1. 引言
天然气是我国的重要能源,目前主要采用管输的方式运输,但管道运行过程中,会因为腐蚀、机械破坏、外力作用、制造缺陷等原因,造成管道失效,从而造成安全风险和环境污染,因此必须对管道进行检测。根据《天然气管道运行规范》SY/T5922-2012(8.5.2条)规定:“新建管道在3年内进行全面性检测,以后根据管道运行安全状况确定全面检测周期,最多不应超过8年”。常规外检测通常只能通过开挖等方式进行局部检测 [1] ,而智能检测可对管道全线进行各种缺陷的内外检测 [2] ,因此开展智能检测是十分必要的。
2. 相关概述
智能检测目前主要是采用漏磁检测技术,通常可分为几何检测 [3] 和漏磁检测 [4] 两部分,通过对检测数据进行对比、综合后形成最终检测报告。
漏磁检测依靠检测仪器自带强磁场,在金属管壁上产生磁感线,管道本体金属产生形变会导致磁感线变形,通过记录磁感线形状,分析管道金属本体的各种变化,利用已有数据模型,分析金属变形所属缺陷种类。可检测出管道的金属损失、夹具下面的缺陷、环焊缝、直焊缝和螺旋焊缝、点蚀、机械加工类型缺陷、管道壁厚的变化、外部金属支撑、以及金属管件等特征。
为获取可靠数据,需保持检测器的平稳运行,通常要求同时满足运行压力最低在2 MPa以上,流速控制在1 m/s~5 m/s,如果运行速度和压力不在理想范围内,将造成数据降级或丢失。有些管线由于气量低,导致流体流速低于低限,造成某些重要管线无法开展漏磁检测。目前尚未见相关文献提出解决方案,本文拟就该问题进行探讨。
3. 提高流速方式
漏磁检测合理流速的确定,通常根据管径(检测器)大小,要求同时满足合理的运行压力和流速,不同检测公司的要求稍有不同,表1是某检测公司的运行条件。
有些管线由于气量低,导致流体流速低于低限,造成无法开展漏磁检测。
为了提高流速,通常有两种方式:
1) 提高气量。但一般气井有合理定产,提高产能可能造成水淹、损害气井采收率等严重后果,一般不能采用;对集输管线,增加气量的可能性也较小。
2) 在气量一定的情况下,通过降低压力的方式。但由于漏磁检测时,压力至少应高于低限,因此气量不能过低。
因此,本文拟就第二种提高流速的方式进行探讨,即对具备计量及放空的条件下,在保持末端输气压力保持在最低压力前提下,在末端进行放空,降低背压,从而提高流体到所需流速,并利用pipesim模拟计算开展漏磁检测所需的最小气量等参数。
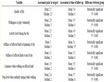
Table 1. Operating conditions of magnetic flux leakage inspection
表1. 某检测公司漏磁检测器运行条件
4. 管线流速模拟计算
PIPESIM是由美国斯伦贝谢公司开发的多相流稳态模拟软件,针对地面管网和井筒等设施进行模拟计算。其基础模块功能包括:管道设计和管径优化、设备计算选型、单井设计分析和人工举升等。PIPESIM对流体的描述分为黑油模型和组分模型,黑油模型可以对油、气、水三相、气液两相以及单相流体进行模拟计算;组分模型可以对化学组份不同的碳氢化合物进行模拟计算。广泛应用于地面管网的工况模拟 [5] 。本文以某D406.4管线为例进行模拟,为提高计算精度,采用组分模型进行模拟,考察日常正常生产工况能否满足漏磁检测条件,以及满足漏磁检测的两种极限运行条件(1 m/s@4 MPa或2 MPa@2.5 m/s)下所需最小气量,其他管线可根据具体情况参照执行。
