1. 引言
液压挖掘机作为一种重型工程机械,其负载具有较高的功率密度和快速的动特性,这些特点使挖掘机的燃油消耗以及废气排放显著增加。液压挖掘机的复杂结构以及多级能量转换特点,也使得系统的能量利用率非常低。混合动力技术在汽车行业近几十年的发展中起到了巨大的作用。受此启发,混合动力技术被引进到工程机械行业,在建筑施工、矿山采掘、交通运输等各类工程实践中有着广泛的应用 [1] 。
2009年日本住友建机推出了混合动力磁盘起吊式挖掘机,并宣称与同型号旧机型相比可节约40%的油耗。2010年,小松推出了低燃油消耗的HB205/HB205LC-1,该混动动力系统主要通过回收传统挖掘机浪费掉的回转减速与制动的能量,以电能的形式储存在蓄电器中。2012年又推出了改进产品HB215LC-1,平均油耗降低了25% [1] 。国外的普渡大学,国内的浙江大学,燕山大学等高校也开展了类似的研究工作。此外,常见的挖掘机多是以主泵通过液压阀控制各执行器,由于阀控具有较严重的节流损失,会造成很大的能量损耗。因此本文采用一种基于多泵系统的混合动力挖掘机,能有效地避免阀控造成的能量损失,达到节能效果。
本文通过simulink软件建立了整个混合动力挖掘机的数学模型,根据已有的挖掘机工作循环,利用动态规划算法,通过调节发动机的转速以及作用在发动机上的扭矩,使发动机在满足挖掘机性能的前提下,工作在经济油耗区,从而降低燃油消耗率,起到节能的效果。并以此得到挖掘机在给定工作循环时的最优控制变量轨迹。
2. 混合动力挖掘机原理
2.1. 混合动力挖掘机结构
混合动力挖掘机的液压结构如图1所示,仅显示了挖掘机的主要工作功能,即回转、动臂、斗杆和铲斗。每个辅助功能与每个主要工作功能共用一个泵。执行器均为差动油缸。驱动这些致动器的泵(单元3、4和5)具有可变排量和过中心的特点,因此能够提供四象限操作 [2] 。回转驱动采用串联混合液压系统,回转马达(单元2)由高压蓄能器提供能量,挖掘机驾驶室旋转产生的制动能量也可以直接存储到高压蓄能器中。单元1称为“储能泵”,安装在发动机轴上。它负责在高功率需求时协助发动机,并在低功率或中等功率需求期间保持蓄能器充满以备之后使用。在这种应用中,操作员通过操纵手柄来达到期望的速度。对于执行机构,手柄指令转换为相应装置的流量指令,最后转换为泵的斜盘角度指令。对于回转马达,手柄指令转化为回转马达的速度指令,通过适当的控制逻辑将其转换为斜盘角度指令。
2.2. 控制系统的结构
本节介绍了一种结合能量管理策略和控制方法的控制系统。如图2所示,操作者通过操作手柄达到期望的速度,此时手柄指令转换为对应的流量信号,进入到管理策略层。该层主要通过分析挖掘机实际工况的特点,并根据所规划的控制策略,计算每个执行机构的控制目标指令,将指令传输到执行元件。此外,执行元件的控制方法与管理策略的控制目标相结合,完成了致动器的控制信号。因此,能量管理策略是解决如何分配发动机功率使得油耗最低的问题,而执行层是解决怎样使用控制算法优化致动器的控制性能的问题。
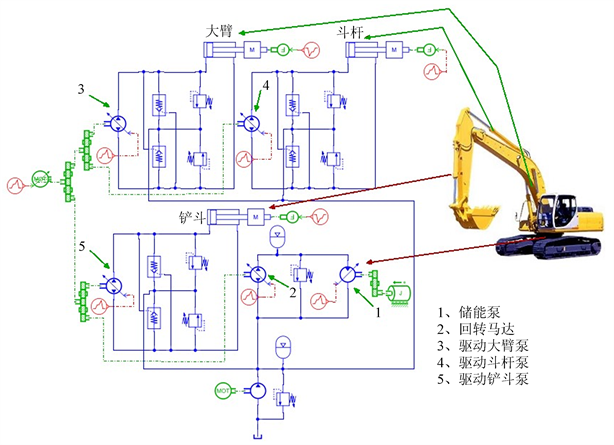
Figure 1. Hybrid power excavator hydraulic system structure
图1. 混合动力挖掘机液压系统结构
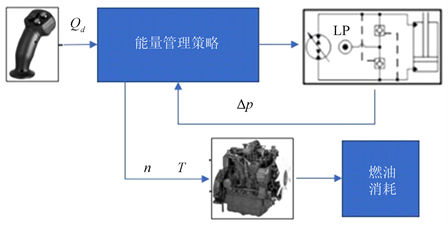
Figure 2. The whole machine control system structure schematic diagram
