1. 引言
2022年,全国粗钢产量超10亿吨,冶金尘泥生产量超过2000万吨,如何合理利用和处置冶金尘泥已经成为钢铁行业可持续发展的关键 [1] 。
在目前处理冶金尘泥的方式中,因转底炉工艺的适应性较好 [2] [3] 、可靠性高、易于操作和维护,且对环境污染相对较小,具有较大应用价值 [4] ,更适合钢铁企业流程化生产 [5] [6] [7] [8] [9] 。
转底炉生产线采用压团工艺对含锌粉尘进行成型及烘干含锌粉尘的脱锌处理 [10] ,锌富集于烟尘进行收集后用于外售。由于含锌粉尘种类多、性能差异大 [11] ,必须使用粘结剂强化成球,以提高成球率及球团强度、保证转底炉运转稳定及产品质量 [10] [12] 。但是,目前大多使用淀粉类粘结剂,存在添加量大(4%~7%)、生产成本高、成品率较低及成品粉化率高(全流程返料量高达30%~60%) [13] 、易导致转底炉底结炉、影响排料等问题,宝武集团环境资源科技有限公司自主研发的新型复合粘结剂有效地解决了以上问题。
2. 原料成分与性质
2.1. 原料种类
试验所用原料由宝武集团上海转底炉基地提供,包括粘结剂、焦化系统除尘灰(CDQ粉)、高炉出铁场灰、高炉二次灰、电炉除尘灰、冷轧泥,以及现场消解后的电炉除尘灰和LT & OG (转炉干法灰&转炉湿法泥)泥灰混合料等。
本研究中用到的粘结剂类型主要包括有机粘结剂(淀粉)、无机粘结剂(膨润土)和自主研发的复合粘结剂三大类。分别为淀粉粘结DF-1#和无机粘结剂膨润土WJ-1#,以及自主开发的新型复合粘结剂(FH-7#、FH-8#、FH9#)。所有粘结剂经低温烘干(<50℃)后用于性能检测和压团试验。
2.2. 试验原料与配料结构
原料粒度对球团成型至关重要,含铁锌的粒度组成和比表面积如表1所示。除冷轧泥外,其他冶金尘泥的粒度均非常细,特别是OG泥和出铁场灰,0.025 mm以下含量分别为93.23%和85.58%。从比表面积来看,所有冶金尘泥的比表面积均较高,其中高炉二次灰的比表面积最低,为1919 cm2·g−1,而高炉出铁场灰最高,为3752 cm2·g−1。
由表2中CDQ粉的粒度组成可见,CDQ粉粒度较细,0.150 mm以下含量约占53%。
表3为根据转底炉生产现场的实际生产物料配比制定配料方案。
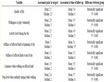
Table 1. The particle size composition of metallurgical dust and sludge
表1. 冶金尘泥的粒度组成
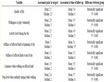
Table 2. The particle size composition of CDQ powder
表2. CDQ粉的粒度组成
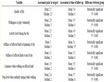
Table 3. Ore blending scheme for optimization test of briquetting process parameters (dry basis)/w%
表3. 压团工艺参数优化试验采用的配矿方案(干基)/w%
3. 研究方法与设备
3.1. 压团工艺参数选择
每次压团试验固定物料干基总重为2 kg。压团工艺参数包括:
1) 粘结剂用量:0%、3%、3.3%、4%、5%、6%;
2) 混合物料含水率:12%、13%、14%、15%;
3) 本研究中用到的所有粘结剂经低温烘干(<50℃)后用于性能检测和压团试验。
3.2. 主要试验设备
压团试验中用到的压球机为对辊压球机,压力可以在0~30 MPa之间调节,压团试验模拟生产现场压球机参数,成型压力选择10 MPa,压辊转速固定8 rpm,所得团块的尺寸为25*25*15 mm的椭圆体长轴形状。
3.3. 试验方法和目的
3.3.1. 团块质量评价方法
生团块的质量评价指标主要有成球率、落下强度、抗压强度和爆裂指数;而干团块的质量评价指标有干燥脱粉率、落下强度和抗压强度。
