1. 引言
随着动力锂离子电池技术的发展,单体电池能量密度不断提升,但锂离子电池对温度极为敏感的缺点一直难以攻克 [1] ,其最佳工作温度在20℃至50℃之间,且模组内电池温差应保持在5℃以下 [2] 。否则会造成电池的循环寿命衰减,安全性降低。并且在持续高温的工作状态下,电池甚至可能会发生热失控,导致新能源汽车起火爆炸 [3] 。因此,高效稳定的冷却系统是保证电池安全运行的必要条件。
目前,液冷和风冷技术被广泛的运用于电池冷却系统。风冷结构简单,但冷却效率低。液冷冷却效率高,但是易造成模组内电池温度不均匀。相比于前两者,相变材料(Phase Change Material, PCM)有着巨大的潜热,并且相变时温度处于一定范围内 [4] ,契合电池的散热要求,使得PCM被运用到电池散热系统中。
由于,PCM的导热系数较低,在电池高倍率充放电的情况下,往往不能够快速的转移热量,导致热量在电池周围集聚 [5] 。因此,一些研究者便通过填充膨胀石墨(EG)构建复合相变材料(composite phase change material, CPCM)以提高导热系数 [6] [7] 。但导热系数的增加是有限的,并且随着EG填充数量的增加,CPCM的潜热也会变低。Jiang等 [8] 研究了EG填充分数对散热系统性能的影响,结果表明EG分数在9%至20%之间的CPCM散热性能最佳。然而,当电池处于高倍率或循环充放电工况时,发热量过大,PCM潜热耗尽完全熔化后,冷却系统将失效 [9] 。一些研究者通过引入液冷构建复合散热系统来回收PCM潜热。而Cao等 [10] 发现通过在CPCM系统中复合液冷,能够延长CPCM的相变时间,降低电池最大温度,但是会使得温差增大,破坏了PCM散热系统温度均匀性较好的优势。因此,众多学者开始考虑如何有效地结合PCM和液体冷却,在保证散热要求同时提高系统温度均匀性。Song等 [11] 提出了一种含有导热柱和散热板的PCM复合液冷散热结构,PCM填充在电池缝隙中,散热板紧贴电池用来提高温度均匀性,导热柱埋在CPCM中并与底部冷板相连用来回收PCM潜热。Cao等 [10] 人提出了一种PCM与延迟液体冷却相结合的复合冷却模式,发现冷却液的延迟介入能够很好的控制电池温差。Zhang等 [12] 提出了一种在液冷流道与PCM间添加翅片的方法,发现合理的翅片布局能够降低最高温度的同时减小温差。
如上述方法相同,大部分学者提出的改善温度均匀性方法均是从液冷侧出发的,很少考虑通过对PCM进行优化改善温度均匀性的。本文构建一种CPCM复合液冷的电池散热系统,在保证电池散热要求的前提下,通过将CPCM模块划分为蓄热区和导热区,填充不同EG分数的CPCM,来改善电池温度均匀性,同时研究了分区处理对CPCM潜热回收的效率及均匀性影响。
2. 模型与方法
2.1. 几何模型
