1. 引言
管道系统作为流体传输、能量转换的重要通道,在石油化工、能源动力、航天航空等工程领域具有广泛应用 [1] 。管道服役过程中,特别在结构、流体载荷综合作用下,弯头部件易产生局部变形和应力集中等问题。在较大外力作用下,弯头横截面在弯曲时会趋于扁平化或呈“椭圆形”,这将导致弯头的应力值进一步增大。因此,美国机械工程师协会(ASME)提出的ASME B31.1、ASME B31.3 [2] 等一系列管道规范规定在计算管道系统应力时应考虑局部应力增大的影响,计入应力增大系数(Stress Intensification Factor, SIF)。
根据管道设计规范,管道设计时应分别考虑一次应力和二次应力校核,一次应力校核主要针对管道在管内压力和重力等持续性载荷作用下的应力,二次应力校核主要针对由于温度效应及位移荷载产生的应力 [3] 。SIF作为管道系统二次应力分析中的一个重要影响因子,其研究始于20世纪40年代,Markl [4] 最早完成了一系列管道疲劳试验及其分析,为应力增大系数的研究奠定了基础,现行标准中的应力增大系数的计算公式仍建立在Markl工作的基础之上;Nordham和Kaldor [5] 基于管系结构弯头应力数值分析,提出了具有不同附管长度的弯头应力增大系数计算公式;Nikola [6] 基于数值模型的管道应力强化因素分析提出了新的弯头应力增大系数计算方程,结果表明该方程更适合于数值数据;Nikola等 [7] 还提出了适用于大径厚比弯头(即D/T > 100)的应力增大系数方程;Matzen和Tan [8] 综述了应力强度因子与C2和B2应力指数之间的关系;高建林等 [9] 应用FE Tools软件模拟计算了弯头应力增大系数值,并与ASME B31.3规范结果进行了比较。
目前已有研究成果主要用于分析单弯头管道结构,行业内常用的ASME B31.3规范给出的应力增大系数计算得到的弯头应力与实际值仍存在一定差距,且相关实验数据较少。本文以工程中常用的U型连续弯管结构为研究对象,搭建了弯管应力实验平台,测得了弯头应力随外载荷的变化规律;建立了弯管有限元模型,并将其数值结果与实验结果进行了对比;提出了修正的弯头应力增大系数计算公式,该计算公式与现行管道设计规范ASME B31.3已有公式相比,具有更高的计算精度。
2. 连续管道弯头应力实验
2.1. 实验试件
为测得连续管道弯头在外力作用下的应力值,制作了工程中常用的U型连续弯管实验试件,通过电子万能试验机对该试件进行拉伸实验。U型弯管结构示意图及制作件如图1和图2所示,该试件由管径D = 19 mm,壁厚T = 1.5 mm,曲率半径R = 38 mm的冲压成型弯头部件和与弯头部件管径、壁厚相同的直管部件焊接而成。试件全长L = 384 mm,所用材料为SUS304不锈钢,材料参数见表1。管道部分设计全长360 mm,该结构共包含四个弯头,每个弯头处内拱线、外拱线、中性线的中点分别作为应力测点,应变片型号为BX120-3AA。
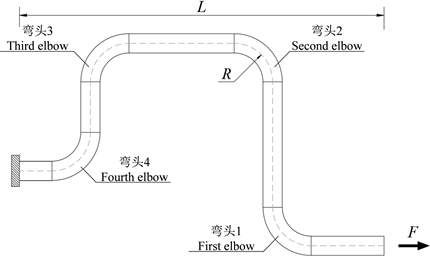
Figure 1. Structural diagram of U-bend
图1. U型弯管结构示意图
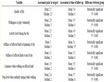
Table 1. SUS304 material parameters
表1. 不锈钢SUS304材料参数
2.2. 实验过程
