1. 引言
随着北京首钢冷轧公司高端汽车外板的增量,尤其是日系汽车板正常供货后,现有的重卷机组无法满足生产需要。某重卷机组位于两条镀锌线的出口,下线的钢卷可以直接吊运到重卷机组进行生产,既能降低倒运费用,又能减少在倒运过程中产生的次生缺陷,因此对现有重卷机组进行改造迫在眉睫。此次改造,增加焊机和张力辊、升级圆盘剪和涂油机、增加硬芯卷取和带头定位功能,以实现重卷机组对高端汽车外板的稳定生产。
2. 存在的问题
原重卷机组为非连续生产机组,定位为普通级别带钢的检查、分卷、涂油、切边等功能,无法满足高端外板生产要求,存在如下问题:
1) 该重卷没有焊机,每卷带头都需要人工手动穿带,节奏慢,无法连续生产。
2) 穿带和甩尾过程中,带钢下表面一直与导板台接触,出现擦划伤缺陷,无法满足外板生产要求。转向辊及各导板台设计不合理,易产生二次辊印和擦划伤缺陷。在线转向辊采用卷板辊设计,辊面耐磨性差,易产生辊印缺陷 [1] 。
3) 该重卷没有张力辊,分卷时无法保持张力,造成带钢下表面与导板接触,产生划伤。
4) 设备布置松散,局部设备间导板台过长,导板与辊子之间的角度不合理,在穿带、甩尾时易产生擦划伤缺陷 [2] ;立式检查台和水平检查台距离远,需要升降立式辊才能检查带钢下表面,影响机组效能。同时,带头40 m和带尾100 m带钢下表面存在盲区,无法满足外板通卷检查要求。
5) 现有圆盘剪切边质量不稳定,无法满足外板切边需求。
6) 现有涂油机无法使用高粘度防锈油,尤其是冬季时,3802和4107等油品经常涂油不均,造成质量异议。
7) 卷取机没有带头定位功能,下线钢卷内圈100 m范围内出现带头压印缺陷,无法满足高端产品要求。
上述一系列问题导致该重卷机组无法满足高端汽车板生产和检查需求,因此需要整体进行外板专线化升级改造。
3. 技术分析
3.1. 开卷机芯轴的改造
该重卷原开卷机卷筒利用碟簧辅助进行缩径,维护量大、碟簧更换成本高、故障率高。
改造后,选用简单的四棱锥套配扇形板结构的芯轴结构,结构简单,易于维护 [3] 。
3.2. 取消矫直机
由于机组的原料质量较好,极少需要进行带头矫直;在穿带或卸张爬行过程中,矫直机的下辊经常会对带钢造成擦划伤。为了减少带钢表面划伤,在本次改造中取消了原有的五辊矫直机。
3.3. 入口转向夹送辊可随着开卷机移动
入口转向夹送辊机架与开卷机本体进行刚性连接。当开卷机CPC投入使用时,入口转向夹送辊随开卷机同步滑动,避免开卷机纠偏时带钢与入口转向辊的辊面因为轴向相对运动而产生的带钢表面擦划伤。入口转向夹送辊的机架放置在LM导轨上,摩擦阻力小,与开卷机同步精度高。夹送辊采用垂直升降结构形式,配置同步机构,以保证上下夹送辊工作的位置精度,可减少穿带夹送时产生局部辊印,夹送时带钢跑偏。
3.4. 增加焊机
为了实现连续生产,在入口切头剪和纠偏辊之间增加了一套焊机。为了确保焊接质量稳定、提高热效率、节能降耗,增加的焊机采用了中频技术。中频焊机变压器重量和体积小,输入功率低,响应速度仅为工频焊机的1/20,电流能够更快地达到设定值,更准确地分析参数,焊接质量控制更精确。
3.5. 纠偏辊改造