图1为本文构建的CPCM/液冷复合的电池散热系统,以21,700电池作为研究对象,每两列电池中间放置液冷板,CPCM填充在液冷板和电池的间隙中,模组上下部由10 mm的结构胶密封。同列两电池间距为2 mm,电池与液冷板间距为1 mm。选用孔隙式液冷板,增加CPCM填充量,流道截面宽2 mm、长4 mm,壁厚为0.5 mm,流道间由多条宽4 mm起到均热作用的支撑柱连接。冷却液为50%水50%乙二醇,相邻流道内冷却介质错流流动。根据电池外壁面到液冷板距离d将CPCM划分为不同功能区,电池与冷板间为蓄热区,其余为导热区。表1为系统内各部件相关参数。初始模型填充EG分数为9%的CPCM,根据Ling等 [13] 提出的计算公式,得到的不同EG分数CPCM的导热系数、比热容和潜热,见表2。在电池充放电时,CPCM模块与液冷模块协同散热,热量首先由CPCM模块相变吸收,当CPCM模块液相分数达到0.9时,启动液冷模块对电池降温并回收CPCM潜热。
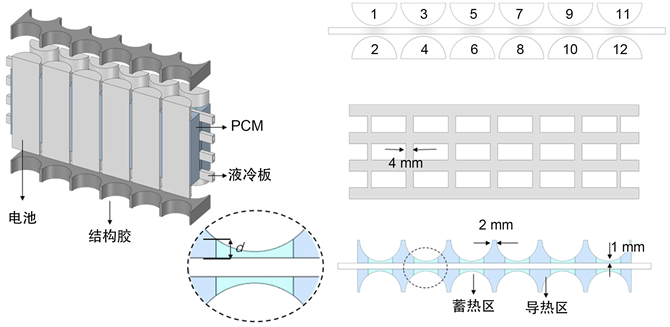
Figure 1. CPCM/liquid cooling composite cooling system model
图1. CPCM/液冷复合散热系统模型
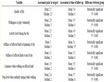
Table 2. CPCM parameters of different EG filling fractions
表2. 不同EG填充分数CPCM参数
2.2. 数学模型
在数值计算时,考虑冷却介质与液冷板间的对流传热以及电池模组内部各模块间的导热。将CPCM熔化后视作黏度无限大流体,不考虑流动,忽略自然对流对内部传热的影响。且将CPCM物理参数设为定值,不考虑相变后物理参数的变化。
正确的电池产热模型是仿真计算的前提,本文采用Bernardi [14] 电池产热模型,根据刘等 [15] 提供的21,700电池参数进行生热计算。
(1)
式中,I为工作电流,R为内阻,
为温熵系数。
CPCM模块传热方程:
(2)
(3)
(4)
式中,ρPCM和kPCM表示PCM密度和导热系数,H为PCM焓值,L为相变潜热;TS和TL分别为PCM凝固温度和熔化温度。
本文冷却介质为50%水50%乙二醇,冷却模块的能量、动量及连续性方程如下:
(5)
(6)
(7)
式中,ρc、cp,c和kc分别为冷却介质的密度、比热容和导热系数,v为冷却介质流速,P为压力。
2.3. 数值方法及模型验证
采用ANSYS FLUENT对模型进行网格划分及仿真分析,为减少计算量,将模型对称处理。主要考虑CPCM及液冷板对电池圆柱面的散热,忽略电池正负极处的自然对流。本文主要考察电池在35℃、3C放电工况下,冷却系统运行情况。冷却液流速为0.2 m/s,入口温度为35℃。
为确保电池生热率模型的正确,参考刘等 [15] 文献中21,700电池相关参数,在环境温度25℃、单体电池1C放电工况下进行仿真计算,与文献中实验数据对比,如图2。图中仿真结果和实验结果相差较少,最大误差为2.9%,在可接受范围内。表明本文使用的生热率模型及数值仿真方法是可行的。
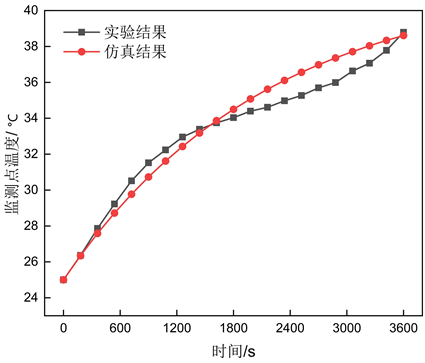
Figure 2. Comparison of simulation and experimental results
