1. 引言
为提高机床批量加工零件时的生产效率,车间常用夹具快速找正并固定工件在机床上的加工位置。零件的生产过程中不可避免有人工、变形、装配偏差等各类加工误差,其中夹具系统造成的误差约占6%~10%,故夹具设计质量的高低决定了机床能否提高生产效率、控制成本、操作方便以平稳地生产工件 [1] 。下面就夹具设计的几个重要方面展开论述:在确定夹具有关尺寸、配合及夹具技术条件方面,张新义 [2] 、张俊俊等 [3] 采用概率论以及可靠性技术等方法建立了夹具定位销精度设计的概率法,该法能有效解决装配方便和加工精度之间的矛盾。沈为清等 [4] 引用刚体动力学分析方法,推导出了一种敏感度指标用于评价“一面两销”夹具定位销布局设计的鲁棒性。CALABRESE M等 [5] 根据工件的局部刚度特性,对夹具–工件系统进行拓扑优化,该方法改变了优化问题的拓扑设计变量和优化约束,提供了夹具精度优化设计的新方法。VUKELIC D等 [6] 基于接触界面的预处理并将夹紧元件压入工件中,以达到提高工件与加工夹具之间夹紧力的目的。YACOB F等 [7] 为了降低数学复杂性,提出了双四元数来表示和转换虚拟零件和夹具;在确定夹具的结构方案方面,徐旭松等 [8] 讨论了销/孔定位精度分析方法,通过优化定位结构的方式提高了一面两孔夹具的定位精度。吴盘龙等 [9] 用多齿瓣圆柱销代替了传统的定位销结构,消除了销/孔之间的配合间隙,该方法实现了定位基准相对统一。QI R等 [10] 设计了一种可变多点多自由度配套夹具,提高了生产效益。NUGRAHA A D等 [11] 在Abaqus/CAE中利用有限元方法,该法确定了夹具的几何形状和尺寸对加工结果的影响并对夹具进行结构优化设计。XIE W等 [12] 开发了基于持续优化方法的增强蚁群算法(ACA),以优化多工位装配过程中2D刚性零件的夹具布局。VINOSH M等 [13] 重点研究了夹具位置对钣金件尺寸质量的影响,该法使用混合优化技术,通过有限元分析方法确定最佳装夹位置,以实现最小变形。PARK J W等 [14] 提出了一种基于可变形引脚阵列的零件夹具系统,该系统可用来固定零件,并自适应地支撑不同形状的零件;在研究夹具定位误差分析方法方面,李双成等 [15] 提出应用尺寸链原理解决“一面两销”定位夹具的定位误差分析与计算,该方法弥补了几何解析法计算空间定位误差的不足。宁龙等 [16] 基于吴玉光提出的机构学模型,提出了基于ADAMS软件的夹具定位误差分析方法,通过等价机构建模,应用统计学分析夹具定位误差的概率结果。刘亚雄等 [17] 以运动学原理为基础,分析了基于零点定位系统的夹具精度,建立了夹具定位误差的分析模型。此外,齐振超等 [18] 、郑伟 [19] 、韩变枝等 [20] 分别为工程实际中的具体案例设计专用夹具,并运用MATLAB、ADAMS等软件对夹具的定位误差进行分析。
在对夹具定位设计的研究中,学者们对于如何有效减小夹具定位误差已经有了相对成熟的研究,但若一味提高夹具定位精度而忽视夹具与工件之间的装夹成功率往往会得不偿失,反而会降低工件加工效率。除此以外,若仅对夹具进行尺寸公差设计,忽略几何公差和公差原则,会导致夹具精度得不到有效控制,从而降低定位精度、产生加工误差。因此,在对夹具进行精度设计时,须充分考虑夹具与被装夹零件的装夹成功率及其定位精度,并合理运用尺寸公差和几何公差来保证夹具本身的精度。