准静态拉伸实验在WDW-50E型程控电子式万能试验机组上进行,实验过程示意图及实验设备如图3所示。参照GBT 228.1-2010《金属材料拉伸试验第1部分:室温试验方法》 [10] 加载方式采用力加载,加载速率为0.5 mm/min。根据管道设计中二次应力校核的工况荷载条件 [11] ,以管件臂端处的轴向荷载作为管件端点位移荷载,实验过程中外荷载F作用在弯管端部,分别从0加载至150 N、200 N和250 N,同时记录试件端部位移。实验中,试件四个弯头各个测点处分别安置电阻应变片,采用16通道UT8508动静态应变采集分析系统对应变进行采集,桥接方法采用1/4桥并使用温度补偿。由电阻应变片测量得到弯头各测点处应变值,计算得到相应测点处弯头应力值。
2.3. 实验及数值结果对比分析
为对比分析弯头最大应力值随外力的变化规律,应用ANSYS软件分别建立了连续弯管试件的管单元模型和壳单元模型,如图4所示。管单元模型采用PIPE16单元和PIPE18单元分别模拟直管段和弯管段,其求解速度快,但无法模拟弯头横截面的实际变形,所以常用应力增大系数进行修正;壳单元模型采用SHELL181单元整体建模,计算工作量大,却更符合管路的实际受力和变形状态。根据ASME B31.3规范,应用管单元模型计算弯头修正前的应力值;使用壳单元模型来模拟管路的真实状态,获取管路弯头的真实应力值。模型边界条件与实验过程保持一致,短端固定,长端沿管道轴向施加外力荷载;材料应力应变关系采用理想弹塑性模型 [12] 。计算获得弯头的von Mises等效应力云图如图5所示,从图中壳单元模型应力计算结果可以看出在开弯状态下弯头内弧及中性层处的应力较大,应力分布呈递减趋势向周围分散。
将实验结果与有限元结果进行对比分析,弯头应力的实验值与有限元壳单元模型计算结果吻合较好,其平均误差为3.2%;弯头应力峰值出现在内弧线中点附近,且随着外荷载的增加,弯头应力近似表现为线性增长关系;同时U型弯管中各个弯头应力值随外弯矩增加而增大。图6给出了U型弯管各个弯头内拱线中点处应力值随外载荷的变化曲线。从图中可以看出,在弹性阶段随着外荷载的增加,四个弯头最大应力值呈线性增加,在相同外荷载作用下,弯头2的应力值高于其它弯头,这主要是由于结构中弯头2到荷载作用端的垂直距离最远,因此作用在弯头2上的外弯矩最大导致的,同时其弯头附近的应力分布受结构整体变形影响较大。
(a)
(b)
Figure 4. Finite element model of U-shaped elbow (a) Pipe element model; (b) shell element model
图4. U型弯管有限元模型(a) 管单元模型;(b) 壳单元模型
(a)
(b)
Figure 5. Stress nephogram of elbow (a) Pipe element model; (b) shell element model
图5. 弯头应力结果云图(a) 管单元模型;(b) 壳单元模型
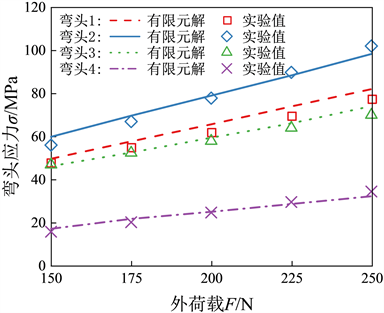
Figure 6. Comparison between finite element analysis and experimental results
图6. 有限元与实验结果对比
3. 弯头应力增大系数(SIF)
3.1. 现行规范SIF计算及其误差分析
现行管道规范ASME B31.3规定在计算管道弯头应力时应考虑局部应力增大的影响,计入应力增大系数,其计算公式为:
(1)
式中:iin为应力增大系数,h为柔度特性,其表达式为
,其中T,R,r分别为弯头壁厚,弯头曲率半径,管道平均半径,m。该计算方法的提出基于Markl在1952进行的管道部件疲劳实验。随着现代工业管道技术的发展,已有研究表明现有规范SIF计算方法可能产生较大计算误差,导致低估管道应力,造成强度或疲劳分析结果不可靠 [6] [7] [13] 。有限元软件ANSYS在PIPE单元模块内置了SIF命令,可以通过设置SIF基础值考虑弯头应力增大效应,从而获取更为准确的弯头应力。图7给出了基于ASME B31.3规范标准的管单元模型计算结果与实验结果及壳单元数值计算结果对比曲线,从图中可以看出,使用ASME B31.3规范SIF计算方法得到的弯头应力普遍低于实验测试值及壳单元数值计算结果,且随着外荷载的增加,相对误差逐渐增大,最高误差可达28.65%。这表明ASME B31.3规范给出的应力增大系数与实际值存在一定差距,原因是规范中未考虑外载荷对应力增大的影响,当外载荷在弯头处产生较大弯矩作用时,弯头同样会因为截面变形产生应力集中现象 [14] ,从而导致弯头处的应力进一步增大。

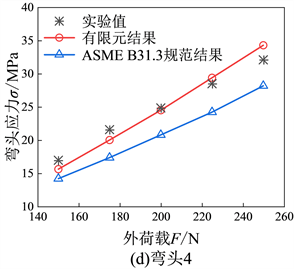
Figure 7. Curve of elbow stress with external load
图7. 弯头应力随外载荷变化曲线
3.2. 修正SIF计算公式
确定应力增大系数的方法主要有疲劳试验法和数值分析法,数值分析法主要采用有限元分析软件对管道部件进行详细的局部应力分析来确定应力增大系数,其因为效率高,成本低得到了广泛应用 [15] 。将管单元模型计算结果和壳单元模型计算结果进行对比分析,同时考虑修正系数与原规范公式的可类比性,通过引入弯矩对弯头应力的理论影响分析和量纲分析提出如式(2)所示的修正模型:
(2)
式中:M = FL,F为管道端部外载荷大小,N;L为外载荷对弯头的力臂,m;EI为抗弯刚度,N·m2;T,R,r分别为弯头壁厚,弯头曲率半径,管道平均半径,m;a−e为常数。
通过实验数据和有限元数值计算结果对式(2)进行拟合分析,得到式中常数分别为:a = 2.084;b = 0.3333;c = 7.04;d = 1.987;e = 4.039。
取a = 2.1;b = 1/3;c = 7;d = 2;e = 4,由此得到修正项δ如式(3)所示:
(3)
由此得到经校核修正后的弯头SIF计算公式为:
(4)
将ASME B31.3规范公式(1)和修正公式(4)计算的弯头应力值与实验及有限元结果对比分析,其结果如图8所示。可以看出,修正公式得到的弯头应力更接近实验值,且与有限元结果基本吻合,平均误差小于5.16%。现行规范计算得到的弯头应力最大值普遍小于实验值及有限元壳单元模型结果,且误差较大,其平均误差为16.34%。表2给出了各个弯头由不同计算方法得到的应力值,相较于实验值,修正公式计算弯头1应力值比原公式相对误差降低了12.43%,弯头2降低了19.18%,弯头3降低了18.85%,弯头4降低了16.63%。这表明修正后的应力增大系数公式计算结果更接近实际值。
