1. 引言
目前,航天类产品壳段多为整体铸件材料机加产品,内部铆接装配电缆支架、仪器安装支架等,该类铆接装配生产国内仍然采用传统的手工工艺,手工划线定位支架、手工制孔、手动气动锤击铆接。
锤铆是最基础的铆接方式之一,手工锤铆是在铆钉的另一端用顶铁顶住,通过不断的冲击使铆钉产生变形,形成镦头,需工人手持气动铆枪完成。工业机器人人由于自动化程度高、位置和姿态调整灵活、编程方便通用等特点,越来越多地被用于航空制造领域 [1] 。机器人自动铆接采用气动锤铆方式,通过各气阀的通短配合,压缩空气进入铆汽缸,推动活塞往复运动,并撞击冲锤,冲击铆钉使其变形。
国内外对机器人锤铆这种方式的研究还不够成熟,理论成果也较少。Xi [2] 等构建了一个机器人与5轴联动顶铁支架相互协作的自动化气动锤铆系统和一种单机器人压铆系统。Huan, H [3] 等人为了提高铆接效率和质量,设计了一种用于机身壁板装配的双机器人气动锤铆系统,其中介绍了包括系统设计、动力学分析和灵敏度分析等内容,最终在可能的情况下取代传统的双人协作铆接方法。于渊 [4] 等以2A12蒙皮为对象,建立有限元分析模型,结合剪切、拉脱试验,得出了自动锤铆工艺性能优于手工锤铆的结论。刘现伟 [5] 等,在自动铆接试验台上进行锤铆试验工艺,建立试验台铆接系统的动力学模型,优化出能够得到符合铆接通用技术要求的镦头高度及较好的铆接件表面质量,减小铆接变形量的参数与方案。周珂 [6] 等搭建带有测力系统的气动接试验平台,得出了弹簧刚度和弹簧预紧力对于铆接冲击力的影响更大、铆枪气压对铆接效率的影响显著的结论。
本文以铸件材料为研究对象,通过铆钉剪切试验、拉脱试验,分析铆接接头铆钉剪切力和拉脱力,宏观上对比自动锤铆和手工锤铆工艺性能。开展轴向剖切金相分析试验,从微观上观察铆接后钉杆不同位置与铝合金夹层材料连接情况,对比自动锤铆和手工锤铆铆接质量。
2. 铆接接头剪切性能对比试验
2.1. 试验材料与设备
剪切试片采用夹层结构,选用ZL205A和2A14的铝合金板料铆接成“一字型”,ZL205A铝合金板料厚度6 mm,2A14的铝合金板料厚度4 mm,搭接区长度20 mm,试片尺寸见图1,铆钉为YC0894-88 4 × 13LY10。剪切测试采用Instron 5985万能试验机进行,剪切速度设置为2 mm/min。剪切试验运用万能试验机分别对手动锤铆和机器人锤铆的试片进行破坏试验,各进行3组试验,测量铆钉铆接件的最大载荷,考核接头的力学性能。
机器人自动锤铆时,需要工装来定位两块板料的姿态,在一块厚10 mm的废料板上一侧铣6 mm深、一侧铣4 mm深槽,通过螺钉连接试片,将两个板放入槽中搭接处铣中空,这样就能将板定位在机器人试刀台上进行定位,铆接后,也能顺利取出铆接后的试片。
2.2. 试验结果对比分析
试片剪切后,手动锤铆和机器人锤铆试片破坏方式一致,钉杆被剪断(两层板件面-面接触的部位),见图2。剪切试验得到的力学性能数据见表1,通过对比分析手动锤铆与机器人锤铆铆钉可承受的最大剪切力相差无几,自动锤铆均值4.29 KN,且数值较为集中,手工锤铆均值4.21 KN,且数值较为离散,但是机器人锤铆铆钉成型一致性控制较好,铆钉性能的波动较小,可以得出自动锤铆剪切性能优于手工锤铆。
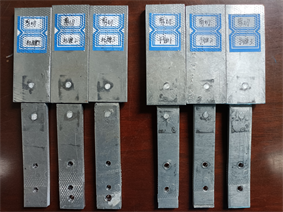
Figure 2. The breaking test for sample of automatic and manual hammer riveting
