1. 拉铆钉技术发展及应用
拉铆钉又叫做虎克螺栓(Huckbolt,以其发明者LouisHuck的名字命名),最早是为航空航天工业开发,如图1所示 [1]。从单一领域的新发明开始,拉铆钉技术发展至今已有七十余年的历史,并且由于其自身优势而得到越来越广泛的应用。
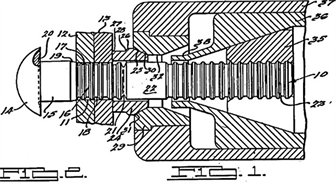
Figure 1. Patent specification of huckbolt [1]
图1. 虎克螺栓专利图示 [1]
1.1. 发展进程和应用
为适应不同结构和连接需求,拉铆钉从最初的简单形式逐步发展,衍生出多种类别,为了方便在飞机不开敞部位进行铆接,并保证其强度、可靠性和寿命,美国于20世纪70年代研制了机械锁紧鼓包型抽芯铆钉,我国于1999年成功研制了国产的该型铆钉 [2];为了追求轻量化、高热强度和耐腐蚀性,我国在20世纪90年代成功研制了钛合金抗拉型环槽铆钉 [3]。目前常用的拉铆钉类别有短尾钉、拉断钉、抽芯铆钉和防漏铆钉等,如图2所示。
与此同时,在工艺和检测等方面,拉铆钉技术也取得了长足的进步。为克服安装噪声,国外于20世纪70年代研究出了无声拉铆工艺,我国也从1975年开始组织研究 [4];为了方便对拉铆钉进行质量检查,刘廉恒基于LabVIEW平台,设计了拉铆钉横向振动试验台 [5];为解决在役环槽铆钉夹紧力检测的问题,左世斌等基于声弹性原理,提出了利用超声波间接检测的方法 [6];王立洋优化了A-286合金抗拉型抽芯铆钉钉套的局部退火工艺,研究了其制造设备,实现了该型铆钉的国产化 [7]。
拉铆钉早期主要应用于飞机结构,每架飞机所需的拉铆钉约占全部紧固件的40%,如大型客机空客A380每架会使用超过100万颗拉铆钉。20世纪70年代,拉铆钉开始应用于铁路车辆的心盘连接并沿用至今,我国引入了该技术,并逐步将其应用于C70和C80型货车 [8]。除此之外,各种形式的拉铆钉还广泛应用在卡车、升降机和太阳能发电等领域,如图3所示 [1] [9]。
1.2. 原理和特点
虽然现有的拉铆钉种类繁多,但主要使用的是如图4所示的两种拉铆钉。术语“拉铆钉系统”与术语“螺栓总成”类似,它是一种两件式紧固件,由一颗特定强度等级的拉铆钉和相应的套环组成,主要由碳钢材料制成。和螺栓一样,拉铆钉的强度等级有5.8、8.8和10.9级三种,公制尺寸拉铆钉的公称直径范围一般在4.8~36 mm。
(a)
(b)
(c)
(d)
Figure 3. Application fields of lockbolts. (a) Truck; (b) Rail vehicle; (c) Ship lift; (d) Solar power plant
图3. 拉铆钉的应用领域。(a) 卡车;(b) 轨道车辆;(c) 升降机;(d) 太阳能发电

Figure 4. Pull off lockbolt (left) and short tail lockbolt (right). ① Collar, ② Pintail, ③ Locking groove, ④ Shank, ⑤ Head, ⑥ Breaking groove
图4.“拉断型”(左)和“短尾型”拉铆钉(右)。 ① 套环, ② 尾牙, ③ 锁紧槽, ④ 钉杆, ⑤ 钉头, ⑥ 拉断槽
