1. 引言
锂离子电池作为电动汽车(EV)最有前途的电源和主要的储能模块部件 [1] [2],已经在世界范围内引发了关注。其与铅酸和磷酸铁锂电池相比具有高能量密度、无记忆效应、长寿命和低自放电率的显著优势 [3] [4]。然而,锂电池的多数性能对温度很敏感 [5] [6] [7],高温时,电池内部的热量容易堆积,当电池模组的热量没有进行疏导散热时将会导致其温度一直上升,容量衰减,寿命减少,最终发生热失控 [8] [9]。低温时将会影响电池内阻、放电容量和使用寿命 [10],电池内部的内阻增大,放电能力急剧下降,从而影响电动汽车的驾驶性能。因此,设计出一套高效、合理的锂离子电池热管理系统是非常重要的。而锂离子电池热管理和热设计与电池热物性参数如比热容和导热系数密切相关,深入研究锂离子电池热物性参数及其热行为,对于准确预测电池温度变化、进行有效的热管理和热防护有重要的指导和实际意义。Zhang等人 [11] 基于传热学集总参数法建立了锂离子电池的比热容理论模型,以方形LiCoO2电池为研究对象,测得比热容为908 J·kg−1·℃−1。Drake等 [12] 基于准稳态原理对18,650和26,650两种尺寸圆柱电池的导热系数和比热进行了测量。Loges等人 [13] 对6种不同电池材料进行比热容测量,发现比热容随温度增加而增加,受荷电状态(SOC)影响较小,在25℃时比热容取值在870~1040 J·kg−1·℃−1之间。Maleki团队 [14] 使用激光闪光技术测量了电池电极材料层的导热系数和比热。然而,上述研究在实际测量中都未考虑热损的影响。吴青余等人 [15] 在考虑热损的情况下采用校准量热法对锂电池的比热和生热率进行了测量。
本文提出了一种基于准稳态法的单体电池热物性参数测量装置,通过Ansys仿真软件对所提出的装置测量中的热损失进行了数值仿真。仿真研究了不同对流换热系数下电池的温度分布及向外热损失情况。
2. 基于准稳态测量的理论分析
本文针对2.5 Ah的圆柱单体电池进行了研究,通过在电池表面建立恒热流边界条件来测量其轴向导热系数及比热。具体分析如下:
将恒定热流q输入到相对于电池负端子表面,假设其他边界绝热,电池的温度随着时间呈上升的趋势。根据瞬态热传导理论 [16],电池在短时间加热后就能够达到准稳态,由能量守恒定理得:
(1)
式中,q垂直于电池负极端子表面的热流,S是圆柱形电池的端子表面面积,m和c是电池的质量和平均比热,dT/dt代表电池的平均温升率。
因此,电池的平均比热c可以表示为
(2)
式中,ρ和H分别为锂离子电池的密度和长度。
对于电池轴向加热的情况,热传导微分方程和边界条件由下式给出
(3)
在Z = H时
(4)
在Z = 0时
(5)
其中
是电池温升,kz是电池的轴向导热系数。
考虑电池的初始温度与环境温度相同,即
,用拉普拉斯变换法或变量分离法求解热微分方程(3),得到温度场的时空解析解
(6)
其中
是热傅里叶数。电池轴向传导期间的热傅里叶数计算如下
(7)
根据公式(6),可以通过
和
之间的差值获得与电池轴向导热系数kz有关的表式
(8)
式中,ΔT是锂离子电池正极和负极端子表面之间的温差。
由于时间的指数依赖性,发现方当傅里叶数超过二分之一时,方程(8)中级数项的数值可以忽略。因此,电池的轴向导热系数kz以简化为
(9)
3. 数值仿真分析
本文以2.5 Ah的18,650圆柱单体电池为仿真研究对象,本文仿真建立的包裹绝热材料装置的三维几何模型如图1所示,在Ansys中fluent模块对其进行数值仿真分析,仿真设置边界条件如表1所示:
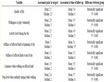
Table 1. The parameters in simulation model
表1. 数值仿真模型参数
仿真在25℃下进行,在电池负极端面输入3844 W·m−2的热流,仿真先研究了电池外部对流换热系数在5~50 W·m−2·℃−1时的热损失情况,此时电池直接与空气接触,然后在电池四周裹上20 mm绝热材料,在绝热材料四周输入相同的对流换热系数研究其向外热损失,时间总步长设置为600 s,仿真监测电池正负端面的面平均温度,同时监测电池正负端面及侧面的热损。
