1. 背景
随着动车组运行速度的提高,车轮磨耗也显得异常严重,为了确保轮轨接触关系正常,保证车辆的安全运行,需要定期对轮对进行镟修处理。由于我国动车组日均运行里程长,运行交路跨距大,轮对的镟修周期也较短,为轮对的使用寿命带来了严峻的考研,造成了大量轮对的维修和更换,带来了大量运维成本的增加。为了有效解决这一难题,科研学者在轮对的镟修和轮对设计方面进行了大量的研究。李秋泽等 [1] 对XP55-28踏面的经济型镟修踏面进行了设计,在保证车辆安全运行的前提下提出了经济型镟修踏面的设计原则,通过仿真分析和实验测试,该设计原则能有效延长轮对的使用寿面,且能确保安全余量。张旗等 [2] 对LMD踏面的廓形进行了研究,设计了薄轮缘踏面,在运行过程中能保证车辆的运行安全,并能合理的降低维护成本。李国栋 [3] 对LMB-10踏面旋修方案进行了优化,在不改变原型踏面工作区间的前提下,对轮缘跟踏面的过渡曲线进行了调整,该方法能有效减低踏面的旋修量。董孝卿 [4] 等通过大量的跟踪测试,分析车辆的振动特性和磨耗周期性能,制定了车轮镟修的策略和评价方法。综上研究成果显示,在理论和测试上对轮对的镟修方案的研究对轮对的镟修和安全性能方面都有一定的提升,但轮对的管理在各应用站段有特殊的需要和条件限制,有必要根据实际情况建立个性化的维修管理体系,实现站段管理与总公司轮对管理系统的有效整合。
在该镟修过程中,作业人员根据长期的运用经验给定一个镟修量,选择一个符合标准范围的踏面廓形进行镟修处理。由于该操作流程不能对整列车的轮对状态进行评价,导致轮对直径过渡的镟修,造成大量的浪费现象。为此,本文基于动车组运行情况,对踏面的镟修模板进行优化分析,通过不同轮缘厚度等级的模板设计,以有效提高轮对的使用寿命,降低轮径在镟修过程中的浪费,且满足不同条件下的旋修要求。通过该方法的实施,可以在保证踏面等效锥度不变的前提下降低踏面的镟修量,并能保证同一转向架、同一车辆以及同一单元轮对踏面有合理匹配的模板。
2. 镟修现状分析
动车组镟修车床主要自欧洲引进,其修型方法主要参照EN13715标准和DIN5573标准制定。其要求镟修后车轮踏面外形和等效锥度会随镟修后轮缘厚度变化,轮缘厚度越小踏面处外形变化越大,等效锥度越小;镟修后轮缘高度变小,轮缘厚度越小,轮缘高度越小,对轮对造成的浪费就相当明显。依据现有的技术要求对轮对踏面进行镟修,由于认为因素的影响会造成大量的轮对浪费,且还会因镟修不合理缩短整车轮对的使用寿命,增加现场运维的工作量。鉴于此,对两年共计1128条LMA轮对镟修数据进行的统计分析,通过轮径与轮缘厚度的镟修关系探讨如何有效控制轮对的损耗,以提升轮对的使用寿命。调研数据如图1所示。一般轮缘厚度镟修量达到1 mm,轮径需要镟修量集中在6 mm左右,严重的情况下能达到10 mm以上。由此可见,轮到的镟修量远大于轮对正常运行的磨耗量,导致轮对的使用寿命极度缩短,运维成本极度增加 [5] 。此外,部分轮对还存在剥离、凹陷磨耗以及偏磨等异常现象,为了满足镟修标准及安全运行的要求,还会损失更多的轮径值以保证轮缘厚度在标准规定的范围。
3. 优化设计
为了能有效降低LMA踏面的损耗,提升轮对的使用周期,需要采用合理的廓形模板指导轮对的镟修,以延长轮对的使用寿命。为保证合理的轮轨关系,车轮踏面廓形是通过若干段曲线组成,以满足车辆在线路上正常运行,合理的设计能提升车辆的安全性、舒适性和通过性能力。为此,通过分析踏面曲线段的连接关系,改变曲线的长度和曲率即可获取合理的踏面廓形模板。对比LMA薄轮缘踏面外形与原有标准轮缘踏面外形,保持D~E~F段和G (G’)~J段外形不变,确保轮轨接触关系正常。将标准轮缘踏面在F点断开,D~E~F段向左平移,平移的距离等于轮缘厚度的减少量,常规的薄轮缘踏面外形分别为LMA-32.5,LMA-32,LMA-31.5,LMA-31,LMA-30.5,LMA-30,LMA-29.5,LMA-29,LMA-28.5,LMA-28,LMA-27.5,LMA-27,LMA-26.5,LMA-26,如图2所示。根据轮缘厚度标准要求,按照轮缘厚度的限定值要求仅能达到14种标准廓形模板,若对以上模板进行细化,考虑0.1 mm的模板间隔,则可形成70种廓形模板,能根据实际磨耗情况选择不同的廓形作为镟修依据,防止各轮对采用统一的镟修参考模板,尽可能的节约轮对镟修量,以达到延长使用寿命的目的。