钉杆上的锁紧槽用于与套环配合安装,末端的尾牙则用于连接安装工具;“拉断型”拉铆钉的尾牙会在达到装配所需的拉伸载荷后在预定的断点断开,“短尾型”拉铆钉的尾牙在装配完成后则仍在铆钉上。与传统螺栓连接以控制扭矩的方式将螺栓和螺母拧紧在一起的装配方式不同,拉铆连接的装配原理是通过工具对系统施加拉伸载荷,将各部件拉在一起,使由更软材料制成的套环发生塑性变形,将其压入钉杆上的环槽中,这是一种永久变形,且装配完成时铆钉已经被施加了预紧力。拉铆钉系统的装配过程大致可以分为四个阶段,图5以“短尾型”拉铆钉系统为例,说明了该过程 [10]。

Figure 5. Assembly process for a short tail lockbolt system [10]
图5.“短尾型”拉铆钉系统的装配过程 [10]
装配完成后,拉铆钉中产生了永久的预紧力,装配预紧力对保证连接的可靠性至关重要。拉铆连接的显著优点是,相比于螺栓连接,其装配预紧力的分散程度更低,且不会发生自松。德国指南VDI 2230 Part 1 [11] 《高强度螺栓的系统计算》对机械工程中的螺栓连接定义了紧固系数αA的概念,表示在一组装配完成的螺栓连接中,装配预紧力的最大值FMmax和最小值FMmin之间的分散程度,其值由式(1)确定。指南 [11] 表明,螺栓连接αA的值在1.1~4之间。2017年德国焊接学会发布的针对拉铆连接计算的技术公报DVS/EFB 3435-2 [12] 参考这一概念,定义拉铆连接的αA = 1.05,表明其预紧力的分散程度最多在5%。文献 [1] [9] [13] 均用实验的方法证明了这一说法,得到多条拉铆钉的预紧力–时间曲线,表明其预紧力的变异系数(一组铆钉预紧力的标准差值/平均值)均在5%以内,如图6所示。同时,图6亦能表示拉铆钉的装配过程。
(1)
(a)
(b)
Figure 6. Preload-time curve for lockbolts. (a) [1] [13]; (b) [9]
图6. 拉铆钉的预紧力–时间曲线。(a) [1] [13];(b) [9]
相比于承受轴向载荷,当螺栓类连接承受交变横向载荷时,自松现象要严重得多。Junker开发了一种振动实验台,可以通过对螺栓连接施加循环的横向位移来研究其自松行为 [14]。测量一定循环次数下的预紧力下降值,如图7所示是通过实验确定的相对预紧力和载荷循环次数间的关系,该图说明了在相同条件下,非固定螺栓连接、有垫圈的螺栓连接和拉铆连接的松动行为。由图7分析可知,拉铆钉没有自松效应,它是一种防振动紧固件 [1] [9],无需对其进行额外的紧固,这为拉铆连接的可行性提供了便利,也提高了它的经济性。
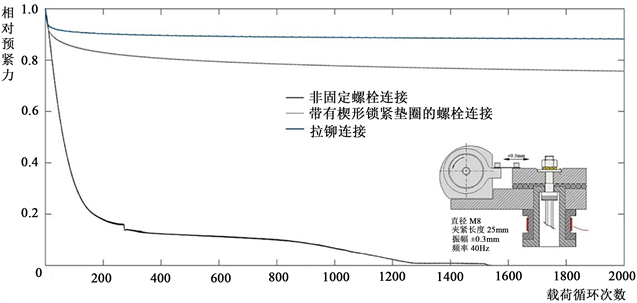
Figure 7. Comparison of the securing effect of different fasteners [9]
图7. 不同紧固件的紧固效果 [9]
2. 拉铆连接可靠性评价方法
在工程中通常使用VDI 2230指南 [11] [15] 去评价传统螺栓的可靠性,这是因为其在业内已相当成熟。但到目前为止,对于拉铆连接,只有少量文献资料可用于评价其可靠性。参考这些文献的内容,本文介绍了拉铆连接的承载特性,提出了其可靠性评价方法和具体的计算过程。
2.1. 承载特性