图2. 仿真与实验结果对比
本文采用FLUENT meshing划分多面体网格,图3为复合散热系统局部网格图。为了考虑计算经济性,对网格进行无关性验证。在环境温度35℃,入口速度0.2 m/s条件下,对CPCM/液冷复合散热系统仿真计算。图4为网格无关性验证结果,网格数量增加到420万时,继续加密网格对结果的影响很小。因此,本文选用420万网格进行后续计算,最大网格尺寸为2 mm,局部最小尺寸0.2 mm。

Figure 3. CPCM/liquid cooling model grid diagram
图3. CPCM/液冷模型网格图
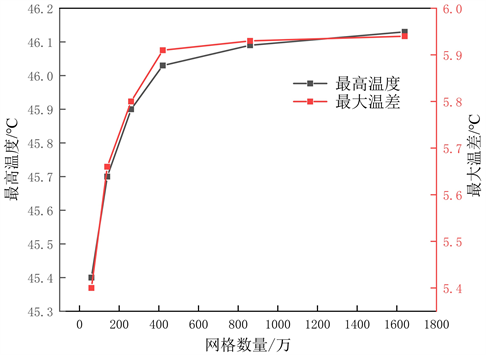
Figure 4. Grid independence verification
图4. 网格无关性验证
3. 结果与讨论
3.1. CPCM/液冷复合散热系统仿真结果
为了验证CPCM/液冷复合电池散热系统的性能,在环境温度35℃、3C放电工况对电池模组进行仿真分析。图5为单一CPCM散热系统及CPCM/液冷复合散热系统在放电过程中,模组内最高温度、最大温差及液相分数的变化情况。从图中看出,单一CPCM散热系统仅依靠有限的相变潜热不能够抑制电池温升,在900 s左右液相分数达到1,CPCM散热模块失效。放电结束时,模组内电池最高温度攀升至57.6℃。而CPCM/液冷复合电池散热系统在放电全程模组内电池最高温度为47.5℃;放电结束时最高温度为46.03℃,CPCM模块液相分数也从0.9降低到0.2。表明本文构建的相变/液冷复合散热系统基本能够完成电池散热任务,将模组内电池最高温度保持在50℃以下,且液冷启动后能够快速对电池降温并回收CPCM潜热能力。但观察图5中温差变化情况,相比于单一的CPCM散热系统,复合系统的温差相对较大,电池放电结束时最大温差达5.9℃,不能够满足电池温度均匀性要求。从图5中看出,复合冷却系统内电池最大温差变化主要由3阶段组成。第一阶段CPCM未熔化,第二阶段CPCM开始相变,第三阶段液冷开启后。很显然电池温差较大的问题主要出现在液冷开启后,未开启液冷前最大温差仅为3℃。
图6为CPCM/液冷复合电池散热系统放电结束时电池温度云图,从图中看出由于冷却液错流流动,模组内各电池间温度相对一致,温度不均匀性主要由单体电池径向温差导致。单体电池温度呈环状由外向内增大,2号电池径向温差达5.6℃。主要有两个原因,一方面,圆柱形电池卷绕式结构导致径向热阻较大;另一方面电池外壁面与液冷板距离较近,传热热阻较小,受液冷影响较大。内外部换热条件的差异导致了电池径向温差较大。图7为不同位置单体电池最大温差变化图,从图中看出,各单体电池温差呈对称分布。靠近入口处的1、2、11、12号电池温差最大,中部电池温差小。下文便以温度均匀性最差的2号电池作为优化对象,通过调整散热结构减小电池温差。
