏点开挖发现,泄露原因为焊口开裂造成。失效管段位置及现场开挖检查见图1、图2。
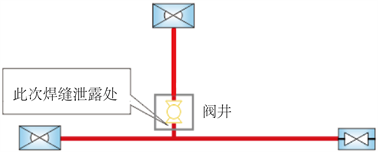
Figure 1. The position schematic of the corrosioin gas tubulation
图1. 失效管段所处位置示意图
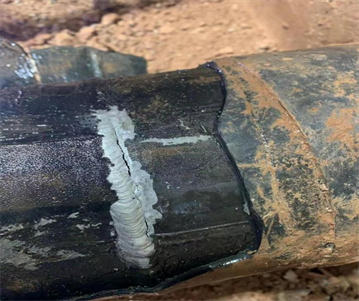
Figure 2. The picture of the welded crack on the scene
图2. 现场焊口裂纹照片
2.3. 管道失效原因概述
基于失效管段焊缝氢含量分析,管段焊缝氢含量检测结果为1.887~2.775 ml/100g,超出临界氢含量。
其结果表明在已存在开裂的情况下,焊缝、热影响区中氢含量仍超过氢致开裂临界值十数倍;冷却过程中大量的溶解氢来不及逸出而被保留在金属中,处于过饱和状态氢会极力扩散,氢的扩散会诱发材料中三向应力区微裂,大量微裂断续合并就形成了宏观裂纹。
3. 失效管段样品分析
3.1. 化学成分分析
依据GB/T 4336-2016《碳素钢和中低合金钢火花源原子发射光谱分析方法(常规法)》对失效焊缝进行化学成分分析,分析结果见表2。由表2可知,该取样母材的化学成分符合GB/T 9711-2017《石油天然气工业管线输送系统用钢管》中对L360N PSL2无缝钢管的要求,焊缝成分符合焊接材料质量证书(DHS/YFB.05)的要求。
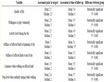
Table 2. The component analysis table of the corrosioin gas pipeline’s texture
表2. 失效管段材质成分分析表
3.2. 金相组织分析
对失效管段焊缝处不同的两处部位参照GB/T 13298-2015《金相显微组织检验方法》金相分析,结果见图3、表3。从图3、表3可知,焊缝的金相组织为铁素体和珠光体;熔合区的金相组织为粒状贝氏体;细晶区的金相组织为多边形铁素体和马氏体。该失效管段焊缝金相组织性能符合相关标准的规定。
(a) 焊缝
(b) 熔合区
(c) 细晶区
Figure 3. The metallographic structure analysis of the corrosioin gas tubulation’s welding line
图3. 失效管段焊缝金相组织分析
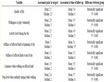
Table 3. The metallographic structure analysis result of the corrosioin gas tubulation’s welding line
表3. 失效管段焊缝金相组织分析结果
3.3. 宏观分析
失效管段样品目视观察其内壁无腐蚀痕迹,见图4,焊缝两侧根部位置有多条裂纹,环焊缝两侧管材壁厚存在差异,焊缝左右两端管子壁厚相差0.1~1.8 mm,内表面小壁厚端焊趾可见裂纹萌生,呈树枝状分布,主裂纹附件还存在较多二次裂纹,主要呈穿晶形貌,局部呈现沿晶形貌 [2]。焊缝区域有错边,最大错边量达3 mm,见图5。
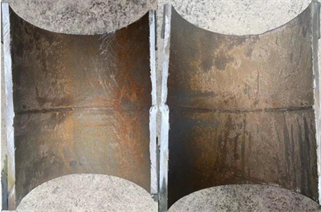
Figure 4. The macroscopic feature of the corrosioin gas tubulation’s wall inside
图4. 失效管段内壁宏观形貌
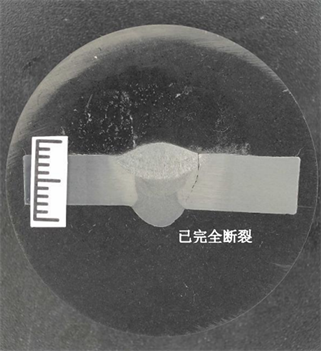
Figure 5. The macroscopic feature of the corrosioin gas tubulation’s welding line
图5. 失效管段焊缝宏观形貌
3.4. SEM微观分析
从失效管段焊缝开裂处取样,采用TESCAN VEGA II扫描电子显微镜对裂纹进行截面、断面的微观形貌观察及分析。
1) 裂纹截面微观分析
使用扫描电子显微镜观察试样截面裂纹、气孔、组织。结果如图6所示。从图中可以看出,裂纹起裂于根焊焊缝根部的热影响区,裂纹扩展为穿晶和沿晶混合型,扩展路径上存在多条分支,且分支裂纹多止裂于焊缝熔合区 [3]。焊缝中存在较多显微气孔,焊缝根焊氩弧焊区显微气孔较多,气孔接近圆形、表面光滑,且多位于先共析铁素体组织上,初步判断为显微氢气孔。
(a) 焊缝根部裂纹
(b) 焊缝根部气孔
(c) 母材裂纹
(d) 熔合区裂纹
Figure 6. The SEM microscopic observation of the corrosioin gas tubulation
图6. 失效管段SEM微观观察
2) 裂纹断面微观分析
对纵向裂纹的扫描电镜观察,发现:
裂纹起源管壁内壁,已基本贯穿整个管壁截面,仅外壁部分有少量连接,见图7。