可以将常用的拉铆连接分为三类:承载型连接、防滑连接和预紧拉伸连接,其中前两类同属于剪切连接,如图8所示 [5] [12] [16]。剪切连接是指被连接件承受剪力的连接,而拉伸连接则承受拉力。

Figure 8. Categories for connections with lockbolts [5]
图8. 常见拉铆连接分类 [5]
防滑连接适用于承受疲劳载荷或变形较小的连接。加载初期,被连接件的位移几乎与外载荷Fv,Ed成正比增加,直到达到极限滑移载荷时,结合面间的摩擦将由静摩擦变为滑动摩擦,即当载荷继续增加时,连接将发生滑移。一旦滑移发生,铆钉就会支撑在受压的孔壁上,这便形成了承载型连接,直到达到失效载荷。所以,防滑连接不允许发生滑移,滑移即失效。对于承载型连接,当载荷增大到其极限承载能力时,伴随着塑性变形,连接将失效,其特征是钉杆被剪断或连接孔被撕裂,如图9所示;该型连接是允许在加载开始后立即发生滑移的。文献 [13] [17] 对螺栓和拉铆钉的防滑连接进行了滑移载荷实验和扩展蠕变实验,结果表明二者的承载特性相同,但由于拉铆连接的预紧力分散更小,所以其极限滑移载荷值的分散也更小,代表拉铆连接的可靠性更高。
(a)
(b)
Figure 9. Failure mode of lockbolt connection. (a) Shear connection; (b) Tensile connection
图9. 拉铆连接的失效形式。(a) 剪切连接;(b) 拉伸连接
受轴向力的拉铆钉系统的失效机制以套环剥离为特征。对一组直径相同的拉铆钉做纵向拉伸实验,它们的载荷–位移曲线呈几乎相同的过程,起初载荷和位移成线性关系,载荷超过一定值时,套环剥离并发出声响,这也被视为拉铆钉系统失效的信号,如图9所示。多次类似结果的实验表明,可以将套环的剥离解释为一种设计原则,连接失效时铆钉已经发生塑性变形,所以其能承受的极限拉伸载荷与其受力横截面的屈服点有关 [12]。
EN 1993-1-9 [18] 提供了关于紧固件连接的抗疲劳设计的信息,它根据应力范围对不同结构进行了分类。文献 [17] 对多组不同直径的螺栓和拉铆钉进行了在恒定平均应力条件下的拉伸疲劳试验,拉铆钉的试验结果为:除4个例外情况外,失效均被确定为发生在第一个承载凹槽内,观察到钉头下部断裂两次,钉杆与凹槽之间的过渡处断裂两次。当置信概率Pü = 95%、标准化斜率m = 3且循环次数NC = 2∙106时,螺栓和拉铆钉的试验结果如表1所示。结果表明,拉铆钉有更高的持续应力范围,直径较小的拉铆钉其应力范围更高,归因于尺寸效应。
螺栓和拉铆钉都属于缺口式紧固件,其几何形状会导致较高的缺口应力,降低抗疲劳性能。定义缺口系数αK为缺口应力σmax与名义应力σN的比值 [9],如图10所示为螺栓和拉铆钉的缺口系数曲线,表明拉铆钉在各个点的缺口系数均小于螺栓,这得益于其特殊的环槽几何形状和从头部到杆部较小的过渡半径。因此相比于螺栓,拉铆钉的局部应力峰值更小,在设计中允许的疲劳极限也就更高。
2.2. 可靠性评价方法
对于上述拉铆连接的几种失效形式,对应地有几种指标来评价其可靠性。
拉铆连接中的横向力是通过摩擦传递的,如果极限滑动力
始终大于横向力
,则连接不会发生滑动,即需要满足如式(2)所示的关系。
(2)
由式(3)计算。
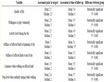