图2. 自动锤铆试片与手工锤铆试片剪切破坏试验
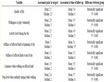
Table 1. Comparison of maximum shear force of rivets
表1. 铆钉最大剪切力对比
3. 铆接接头拉脱性能对比试验
3.1试验材料与设备
拉脱试片选用ZL205A和2A14的铝合金板料铆接成“十字型”,ZL205A铝合金板料厚度6 mm,2A14的铝合金板料厚度4 mm,试片尺寸见图3,铆钉为YC0894-88 4 × 13LY10。拉脱测试采用Instron 5985万能试验机进行,拉脱速度设置为2 mm/min。试件受到拉力作用,拉力作用于铆钉轴线方向,破坏形式为基体或铆钉拉脱。手工铆接和自动锤铆铆接接头在试验机上进行拉脱试验,各进行1组试验,考核铆接接头的力学性能,从失效载荷、失效模式对接头的抗拉脱性能进行分析。
3.2. 试验结果对比分析
拉脱试验运用万能试验机分别对手动锤铆和机器人锤铆的试片进行破坏试验,试片拉脱后,机器人自动锤铆、手动锤铆试片破坏方式一致,均为基体先于铆钉破坏,见图4,铆钉抗拉脱性能均强于基体。
4. 铆接接头轴向剖切金相对比分析试验
4.1. 试验材料与设备
金相试验试片与剪切试验试片尺寸、结构形式相同,试验设备为金相镶嵌机、金相试样切割机、金相显微镜。
金相分析用试样的制备过程包括取样、镶嵌、磨制、抛光、腐蚀等工序。各使用3件自动锤铆与手工锤铆试片制备金相试样,将铆接试片沿钉杆中心线剖开镶嵌,经过水砂纸和金相砂纸打磨、抛光、腐蚀后立刻利用金相显微镜进行观察,见图5。
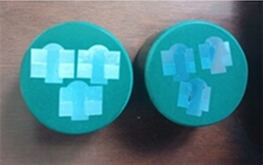
Figure 5. The axial section metallographic analysis sample
图5. 轴向剖切金相分析样件
4.2. 试验结果对比分析
样件金相图见图6,从样件金相图可以看出,机器人自动锤铆钉与孔壁紧密配合、孔径一致、孔壁无缺陷、铆钉墩头成性良好;手动锤铆钉与孔壁有间隙、孔径不一致、孔壁有缺陷、铆钉墩头有侧歪现象。由此得出,自动锤铆铆接质量优于手工锤铆。
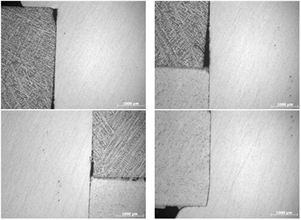
(a)(b)
Figure 6. The metallographic diagram of sample. (a) Automatic hammer riveting metallographic diagram; (b) Manual hammer riveting metallographic diagram
图6. 样件金相图。(a) 自动锤铆金相图;(b) 手工锤铆金相图
5. 总结
通过对比试验和质量分析可以得到以下结论:
1) 通过剪切、拉脱试验对比分析自动锤铆与手工锤铆接头力学性能,自动锤铆与手工锤铆铆钉可承受的最大剪切力相差无几,剪切强度、拉脱强度接近,高于铆钉本身的最小破坏单剪力、拉脱力;
2) 通过轴向剖切金相对比分析试件铆接质量,机器人自动锤铆钉与孔壁紧密配合、孔径一致、孔壁无缺陷、铆钉墩头成形良好。
3) 自动锤铆铆钉成形一致性控制较好,铆钉性能的波动较小,自动锤铆铆接工艺性能优于手工锤铆。采用机器人自动锤铆代替手工锤铆,可以提高铸件材料舱段铆接质量。
参考文献
NOTES
*通讯作者。