1. 引言
2015年初,国家提出全面实施“中国制造2025”,这给中国制造业提出了更高的要求,不能只停留在“能制作”的层面上,要向工业设计等方面侧重。作为第三次工业革命的领头羊德国,提出的“工业4.0”后,工业建模仿真软件Plant Simulation应运而生,本文重点研究了该软件在装配线仿真上的应用。
2. 装配线仿真的步骤
一般仿真步骤如下表1:
3. Plant Simulation对装配线的建模
3.1. 利用软件内的功能模块实现产品装配的建模
软件中的Mus模组中,有Part和Container两个模块可以用来进行装配作业的建模,其特性见表2。
基于以上两种模块的基本属性,我们可以对装配作业进行简单建模。例如:假设手机共由四个部件组成,分别是手机下壳、主板、电池和显示屏。装配顺序如图1。
其中主板和下壳为被装配对象,可用Container表示,电池和显示屏为装配对象,可用Part表示。
3.2. Part和Container的扩展信息
➢ Part零件是没有负载能力的移动物料流对象,它在物料流对象上进行移动。零件表示正在生产和运输的各种零件,但不运输其他工件。
➢ Container容器是用于运输其他MU的移动物料流对象。可以使用它来对托盘、箱子、箱子等进行建模。
➢ 定义装载空间的容量,仅指MU的数量,而不是它们的物理大小。
➢ 在模拟运行期间,工厂模拟沿连接器将容器从一个物料流对象移动到另一个物料流对象 [4] 。
3.3. 对多人工多配件的装配线进行建模
在确定了主配件的建模方法后,还需要对加工中心进行建模,在软件中需要用到Station和DismantleStation两个模块,其特性见表3。
3.4. 模型建立
本文研究对象为装配流水线,涉及到加工和装配两种作业。因此需要用到Station和DismantleStation两个模块。零件需要用到Part和Container两个模块。分别对工位和传送带建模如图2和图3,并根据企业实际情况,将工作台及传送带按需组合,得到流水线如图4。
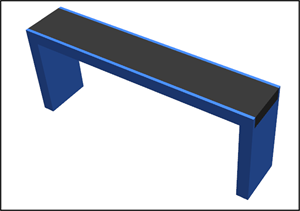
Figure 3. Conveyor belt modeling diagram
图3. 传送带建模图
在对Station模块进行建模或模型更改时需注意,尺寸和形状的改变不能改变该Station中工作面的位置,如图5所示。零件的位置不会自动在工作台上,有可能在平面上,有可能在模型外,因此,在对Station进行形状更改时,需要对其内置参数进行变更,从而调整加工零件的相对位置。
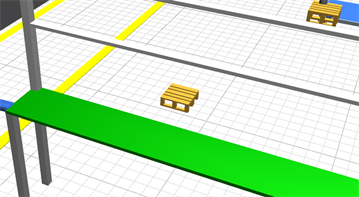
Figure 5. Schematic diagram of part position
图5. 零件位置示意图
在人员方面,需要用到Resources模组中的WorkerPool、Broker和ShiftCalendar。其中WorkerPool控制着工人的发生和回收,Broker控制工人池、日程表和Station的连接关系。这里以WorkerPool为例,展示三者之间的相互关系,如图6所示。在WorkerPool一层界面属性栏中,可以看到工人、协调器和班次日程表三个可定义选项,其中工人中的创建表指的是需要定义该工人池中,工人的名称、数量及对应的工作等信息,如图7所示。协调器则控制着Station和工人池之间的工人交互关系,如想通过工人池向Station发送工人,则需要在一个协调器的控制下,班次日程表同理。
4. Plant Simulation对装配线的仿真
4.1. 装配线的节拍
在装配线上,一般将此装配线上工时最长的工位定义为瓶颈工位,而瓶颈工位的工时即为该条装配线的节拍。通过节拍,可以计算出该条装配线的小时产能、日产能和线平衡率等数据。