Table 1. Results of tensile fatigue test in [17]
表1. 文献 [17] 中的拉伸疲劳试验结果
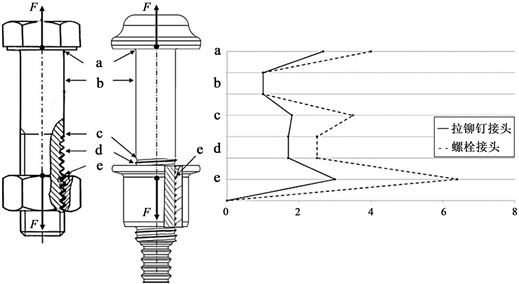
Figure 10. Notch factor curves for bolt and lockbolt connections
图10. 螺栓接头和拉铆钉接头的缺口系数曲线
(3)
式中:μTmin为结合面处摩擦系数的最小值;FKRmin为最小剩余夹紧力,由式(4)计算。
(4)
式中:FAmax为最大轴向力,如连接不承受轴向力则取FAmax = 0;
为必需的装配预紧力,由式(5)计算;
为载荷系数,由式(6)计算;FZ为由于嵌入导致的预紧力损失,由式(15)计算。
(5)
式中:As为拉铆钉的应力横截面积;
为屈服强度利用率;
为拉铆钉材料的屈服强度。
(6)
为了计算拉铆钉柔度δSRB,假设拉铆钉系统由几个单元组成,这些单元可以用不同长度li和不同横截面积Ai的圆柱体代替,如图11所示。拉铆钉总柔度可以通过将夹紧长度内和外部变形区域内的各个柔度δi相加得到,如式(7)所示。
(7)
式中:δSK为铆钉头的柔度;δSch为钉杆的柔度;δRil为未受力凹槽处的柔度;δSR为套环成型区域的柔度。
每个圆柱体单元的柔度δi由式(8)计算。
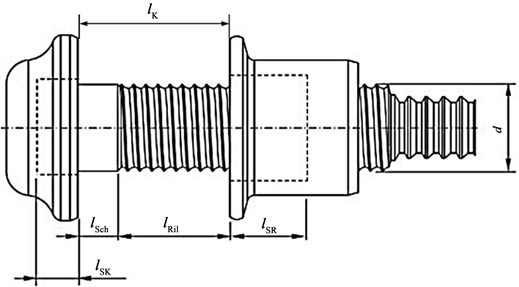
Figure 11. Division of an lockbolt system into individual cylindrical bodies and deformation areas outside the clamping length
图11. 将拉铆钉系统划分为单独的圆柱体和夹紧长度之外的变形区域
(8)
式中:ES为拉铆钉材料的杨氏模量。
计算被连接件柔度δP时,要利用到夹紧体和变形锥的概念 [11] [12],在计算前应先比较结合面处替代外径DA和变形锥极限直径DA,Gr的大小。DA一般由具体计算模型确定,DA,Gr则由式(9)计算。
(9)
式中:dW为钉头承载面的外径;lK为夹紧长度;
为变形锥的锥角。
由式(10)计算。
(10)
式中:
为长度比,由式(11)计算; 为直径比,由式(12)计算。
(11)
(12)
当
时,δP由式(13)计算。
(13)
式中:dh为孔径;EP为被连接件材料的杨氏模量。
当
时,δP由式(14)计算。
(14)
(15)
式中:fZ为嵌入量的大小,它取决于载荷的类型、结合面数量和表面粗糙度,具体数值可参考文献 [11] [12]。
在过载的情况下,应验证连接的受剪或承载压力的能力,必须证明每个剪切平面上的横向力不超过拉铆钉允许的与剪切相关的承载能力FQzulS,FQzulS由式(16)计算。
(16)
式中:τB为拉铆钉材料的剪切强度;Aτ为剪切面积。
至少取SA = 1.25的剪切安全系数,以防止由于剪切导致的断裂失效,由式(17)计算。
(17)
还应验证拉铆钉孔壁上承载的压力不超过允许的承载压力FQzulL。FQzulL受到连接中较弱部件失效的限制,所以最小板厚h是决定性的,FQzulL由式(18)计算。
(18)
式中:dτ为剪切横截面直径;Rp0.2P为被连接件材料的屈服极限。