图8为复合散热系统放电结束时CPCM液相分数云图,结合图5中液相分数曲线图发现,在放电结束时,CPCM模块整体液相分数下降到0.2左右,与液冷板距离较近的CPCM已完全凝固,但位于两单体电池间的CPCM依然处于液相状态。这表明CPCM潜热回收也存在着不均匀性。实际上,CPCM的液
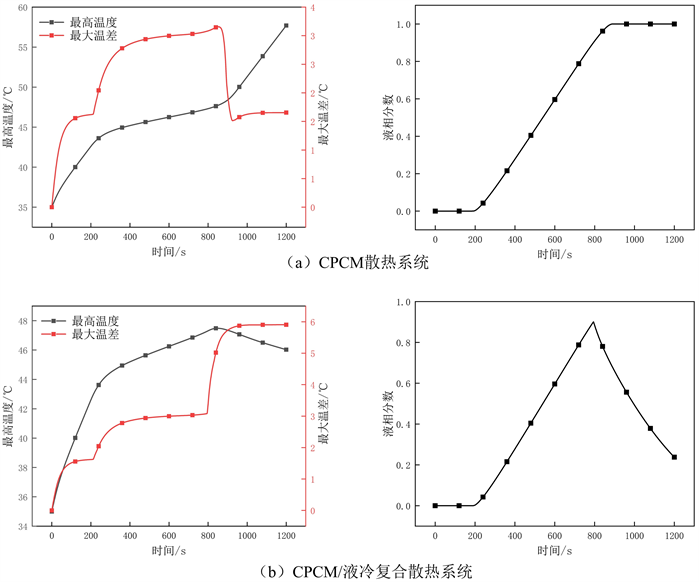
Figure 5. Change curve of battery temperature, temperature difference and liquid fraction in single CPCM and CPCM/liquid cooling composite cooling system
图5. 单一CPCM和CPCM/液冷复合散热系统内电池温度、温差及液相分数变化曲线
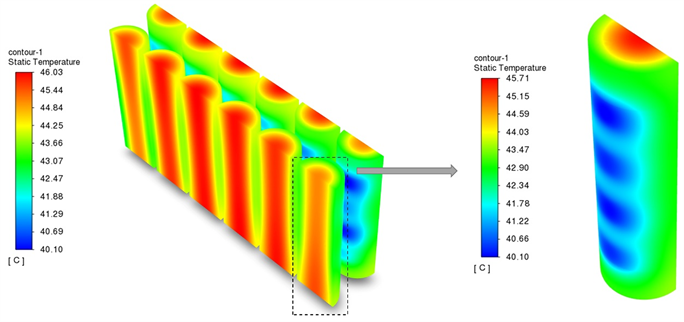
Figure 6. Cloud chart of battery temperature at the end of discharge of CPCM/liquid cooling composite cooling system
图6. CPCM/液冷复合散热系统放电结束时电池温度云图
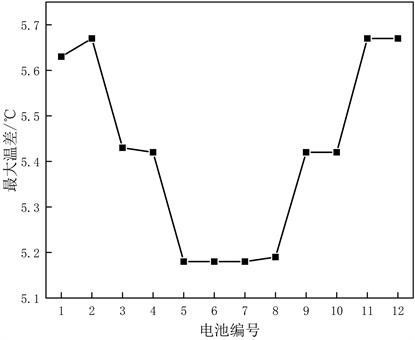
Figure 7. Maximum temperature difference change of single cell at different positions
图7. 不同位置单体电池最大温差变化
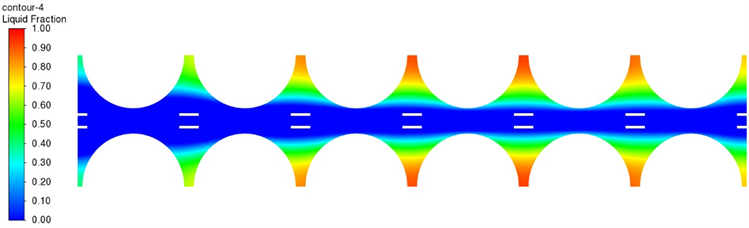
Figure 8. CPCM liquid phase diagram at the end of discharge of CPCM/liquid cooling composite cooling system
图8. CPCM/液冷复合散热系统放电结束时CPCM液相云图
相分数主要由其温度决定,温度低于固相线温度时,液相分数为0;温度高于液相线温度时,液相分数为1。根据液相图可以看出,靠近液冷板处CPCM温度必定低于41℃,而两相邻电池间CPCM温度必定高于41℃,甚至局部温度超过44℃。所以,液相分数的不均匀性本质上就是CPCM内部的温度不均匀性。和上文中单体电池温度不均匀的原因相同,CPCM模块内部的温度不均匀性也是由于不同位置CPCM与液冷板间传热距离不同导致的。靠近液冷板处CPCM与液冷板传热距离较小,传热热阻较小,换热量较大,此处潜热被快速回收并由液态转变为固态。而两相邻电池间的CPCM与液冷板传热距离较远,散热缓慢,导致在放电结束时依然处于液态。这或许也是导致单体电池温差较大的一个原因,单体电池两侧壁面接触的CPCM处于液态,温度高于41℃;而单体电池中部壁面接触的CPCM为固态,温度低于41℃。电池外壁CPCM液相分数的不均匀必定会加剧单体电池内部的温度不均匀性,因此对CPCM模块的结构优化是有必要的。
3.2. CPCM分区填充