4.1. 日常正常生产工况
4.1.1. 边界条件
1) 末端输气压力6.1 MPa;
2) 出站温度50℃;
3) 管线规格D406.4*12.5-6.52 Km;
4) 流量44 × 104 m3/d。
4.1.2. 模拟
采用PIPESIM多相流稳态模拟软件模拟,考虑流体中含有气液两相,不能单纯研究气流速度,故以全线各点流体流速为研究对象,模拟结果见图1。
可见在日常正常生产工况下,流体流速在0.67~0.73 m/s之间,不满足漏磁检测最低运行速度1 m/s的要求。
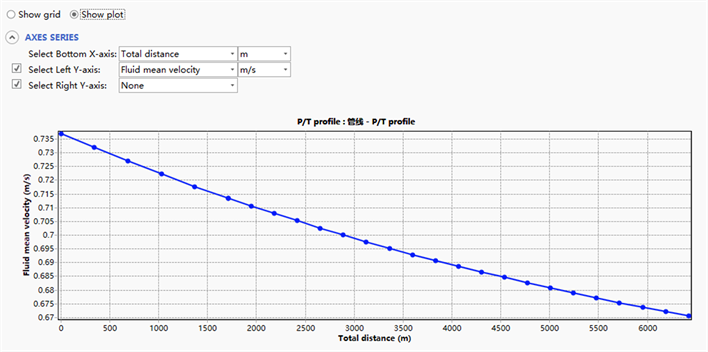
Figure 1. Simulation of pipeline flow rate under daily production conditions
图1. 日常生产条件管线流速模拟
4.2. 运行条件为1 m/s@4 MPa时所需最小气量
4.2.1. 边界条件
保持其他参数不变,改变末端输气压力为4 MPa。
4.2.2. 模拟
指定末端输气压力4 MPa,气量暂定20 × 104 m3/d,以气量(20~100 × 104 m3/d,间隔1 × 104 m3/d)为敏感性参数,模拟结果见图2:
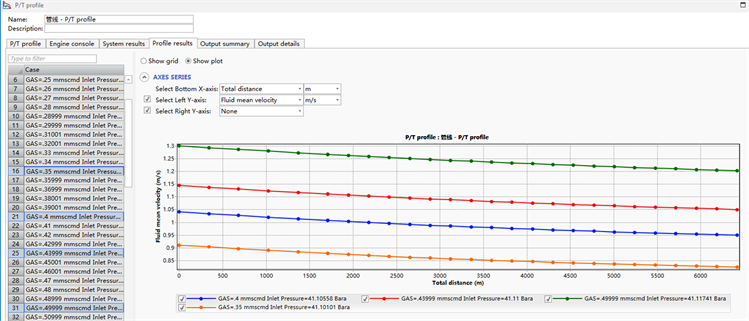
Figure 2. Flow velocity simulation of pipeline with pressure of 4 MPa
图2. 压力为4 MPa管线流速模拟
依次选择气量,观察此气量下,管道沿线各点的流体流速,当所有点的流速均满足在此压力下,漏磁检测要求的最低流速以上时,方为最低要求气量。可知气量为43 × 104 m3/d时,流体流速在1.02~1.12 m/s之间(参见图3),满足漏磁检测最低运行速度1 m/s的要求。
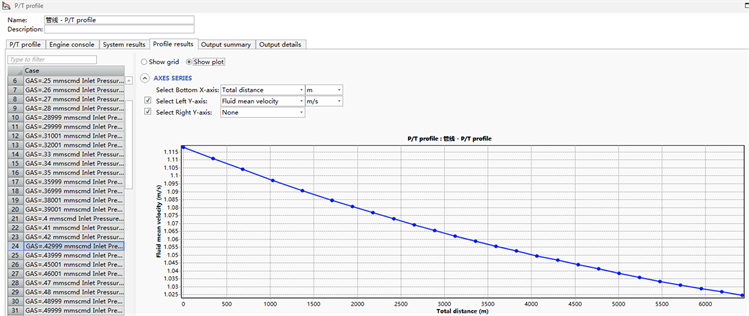
Figure 3. Simulation of pipeline flow velocity with the flow rate of 430,000 m3/day
图3. 流量为43 × 104 m3/d时管线流速模拟
4.3. 运行条件为2.5 m/s@2 MPa时所需最小气量
4.3.1. 边界条件
保持其他参数不变,改变末端输气压力为2 MPa。
4.3.2. 模拟
指定末端输气压力2 MPa,气量暂定20 × 104 m3/d,以气量(20~100 × 104 m3/d,间隔1 × 104 m3/d)为敏感性参数,进行模拟,模拟结果是气量为52 × 104 m3/d时,流速大于2.5 m/s。
4.4. 小结
对于日常正常生产工况(输压6.1 MPa,输量44 × 104 m3/d),流体流速在0.67~0.73 m/s之间,不满足漏磁检测最低运行速度1 m/s的要求。
降压后,对比两种最低要求的工况,可知末端输气压力为4 MPa时,最小气量为43 × 104 m3/d时,流体流速大于1 m/s。由于该井气量为44 × 104 m3/d,可满足智能清管条件。