图2为仿真中电池直接暴露在空气中和包裹气凝胶后的仿真网格图,所有组成均以六面体网格为主导去绘制网格,仿真中所用绝热材料为二氧化硅气凝胶。
4. 结果与讨论
图3为电池暴露在空气中直接测量热参数的600 s温度云图,从图中看出,随着电池所处环境对流换热系数的增大,电池单体温度下降,表明对流换热系数的增大加强了测试中向外的热损失。
图4(a)为电池暴露在空气中,不同对流换热系数的电池热损随时间变化图,结果表明即使在外界对流换热系数为5 W·m−2·℃−1时电池向外散失的热流都占输入热流的2.9%,且随着对流换热系数的增大电池向外散失的热流进一步增加,在外界对流换热系数为50 W·m−2·℃−1时向外散失的热流占输入热流的11.5%。图4(b)显示随着电池所处环境对流换热系数的增大,电池轴向导热系数测量值与输入值的相对误差也增加,且在外界对流换热系数为50 W·m−2·℃−1时,电池导热系数测量值的相对偏差高达20%,表明测试中热损不能忽略。

Figure 2. (a) Battery grid (b) Single battery with insulation material grid
图2. (a) 单体电池网格 (b) 单体电池带绝热材料网格
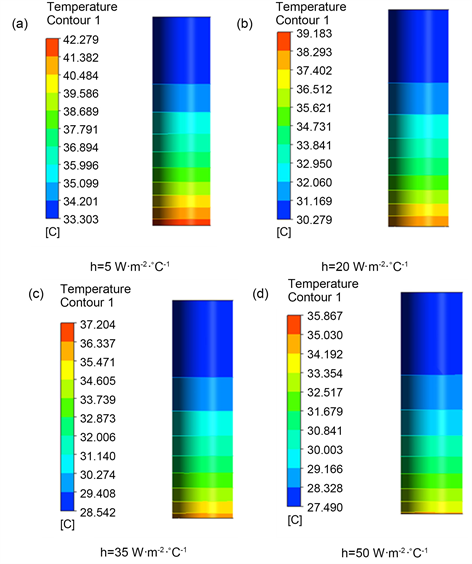
Figure 3. Temperature cloud image measured at 600 s when the battery is exposed to air (a) convective heat transfer coefficient 5 W·m−2·˚C−1 (b) Convective heat transfer coefficient 20 W·m−2·˚C−1 (c) Convective heat transfer coefficient h = 35 W·m−2·˚C−1 (d) Convective heat transfer coefficient 50 W·m−2·˚C−1
图3. 600 s时电池直接暴露在空气中测量的温度云图 (a) 对流换热系数h = 5 W·m−2·℃−1 (b) 对流换热系数h = 20 W·m−2·℃−1 (c) 对流换热系数h = 35 W·m−2·℃−1 (d) 对流换热系数h = 50 W·m−2·℃−1
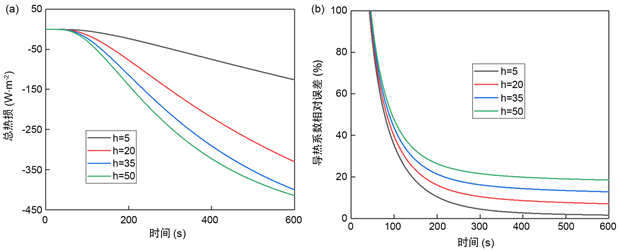
Figure 4. (a) Heat loss diagram under different convective heat transfer coefficients (b) Relative error diagram between the measured value of thermal conductivity and the simulated input value under different convective heat transfer coefficients
图4. (a) 不同对流换热系数下热损图 (b) 不同对流换热系数导热系数测试值与仿真输入值相对误差图
图5为电池包裹绝热材料装置的600 s温度云图,图中表明随着电池所处环境对流换热系数的增大(此时对流换热系数施加在绝热材料外部),电池单体温度略微下降,且在相同的对流换热系数条件上,包裹了绝热材料装置的单体电池温度明显高于电池直接暴露在空气中的电池温度,表明了增加绝热材料后明显降低了测试中的热损。
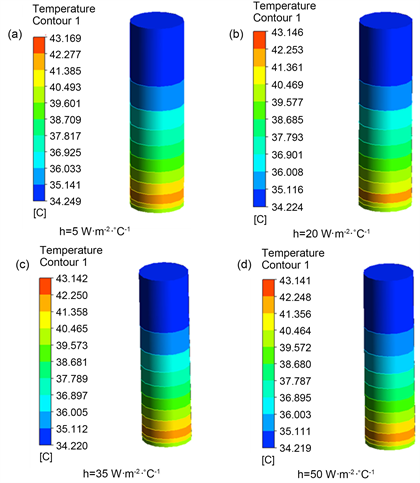