对图7三处开源区观察发现裂纹为多点线性发源,呈放射状向四周扩展,可观察到多条放射性撕裂棱,起源区可观察的一处片状夹杂,但不是初始的裂纹源,对开裂影响有限。
裂口断面表面,大部分区域都覆盖有较厚的氧化物,但仍能分辨出整个断口为脆性准解理和解理断裂特征,解理断口分布区域与金相观察到的层状组织的区域基本一致。
3.5. 腐蚀产物分析
使用体式显微镜与扫描电子显微镜观察失效管段焊缝断面区域腐蚀产物,并使用EDS测定腐蚀产物成分。用刀片刮取失效管段焊缝断面区域腐蚀产物进行XRD测试,结果见图8、图9、表4。
对腐蚀产物横截面进行EDS线扫描,如图9、表4所示,纵向裂纹开裂面覆盖大量较为致密的腐蚀物,EDS表面腐蚀物主要为氧化物,其中的危害元素S、P等未见异常,个别区域有低含量Cl元素应为污染物。
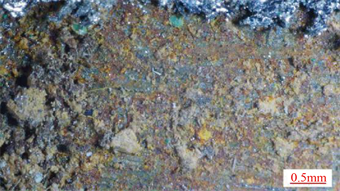
Figure 8. The surface morphology of the corrosion products
图8. 腐蚀产物表面形貌
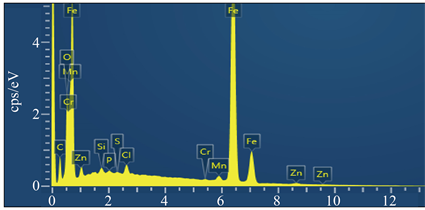
Figure 9. The eds figure of the corrosion products
图9. 腐蚀产物eds图
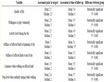
Table 4. The eds table of the corrosion products
表4. 腐蚀产物eds表
根据图10腐蚀产物XRD检测结果显示,腐蚀产物的主要成分为Fe3O4和Fe2O3;根据物相分析结果得可知,失效管段焊缝断面覆盖物主要为铁的氧化物或砂砾成分,并未检测到高含量腐蚀产物特征,符合EDS的实验结果。
3.6. 失效管段焊缝氢含量分析
对失效管段焊缝区氢含量检测结果如表5所示。按氢气密度0.0899 g/L折算,1 ppm相当于1.11 ml/100g。焊缝区域的氢含量均超出临界氢含量。
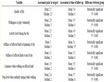
Table 5. The hydrogen concent of the welding line, heat affected zone
表5. 焊缝、热影响区氢含量
4. 失效原因分析
1) 管段样品焊缝存在一定程度的焊接余高超标、咬边、焊瘤、错边、烧穿、未焊透、焊缝成型欠缺等现象,这些问题会引起焊缝应力集中 [4]。
2) 管段内壁及裂纹处腐蚀产物主要为Fe3O4。
3) 管段焊接热影响区存在大量裂纹,裂纹多数起于焊缝根部附近热影响区的过热区和相变重结晶区(正火区),向四周扩展,部分裂纹贯穿管壁;裂纹外扩展路径上有大量细小分支,但均止裂于熔合线附近;大部分裂纹扩展路径均位于焊接热影响区内。裂纹起裂和扩展均为沿晶和穿晶混合型,裂纹尖端可见大量沿铁素体晶界分布的小块状珠光体,裂纹优先沿珠光体区扩展。裂纹表现为脆性准解理断裂特征 [5]。
4) 管段焊缝氢含量检测结果为1.887~2.775 ml/100g,超出临界氢含量。
集气管线焊后检查并未发现焊缝区域存在裂纹,但运行数月后发现多条焊缝存在裂纹,根据裂纹出现的时间,结合本次管段样品分析检测结果,认为管线裂纹为焊接冷裂纹中的延迟裂纹,且为常见的根部裂纹,管道焊缝的应力集中和焊缝中氢含量超标会促进裂纹的发展。
根据焊接记录和对当地天气的追溯,该部分管道在焊接时多日处于阴雨天气,由于野外工作且长时间处于阴雨天,因此怀疑管道内壁和坡口区域很容易存在大量铁锈,焊接时这些铁锈很难清除特别是管道内铁锈,富含水的铁锈进入熔敷金属中导致焊缝氢含量超标。同时检查发现焊缝中存在大量显微近乎球形的微小气孔(焊评无法发现),符合焊缝氢气孔的特征;对焊缝氢含量检查,结果也表明在已存在开裂的情况下,焊缝、热影响区中氢含量仍超过氢致开裂临界值十数倍;冷却过程中大量的溶解氢来不及逸出而被保留在金属中,处于过饱和状态氢会极力扩散,氢的扩散会诱发材料中三向应力区微裂,大量微裂断续合并就形成了宏观裂纹 [6]。
5. 结论及建议
1) 基于以上实验结果,认为该失效管段材质的金相组织,化学成分均符合GB/T 9711-2017《石油天然气工业管线输送系统用钢管》对L360N材料的相关规定,材料本身的资料不是诱发焊缝开裂的因素。
2) 通过对实验结果分析认为失效管段裂纹为焊接冷裂纹中的延迟裂纹,管道焊缝的应力集中和焊缝中氢含量超标会促进裂纹的发展。
3) 针对以上实验结论,我们建议扩大同批次同类型管道焊接接头质量的抽查范围,及时发现缺陷并进行处理,同时做好集气管道运行过程中的跟踪检测工作 [5]。
4) 强化管道产品的质量控制和管道工程的验收管理,切实实现管道“优生优育”。严格执行标准,加强管道焊接过程质量控制。同时,不断强化施工过程中的管理监督,尤其重点提升不等壁厚管道焊接质量。从而切实消除焊接质量对管道本质安全的影响,遏制安全事故的发生。