从上文分析可知,单体电池温度分布及CPCM潜热回收的不均匀性都与传热热阻相关。因此,本节通过改变不同区域热阻值大小来优化系统内的温度均匀性。根据电池外壁面到液冷板的传热距离,将CPCM模块进行功能分区,定义d为分区距离。传热距离小于d,即电池与液冷板之间的CPCM划分为蓄热区,填充纯PCM,利用其高潜热、低导热的特性来缓冲液冷板与电池间换热。传热距离大于d,即两相邻电池间划分为导热区,填充EG分数为20%的膨胀石墨,提高导热系数来减小传热热阻。通过改变分区距离d的大小观察分区位置的变化对复合散热系统温度及液相回收均匀性的影响。
图9为d取不同值,模组3C放电结束时2号电池的温度云图。与上文图6中2号电池温度云图对比,电池最低温度所处的位置由原本的蓄热区向两侧导热区移动。随着分区距离d的增大,蓄热区的长度和厚度在增加,最低温度也不断向电池两侧移动。从图9中发现,不论d取何值,最低温度均移动至蓄热区和导热区交界处。主要是对CPCM模块进行分区处理后,蓄热区导热系数较小,传热热阻大,电池外壁面受液冷板的影响变小;而交界处虽与液冷板距离较远,但导热区填充的是20% EG的CPCM,导热系数为纯PCM的36倍,传热热阻较小,受液冷板的影响较大。因此,在导热区与蓄热区交界处,电池外壁面与液冷板传热热阻最小,使得此处成为最低温度区。
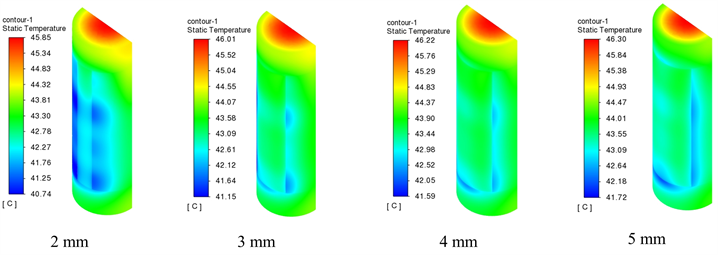
Figure 9. Temperature nephogram of No. 2 battery under different d values
图9. 不同d取值下2号电池温度云图
图10为2号电池在不同分区位置时温差、最高及最低温度变化曲线图,随着d的增大,蓄热区厚度增大,电池内外温差逐渐减小。当厚度达到3 mm时,2号电池温差降到5℃以下,4 mm厚度时温差为4.63℃,继续增加蓄热区厚度时温差减少较小。从右侧温度变化图看出,随着d的增大,2号电池的最低温度和最高温度均在增加,但最低温度增加的速率高于最高温度,这便是2号电池内外温差减小的原因。通过在蓄热区填充导热系数低的PCM减少传热,使得电池最低温度上升的同时也导致了整个单体电池与液冷板间换热变弱,电池最高温度上升;但在导热区又填充了高导热系数的CPCM,增加传热,因此在一定程度上抑制了电池最高温度的增长,使得温升速率下降。
图11为整个电池模组在d取不同值时最高温度及温差的变化情况,可发现当d为4 mm时电池模组内最大温差为4.93℃,低于5℃,最高温度为46.52,低于50℃。与未进行CPCM分区的模型相比,最大温差降低了0.98℃,降幅为17%,最高温度增加了0.55℃,增幅为1%。虽然,将复合散热系统分区后牺牲了一定的散热能力,使得电池最高温度上升,但模组内温度均匀性却获得了较大的提高。表明通过将CPCM划分为蓄热区和导热区,填充不同EG分数的CPCM可以改善模组内的温度均匀性。