2. 装夹成功率的计算模型
工件采用“一面两销”定位时,工件能否成功装夹到夹具上主要取决于定位元件(定位销/孔)能否装配成功。张新义 [2] 建立了定位销/孔装配成功率数学模型,文中引用该模型分析床头箱盖夹具设计方案的装夹成功率,具体推导过程不再赘述。
一般情况下,定位销/孔尺寸与间隙均符合正态分布规律,故销/孔尺寸与间隙分布的概率密度函数为:
(1)
式中:δ为销/孔尺寸与间隙,是符合正态分布的随机变量;
为销/孔尺寸与间隙的平均值;
为销/孔尺寸与间隙的标准偏差。
销/孔中心的偏离距离S为偏态分布,即可视为销/孔中心与位置度圆心的连线在以位置度圆心为原点、销/孔几何公差带为直径建立的坐标系内的矢量分布情况,即角度的均匀分布与偏心距正态分布的综合结果,其概率密度函数
为:
(2)
式中:
为偏心距离S的标准偏差。若孔心落在位置度圆内(即定位孔几何公差带
内)的置信度为H,则有:
,根据
原则取
,代入原式可得
,即
,故销/孔中心偏离距离S的标准偏差
为:
(3)
式中:
为定位孔的几何公差;
为定位销的几何公差。
由式(3),定位孔在相关公差原则下,主、副定位销/孔装配偏心距离S的标准偏差
、
为:
(4)
(5)
式中:
、
为主、副定位孔的实际加工尺寸;
、
为主、副定位孔公称直径尺寸;
、
为主、副定位孔最大、小设计尺寸与公称直径的差值;
、
为主、副定位孔实际加工尺寸对公差的补偿值;
、
、
为主、副定位孔/销的几何公差。
将工件安装到夹具上时,先对正主定位销/孔,主定位销/孔的装夹成功概率为:
(6)
式中:
、
为主定位销/孔间隙的均值与标准偏差;
;
;
。
对于副定位销/孔:当两销/孔间隙之和大于副定位销/孔的实际偏心距离S时装夹成功,副定位销/孔的装夹成功率为:
(7)
式中:
、
为副销/孔间隙的均值与标准偏差;
;
。
综上,夹具与被装夹工件之间的装夹成功率P为:
(8)
3. 夹具定位销初始精度设计与装夹成功率分析
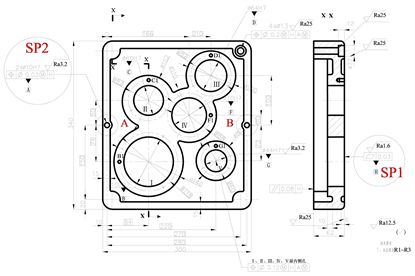
Figure 1. Schematic diagram of bedside box cover parts
图1. 床头箱盖零件简图
图1为床头箱盖的零件简图 [21] ,需设计专用夹具装夹:夹具采用“一面两销”定位方式,需设计夹具体上定位面和定位销的尺寸与公差。零件以图中大平面H作为第一定位基准(标注有SP1技术规范);以孔A (主定位孔)的中心线为第二定位基准、孔B (副定位孔)的中心线为第三定位基准(标注有SP2技术规范),下面先对夹具定位销进行初始精度设计与装夹成功率分析。
3.1. 定位销初始精度设计
如图1所示,两定位孔尺寸为
mm,实际设计中 [22] 主定位(圆)销直径尺寸d1的上限值为定位孔直径尺寸D1的下限值,考虑优先配合需求,主定位(圆)销尺寸设计为
mm。副定位销选用菱形销结构,菱形销的结构尺寸按照标准选用宽度b为4 mm。常规设计中,通常会代入两销/孔中心距公差计算副定位销/孔最小间隙,再对菱形销进行精度设计。案例中两孔中心距为理论正确尺寸,且以几何公差控制两孔轴线位置,显然不适用传统设计方法。张新义 [2] 给出了考虑销/孔几何公差时,菱形销与定位孔最小配合间隙c2的计算方法:
(9)
式中:D2为副定位孔公称直径尺寸;c1为主定位销/孔最小配合间隙;
、
为定位销、孔几何公差。
主定位销/孔最小配合间隙c1为0 mm,两销/孔几何公差均为0.030 mm,将各参数代入式(9)可得菱形销与定位孔最小配合间隙c2为0.048 mm,菱形销/孔的配合也为H7/h6,菱形销尺寸设计为
mm,如图2所示为床头箱盖夹具初始设计简图。
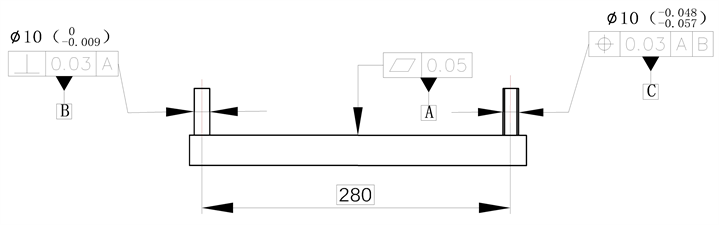
Figure 2. Initial design diagram for fixture positioning of headbox cover
图2. 床头箱盖夹具定位初始设计简图
3.2. 蒙特卡洛模型模拟与MATLAB求解
研究表明,批量生产时定位销/孔加工尺寸与间隙均符合正态分布规律 [23] ,蒙特卡罗模型是一种可以按照分布类型随机取样的仿真模型。两定位孔直径分布范围均为ϕ10 mm~ϕ10.015 mm,圆销为ϕ9.991 mm~ϕ10 mm,菱形销为ϕ9.943 mm~ϕ9.952 mm。在MATLAB中调用normrnd ( )函数生成销/孔尺寸范围内的随机数,为提高模拟精度,模拟次数为5000次。可将模拟圆孔尺寸的代函数与两销尺寸的代函数相减表征定位销/孔间隙的分布情况。定位销/孔的尺寸分布模拟程序可表示为:R = normrnd (10.0075, 0.0025, 50000, 1);A = normrnd (9.9955, 0.0015, 50000, 1);B = normrnd (9.9475, 0.0015, 50000, 1)运行程序并整理定位销/孔尺寸与间隙模拟情况如表1所示,图3所示为定位销/孔尺寸与间隙分布模拟结果的频率分布直方图及其正态分布拟合曲线。
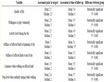
Table 1. Pin/hole size and gap simulation
表1. 销/孔尺寸与间隙模拟
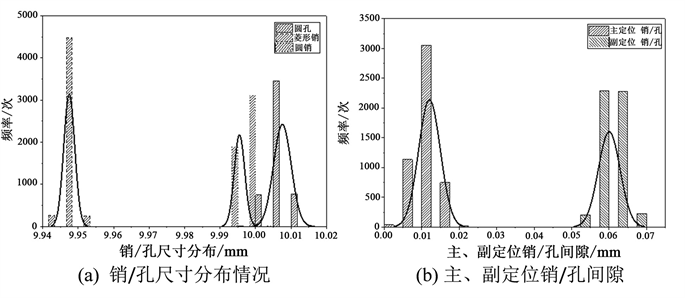
Figure 3. Locating pin/hole size and gap distribution
图3. 定位销/孔尺寸与间隙分布情况
将表1主定位销/孔尺寸模拟数据代入式(1)~(8)中,销/孔间隙数值较小且公式较为复杂,在MATLAB中调用integral()函数求解式(6)~(7)积分结果。解得主定位销/孔装夹成功率为96.83%,副定位销/孔装夹成功率(运算程序与主定位销/孔装夹成功率运算程序调用函数一致,此处不再赘述)为98.04%,故床头箱盖夹具初始定位设计方案的装夹成功率P为94.93%。
4. 面向装夹成功率的定位销精度优化设计
4.1. 定位销尺寸优化设计方案