4.2. 传统节拍的使用方法和仿真模型中的节拍
在传统节拍的使用方法中,一条装配线的产能即等于该条产线可投入生产使用的时间除以节拍,无论瓶颈工位在该条装配线的哪个位置,计算公式都如上述一样,但这样计算存在一定的误差,即:假设该条装配线共有20个工位,在产线清空且没有在制品的情况下,瓶颈工位在该条产线的第一个工位,若瓶颈工位一天的产能为20个产品,瓶颈工位的产能即为该条产线的产能,那么存在一个问题,在可用时间耗尽时,第一个工位即瓶颈工位可以恰好产出20个产品,但是其后续的第二个工位可用时间耗尽,无法继续制作第一个工位即瓶颈工位所制造的第20件产品,同理,剩余的18个工位也没有可用时间用来制造剩余产品。所以,在实际生产过程中,装配线的实际产能应该是低于利用瓶颈工位计算出来的理论产能。如果要正确的使用产线产能等于可用时间除以瓶颈时间这个公式,那么就需要加一个必要条件,即:在生产活动开始时,每一个工位都需要有至少一件在制品,才能保证瓶颈工位的产能是该条产线的产能。
但是,在工厂实际的生产活动中,行业法规一般要求任务单切换时或交接班时,产线要清空,无法保证每一个工位都有至少一件在制品,所以上述的产能计算公式无法得到准确的理论产能数据。如果要得到更为准确的理论产能数据,那么就需要在可用时间里减去产品首尾件的时间。
如果要将节拍数据和可用时间数据导入仿真模型中,那么在设置每个工位的可用时间时,就不能减去首尾件的时间。因为在Plant Simulation软件中,产品在产线的流转时间,已经被运算过了,如果再减去首尾件的时间,那么会导致数据不准确,而我们得出的仿真结果,也会不准确。
4.3. 产品实际在传送带上的位置和仿真模型中的位置偏差
在工厂的实际生产过程中,如果流水线选用的是倍速链,那么产品在倍速链上的相对位置是固定的,我们可以通过倍速链的速度和长度,以及每个工位的工时即可算出产品在产线上的周期时间。如果流水线选用的是普通传送带,且传送带速度相对较慢,而且员工需要将产品从传送带上取下作业,那么会出现一种情况,即:员工从传送带上取放产品时的位置是不确定的。所以如果通过传送带的速度、长度和工位的工时,无法计算出准确的理论产品周期时间,因为员工的取放产品位置,会导致传送带的长度变长或变短。
因此在仿真模型中,如果不对产品取放位置对传送带长度的影响进行补偿,那么每个工位的产品取放位置,应尽可能设置在工位的正中间,以减少实际生产过程中员工取放产品位置不确定的影响。
4.4. 装配线仿真
通过上述方法对某工厂的手工装配线和配料进行建模仿真,得到仿真效果图如图8和图9。从3D模型中可以看到物料的实时流转和产品的加工过程,便于生产管理者掌握工厂整体情况。
得到仿真数据如图10、图11和图12所示。
通过软件我们可以得到该条装配线的产能、节拍和线平衡率等数据。同时可以得出每个工位的等待时间占比和阻塞时间占比。并且通过图表可以快速看到产线的各类损失时间,如计划损失,异常损失等,方便我们计算产线的效率,分析原因。此外还可以快速地找到影响整体产能的问题工位或问题点,方便未来开展针对性工作并作出改善。
5. 仿真结果同传统IE理论的对比分析
将仿真结果汇总并与理论计算结果进行对比,整理成对照表见图13。
从图中可以看出计算出的理论每日产能为668个,仿真出的每日产能为666个,在实际生产过程中,应该以装配线最后一个工位的产出作为该条线的产出,即每日产能为666个。
6. 结论
本文通过分析Plant Simulation软件在多工位手工装配线的应用方法,并对一案例进行仿真建模,验证了方案的可行性。同时,将传统IE对生产理论计算数据与仿真数据进行对比,分析其差异原因,并优化了仿真参数的输入方法。通过实际案例,将理论方法运用于实践,验证了技术路线的可行性,证明了文中所述方法的实践性。