因为圆盘剪对板带钢的对中有极高的要求。且开卷机到圆盘剪的距离较远(约20米),如果仅靠开卷机的对中系统很难保证进入圆盘剪的板带对中精度。这时需要采用HQT (High Quality Twin)高质量双重化纠偏系统 [4] 。
所谓双重化纠偏系统,就是在圆盘剪的前面放置一套对中纠偏装置,如图1所示。这套对中系统与开卷机对中系统联合起来,调节板带位置。开卷机的纠偏装置和圆盘剪前面对中纠偏装置各是一套独立的闭环调节系统,通过自适应PID调节,分别对带钢进行纠偏。工作时,根据机组的速度和开卷机到圆盘剪前纠偏辊的距离,同时将圆盘剪前对中纠偏装置的机械位移量和开卷机的机械位移量,通过双重化补偿算法计算,得到的补偿值作为开卷机纠偏系统的板带中心偏移的输入信号(Offset),以提高纠偏精度。这种双重化纠偏系统,完全能达到圆盘剪对系统对中的要求。
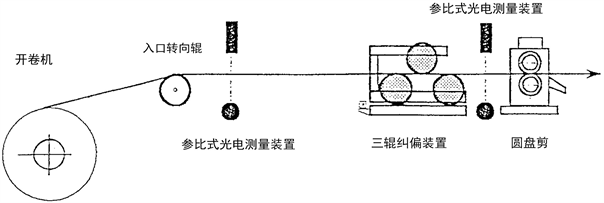
Figure 1. Arrangement for the steering system
图1. 纠偏系统布置
由于圆盘剪对纠偏系统的精度要求高,在选择纠偏辊时,一般采取PI辊,即比例积分动作纠偏辊。
比例积分动作纠偏辊是在冷轧生产线上大量应用的一种纠偏辊形式,实际上可以将其理解为P型纠偏辊和I型纠偏辊的组合。PI型纠偏辊在使用时也需要较长的自由进带距离(大于8倍带宽);自由出带距离可以短些,一般要有5倍带宽。如果机组的布置无法满足自由出带的距离,可以缩短自由出带距离(可以到1倍带宽),这时需要在电气控制上采取一定的措施,根据板带的偏差和速度来调整控制系统的参数。
比例积分动作纠偏辊的动作可以分解为比例动作和积分动作。纠偏辊的活动框架以与进带平面垂直并在纠偏辊之前的转轴为中心旋转(一般是虚拟的转轴),首先,纠偏辊转动时,使测量点板带如同P型辊产生横向位移,板带成比例移动;其次,纠偏框架转动时,纠偏辊轴线形成偏转角度,利用“辊效应”使板带受到侧向力,使板带回复正确位置。
该重卷机组原来选用的纠偏辊为水平摆动式纠偏辊,如图2所示,纠偏辊与带钢呈线接触,摩擦力小且不可调整,纠偏能力小。在原料表面涂油较多时,纠偏辊不能有效地进行纠偏,满足不了生产的需求。

Figure 2. Original style of the steering roll
图2. 原纠偏辊形式
为解决这一问题,将圆盘剪前纠偏更改为三辊式,如图3所示。
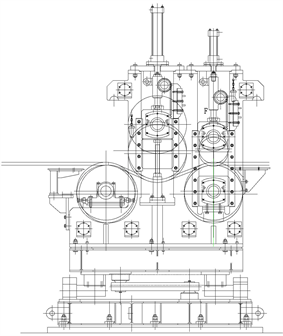
Figure 3. Triple-rolls style steering roll
图3. 三辊式纠偏辊
三辊纠偏装置是在可转动的机架上装有三个辊子,通过两根连杆支撑移动,使带钢与辊面之间形成的夹角(积分调节部分)与带钢横向移动(比例调节部分)进行适当的组合调节,除了对出带位置进行精确的纠正之外,对进带也有纠偏效果。带钢无需在辊上绕向就能实现带钢的纠正。
三辊式纠偏装置可通过调节上纠偏辊的位置,以调节带钢在纠偏辊上的包绕量,从而调整纠偏辊与带钢间的摩擦力。在其它参数不变的情况下,可通过改变上辊的下压量,调整纠偏力。三辊式纠偏,可增加纠偏能力和精度,且不改变轧制线的标高。
3.6. 新增张力辊
在水平检查台前,增加一套二辊式张力辊,如图4、图5所示:
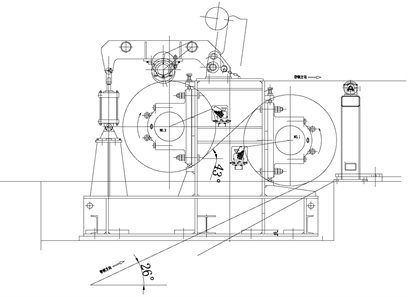
Figrue 5. Sketch of the two-roll style bridle roll
图5. 二辊张力辊示意图
• 便于实现入、出口段的张力分段,在出口段带钢检查、出口剪切头,而需要出口段卸张时,入口段能保持张力;
• 便于停机时张力保持,实现在水平检查台进行质量缺陷分析和静张力打磨;
• 当入口段在切头、焊接需卸张时,出口段能保持张力。
3.7. 升级涂油机
在板带后处理机组,涂油是卷取前的最后一道工序,涂油的均匀性会直接影响产品直观质量和表面质量。随着产品的开发,油品的更新换代,越来越多的下游厂家对钢卷涂油提出了更高的要求,尤其是在附加值相对较高的汽车板产品机组,涂油成为钢卷产品质量的一个重要考核方面,因为涂油不均和边部超重等原因,每年都会因此造成一定量的产品质量异议。
这就对涂油机设备提出了更高的标准,主要体现在以下两个方面:
① 汽车板和高档家电板涂敷的油品种类越来越多,从普通防锈油到可以直接冲压的高粘度润滑油,油品物理化学特性、粘度及添加物等等对静电雾化的要求越来越高,难度也越来越大,尤其是在低速低涂油量极限工作状态下的涂油精度和稳定性的挑战也大大增加。
② 配备在线油膜仪实时监测并提供油膜曲线报告,对涂油机的工作稳定性提出了更高要求(部分汽车板厂家要求在低速情况下肉眼检查板带表面质量)。
从油品性能考虑,高粘度油有着不可替代的作用,比如满足直接深冲加工需求,节省生产工序,提高效率等。但是高粘度油在涂覆过程中面临的风险和挑战也会增加,尤其是在汽车板产品中,由于高粘度油对于雾化条件的苛刻,板面油膜成型难度增加,油品缺少流动性,一旦在板面附着后基本不会扩散,因此,就要求在第一次雾化后涂覆的油膜表面满足汽车板厂家要求。
为了改善高粘度油品的雾化性能,此类油品必须精确有效的控制油品温度,整个涂油设备流程中各个环节所需要的参考温度,根据不同油品的物理化学特性适当调整,满足最佳的雾化条件。
对汽车板客户要求涂敷FUCHS 3802、4107、3802-39S等高粘度润滑油的实际情况,本次改造的涂油机具备全系统加热保温功能,对油品全部路径和雾化工作环境进行实时自动温度控制,确保雾化效果。
从油箱开始,工作油箱设计加热保温,过滤器、阀块、泵站、管路、机体侧壁、雾化室内部工作环境及回油管路均设计完整的伴热保温组件,保证油品温度,同时在刀梁处设计恒温控制,使油品达到最佳雾化的温度。
3.8. 锥度张力控制
在卷取过程中,随着钢卷卷径的增大,使钢带张力逐步减小的控制称为锥度张力控制。锥度张力控制可使钢卷的内层收得较紧,从而使钢卷内圈的层与层之间不打滑,防止钢卷卷取时内圈张力小而造成的塔形卷和板缝。
锥度张力控制采用三个可调参数进行控制,即锥度张力系数、起始厚度、终止厚度,如图6所示。终止厚度时的张力与基本张力和锥度张力系数满足如下关系式
TN——基本张力,RS——起始厚度,RE——终止厚度,K——张力锥度。
Figure 6. Taper chart of the tension
图6. 张力锥度图