1) 成球率:定义为每次压团试验一次成型所得生团块中+8 mm粒级的百分含量。+8 mm粒级含量越高,意味着团块强度高,后续筛分可能产生的返料量少。
2) 落下强度,采用了两种方法进行测定:
a) 取10个外形完整的生团块或干团块,分别从0.5 m高度摔落到5 mm钢板,记录下各团块破碎1/4以上时所对应的落下次数,最终落下强度定义为:所有团块落下次数的平均值,单位为“次∙(0.5 m)−1”;
b) 每次取10个外形完整的生团块或干团块,称重记录初始重量后,从0.5 m高处摔落至5 mm钢板上10次,然后用8 mm方孔筛对团块进行筛分,+8 mm以上团块所占的百分含量定义为落下强度。每组试验重复2~3次。
3) 抗压强度:取10个外形完整的生团块或干团块,依次对每个团块缓慢施加压力,记录团块被压溃瞬间的强度,最后求取平均。
4) 爆裂指数:每取20个外形完整的生团块装入底部带孔的不锈钢罐中,料层高度约100 mm,在鼓风风温350℃、风速1.5 N∙m∙s−1的条件下,干燥5 min后取出冷却,称重并记录团块质量,然后用8 mm方孔筛筛出−8 mm粒级,以该粒级的百分含量表征生团块的爆裂指数。爆裂指数越低,意味着生团块的热稳定性越好。
5) 干燥脱粉率:取一定量外形完整的生团块,置于105℃烘箱烘干6 h后取出冷却、称重,然后筛分、计算得到8 mm以下粒级的百分含量。该数值越高,意味着生团块的强度较差,生产中易在干燥中产生粉末,增加返料量。
3.3.2. 试验目的
为了确保含锌粉尘球团被转底炉还原后得到较高的金属化率、脱锌率、抗压强度以及较低的粉化率的金属化球团,在压团过程中需要严格把控各项工艺参数,包括粘结剂种类选择、粘结剂用量、球团水分等指标。本文研究的新型复合粘结剂克服了传统单一淀粉类粘结剂添加量大、返料比高以及球团质量差的问题,球团质量指标要求见表4所示。
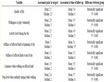
Table 4. Requirements of pellets entering the furnace in rotary hearth furnace process
表4. 转底炉工艺对入炉球团指标要求
4. 含锌粉尘压团试验
4.1. 单一淀粉粘结剂压团试验
参考表3配料结构压球,DF-1#压团试验结果见表5所示,当添加量在DF-1为4%、物料含水率为14%、成型压力为20 MPa时,所得生团块的成球率92.8%,落下强度为93.5% (+8 mm)和11.8 次∙(0.5 m)−1,抗压强度为56.7 N∙个−1,爆裂指数为1.4%;干团块的干燥脱粉率为1.0%,落下强度为97.4% (+8 mm)和11.5 次∙(0.5 m)−1,抗压强度137.8 N∙个−1;爆裂指数和干燥脱粉率 ≥ 1%,由此可推断球团在烘干和还原过程中极易发生爆裂和粉化现象,最终导致生产过程中返料比和还原粉化率升高,降低生产作业率。
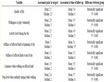
Table 5. Briquette test with DF-1# binder
表5. 以DF-1#粘结剂的压团试验
4.2. 单一膨润土压团试验
参考表3配料结构压球,WJ-1#属于钠基膨润土,压团试验结果见表6所示,与淀粉粘结剂相比,膨润土作为粘结剂的压团性能明显更差。当WJ-1#用量为4%、压团物料含水率为14%、成型压力为10 MPa时,所得生团块的成球率为87.4%,落下强度仅为69.5% (+8 mm)和4.5 次∙(0.5 m)−1,抗压强度为31.9 N∙个−1,爆裂指数为0.2%;干团块的干燥脱粉率为1.0%,落下强度为86.3% (+8 mm)和8.2 次∙(0.5 m)−1,抗压强度为104.3 N∙个−1。当膨润土用量由4%增加到6%时,生团块的落下强度由4.5 次∙(0.5 m)−1略增加至5.0 次∙(0.5 m)−1,而干团块的落下强度反而有所下降。由试验结果可知,单纯增加膨润土用量,并不能明显改善含锌粉尘团块的性能,团块质量指标无法满足转底炉生产要求。