图2. 整机控制系统结构示意图
3. 整机数学模型的建立
3.1. 主泵的数学模型
可变排量泵1、3、4、5均通过机械方式与发动机相连。通过它们的理论流量Q是泵的斜盘摆角
、排量
、和速度
的函数。流量损失
是变量
、
和泵压差
的非线性函数 [3] 。流量损失
始终假定为正值,当泵的A口压力大于B口压力时,泵两端的流量为:
(1)
(2)
当泵的A口压力小于B口压力时,泵两端流量为:
(3)
(4)
由于泵的物理过程的复杂性,与控制方程的近似值相比,使用基于测量数据的纯经验模型对其损失特性进行建模更为准确。这种模型可以通过最小二乘多项式回归来创建,得三个变量的三阶多项式的形式:
(5)
将流量损失拟合为泵的压力、速度和排量的函数:
(6)
将扭矩损失拟合为泵的压力、速度和排量的函数:
(7)
泵模式下轴的扭矩:
(8)
在文中,定义泵两端压差、速度和流量与轴扭矩
的关系:
(9)
3.2. 液压缸的数学模型
文中的所有液压缸均采用相同的方法进行建模,如图3所示。根据牛顿第二定律得液压缸的力平衡方程:
(10)
其中
和
是液压缸两侧的截面积,
是摩擦力,
表示施加在油缸上的载荷,
是液压缸杆的位移。
、
是液压缸两腔的压力,
为内泄露量,
、
为液压缸两腔的体积,液压缸的流量连续性方程 [4] 如下所示:
(11)
(12)
(13)
3.3. 回转机构的数学模型
回转机构的工作模式如图4所示,由蓄能器驱动回转机构,进而使挖掘机驾驶室得以旋转,
为回转机构的转动惯量,
为回转马达与回转机构的转速比,
为回转机构的角加速度,回转机构的受力方程:
(14)
3.4. 蓄能器的数学模型
蓄能器中的压力积聚(或排放)是有效流量
和
相互作用的结果,如图4所示,因此蓄能器的压力方程可得:
(15)
电容
可从第一原理导出,除了随压力
变化外,还取决于蓄能器预充压力
,有效气体体积
和各向同性气体系数n [5] 。
(16)
3.5. 发动机的数学模型
发动机的工作过程比较复杂,因此在控制中很难用一个精确的数学表达式来描述,通常发动机数学模型的建立是基于发动机速度特性、输出转矩和燃油消耗率等试验数据基础上,采用数表或者公式拟合的方法来描述 [6] 。用
表示发动机的燃油质量。稳态条件下的燃油消耗率
是发动机转速
和扭矩
的函数,可以用二维多项式来描述:
(17)
发动机的动态特性近似为一阶系统,其中是
发动机工作时扭矩,
是粘性摩擦,
是发动机轴上的外部负载。负载扭矩是液压泵扭矩的总和,其中r表示连接到发动机变量泵个数。输出扭矩
是负载扭矩
和加速所需惯性扭矩之和。
(18)
(19)
(20)
在挖掘机工作过程中,发动机的油耗是由发动机转速以及扭矩决定的。发动机轴上的扭矩是各个泵上的轴扭矩之和。而泵上的扭矩是由泵两端的压差以及泵的排量来决定的,泵两端压差即为液压缸两端的压差。因此发动机的油耗函数可以表示为:
(21)
4. 控制策略分析
动态规划方法本质上是一种非线性规划,是将分级决策方法和最优化原理结合的一种有效的计算方法,用于求解多阶段决策问题,在理论上可以找到任何复杂问题的最优解。该原理可以用递归关系来概括,以帮助决策过程不断转移。将多步最优控制问题转化为多个一步最优控制 [7] 。通过不断递归计算,可以实现在给定循环条件下获得控制和状态的最优轨迹的目的。首先是反向搜索每个设定步长的最小成本函数,并记录相应的最优控制。之后是通过使用由第一步获得的最优控制进行搜索,进而得出最优变量控制。
4.1. 所用工作循环