Figure 5. Temperature cloud picture of the cell coated with adiabatic material at 600 s (a) convective heat transfer coefficient 5 W·m−2·˚C−1 (b) Convective heat transfer coefficient 20 W·m−2·˚C−1 (c) Convective heat transfer coefficient h = 35 W·m−2·˚C−1 (d) Convective heat transfer coefficient 50 W·m−2·˚C−1
图5. 600 s时裹上绝热材料电池温度云图 (a) 对流换热系数h = 5 W·m−2·℃−1 (b) 对流换热系数h = 20 W·m−2·℃−1 (c) 对流换热系数h = 35 W·m−2·℃−1 (d) 对流换热系数h = 50 W·m−2·℃−1
图6(a)为包裹绝热材料后不同对流换热系数下电池的热损图,结果表明在电池四周裹上绝热材料,电池向外的热损失得到了减少,且测试热损随对流换热系数的增大几乎不增加。图6(b)显示随着电池所处环境对流换热系数的增大,电池轴向导热系数测量值与输入值的相对误差几乎不变,测试中热损随时间的增加而增加,且在外界对流换热系数为50 W·m−2·℃−1时,电池导热系数测量值的相对偏差控制在5%以内,表明加入绝热材料显著降低了热损。
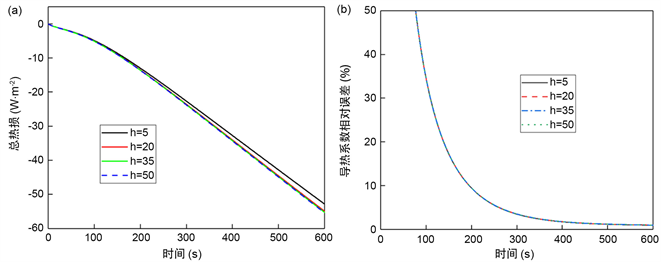
Figure 6. (a) Heat loss diagram under different convective heat transfer coefficients (b) Relative error diagram between the measured value of thermal conductivity and the simulated input value under different convective heat transfer coefficients
图6. (a) 不同对流换热系数下热损图 (b) 不同对流换热系数导热系数测试值与仿真输入值相对误差图
5. 实验验证
针对本文提出的两种测量装置,在25℃采用304不锈钢模拟电池进行了验证,模拟电池的尺寸与18,650锂电池一致,在模拟电池负极端面采用直径为18 mm的薄膜加热器进行加热,薄膜加热器与直流电源相连以恒功率提供热流,在电池正、负极端面布置热电偶以监测温度。对单体模拟电池来说,以1 W恒功率对其进行加热,通过正负极温差采用公式计算出比热和导热系数值,其测量值及与304不锈钢的标准值误差均如表2所示:
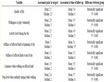
Table 2. Test results and error analysis of dummy batteries made of ANSI 304 stainless steel
表2. 不锈钢模拟电池的测试结果和误差分析
结果表明,在电池测量中的热损是不能忽略的,对于比热测量来说,在电池四周裹上绝热材料大大提高了其测量精度。
6. 结论
本文基于准稳态法对2.5 Ah圆柱单体电池测量中的热损失进行了数值仿真研究,结果表明随着电池直接接触的空气对流换热系数的增大,电池测量过程向外散失的热损失越多,即使在外界对流换热系数为5 W·m−2·℃−1时电池向外散失的热流都占输入热流的2.9%,在外界对流换热系数为50 W·m−2·℃−1时向外散失的热流占输入热流的11.5%,电池导热系数测量值的相对偏差高达20%。在电池四周裹上绝热材料可减少测试中产生的热损,随着电池所处环境对流换热系数的增大,电池单体温度略微下降,且在外界对流换热系数为50 W·m−2·℃−1时,电池导热系数测量值的相对偏差控制在5%以内,指出了在电池热物性参数测试中,向外的热损不能忽略。同时,本文针对提出的两种装置,采用304不锈钢模拟电池进行了验证,结果表明在电池四周裹上气凝胶后,电池导热系数测量值的偏差从12.75%降至4.70%,比热测量值的偏差从29.35%降至12.79%,进一步表明了测试中热损是不容忽视的。