工件批量生产时,若不能顺利安装到机床上,常常直接削减定位销尺寸或钻大工件孔径以确保夹具与被装夹工件之间的装夹成功率,但却会导致工件与夹具之间有较大的定位误差,显然是不合理的。主要原因是定位特征的几何误差未得到有效控制。因此,在零件设计及夹具设计时,应采用尺寸公差、几何公差来综合控制尺寸误差和几何误差的综合作用的结果,从而能保证销/孔装配的一次成功率:当孔/槽的最大实体实效边界等于销/轴的最大实体实效边界时,定位销/孔100%装夹成功。床头箱盖定位孔的最大实体实效尺寸DMMVB = DMMC − 几何公差,即ϕ9.97 mm。当定位销的设计尺寸小于ϕ9.97 mm时,销/孔100%装夹成功,为避免销/孔定位误差过大,定位销公称直径设计范围为ϕ9.97 mm~ϕ10 mm,几何公差的取值范围为0.025 mm~0.030 mm,定位销精度设计的其它参数设计步骤与初始方案一致。夹具定位销精度优化设计方案整理如表2所示。
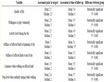
Table 2. Optimization design scheme for positioning pin accuracy
表2. 定位销精度优化设计方案
4.2. 蒙特卡洛模型模拟与装夹成功率求解
采用蒙特卡洛模型模拟销/孔尺寸与间隙分布情况,在MATLAB中输入模拟次数为5000次(具体分析步骤与初始方案(3.1、3.2节)一致,此处不再赘述)得到主、副定位销/孔间隙分布模拟情况,见表3和表4。
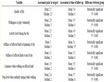
Table 3. Simulation of the clearance distribution of the master positioning pin/hole
表3. 主定位销/孔间隙分布模拟
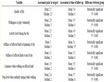
Table 4. Simulation of clearance distribution of secondary alignment pin/hole
表4. 副定位销/孔间隙分布模拟
将表3、4中的模拟结果代入MATLAB计算程序,计算出的各方案装夹成功率如表5所示。
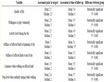
Table 5. Success rate of main and auxiliary pins/holes and final assembly
表5. 主、副销/孔与总装夹成功率
4.3. 方案分析与讨论
分析定位销公称直径对装夹成功率的影响时,保持定位销几何公差不变,即讨论A、B、C、D、E、F六组数据的变化趋势;分析几何公差对装夹成功率的影响时,保持定位销公称直径不变,即讨论A1、B1、C1、D1、E1、F1 (A2、B2、C2……)四组数据的变化趋势。由表5可知:当定位销几何公差不变,公称尺寸减小时,总装夹成功率呈起伏上升趋势;当定位销公称尺寸不变,几何公差减小时,总装夹成功率呈稳定上升趋势;当定位销设计方案为D3即定位销几何公差为0.028 mm、公称直径为ϕ9.98 mm时,工件在夹具上的装夹成功率最大,为98.69%,较定位销初始精度设计方案F1提升了3.76%。
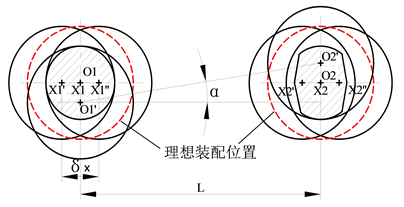
Figure 4. Schematic diagram of workpiece positioning error