对于套环脱落这一失效机制,应计算拉铆钉在应力截面处的最大工作应力σZmax,比较其与拉铆钉屈服点Rp0.2的大小,留有1.1的安全系数,即为了防止套环脱落,应满足如式(19)所示的关系。
(19)
σZmax由式(20)计算。
(20)
当考虑疲劳强度,即连接承受轴向交变应力时,其应力幅值由式(21)计算。
(21)
式中:FAmin为最小轴向力。
在
的循环次数下,与应力截面面积AS相关的持久极限由式(22)计算。
(22)
式中:∆σc为
时,纵向应力范围的参考值。
为保证连接不发生疲劳失效,取抗疲劳失效的安全系数
,且有:
(23)
式(23)为评判拉铆连接疲劳失效的基本准则。
2.3. 试验分析
为验证上述评价方法的可行性,在眉山车辆有限公司实验室的协助下,本文选取了强度等级10.9级的3种直径的短尾钉(M16、M20和M22)和对应孔径的工件各3套,铆接完成9套拉铆钉连接副,对其进行剪切试验。两块试验连接板的厚度均为10 mm,试验前还需在连接板侧面各画两条垂直标记线,试验设备如图12所示。
试验时将9套连接副逐个安装在三思纵横万能试验机的装夹位置,分别手动操作试验台控制手柄进行预夹紧,然后通过电脑控制油缸进行加载,待确认完全夹紧后减慢加载速度。加载过程中,观察连接副上所画的标记线是否发生错位,记录下刚发生错位时载荷的数值,之后持续加载直至连接副发生破坏,并记录破坏时的载荷大小。标记线错位表明连接发生滑移,连接副发生破坏的最早表现形式为铆钉剪断,如图13所示。
依据本文第2.2节中的评价方法,对3种不同直径的拉铆钉连接副进行理论计算,计算的主要目的是得出连接副发生滑移和破环的临界剪切载荷,与试验结果进行对比。
对于不同直径的连接副,其计算方法相同,因此以M22的铆钉为例,将计算前所需要的计算参数列于表2。
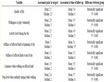
Table 2. Calculation parameters of M22 lockbolt
表2. M22铆钉计算参数
将上述计算参数代入第2.2节中的计算公式,关键计算量的数值列于表3。
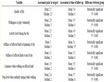
Table 3. Calculation results of M22 lockbolt
表3. M22铆钉计算结果
对3种直径的连接副的试验与理论计算结果的对比如表4所示。
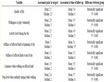
Table 4. Comparison of test and theoretical results
表4. 试验与理论计算结果的对比
对比结果表明,依据本文第2.2节中的评价方法进行理论计算得出的结果与试验结果的相对误差均在20%以内,考虑到读数误差和试验设备的误差,本文认为上述评价方法具有一定的可行性。
3. 结论与展望
拉铆钉技术由于其独特的环槽设计和安装方式,拥有装配预紧力分散小、防松性好和抗疲劳性能佳等优点,从开始在航空航天工业应用,发展至今,已在多个领域充当重要角色。拉铆连接往往只能以破坏性方式分离,这可能对临时结构不利。虽然无法重新紧固,但如果装配过程正确实施,则无需重新紧固。
现有的拉铆钉技术的可靠性评价方法比较新颖,也有一定的可行性,但还有一些问题还未完全解决,例如是否需要考虑其剪切疲劳问题,故仍有待继续研究和完善。另外,必要时也可以借助有限元分析方法进行辅助研究。