在影响弯头应力分布的截面参数中,管道径厚比D/T和相对管径D/R对弯头的应力分布具有较为明显的影响。图9和图10分别给出了弯头4在不同径厚比和相对管径下规范公式和修正SIF公式得到的弯头应力变化曲线。由图9中弯头应力与D/T关系可以看出,在相同荷载作用下,随着径厚比增加,弯头应力逐渐减小,其原因是高径厚比弯管(薄壁管)比低径厚比弯管刚度更低,变形更大,从而增加了管道的整体柔性,降低了管道应力。当径厚比较小时(D/T ≤ 16),修正公式计算值与有限元结果吻合较好,其平均误差为5.71%,随着径厚比的增加误差略有增大,其平均误差最大为9.20%。而使用规范式计算得到的弯头应力最大值与有限元数值计算结果相比误差均较大,其平均误差为24.5%,且随着D/T比值的增加,该误差逐渐增大,最高可达27.0%。这表明对于不同径厚比的情况,修正公式相较于原规范公式其计算结果更接近实际值。
图10为不同相对管径下弯头应力的变化曲线。由图中可以看出,在相同载荷作用下,随着相对管径D/R比值的增加,弯头应力最大值逐渐增大,这主要是由于增大相对管径会弱化弯管的整体变形,从而降低弯管的柔韧性,提高整体应力。由修正SIF计算式得到的弯头应力最大值略高于有限元数值计算结果,其结果偏保守,最小误差为5.32%,平均误差为6.10%。而使用规范SIF计算式得到的弯头应力最大值与有限元结果相比误差均较大,最小误差为25.29%,平均误差为25.7%。可以看出,修正SIF计算式比原规范公式具有更好的相关性和更高的计算精确度。
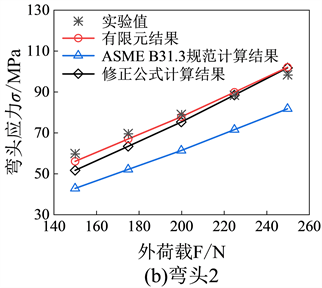
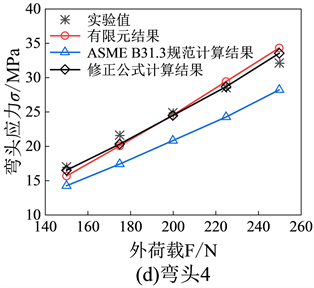
Figure 8. Comparison of ASME B31.3 code and modified formula with experimental values and finite element results
图8. 修正公式和ASME B31.3规范式与实验值及有限元结果对比
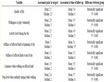
Table 2. Stress value of each elbow under different calculation methods
表2. 不同计算方法下各弯头应力值
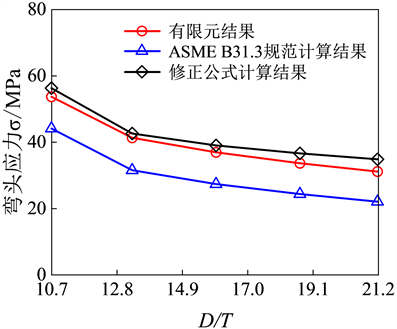
Figure 9. Elbow stress curve of different D/T
图9. 弯头应力随D/T变化曲线
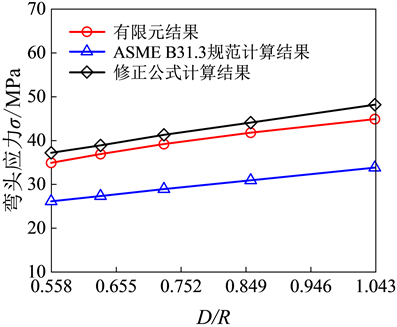
Figure 10. Elbow stress curve of different D/R
图10. 弯头应力随D/R变化曲线
4. 结论
1) U型弯管弯头在弹性阶段其应力峰值出现在弯头内弧中心点附近,且随着外荷载的增加,弯头应力近似表现为线性增长关系。壳单元有限元模型计算得到的弯头应力值与实验测试值吻合较好,其平均误差小于5.0%。U型弯管中各个弯头应力分布规律受外弯矩作用的影响,具体表现为外弯矩越大,弯头应力值越高。
2) 提出了修正的平面内弯头应力增大系数计算公式,该公式与现行ASME规范公式相比其应力计算结果更接近弯头实际应力值,计算精确度更高,误差更小,其计算精度提升了16.77%。
3) 在相同荷载作用下,弯头应力值随弯头径厚比的增加而减小,随相对管径的增加而增大。对于不同径厚比和相对管径的情况,修正公式更适用于小径厚比弯管,其计算结果偏保守较为安全,相较于原始公式的计算结果更接近实际值,平均误差分别为5.71%和6.10%。
参考文献
NOTES
*通讯作者。