末端输气压力为2 MPa时,最小气量需52 × 104 m3/d,流体流速才满足此压力条件下,流速大于2.5 m/s的要求。
因此,日常正常生产工况流速不满足智能清管条件的,是有可能通过降低压力,提高流速来达到满足智能清管条件的。
5. 其他问题
5.1. 水合物形成分析
1) 为判断管道是否会形成水合物,pipesim软件常用过冷度来判断,即水合物理论形成温度减去流体实际温度,若流体实际温度高于水合物理论形成温度,则不会形成水合物,此时过冷度为负。该管道流体出站温度50℃,末端的进站温度约28.9℃,通过模拟,过冷度均为负(参见图4),因此管道全程不会形成水合物 [6] 。
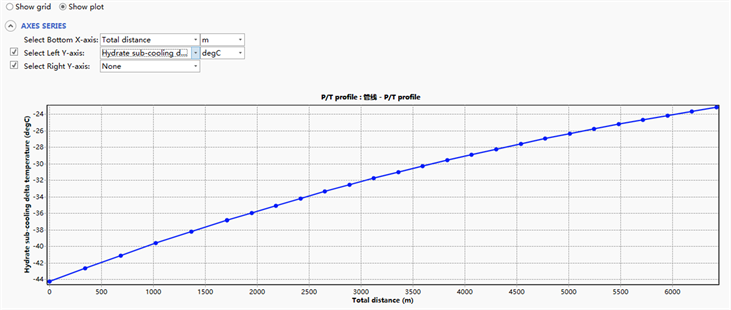
Figure 4. Simulation of hydrate sub-cooling DT
图4. 过冷度模拟
2) 由于放空节流阀有节流效应,需单独对泄压放空系统节流分析,以判断是否会形成水合物。该管线放空系统节流阀后端放空管线为DN300,采用PIPESIM模拟放空工况,模拟结果是放空管线过冷度均为负,不会形成水合物(参见图5)。
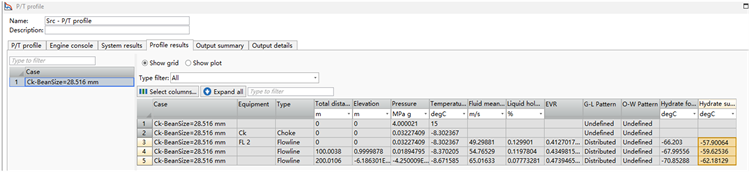
Figure 5. Choke analysis of vent system
图5. 放空系统节流分析
5.2. 泄压放空系统适应性
泄压放空系统对超压泄放、紧急放空及开工、停工或检修时排放出的可燃气体进行收集和处理的设施。泄压放空系统由泄压设备(放空阀、减压阀、安全阀)、收集管线、放空管和处理设备(如分离罐、火炬)或其中一部分设备组成。在设计及建设环节,泄压放空系统已考虑了全量放空的安全性 [7] ,因此放空是安全的。本例中,由于放空管径合理,放空时冲蚀速率比EVR小于1 (参见图5),不会造成冲蚀。
5.3. 放空气量损失
放空气通常采用燃烧处理,无法回收,因此会造成一定的经济损失,损失气量等于放空气量。例如,该管线长6520 m,流速等于1 m/s时,放空时长需1.81 h,由于日产气量为44 × 104 m3/d,故需最少需放空气量3.318 × 104 m3。
6. 现场操作
通过以上理论分析可知,通过控制末端压力,从而提高流速是可以对某些日常工况条件下不能达到漏磁清管流速要求的管线开展漏磁检测的。
现场应具有的条件:1) 具有流量计;2) 具有单独对该管线放空的节流放空阀。
现场操作:待完成预清管后,操作重点一是保持流量(井口流量或集气站的输出流量),当流量计读数有明显变化时,应微调井口节流阀或输气管线来气量。二是在管线末端打开放空节流阀,同步关闭进入站场集输流程阀门,使末端压力降至需要的压力,针对具体管线,若有水合物生成风险,应进行保温。
7. 结论
1) 对于具有单独计量及放空条件的管线,可通过放空方式,达到增加管线流速的效果。
2) 对于管线流速控制,可通过PIPESIM等软件进行理论计算,通过控制气量来控制流速。
3) 根据管线具体工况,若有水合物生成风险对放空阀应采取保温措施,防止水合物生成,导致堵塞。
4) 对管线较长的管线,可能造成较多的气量损失,需对经济性进行考虑。