图4. 工件定位误差示意图
对夹具定位销进行精度优化设计时,不仅需要保证夹具与工件之间具有较高的装夹成功率,还须确保工件有较小的定位误差。如图4所示,工件以“一面两销”方式装夹到夹具上时,相对理想装夹位置有平移和转动两种位置变化,分析工件定位误差时需从这两个方面进行考虑。何聪惠 [24] 给出了计算工件定位误差时的常用公式:
1) 因平移引起的两定位销连心线X1~X2方向的定位误差
:
(10)
2) 因工件转动引起的垂直于两销连线方向的转角误差
:
(11)
式中:
、
为工件两定位孔几何公差;
、
为夹具两定位销几何公差;
、
为主、副定位销/孔最小间隙;L为两销/孔中心距。
计算
、
时代入表3、4间隙模拟值的最小值,由式(10)、(11)可得工件定位误差如表6所示。
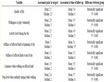
Table 6. Workpiece positioning error
表6. 工件定位误差
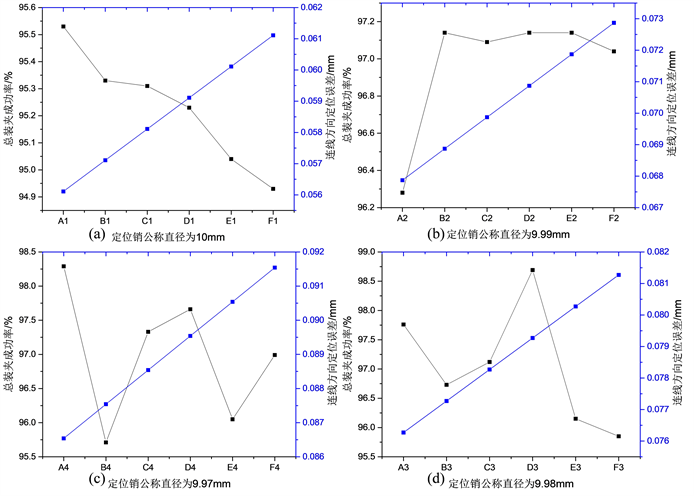
Figure 5. Clamping situation under different geometric tolerances
图5. 不同几何公差下的装夹情况
如图5所示为不同几何公差、相同公称直径情况下的夹具装夹成功率与定位误差的情况,显然销/孔间隙越大,工件–夹具定位误差越大,总装夹成功率越低。比较发现A1、A2和F1方案相对较好,综合权衡装夹成功率和定位精度,选择方案A2作为夹具定位销最佳精度设计方案。该方案与A1相比两销连线方向定位误差增加了0.01176 mm,转角误差增加了0.00004,总装夹成功率提高了0.75%;与方案F1相比总装夹成功率增加1.35%,两销连线方向定位误差增加0.00676 mm,转角定位误差增加0.00001,在可接受范围内,与初始方案相比,较为合理。故床头箱盖夹具改进后公差设计方案为:圆销尺寸为
mm,菱形销尺寸为
mm,两销几何公差均为0.025 mm,其图样标注如图6所示。
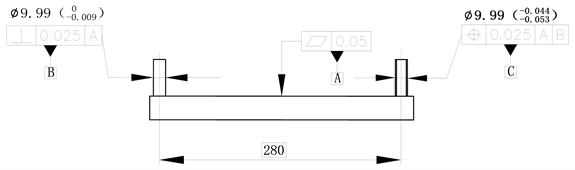
Figure 6. Schematic diagram of improved design for fixture positioning of bedside box cover
图6. 床头箱盖夹具定位改进设计简图
5. 结语
1) 在保证工件加工精度的前提下,通过对比不同定位销尺寸设计方案中工件与夹具之间的装夹成功率,选定最佳定位销尺寸与几何公差设计方案,优化方案较原始方案装夹成功率提升了1.35%,给夹具精度设计方法提供了新思路。
2) 模拟定位销/孔实际尺寸时忽略了很多实际加工时的不利因素,工件模拟尺寸相比较实际加工尺寸误差较小,实际生产中工件与夹具之间的装夹成功率与文中分析结果相比较小。除此以外,装夹成功率数学模型只分析了定位销/孔尺寸与几何公差对装夹成功率的影响,分析结果具有一定的局限性,后续可从温度、变形、材料等方面入手,分析其对工件与夹具之间装夹成功率的影响。
基金项目
江苏省(校)研究生实践创新计划项目(XSJCX21_42);江苏高校“青蓝工程”资助。
NOTES
*通讯作者。