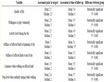
Table 6. Briquette test with WJ-1# binder
表6. WJ-1#粘结剂的压团试验
4.3. 复合粘结剂试验研究
由以上试验结果可知,采用单一淀粉类粘结剂和膨润土粘结剂得到的球团质量都不能完全满足转底炉对含锌粉尘团块的强度要求,本章结合有机粘结剂和膨润土粘结剂压团过程存在的问题进行了复合粘结剂的压团研究,复合粘结剂是由3种以上的无机粘结剂和有机粘结剂原料按照一定的比例搭配混合而成,包括膨润土、淀粉以及有机物等,其中膨润土在还原过程起到降低球团粉化率的作用,淀粉粘结剂可以提高成球率和干团块强度,有机物的大分子链将物料颗粒包裹在一起,对于提高球团抗压强度和降低爆裂指数、干燥脱粉率有明显作用。
4.3.1. 不同种类复合粘结剂试验研究
参考表3配料结构压球,针对自主开发优选的3种复合粘结剂进行压团试验,压团参数:成型压力10 MPa,考虑复合粘结剂吸水性较强,水分含量选择14%、15%,试验结果如表7和图1所示,其中3种复合粘结剂中FH-9#粘结剂在添加量为4%、水分为14%时,压团得到球团质量比其他复合粘结剂高,团块各项指标最优,远高于转底炉对球团的质量要求,尤其是抗压强度如果达不到180 N以上,团块在烘干和还原过程中极易被压碎,不利于转底炉生产。
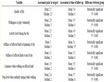
Table 7. Result of briquette test of different kinds of composite binders
表7. 不同种类复合粘结剂的压团试验结果
(a) 含水率14%
(b) 含水率15%
Figure 1. Pellet performance index of FH-7#, FH-8# and FH-9#
图1. FH-7#、FH-8#和FH-9#的球团性能指标
4.3.2. FH-9#粘结剂对比试验
基于FH-9#较好的试验结果,降低用量与生产现场使用的DF-1粘结剂进行对比试验,提高水分含量虽然可以提高团块质量,但是物料水含量升高以后容易引起粘堵,影响产线顺行,根据前期试验结果,同时结合转底炉产线实际运行情况,含锌粉尘混合料水分确定为14%进行压球,试验结果见表8和图2所示。当FH-9#粘结剂用量降到3%时,球团质量指标与现场使用淀粉粘结剂DF-1添加量4%时的指标相当,添加量降低了25%,成本降低约20%以上,且采用该复合粘结剂的干团块质量明显提升,由此说明,复合粘结剂对于提高转底炉压团质量、降低成本有显著作用。
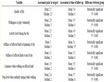
Table 8. Comparison between the index of FH-9# composite binder and the quality of DF-1# briquette
表8. FH-9#复合粘结剂指标与DF-1#压团质量的对比
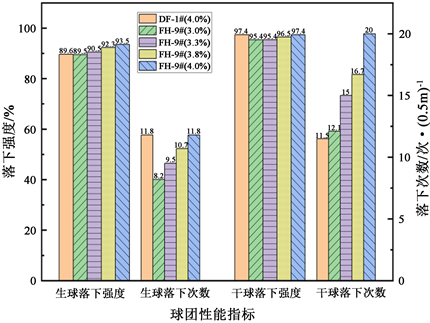
Figure 2. Comparison of pellet performance index between FH-9# binder and DF-1# binder with different addition ratios
图2. 不同添加比例FH-9#粘结剂与DF-1#粘结剂的球团性能指标对比
4.4. 复合粘结剂与淀粉粘结剂性能试验研究
4.4.1. 微观结构分析
图3为淀粉粘结剂DF-1#和复合粘结剂FH-1#粘结剂的微观颗粒形貌。可以看出,DF-1#粒度较大,且夹带少量无机物;FH-9#的粒度较细,杂质较少,质地较为均匀。
(a) DF-1#粘结剂
(b) FH-9#粘结剂
Figure 3. Microscopic particle morphologies of different binders
图3. 不同粘结剂微观颗粒形貌
4.4.2. 粘结剂的化学性质分析