该重卷在长时间的运行过程中,基本上采用K = 1.2倍的张力系数,起始厚度为800 mm,终止厚度为1200 mm。也就是钢卷直径从610 mm~700 mm之间采用的是1.2倍的张力,从800 mm到1200 mm,张力逐步减小到1.0倍,呈线性关系,1200 mm开始保持恒张力不变运行。
3.9. 带头定位
3.9.1. 带头印
该重卷机组原料来自镀锌机组,而且原料都是高级别汽车板,因此要避免对带钢产生新的缺陷,带头印就是其中最常见的一种。随着北京首钢顺义冷轧打造高端板材生产经营策略不断推进,加之部分高端汽车板材如宝马、长城等产品需求,这就对产品质量提出了更高的要求,其中亟待解决的一项就是带头印的问题。
带头印是横向的压痕印,打磨发亮,高端用户要求消除带头印,因此解决带头压痕,提高成材率是冷轧公司该重卷攻克的重点课题之一。
3.9.2. 控制方案
在卷取机芯轴上装有带沟槽的橡胶套筒,橡胶套筒的端部固定有反光材料,在外支撑上安装可识别反光材料的光栅。首先将套筒定位在一个特定位置,穿带时带钢到达特定的位置后,然后通过程序计算卷取机芯轴的启动时间,保证带头穿带到达芯轴上时,正好落在卷取机上橡胶套筒的沟槽位置,消除外层带钢的带头硌印 [5] 。如图7所示
1卷取机;2橡胶套筒;3沟槽;4外支撑;5光栅。
Figure 7. Sketch of the strip head positioning
图7. 带头定位示意图
以上卷取模式、橡胶套筒外径为610 mm为例来进行说明如何实现带头定位功能。
根据现场设备技术指标,带沟槽的橡胶套筒胀径后直径D为610 mm,出口穿带速度V为20 m/min,出口夹送辊前上方对射光栅在带钢上的投影点与皮带助卷器咬入缝隙之间的带钢运行轨迹的长度为L,通过测量可以得到L1。如图8所示:
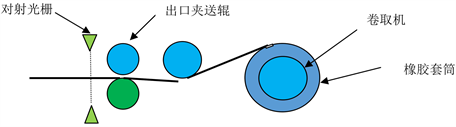
Figure 8. Principle of the strip head positioning
图8. 带头定位原理图
带钢由静止状态加速到20 m/min的恒速状态的时间为t。
带钢由静止状态加速到20 m/min的恒速状态的距离为L2
橡胶套筒上的白条由光栅检测,白条到钢带穿带到卷取机上的咬入点的距离已知,通过现场测量已知为l。卷取机转动以20 m/min的速度运行,而且在穿带过程中需增加一个
。
当检测元件检测到出口带头信号后,需要延时T启动卷取机,保证带钢咬入橡胶套筒的白条范围:
目前该重卷机组带头定位通过不断地完善改进,已能使带头准确定位在套筒沟槽区域。重卷线经过不断积累数据、程序优化,总结出不同钢带规格下的延时时间。可确保机组带头定位的稳定运行,有效解决带头印的问题,提高产品质量。
4. 结束语
该重卷机组改造项目,通过采取更改开卷芯轴、取消直头机、改造纠偏辊、增加焊机、增加张力辊并对涂油机进行改造成功解决了开卷涨印、辊面硌印;不能涂覆粘度较大的油品、如福斯3802-39s;系统不稳定,不能稳定高速生产;卷取质量不佳,成品卷不能满足客户需求等问题。增加了张力分段控制、硬心卷取、带头定位卷取等功能,为高端汽车板的生产提供了丰富的手段。系统改造后,可完全胜任宝马、奔驰及长城等高端汽车板的生产。这为冷轧公司获得高端汽车板订单,开拓并占稳市场,保持并不断提升市场占有率,奠定了坚实的基础。
参考文献