图12为分区距离d不同取值下放电结束后CPCM模块液相分数云图,用以分析分区填充对潜热回收均匀性的影响。相比于图8中未分区模型的液相分数图,显然当d取值为2时,CPCM模块液相分数分布更加均匀,局部最大液相分数为0.5左右。但随着d值的增大,蓄热区厚度增加,导热区液相分数逐渐增大。d值为4 mm时,局部最大液相分数为1。很显然,随着蓄热区厚度的增加,潜热回收的均匀性再次变差。图13为不同d取值下CPCM模块整体液相分数变化曲线,当d大于2 mm后,CPCM模块整体液相分数反而增大,d为4 mm时液相分数甚至高于CPCM未分区的模型。这些主要由于蓄热区厚度的增加使得导热区与液冷板间传热面积减少,换热能力下降,CPCM中热量不能及时被液冷板带走。显然,通过划分蓄热区和导热区可以提高CPCM模块潜热回收的效率和均匀性,但d值大于2 mm时,潜热回收的效率和均匀性反而变差。这和提高温度均匀性所需的d值冲突,d值为2 mm,CPCM潜热回收效率及均匀性最佳,但电池模组内最大温差为5.41℃,不满足温度均匀性要求;d值为4 mm时,模组最大温差为4.93℃,满足温度均匀性要求,但潜热回收的效率及均匀性又变差。在电池散热系统中,模组温度均匀性的重要性高于潜热回收均匀性,因此下文选用d值为4 mm的分区模型,在保证温度均匀性的前提下优化潜热回收均匀性。
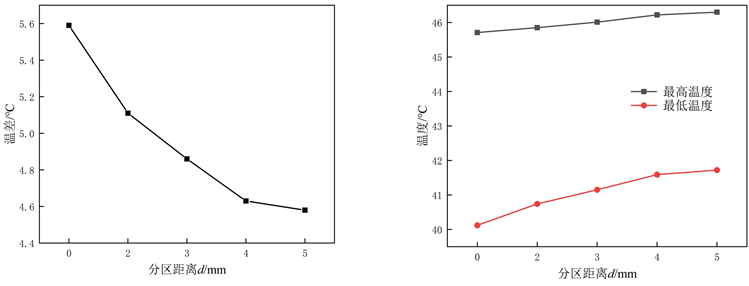
Figure 10. Temperature difference, maximum and minimum temperature variation diagram of No. 2 battery under different d values
图10. 不同d取值下2号电池温差及最高、最低温度变化图
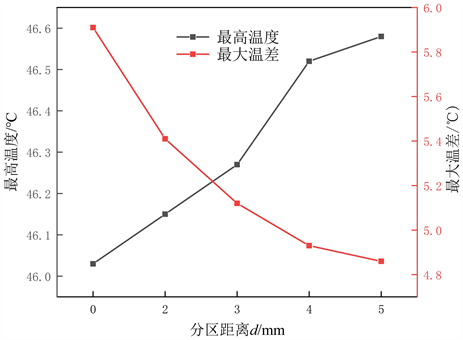
Figure 11. Overall temperature difference and temperature change diagram of module under different d values
图11. 不同d取值下模组整体温差及温度变化图
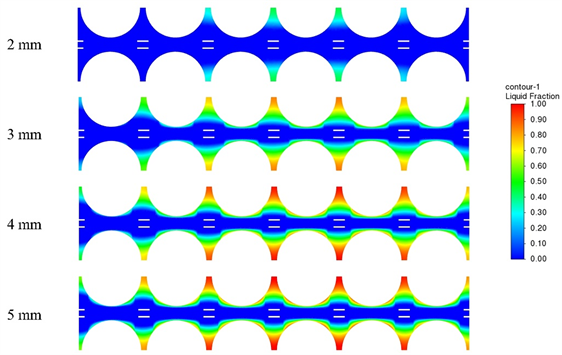
Figure 12. Liquid phase nephogram of CPCM module under different d values
图12. 不同d取值下CPCM模块液相云图
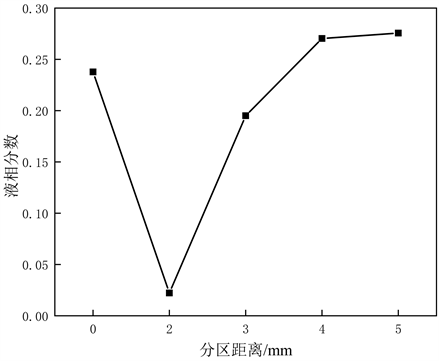
Figure 13. Change curve of liquid fraction of CPCM module under different d values
图13. 不同d取值下CPCM模块液相分数变化曲线
3.3. 导热区不同EG分数CPCM填充
根据上节分析,当d大于2时,潜热回收的均匀性随d值增大而变差,主要由于传热面积的减小导致的换热减弱。因此本节在接触面积不变的前提下,继续提高CPCM中EG填充分数以增加导热区的导热系数,增强导热区与液冷板间的传热。以CPCM蓄热区厚度为4 mm为基础模型,分别向导热区中填充EG分数为20%、30%、40%和50%的CPCM,观察对潜热回收均匀性的影响。