如图5所示的一个完整挖掘周期,在0到2.5秒为提升和回转阶段,动臂伸出,回转结构转动,在此阶段,斗杆缩回,为倾倒土做准备,在2.5到4秒阶段,铲斗回缩,倾倒土,回转开始转回,4到7秒阶段,动臂下落以及回转转回初始位置,7到10秒为挖掘阶段,动臂和回转基本不动,此时斗杆和铲斗伸出 [8] 。
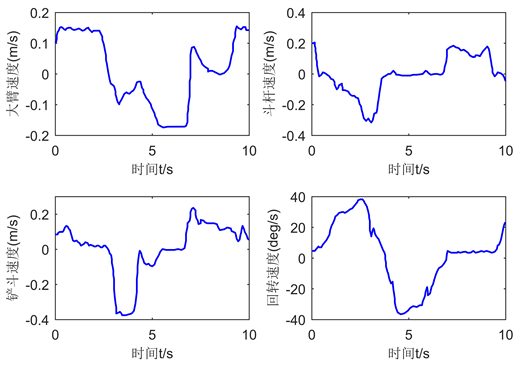
Figure 5. One complete excavation cycle for excavators
图5. 挖掘机一个完整挖掘周期
4.2. 系统的状态量和控制量
系统的状态变量一些由输入的周期定义,另一些由基于相互关系的方程式可以计算出结果 [9] ,例如泵的出口流量,轴上的作用扭矩等。所以定义系统的状态变量为:高压蓄能器压力
和转速n。同理,可得控制量为储能泵排量
。
4.3. 目标函数
发动机的最低燃油消耗是确定动态编程模拟的优化目标:
(22)
式中,
是总燃油消耗量,
是离散时间步长,
是燃油消耗率,由作用在发动机轴上的瞬时扭矩和转速计算得出。
4.4. 算法编程
发动机的油耗函数是从发动机万有特性曲线引出的。动态规划算法的核心是让发动机的转速和转矩一直运行在发动机低油耗区间,也就是在整体时刻加起来,使得发动机的油耗函数的值最小。液压缸的驱动是由泵的出口流量控制的,而泵的出口流量是发动机转速以及泵排量的乘积。泵排量和出口压差,又决定着发动机的扭矩。当液压缸的行程确定后,流量和压差已经确定了。因此动态规划的核心是改变发动机的转速以及泵的排量,每一时刻取的值,都是在当前时刻,油耗函数整体最小的值,此时储存发动机的转速数据。
图6描述了基于离散动态规划算法的编程流程图。程序总体分为三个循环,采用内嵌套的方式,最内层为控制量的循环,中间层为状态量循环,最外层为将工况划分成时间间隔dt的离散面。所以针对每个离散的面上所有的状态,每个状态都进行一次所有控制量的计算,控制量计算对应的油耗值并与当前的状态油耗值相加,选出最小油耗的值存入该状态点对应的矩阵。
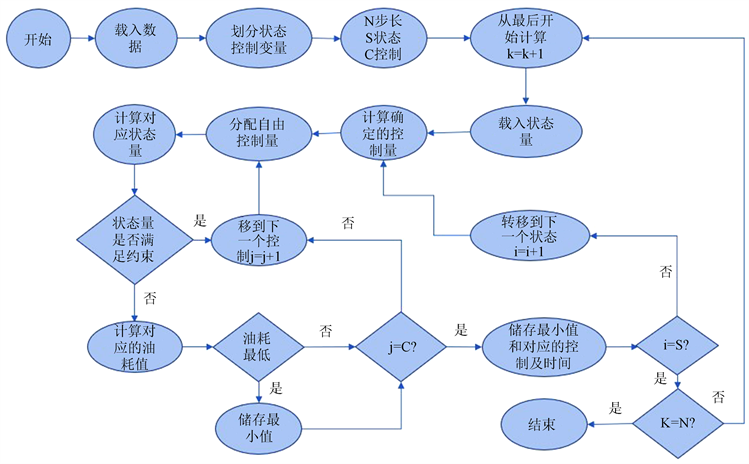
Figure 6. Algorithm programming flow chart
图6. 算法编程流程图
4.5. 仿真结果与分析
图7显示了主要动作元件泵/马达的最优排量,大臂、斗杆与铲斗的最优泵排量随各自所需致动器速度的变化而变化,且每一时刻至少有一个变量泵接近满排量。这意味着发动机处于最小允许速度,从而才能在执行元件处满足流量要求,回转机构的排量是根据其所需的扭矩进行变化。
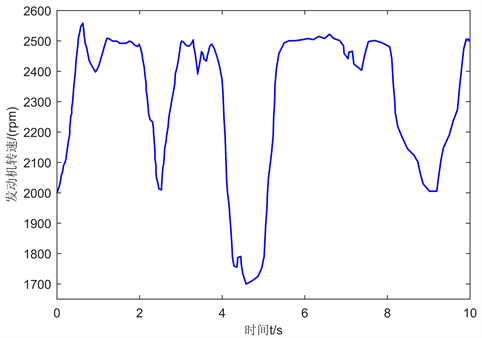
Figure 7. Optimal engine speed under dynamic planning
图7. 动态规划下最优发动机转速
表1显示了一个完整的挖掘周期下,动态规划算法与恒定发动机转速下的油耗进行对比,发现动态规划控制策略下的发动机油耗明显降低。
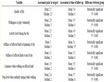
Table 1. Fuel consumption comparison
表1. 燃油消耗比较
5. 结论
本文根据已知的挖掘机工作循环,利用动态规划算法,通过调节发动机的转速以及作用在发动机上的扭矩,使得发动机保持在最佳燃油点工作。通过油耗比较可以看出,利用动态规划算法可以显著降低燃料消耗,并且获得的最优控制轨迹可以为其他的控制策略提供基准。因此,本文的工作对于未来使用其他不同的控制策略,以及对挖掘机的结构优化具有一定的启发意义。