相较于原标准,G-H段曲线是轮轨接触的主要区域,决定了轮轨接触时的等效锥度,进行薄轮缘设计时该部分曲线保持不变,D-E-F处外形与轮缘脱轨系数息息相关,该部分曲线在新模板设计时也未变化,通过使用高次曲线连接F-G段,以得到不同轮缘厚度的车轮外形。而通过调整Ra、Rb、Rc圆弧的圆心与半径,保证新外形高度与原形高度相同。
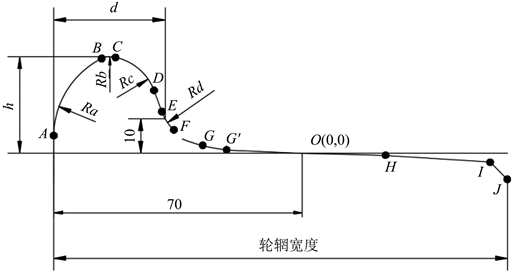
Figure 2. The template of LMA-type wheel tread profile
图2. LMA型踏面模板
为验证上述设计方法的合理性和可行性,对比了两种模板下轮对的旋修情况,其对比表1如所示,镟前轮缘厚集中在区间32.5~33 mm内,在0.5 mm模板镟修模式下,将根据左右车轮镟前轮缘厚选择厚度为32.5 mm或33 mm的模板。对于细化后的模板,可供选择的轮缘厚更多,同时允许左右车轮镟后存在轮缘厚差。结果显示以0.1 mm间隔的轮缘厚模板进行镟修作业时可以有效降低镟修量,从而论证了薄轮缘模板的合理性和可行性。
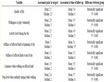
Table 1. Data analysis of different rotating repair templates
表1. 不同旋修模板数据分析
4. 寿命预测
基于车轮磨耗和镟修规律模型,对不同间隔轮缘厚模板下的车轮剩余使用寿命进行预测,进一步验证采用0.1 mm间隔轮缘厚模板镟修的经济性。考虑一个运维周期,基于磨耗数据统计和对应的镟修摸则可有效预测轮径和轮缘厚度的磨耗量。
一个镟修周期内轮径磨耗预测公式如下,
(1)
其中,a1,b1,c1是常数,D1为上次镟后轮径值(mm),L为走行公里数(km),D2为当次镟前轮径值(mm)。
一个镟修周期内轮缘厚磨耗预测公式如下,
(2)
其中,a2,b2,c2是常数,B1为上次镟后轮缘厚值(mm),L为走行公里数(km),B1为这次镟前轮缘厚值(mm)
选取某新轮对进行寿命到限预测,该车轮新轮径为860 mm,轮缘厚32.9 mm,若均以增厚镟进行镟修,新轮运行100万km后,使用0.5 mm轮缘厚模板镟修的车轮因镟修轮径损耗较大,而使用0.1 mm轮缘厚模板镟修的车轮轮径损耗相对较小,轮径和轮缘厚度的变化如图3所示。
通过上述分析可以得出结论,若能将现有LMA型踏面0.5 mm间隔踏面廓型进行细化,形成0.1 mm间隔踏面廓形标准,采用细化后的踏面廓形标准可有效降低轮径旋修量,延长轮饼使用寿命。对不同轮缘厚度间隔模板下的车轮剩余使用寿命进行了预测,进一步验证采用0.1 mm间隔轮缘厚模板旋修的经济性。使用0.1 mm轮缘厚旋修模板后,单周期轮径旋修量降低,同时保证轮缘厚度在合理区间内,使得车组不会因轮缘损耗而导致高级修恢复轮缘厚度产生旋修量过大,可有效地延长了车轮的使用寿命。
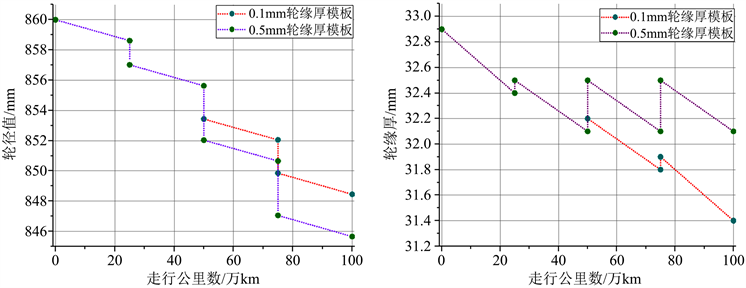
Figure 3. Wheelset wear process simulation
图3. 轮对磨损过程模拟
5. 结论
车辆轮对的合理维修策略能有效提高其使用寿命,常规的轮对镟修方案过于粗糙,本文在基于现有轮对镟修模板的基础上进行调研,在保证轮轨关系不发生改变的前提下对轮对模板进行细化,将0.5 mm间隔的模板细化为0.1 mm间隔的模板,能为镟修提供更多的参考模板,防止轮对镟修的浪费。通过以上手段对新轮的磨耗分析可知,相对于0.5 mm的镟修模板,采用0.1 mm的镟修模板能节约2 mm以上的轮径镟修量,而轮缘厚度也不用恢复至标准轮缘厚度的状态。随着运行里程的增加,该模板的优势更明显。该细化模板能后有效延长了轮对的使用寿命,提升了经济效益,为轮对的健康管理提供了参考。
基金项目
铁路局自主项目(ZX2112)。