图14为不同EG分数CPCM填充下,放电结束时CPCM模块液相分数云图。从图中可以看出,随着EG填充分数的增加,CPCM模块液相分数显著下降,当EG填充分数达到50%时,CPCM基本全部凝固,液相分数分布也比较均匀。图15为CPCM模块整体液相分数随EG填充分数增加的变化情况。随着EG填充分数的增加,CPCM模块整体的液相分数逐渐降低。EG填充分数大于50%时,放电结束后CPCM模块液相分数仅为0.02,相变潜热基本全部回收。随着EG填充分数的增大,导热区CPCM的导热系数不断增加,使得热量快速的传递到液冷板中,被冷却液带走。这表明在导热区填充导热系数更高的CPCM能够起到提高潜热回收能力及回收均匀性。
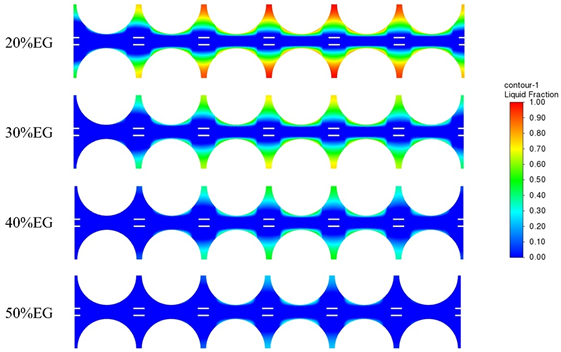
Figure 14. Liquid phase nephogram of CPCM module under different EG filling fraction
图14. 不同EG填充分数下CPCM模块液相云图
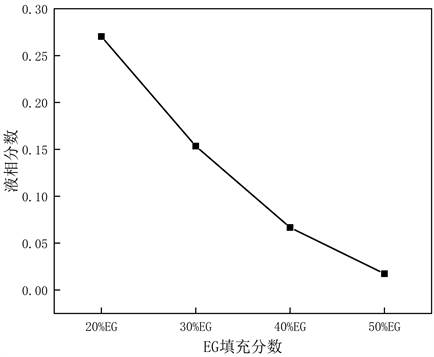
Figure 15. Liquid phase change curve of CPCM module under different EG filling fraction
图15. 不同EG填充分数下CPCM模块液相变化曲线图
但根据表2中不同EG分数填充下CPCM的潜热值,可以发现随着EG填充分数的增大CPCM的潜热值大小显著下降,相比于EG填充分数为20%的膨胀石墨,EG填充分数为50%的CPCM潜热值为113,300 J/kg,降低了约37%,即潜热模块的散热量上限降低了37%左右。仅仅为了提高潜热回收的均匀性而提高EG填充分数,导致潜热模块散热能力减弱是不经济的。因此,针对潜热回收不均匀性问题,需考虑其他方法解决,后续工作中将会继续对此研究。
4. 结论
本文通过将CPCM模块划分为蓄热区和导热区,分别向其中填充不同EG分数的膨胀石墨,用来提高复合冷却系统模组内部温度均匀性,并研究分区后对潜热回收均匀性和效率的影响,得出以下结论:
1) 相比于单一的CPCM散热,复合液冷的CPCM散热系统能够对电池快速降温并回收CPCM的潜热,但引入液冷会导致单体电池径向温差较大,温度均匀性较差,且存在潜热回收不均匀的问题。
2) 通过对CPCM模块分区后,随着分区位置的变化,当d为4 mm时,单体电池径向温差及模组整体温差分别下降到4.63℃、4.93℃。当d为2 mm时,CPCM模块潜热回收效率和均匀性都有所提升,但随着d值增大,潜热回收效率和均匀性再次变差。提高温度均匀性所需的d值与提高潜热回收均匀性所需的d值冲突。
3) 随着导热区CPCM中EG填充分数的增加,潜热回收的效率及温度均匀性逐渐提升,EG填充分数达到50%,CPCM整体液相分数仅为0.02。但相比于20% EG填充的CPCM,EG填充分数为50%的CPCM潜热值降低了约37%。仅仅为了提高潜热回收效率和均匀性损失较多的潜热模块散热量明显是不合适的。