图4给出了淀粉粘结剂DF-1#和新型复合FH-9#粘结剂的红外光谱图,对红外光谱检测结果中各波数下特征峰的归属进行分析,列于表8中。由图4和表9可知,DF-1#和FH-9#粘结剂中均含有大量的羟基-OH、脂肪烃、芳烃C=C、羧基-COOH类官能团,另外还含有少量的酰胺-NH2和C-卤素类官能团,这些复杂官能团的存在对于提高粘结剂粘性有较大作用。相比于FH-9#粘结剂,DF-1#粘结剂在2926 cm−1的峰强较弱,提示脂肪烃类官能团含量较少。此外,DF-1#在1422 cm−1、1372 cm−1处的峰较强,提示其含有更多的饱和烃-CH和酚羟基-OH类官能团。
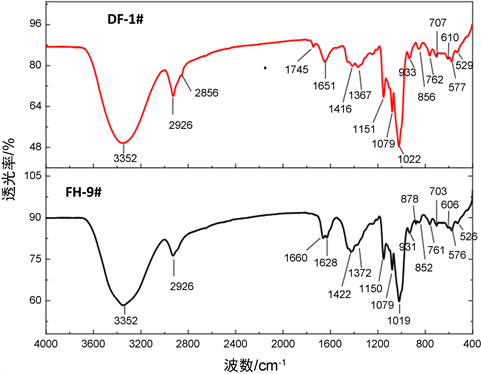
Figure 4. Infrared spectra of different binders
图4. 不同粘结剂的红外光谱
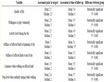
Table 9. Assignment analysis of binder infrared spectral peaks
表9. 粘结剂红外光谱峰的归属分析
4.4.3. “粘结剂–含锌粉尘–水”体系的基本性质
根据表3配矿得到的含锌粉尘与不同种类粘结剂在14%含水率条件下混匀、放置1 h后烘干,含锌粉尘吸附粘结剂颗粒后的微观形貌如图5所示。由图可知,现场用淀粉粘结剂(DF-1#)和新型复合粘结剂(FH-9#)均将含锌粉尘颗粒团聚在一起,但DF-1#和含锌粉尘之间的吸附密度较低、粘结作用一般。
(a) 现场用淀粉粘结剂(DF-1#)
(b) 新型复合粘结剂(FH-9#)
Figure 5. Microscopic morphology of zinc-containing dust after adsorption of different binder particles when the moisture content is 14% moisture
图5. 含水率14%水分时,含锌粉尘吸附不同粘结剂颗粒后的微观形貌
表10为对单一含锌粉尘混合料及含锌粉尘混合料中分别配加5%的DF-1#和FH-9#粘结剂后物料的最大毛细水含量和毛细水迁移速率的测定结果。试验结果显示,不配加粘结剂时,最大毛细水含量为18.70%,毛细水迁移速率为5.14 mm·min−1。配加现场有机淀粉粘结剂后,含锌粉尘的最大毛细水含量明显增加,说明体系的持水能力增加;同时,毛细水迁移速率降低,表明在粘结剂作用下,含锌粉尘的表面亲水性显著增强,毛细水迁移速率过低可能导致在加水混匀过程中水分无法及时渗透和均匀分布于物料中,最终对生团块质量产生不利影响。对比“含锌粉尘 + DF-1#”和“含锌粉尘FH-9#”两种体系,后者的最大毛细水含量更高,毛细水迁移速率较合理。
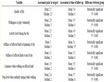
Table 10. Maximum capillary water content and capillary water migration rate after zinc-containing dust and 5% binder
表10. 含锌粉尘及配加5%粘结剂后的最大毛细水含量和毛细水迁移速率
5. 结论
1) 采用单一类的淀粉粘结剂或者膨润土粘结剂都无法完全满足转底炉工艺对球团质量的要求,开发新型复合粘结剂对提高转底炉作业率、降低生产成本有重要意义;
2) 开发的FH-9#新型复合粘结剂与生产现场用的DF-1#淀粉粘结剂相比,在添加量都是4%时,新型复合粘结剂的指标远高于DF-1#粘结剂;新型粘结剂添加量3%的球团指标与FH-9#粘结剂添加量4%的指标相当,新型粘结剂在此添加量前提下,可实现降低粘结剂成本20%以上的目的,当新型粘结剂添加量超过3.3%时,球团质量完全满足转底炉工艺生产需求;
3) 通过试验结果可知,新型复合粘结剂在含锌粉体系中分散性、吸水性等性能较好,适用于转底炉处理钢铁厂含锌固废压团工艺,与生产现场使用淀粉类粘结剂相比,既有技术指标优势,同时又具备成本优势,推广应用前景较好。